Cold environments introduce unique challenges for hydraulic hoses, which are responsible for conveying pressurized fluid and powering machinery. In freezing conditions, standard hoses can become stiff, brittle, and prone to cracking, leading to equipment malfunctions and unexpected downtime.
Effects of Extreme Cold on Hydraulic Hoses
Cold-Induced Changes in Hose Materials
Extreme cold significantly impacts the physical properties of materials commonly used in hydraulic hoses, such as rubber and synthetic compounds. As temperatures drop, these materials become less flexible and can start to harden, losing the elasticity needed for reliable performance. This hardening process makes the hose more susceptible to brittleness and cracking, particularly when subjected to sudden movements or pressure spikes. In subzero environments, hoses made from standard materials may no longer function safely or efficiently, as the cold makes them more prone to fractures and leaks. Choosing cold-resistant materials is therefore essential for hydraulic hoses operating in freezing temperatures to maintain system stability and longevity.
Impact on Bending and Flexibility
Cold temperatures reduce a hose’s ability to flex and bend, which is critical for hydraulic systems where hoses must adjust to moving parts or tight configurations. When exposed to extreme cold, standard hoses stiffen and lose their flexibility, making them more likely to develop fractures or micro-cracks during operation. These fractures often occur when the hose is forced to bend or move while in a hardened state, as the material is unable to withstand the stress. Without sufficient flexibility, hoses can fail under pressure, leading to hydraulic fluid leaks, unexpected downtime, and even damage to nearby components. This loss of flexibility highlights the need for cold-resistant hoses that retain their pliability and can safely handle bending and movement even in low temperatures.
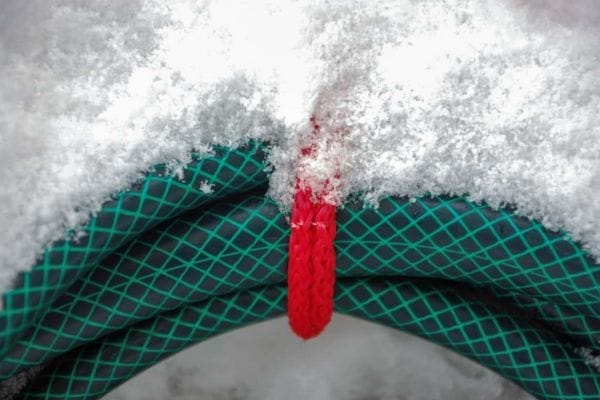
Thermal Stress and Molecular Changes
In extremely low temperatures, hydraulic hoses experience thermal stress, causing molecular changes in the materials. When the temperature reaches a critical point, known as the “glass transition point,” the hose material undergoes a phase change where it becomes rigid and crystallized, losing its natural elasticity. This transition point varies depending on the type of rubber or synthetic compound used, but it generally occurs around -40°C (-40°F) for many standard hose materials. As the material crystallizes, it becomes brittle and less capable of withstanding dynamic loads, which increases the risk of cracking and failure. The glass transition point is a critical factor in hose performance, as hoses made from materials with a lower transition threshold are better suited for cold environments, remaining flexible and reliable in freezing temperatures.
Common Cold-Weather Hose Failures
Brittle Cracking and Fractures
In extreme cold, hydraulic hoses become more susceptible to brittle cracking and fractures. Low temperatures cause hose materials, especially rubber and synthetic compounds, to harden and lose their natural flexibility. When a cold-hardened hose is subjected to movement or pressure changes, particularly sudden or shock loads, it is at a higher risk of cracking or splitting along the hose body. This brittleness is especially problematic in applications that involve frequent bending or rapid movement, as the hardened material cannot adapt to stress as effectively. Cracking or fracturing in hoses not only leads to hydraulic fluid leaks but also requires immediate repair or replacement to prevent further damage to the system.
Reduced Pressure Tolerance
Cold environments also decrease a hose’s ability to withstand pressure, making it more vulnerable to bursts and leaks when exposed to high pressures. As temperatures drop, the molecular structure of the hose material changes, resulting in increased rigidity and a decreased tolerance for internal pressure fluctuations. When hoses lose flexibility, they cannot distribute internal pressures as efficiently, which can result in ruptures or bursts under typical operating pressures. In extremely cold conditions, hoses that were designed for a specific pressure range may underperform or fail altogether, highlighting the importance of using hoses with verified low-temperature pressure ratings. Choosing cold-resistant hoses that retain pressure tolerance in subzero conditions is essential to prevent unexpected system shutdowns and costly repairs.
Abrasion and Surface Degradation
In extreme cold, hoses are more likely to experience surface degradation due to abrasion. As hose materials harden, their outer covers lose flexibility and are more prone to wear from external contact. The rigid outer layer of a cold-exposed hose can become easily scratched, scuffed, or worn down when it rubs against rough surfaces or other components. This degradation increases the risk of exposing the hose’s internal reinforcement layers to environmental elements, which can accelerate wear and lead to leaks or hose failure. Cold-hardened hoses are particularly vulnerable to abrasion in applications with significant movement or where hoses contact other surfaces, underscoring the need for abrasion-resistant outer covers in cold environments.
Selecting Cold-Resistant Hose Materials
Synthetic Rubber Options for Cold Environments
For hydraulic systems operating in subzero temperatures, selecting hoses made from cold-resistant synthetic rubbers like EPDM (Ethylene Propylene Diene Monomer) and nitrile is essential.
EPDM: EPDM rubber is known for its excellent resistance to low temperatures, maintaining flexibility and elasticity even when exposed to extreme cold. This material resists hardening, cracking, and brittleness, making it a strong choice for applications where hoses face continuous or intermittent exposure to freezing conditions. EPDM also offers good resistance to environmental elements such as ozone and UV rays, adding durability for outdoor use.
Nitrile: Nitrile rubber is another option, particularly for applications involving exposure to oil-based fluids. It maintains flexibility at lower temperatures and provides durability in cold environments. Nitrile-based hoses are especially useful in hydraulic applications requiring resistance to fuel, oil, and grease, making them suitable for outdoor machinery and equipment exposed to low temperatures.
Both EPDM and nitrile rubber are highly effective for cold environments due to their ability to resist hardening and cracking, helping to ensure consistent performance and longevity in subzero conditions.
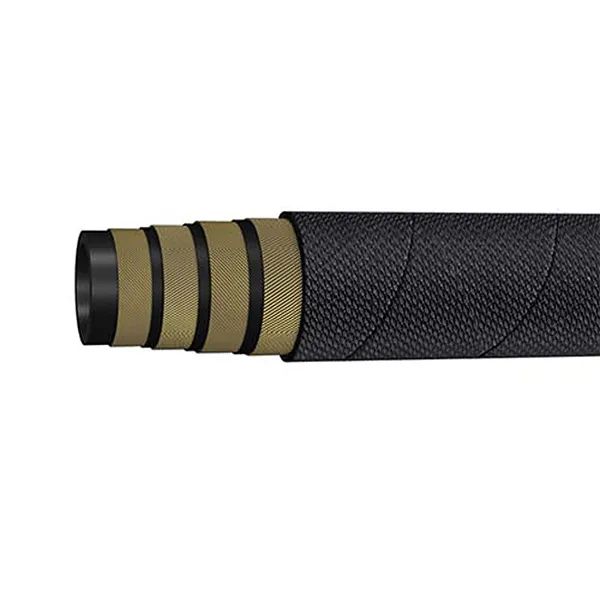
Thermoplastic and Specialty Compounds
Thermoplastic hoses are particularly advantageous for cold-weather applications, offering improved flexibility and durability compared to traditional rubber-based hoses.
Flexibility: Thermoplastic materials retain their flexibility in low temperatures, enabling the hoses to bend and move more easily without risk of fractures. This flexibility is especially useful for hydraulic systems that require frequent hose movement or operation in extreme cold, such as outdoor construction and forestry equipment.
Chemical Resistance: Thermoplastics also provide excellent resistance to a range of chemicals and fluids, making them suitable for applications that involve exposure to oils, fuels, and other hydraulic media. This chemical compatibility enhances hose durability and reduces the risk of chemical-induced wear, even in freezing environments.
Thermoplastic hoses are a versatile solution for hydraulic systems exposed to both cold temperatures and harsh chemicals, ensuring reliable performance without compromising flexibility.
Advantages of Low-Temperature Hoses
For extreme cold applications, specialized low-temperature hydraulic hoses are designed specifically to withstand subzero conditions without losing performance.
Durability in Freezing Temperatures: Low-temperature hoses are engineered with materials and construction techniques that allow them to retain their flexibility and pressure tolerance in extreme cold, sometimes down to -70°F (-57°C) or lower. These hoses undergo rigorous testing to ensure they maintain flexibility, resist brittleness, and withstand mechanical stress in freezing conditions.
Resilience Against Abrasion and Environmental Factors: Many low-temperature hoses also feature reinforced outer covers that protect against abrasion, ozone, and UV exposure, providing additional durability in outdoor environments where hoses face constant cold exposure and surface contact.
Temperature Rating Standards for Cold-Weather Hoses
Understanding Temperature Ratings and Standards
In hydraulic systems operating in cold-weather environments, selecting hoses with the appropriate temperature ratings is essential to ensure safe, reliable performance. Exposure to extreme cold can affect hose flexibility, durability, and pressure tolerance, potentially leading to brittle fractures or unexpected system failures. Temperature ratings and established performance standards help operators identify hoses that will withstand these challenges.
One of the primary standards for assessing hose performance in low temperatures is ISO 10619-2. This international standard specifies methods for testing the bending force of hoses at low temperatures to ensure they maintain flexibility and reliability in subzero conditions.
ISO 10619-2: This standard is designed to evaluate how flexible and resilient hoses remain when exposed to cold temperatures. During ISO 10619-2 testing, hoses are subjected to specific low temperatures, and their bending force is measured to assess whether they retain the flexibility necessary for safe use. Hoses that meet ISO 10619-2 standards have been rigorously tested to resist brittleness and deformation, ensuring they can perform safely in environments that expose them to extreme cold.
Adhering to these standards provides operators with confidence that the hoses they select will maintain their structural integrity, pressure tolerance, and flexibility in subzero conditions, supporting consistent performance and reducing the risk of sudden failures.
Typical Temperature Ranges for Low-Temperature Hoses
Cold-resistant hydraulic hoses are typically rated within specific temperature ranges, enabling operators to choose hoses suited to their particular environmental needs. Selecting hoses with the correct temperature ratings not only ensures safe operation but also maximizes hose longevity by reducing the likelihood of cold-induced damage. Here are some common temperature ratings for low-temperature hoses and examples of suitable applications:
Standard Low-Temperature Hoses (-40°F to -50°F / -40°C to -45°C): Hoses rated for this temperature range are designed to handle moderately cold environments and are commonly used in winter conditions where subzero temperatures are expected but not extreme. These hoses retain flexibility in conditions often encountered in temperate climates or refrigeration facilities. Typical applications include outdoor construction, material handling, and agricultural equipment, where temperatures can drop below freezing but remain within a moderate range. These hoses are also ideal for equipment that operates outdoors seasonally or intermittently in cold weather.
Extreme Low-Temperature Hoses (-65°F to -70°F / -54°C to -57°C): Hoses rated for extremely low temperatures offer superior cold-weather performance, retaining flexibility and durability in harsh, subzero environments. These hoses are designed for industries operating in Arctic or sub-Arctic conditions where temperatures consistently fall well below freezing, such as in forestry, mining, and oil and gas operations. Hoses with this rating are suitable for snow and ice management applications, where the ability to flex and operate reliably in freezing conditions is crucial. These hoses are engineered to maintain resilience against extreme cold, minimizing the risk of brittleness, fractures, and cold-induced pressure loss. Applications like snow grooming equipment and cold storage facilities rely on these hoses to maintain hydraulic function in unforgiving environments.
Protective Measures to Extend Hose Life in Cold Conditions
Using Insulation Wraps for Thermal Protection
Insulation wraps provide a crucial layer of thermal protection for hydraulic hoses operating in extreme cold. These wraps act as a barrier, helping retain heat within the hose and protecting it from direct exposure to freezing temperatures. By wrapping hoses with insulation, operators can reduce the risk of freezing and prevent the hose material from hardening. Insulation wraps are especially beneficial for long hose runs or static applications where hoses are more vulnerable to cold-induced brittleness. For hoses exposed to sustained cold, installing insulation wraps is a simple yet effective way to preserve flexibility, maintain pressure capacity, and extend hose life.
Positioning and Rerouting Techniques
The positioning of hoses can greatly impact their performance in cold conditions. Rerouting hoses away from areas exposed to wind chill or frequent freezing cycles helps protect them from premature hardening and cracking. For example, where possible, hoses should be positioned away from open-air exposure or rerouted through sheltered areas to minimize direct contact with cold air. Rerouting can also involve positioning hoses in ways that reduce bending stress, ensuring they maintain flexibility and resist damage during temperature fluctuations. By carefully considering hose positioning, operators can protect hoses from the effects of colds and prevent common cold-weather failures.
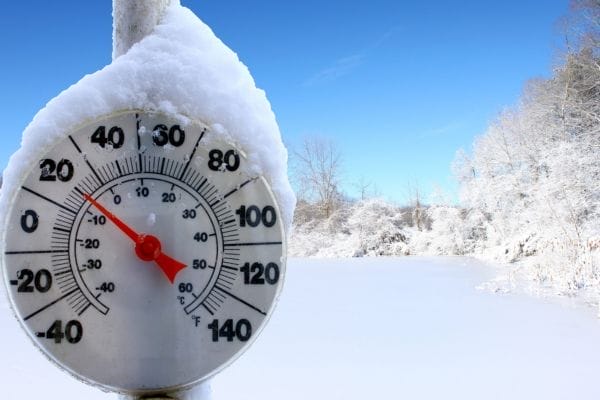
Regular Inspection and Maintenance
Routine inspection and maintenance are vital for detecting early signs of cold-related damage in hydraulic hoses. In freezing environments, hoses should be regularly checked for signs of cracking, stiffness, or surface degradation, which can indicate that the material is becoming brittle. Inspecting hoses for leaks or bulges can also reveal pressure-related stress due to cold exposure. Regularly replacing damaged hoses and scheduling maintenance helps avoid unexpected failures that could lead to costly repairs or downtime. By proactively monitoring hose conditions and performing timely maintenance, operators can extend hose life and keep hydraulic systems running smoothly, even in challenging cold weather conditions.
Conclusion
Selecting the right cold-resistant hoses and adopting preventive strategies are essential steps in maintaining hydraulic system efficiency, even in freezing conditions. By investing in hoses designed for low temperatures and actively managing the risks associated with cold exposure, operators can avoid costly repairs, reduce downtime, and extend the life of their equipment.
FAQ
Why is selecting cold-resistant hose material important?
Cold-resistant materials prevent hoses from becoming brittle, cracking, or losing flexibility in low temperatures, ensuring safe and reliable operation.
What temperature ratings should I look for in a cold-weather hose?
Standard cold-weather hoses are rated to -40°F to -50°F, while extreme low-temperature hoses can go as low as -65°F to -70°F for severe Arctic conditions.
How does extreme cold affect hydraulic hose pressure tolerance?
Cold temperatures can reduce a hose’s pressure tolerance, increasing the risk of bursts and leaks under high pressure. Cold-resistant hoses are designed to maintain pressure capacity in freezing conditions.
What are the benefits of insulation wraps for hydraulic hoses in cold weather?
Insulation wraps protect hoses from extreme cold, helping retain flexibility and reducing the risk of freezing in long hose runs or static applications.
How often should I inspect hoses operating in cold environments?
Regular inspections are essential, especially in freezing conditions, to check for cracks, stiffness, or surface degradation, preventing sudden hose failures.
Should I consult a specialist for selecting hoses for extreme cold?
Yes, a hose specialist can recommend the best cold-resistant hoses and protective solutions based on specific application needs and environmental conditions.