Flat couplers are designed to ensure a safe, leak-free connection between hydraulic hoses and equipment, even at high pressures. By using flat quick couplers, industries can greatly reduce the chances of fluid leakage during connection and disconnection.
Understanding Hydraulic Fluid and Its Dangers
Hydraulic fluids are essential to the operation of hydraulic systems, serving as a medium to transmit power, lubricate moving parts, and cool the system. They play a crucial role in machinery that relies on pressurized liquid to operate—whether it’s construction machinery, manufacturing equipment, or agricultural vehicles.
What is Hydraulic Fluid?
Hydraulic fluid comes in various types, each designed for specific applications. The main categories of hydraulic fluids include:
Mineral Oils: The most common type of hydraulic fluid, mineral oils are petroleum-based and have been used in hydraulic systems for decades. They offer excellent lubrication and heat transfer properties, but they can be hazardous if spilled, as they are flammable and toxic.
Water-Based Fluids: These fluids use water as the primary base, often combined with additives for rust protection and lubricity. Water-based fluids are more environmentally friendly, as they are less toxic and biodegradable compared to mineral oils. However, they tend to be less efficient in extreme temperatures and can cause corrosion in metal parts if not properly maintained.
Synthetic Fluids: Made from synthetic base oils, these fluids are engineered to offer superior performance under a wide range of conditions. They are more resistant to oxidation and offer better low-temperature fluidity. Although less flammable and more durable, synthetic fluids tend to be more expensive and require special handling to avoid contamination.
Each of these fluids has its advantages and disadvantages, but they all share one common characteristic: they are hazardous when exposed to skin or inhaled, especially under high-pressure conditions.
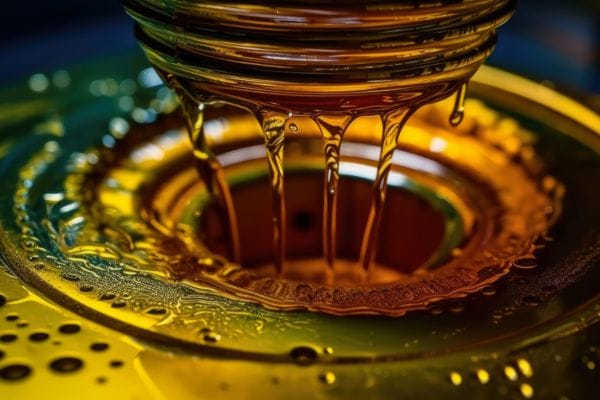
Common Hazards Associated with Hydraulic Fluids
While hydraulic fluids are critical to machinery operation, they pose a range of dangers, particularly when mishandled or when leaks occur.
Burns and Chemical Exposure: Hydraulic fluids, especially mineral oils and synthetic fluids, can cause severe burns if they come into contact with the skin, particularly when under high pressure. Pressurized fluid can penetrate the skin, leading to deep tissue damage. The chemical composition of some fluids also means that they can cause irritation, allergic reactions, or burns upon contact with the skin or eyes. For instance, many synthetic fluids contain esters that, when spilled, can burn the skin upon prolonged exposure.
Poisoning from Ingestion or Inhalation: Some hydraulic fluids, especially older mineral oils, contain toxic substances like benzene, which can lead to poisoning if ingested or inhaled. Prolonged exposure to hydraulic fluid vapors can cause headaches, dizziness, and nausea. In more severe cases, it can result in respiratory issues, neurological damage, or even death, especially in poorly ventilated areas.
Environmental Contamination from Leaks: Hydraulic fluid leaks not only pose a risk to human health but also to the environment. A leak in a hydraulic system can result in fluid spilling onto the ground or into water sources. Given the toxicity of many hydraulic fluids, such spills can harm wildlife, contaminate drinking water, and damage ecosystems. Many hydraulic systems are used in outdoor environments, such as construction sites, farms, or industrial facilities, where spills can have devastating long-term effects on soil and water quality.
Pressure-Related Injuries: One of the most dangerous aspects of hydraulic systems is the high pressure at which the fluid is often stored. A failure in the system—such as a ruptured hose or damaged coupler—can lead to the explosive release of pressurized fluid. When hydraulic fluid is forced into the skin under pressure, it can cause severe injuries. The fluid may not just cause burns but can also carry contaminants into the bloodstream, resulting in infection or even amputation if not treated immediately.
How Hydraulic Systems Operate and Why Leaks Are Dangerous
Hydraulic systems are a critical part of modern machinery, providing the power necessary for a wide range of applications, from lifting heavy loads to controlling complex production lines. The principle behind hydraulic systems is simple: they use pressurized fluid to transmit force and perform mechanical work. However, while these systems are highly efficient and versatile, they also pose significant risks—especially when hydraulic fluid leaks occur.
Overview of Hydraulic Systems
At their core, hydraulic systems rely on the transfer of energy through a liquid, typically hydraulic fluid, to perform work. The basic components that make up a hydraulic system include:
Pump: The heart of any hydraulic system, the pump is responsible for generating the flow of hydraulic fluid. It converts mechanical energy (usually from an engine or electric motor) into hydraulic energy by pressurizing the fluid. There are various types of pumps, such as gear pumps, piston pumps, and vane pumps, each suited for different applications.
Valves: Hydraulic valves control the direction, pressure, and flow rate of the fluid within the system. They ensure that the fluid is directed to the right parts of the system at the appropriate pressure and volume. Valves can be manually or automatically controlled and are essential for regulating the system’s operation.
Hydraulic Hoses and Tubes: These flexible or rigid tubes carry the pressurized fluid between different parts of the system. Hydraulic hoses are designed to withstand high pressures and are made from materials that are resistant to wear, temperature fluctuations, and chemical exposure.
Couplers: Couplers are used to connect and disconnect hydraulic hoses and other components. They are critical in ensuring a safe, leak-free connection between different parts of the system. Different types of couplers are used depending on the application, with flat face couplers being one of the most reliable options for preventing leaks during connection and disconnection.
The efficiency and safety of hydraulic systems depend on the integrity of all these components. Any failure in the system, particularly in the couplers or hoses, can lead to fluid leaks, which pose serious risks.
Hydraulic Fluid Under High Pressure
One of the defining features of hydraulic systems is that they operate under high pressure. The pressurized fluid is what enables hydraulic machinery to move large loads or perform intricate operations with precision. However, hydraulic systems often operate at pressures ranging from 1,500 to 5,000 psi (pounds per square inch) or even higher in some heavy-duty applications. At such high pressures, hydraulic fluid is capable of causing significant damage if not properly contained.
The risks of working with high-pressure hydraulic fluid are exacerbated by the fact that fluid leaks can occur unexpectedly. When hydraulic components such as hoses, valves, or couplers are improperly connected or damaged, or when they are subjected to wear and tear, they can develop leaks. These leaks can occur during routine maintenance, equipment operation, or when disconnecting hydraulic components for service. In these instances, the pressurized fluid is released suddenly, often leading to hazardous situations.
Leaks can occur for several reasons:
Worn-out seals or gaskets: Over time, seals and gaskets can degrade due to exposure to pressure, temperature, and fluid type, leading to leaks.
Improper connection: When couplers or hoses are not securely attached, the risk of leaks increases, especially when the system is under pressure.
Damaged hoses or components: Friction, abrasion, and aging can cause hoses or metal components to crack or rupture, leading to sudden leaks.
Contamination: Debris or contamination in the hydraulic fluid can wear down internal parts, leading to leaks.
The potential danger of hydraulic fluid leaks is further amplified when the system is in operation. If a leak is not detected quickly, it can lead to severe injuries, environmental contamination, or damage to machinery.
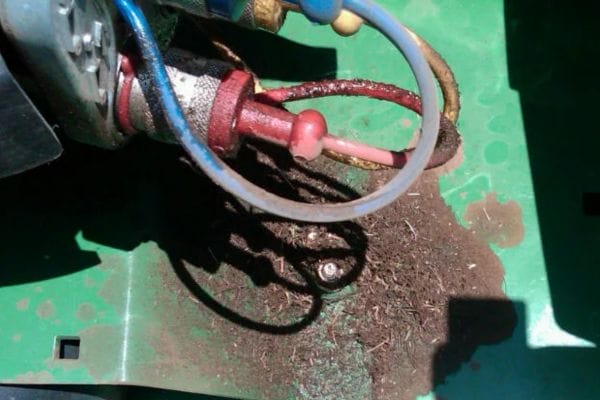
Potential Injuries from Hydraulic Leaks
Hydraulic leaks not only result in costly equipment downtime and environmental damage but also pose serious health risks to workers. The high pressure at which hydraulic fluid is stored means that even small leaks can lead to catastrophic injuries. These risks can be categorized into two main types of harm: physical harm to workers and environmental harm due to contamination.
Physical Harm (e.g., Skin Penetration, Burns): The most dangerous consequence of hydraulic fluid leaks is the potential for high-pressure fluid injection into the skin. When hydraulic fluid is released under pressure, it can penetrate the skin, carrying contaminants with it and causing severe tissue damage. This type of injury is often misdiagnosed because the entry point may be small, but the effects can be devastating, as the fluid can spread within the body and cause infection or even amputation. According to the U.S. Centers for Disease Control and Prevention (CDC), hydraulic fluid injection injuries account for a significant percentage of industrial accidents. Burns are also a common risk. Many hydraulic fluids, especially mineral oils and synthetic fluids, are highly flammable or chemically reactive, which can cause severe burns if they come into contact with the skin under high-pressure conditions.
Environmental Harm (e.g., Spills Leading to Contamination): When hydraulic fluid leaks onto the ground or into bodies of water, it can lead to severe environmental damage. Many hydraulic fluids are toxic to aquatic life and can contaminate soil and water sources, harming ecosystems and wildlife. In the construction and agricultural sectors, where hydraulic-powered machinery is used in outdoor environments, even small leaks can have widespread consequences. Spilled hydraulic fluid can seep into the ground, poisoning crops or contaminating groundwater supplies, which can have long-term negative effects on the environment and public health. Furthermore, the clean-up of hydraulic fluid spills is often expensive and labor-intensive, requiring specialized equipment and procedures to safely contain and remove the hazardous materials.
What Are Flat Face Couplings?
Flat face couplers are specialized components used in hydraulic systems to connect and disconnect hoses, valves, and other parts while preventing the leakage of hydraulic fluid. These couplers are designed to address a critical issue in hydraulic systems: fluid leakage during connection and disconnection. They are particularly valued for their safety features, especially in high-pressure applications where leaks could lead to severe injuries or environmental damage.
Definition and Design
A flat face coupler is a type of hydraulic coupling that connects two components of a hydraulic system, such as hoses or machines, through a flat mating surface. Unlike traditional hydraulic couplers that use ball-lock mechanisms or threaded connections, flat face couplers feature a flat, smooth surface that comes into direct contact when the two parts are connected. This unique design ensures that no hydraulic fluid is expelled during the connection process, minimizing the risk of spills and fluid exposure.
Flat face couplers are known for their leak-proof design, which makes them particularly effective at preventing hydraulic fluid from escaping, a significant improvement over other types of couplers. They are widely used in applications where safety is paramount, such as in construction, agriculture, and industrial machinery, where the risk of fluid leaks leading to accidents is high.
There are a few key differences between flat face couplers and other common types of hydraulic couplers:
Ball-Lock Couplers: Ball-lock couplers use internal ball mechanisms to secure the two halves of the coupler. While they are widely used due to their quick connect and disconnect features, they can sometimes create fluid leaks during disconnection, especially if the components are under pressure. This is a significant drawback in high-risk environments.
Threaded Couplers: Threaded couplers rely on a screw mechanism to connect the parts, offering a secure connection. However, these couplers often require a longer connection and disconnection time, and like ball-lock couplers, they may not prevent fluid leakage as effectively as flat face couplers.
Flat Face Couplers: What sets flat face couplers apart is their flush, flat mating surface. When the two parts are connected, they form a solid seal that prevents fluid from escaping. This feature is crucial for maintaining safety, as it virtually eliminates the chances of spills or leaks during connection and disconnection, which are common causes of hydraulic fluid injuries.
How They Work
The primary mechanism behind flat face couplers is their symmetrical design that ensures a tight, secure seal. When the two halves of a flat face coupler are mated, their flat surfaces align perfectly, creating a seal that is less prone to leaking compared to other coupler types. This design prevents hydraulic fluid from spilling when the parts are disconnected, as there is no gap for the fluid to escape from. This is particularly beneficial in high-pressure systems where even a small amount of fluid leakage can result in serious safety hazards.
Here’s a breakdown of how flat face couplers function:
Connection Process: When two flat face couplers are connected, the fluid passages align perfectly. The flat surfaces of the male and female components come into direct contact, creating a seal. Since the fluid is contained within the coupler during connection, there is no spillage of hydraulic fluid into the surrounding environment.
Disconnection Process: One of the key features of flat face couplers is that they allow for a clean disconnection, meaning there is minimal fluid loss when the connection is undone. As the coupler halves are separated, the fluid is retained inside the coupler, reducing the risk of exposure or spills. This is especially important in preventing burns or injuries caused by pressurized hydraulic fluid.
No Check Valves Required: Many traditional couplers rely on internal check valves or spring-loaded mechanisms to prevent leaks, but flat face couplers do not need these additional parts. The design of the coupler itself inherently prevents leaks during both connection and disconnection.
Pressure Control: Because flat face couplers are specifically designed to prevent fluid from leaking at high pressures, they are capable of withstanding the demanding conditions of hydraulic systems that operate at several thousand psi. This makes them ideal for high-pressure applications, where leaks can be particularly dangerous.
By combining a simple yet highly effective design with precision engineering, flat face couplers offer an unparalleled level of leak prevention, making them a preferred choice for industries focused on safety and reliability.
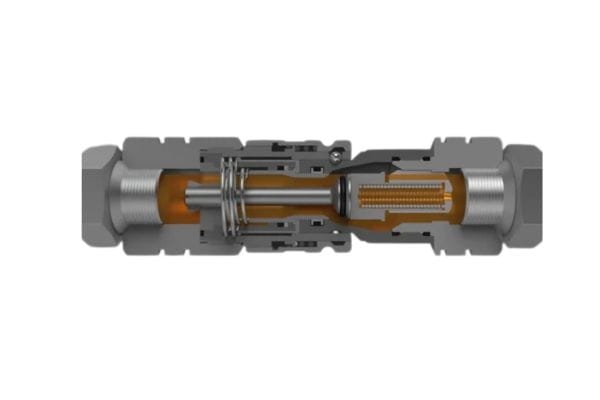
Materials and Durability
Flat face couplers are typically made from high-quality, durable materials designed to withstand the harsh conditions of hydraulic systems. These materials must be able to endure high-pressure environments, exposure to aggressive fluids, and wear and tear from frequent connections and disconnections. Some of the most common materials used in the manufacturing of flat face couplers include:
Steel: Many flat face couplers are made from high-strength steel, which is known for its ability to withstand high pressures without compromising the integrity of the coupling. Steel is also highly resistant to corrosion and damage from external forces, making it ideal for both indoor and outdoor environments.
Stainless Steel: For applications that involve corrosive fluids or are exposed to extreme weather conditions, stainless steel is often used. Stainless steel offers additional protection against corrosion, ensuring a longer lifespan and reliable performance in challenging environments, such as offshore oil rigs or agricultural machinery exposed to harsh chemicals.
Aluminum: In applications where weight is a concern, such as in mobile equipment or aerospace, aluminum may be used. Although it is lighter than steel, aluminum can still offer adequate strength and durability, provided it is appropriately treated to resist corrosion and wear.
Brass and Other Alloys: In certain applications, particularly those involving low-pressure systems or where fluid contamination is a concern, brass or specialized alloys may be used. These materials provide corrosion resistance and durability, ensuring that the couplers function effectively over time.
Key Features of Flat Face Couplers that Prevent Hydraulic Fluid Injuries
Flat face couplers have become a preferred solution in hydraulic systems due to their advanced design features that prioritize safety and minimize the risk of hydraulic fluid injuries. These couplers are specifically engineered to offer a leak-free connection that reduces the potential for hazardous fluid exposure, a critical aspect of preventing accidents and environmental damage in hydraulic applications.
Leak-Free Connection
One of the defining features of flat face couplers is their ability to create a leak-free connection during the coupling and uncoupling process. Unlike traditional couplers that may expel hydraulic fluid when disconnected or connected, flat face couplers are designed to contain the fluid securely within the coupler, preventing any spills or leaks. This leak-proof design is primarily due to the flat mating surfaces that come into direct contact when the coupler halves are joined.
Flat Mating Surfaces: The two halves of the flat face coupler feature flush, smooth surfaces that align perfectly when connected. This design ensures a tight seal without any gaps for hydraulic fluid to escape. The flush connection minimizes the potential for fluid leakage, even in high-pressure environments. When the coupler is disconnected, the pressure within the system is released in a controlled manner, and the hydraulic fluid stays inside the coupler, further reducing the risk of fluid exposure.
Minimized Fluid Spill: By preventing fluid from being expelled during connection or disconnection, flat face couplers significantly reduce the risk of injuries from the pressurized fluid. This feature is crucial because hydraulic fluids, especially at high pressures, can cause serious injuries, such as skin penetration or burns, if leaked during the coupling process. The tight seal provided by flat face couplers ensures that workers are not exposed to hazardous hydraulic fluid.
Cleaner Work Environment: A reduction in fluid leaks contributes to a cleaner, safer work environment. Fluid spills not only pose risks to personnel but also lead to environmental contamination. Flat face couplers’ leak-proof design helps maintain the integrity of both the workplace and the surrounding environment by preventing unwanted fluid spillage.
Seals and Pressure Resistance
Flat face couplers are equipped with high-quality seals that play a crucial role in preventing leaks and ensuring that the connection remains secure under high-pressure conditions. These seals are designed to withstand the mechanical stresses and temperature variations encountered in hydraulic systems.
Seals Types: The primary seals in flat face couplers are o-rings, which are circular rubber seals that fit into grooves within the coupler halves. O-rings create a tight seal between the two halves of the coupler, preventing fluid from escaping. O-rings are made from various materials, such as nitrile rubber, Viton, and polyurethane, each of which is chosen depending on the type of hydraulic fluid used, the temperature range, and the operating environment.
High-Pressure Performance: Flat face couplers are designed to perform under high-pressure conditions, typically ranging from 1,500 psi to 5,000 psi, or even higher in specialized applications. The seals within flat face couplers are engineered to resist deformation and wear under these conditions. This ensures that even in extreme pressure environments, the connection remains tight, and hydraulic fluid cannot escape.
Temperature Resistance: In addition to pressure resistance, the seals in flat face couplers are also designed to handle temperature fluctuations. Hydraulic systems often operate in environments with wide temperature ranges, from extremely cold conditions to high-heat environments. Seals made from materials like Viton or polyurethane are highly resistant to temperature variations, ensuring that they remain effective in sealing the coupler even when the temperature fluctuates.
Comparison with Other Coupler Types
When comparing flat face couplings with other common types of hydraulic couplers, their safety features stand out for their superior leak prevention and overall performance.
Push-to-Connect Couplers: These couplers are known for their quick connect and disconnect functionality. However, push-to-connect couplers can be prone to leakage, particularly if the connection is not perfectly aligned or if the coupler is disconnected under pressure. Unlike flat face couplers, they do not provide the same level of leak-proof connection, which increases the risk of fluid exposure.
Screw-On Couplers: Screw-on couplers, which rely on threaded connections to secure the components, can offer a tight seal, but they generally require more time to connect and disconnect. While they may reduce the risk of accidental disconnections, they still pose a risk of fluid leakage if the connection is not properly made or if the threads wear out over time. Additionally, screw-on couplers may not perform as well under high-pressure conditions as flat face couplers.
Ball-Lock Couplers: Ball-lock couplers are quick-connect devices commonly used in hydraulic systems, but they can sometimes result in fluid spillage, particularly when disconnected under pressure. The ball-lock mechanism is not as effective in preventing fluid leaks as the flat face design, which creates a more reliable and leak-proof connection. Ball-lock couplers also require more maintenance to ensure that the locking mechanism remains intact and fully functional.
Conclusion
Now is the time to assess your current hydraulic systems and consider whether flat face couplers could offer a safer, more reliable solution. For more information, explore Topa manufacturer websites or refer to safety guidelines that provide in-depth resources on hydraulic safety practices.
FAQ
What are flat face couplers?
Flat face couplers are hydraulic connectors designed to prevent fluid leakage during connection and disconnection. Their flat mating surfaces ensure a leak-proof seal, reducing the risk of hydraulic fluid exposure.
How do flat face couplers prevent hydraulic fluid injuries?
These couplers create a tight, leak-free connection by aligning flat surfaces during coupling, which prevents fluid from spilling. They are especially useful in high-pressure systems where fluid leaks could lead to serious injuries.
What types of seals are used in flat face couplers?
Flat face couplers typically use o-rings made from materials like nitrile rubber, Viton, or polyurethane, which offer excellent sealing capabilities under high pressure and varying temperatures.
Can flat face couplers withstand high-pressure environments?
Yes, flat face couplers are designed to handle high-pressure environments, often up to 5,000 psi or more, without compromising the integrity of the seal.
How do flat face couplers differ from other types of hydraulic couplers?
Unlike ball-lock or screw-on couplers, flat face couplers offer a leak-proof connection and prevent fluid spills during both connection and disconnection, making them safer and more reliable in high-pressure systems.
Why should I upgrade to flat face couplers?
Upgrading to flat face couplers can significantly reduce the risk of hydraulic fluid leaks, ensuring a safer work environment and minimizing environmental contamination. It’s an essential step for improving hydraulic system safety.