Selecting the correct hydraulic coupling is critical for ensuring system efficiency and safety. Couplings that are incorrectly sized or incompatible with the system’s operating conditions can lead to pressure drops, leaks, contamination, or even catastrophic system failures. In high-pressure hydraulic systems, the consequences of a coupling failure could be severe, potentially resulting in fluid injection injuries or damage to expensive equipment.
Understanding Quick Coupling Basics
Definition and Function
Quick couplings, also referred to as quick-connect or quick-disconnect fittings, are specialized connectors designed to rapidly join and separate fluid or airlines without the need for additional tools. They consist of two parts: the male (plug) and female (socket) ends, which, when connected, create a secure seal to allow fluid or air to flow freely. When disconnected, integrated check valves or seals prevent any fluid from leaking or spilling. Quick couplings are widely used in both hydraulic and pneumatic systems, offering a convenient and efficient way to maintain equipment, replace components, or perform routine inspections.
In hydraulic systems, quick couplings are crucial for managing the transfer of pressurized fluids like oil. In pneumatic systems, they regulate compressed air flow, ensuring smooth operations in machinery and equipment. Their primary function is to allow operators to connect and disconnect lines easily, improving operational flexibility and reducing downtime during maintenance. Additionally, quick couplings prevent contamination and fluid loss, which is essential in industries where cleanliness and efficiency are critical.
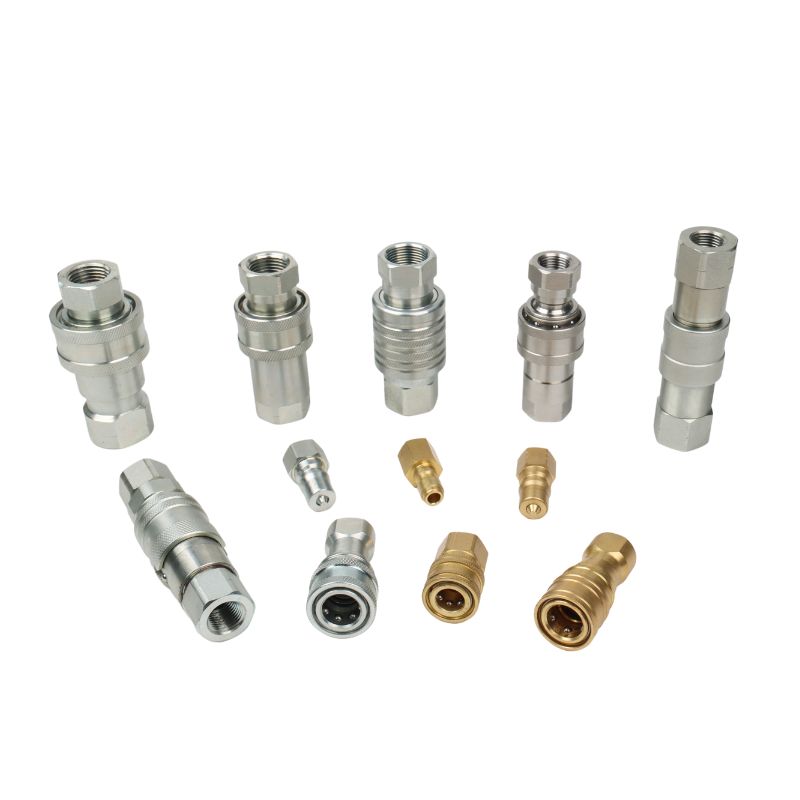
Types of Quick Couplings
There are several types of quick couplings, each designed for specific applications and operating conditions:
Ball-check or Poppet-style Couplings:
These couplings feature a spring-loaded ball or poppet that seals off the fluid path when disconnected. When connected, the balls or poppets push against each other, allowing fluid to flow. They are widely used in hydraulic systems due to their straightforward design and cost-effectiveness. However, these couplings tend to create higher pressure drops and are more prone to leakage compared to other designs.
Flat-face Couplings:
Flat-face couplings have a more advanced design that eliminates internal cavities where fluid or air might be trapped, reducing the risk of spillage or contamination during disconnection. When connected, the flat faces of the male and female ends come together to create a large flow path with minimal pressure drop. These couplings are commonly used in high-pressure hydraulic systems where clean, efficient fluid transfer is critical. They are also known for their durability and ability to handle high flow rates.
Thread-to-Connect Couplings:
These couplings are designed with threads on the male and female sides, which must be tightened together to create a secure seal. Thread-to-connect couplings are typically used in high-pressure applications because they provide a very strong and reliable connection. However, they are more time-consuming to connect and disconnect compared to other types of quick couplings.
Applications in Different Industries
Quick couplings are versatile components used across a wide range of industries, each with specific requirements:
Construction: In heavy machinery like excavators and bulldozers, quick couplings allow for the rapid change of hydraulic attachments such as hammers, buckets, and drills. This improves efficiency and minimizes downtime during equipment changeovers.
Agriculture: Quick couplings are essential for connecting hydraulic lines on tractors and other farming equipment. They help in transferring hydraulic power to various implements, such as plows, harrows, and seeders, making farm operations more productive.
Automotive: In automotive manufacturing and repair, quick couplings are used to connect air tools and pneumatic systems. Their quick connection capability speeds up maintenance tasks and ensures high levels of safety and reliability.
Manufacturing: In industrial manufacturing, quick couplings are found in hydraulic systems that power assembly lines, presses, and injection molding machines. Their ease of use allows for rapid maintenance and minimizes downtime, which is critical in high-output environments.
Factors to Consider When Specifying Quick Couplings
Selecting the correct quick coupling is a vital decision for ensuring that a hydraulic or pneumatic system operates efficiently and safely. To avoid costly mistakes, it’s important to consider several key factors when specifying quick couplings.
Flow Capacity and Size
Choosing the Right Size for Maximum Flow Efficiency
Quick couplings must be appropriately sized to ensure that the system operates at peak efficiency. The coupling size should not be determined based solely on the hose’s diameter; instead, it must be sized according to the flow requirements of the system. Hydraulic and pneumatic systems are designed to move fluids (liquids or gases) at specific flow rates, and undersized couplings can create bottlenecks, leading to pressure drops and reduced system performance.
For instance, if a system is designed to move 8 gallons per minute (GPM) of hydraulic fluid, but the coupling is only rated for 4 GPM, the coupling will limit the system’s performance. This mismatch can increase the backpressure in the system, leading to inefficiencies and potential damage to components over time.
Why the Coupling Should Not Always Match Hose Size
The coupling’s internal diameter, which affects the flow path, is not always equal to the hose size. A common mistake is to select a coupling that matches the thread or outer diameter of the hose, assuming that this would optimize flow. However, the flow rating of a coupling depends on its internal construction and how it handles fluid flow, not just the connection size. This is particularly important when working with high-pressure systems, as smaller couplings can increase pressure drop and decrease the overall efficiency.
Examples of Flow Rates
A 3/8-inch quick coupling typically flows about 4 GPM at 20 psi of backpressure, while a 1/2-inch coupling might flow 10-12 GPM. Selecting the correct coupling size based on flow needs is crucial to avoid flow restrictions that can affect the entire system’s performance.
In pneumatic systems, selecting a coupling based on the air tool’s required cubic feet per minute (CFM) is equally critical, as using an undersized coupling can reduce the power delivered to the tool and increase energy consumption.
Pressure Ratings
Matching the Pressure Rating of the Coupling to the System
The pressure rating of a quick coupling must align with that of the system. Hydraulic and pneumatic systems often operate under high pressure, and mismatched pressure ratings can lead to coupling failures, leaks, or even safety hazards such as fluid injection injuries.
Hydraulic systems: Many hydraulic systems operate at pressures up to 3,000 psi, but high-pressure applications can exceed 5,000 psi. It is essential to use couplings rated for these pressures, as underspend couplings may fail under the load, leading to dangerous fluid bursts or system downtime.
Pneumatic systems: While pneumatic systems typically operate at lower pressures (e.g., 100-150 psi), using a coupling rated for too low a pressure could still result in air leaks or hose whip, especially if the pressure spikes unexpectedly.
Consequences of Using a Coupling with a Lower Pressure Rating
If the coupling’s pressure rating is lower than that of the system, the weakest link in the system will be the coupling. For example, if a system runs at 5,000 psi but the coupling is rated for 4,000 psi, the coupling could fail under pressure. Failure could occur as a catastrophic rupture, leading to equipment damage, fluid leaks, and serious injuries. Additionally, over time, operating couplings close to or above their maximum pressure rating leads to increased wear, reduced lifespan, and higher maintenance costs.
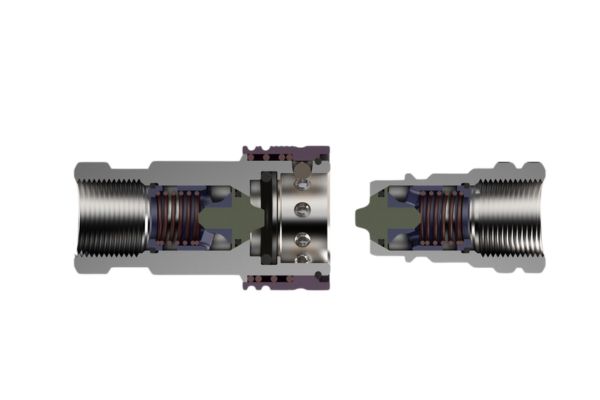
Connection Mechanism
Quick couplings come with various connection mechanisms, each offering different benefits in terms of ease of use, security, and leak prevention.
Push-to-Connect Couplings
These couplings allow for fast, tool-free connections. By simply pushing the male end into the female socket, the connection is made, and fluid or air can flow immediately. This type of coupling is commonly used in pneumatic systems and low- to medium-pressure hydraulic applications where frequent disconnections are required.
Advantages: Extremely easy to use, quick to connect/disconnect, and ideal for frequent cycling applications.
Drawbacks: Less secure than other designs, making them unsuitable for high-pressure applications.
Threaded Couplings
Threaded couplings use male and female threads to create a secure connection. They are typically used in high-pressure hydraulic systems because the threads provide a strong, reliable seal.
Advantages: Very secure and able to withstand high pressures and extreme conditions.
Drawbacks: Slower to connect and disconnect due to the need to tighten or loosen threads.
Screw-In Couplings
Screw-in couplings provide an even more secure connection than push-to-connect designs and are often found in applications where high pressure or extreme vibrations occur.
Advantages: High resistance to accidental disconnection and excellent for use in high-vibration environments.
Drawbacks: Slightly more complex and time-consuming to connect/disconnect compared to push-to-connect couplings.
Material Compatibility
Selecting the appropriate material for quick couplings is critical, especially in systems where fluids are corrosive, or environmental factors like temperature extremes are present. Different materials offer distinct benefits and drawbacks:
Steel: Strong and durable, steel couplings are well-suited for high-pressure hydraulic applications. However, they are prone to corrosion in harsh environments if not protected by coatings such as zinc or chrome.
Brass: Brass couplings are often used in pneumatic systems and lighter-duty hydraulic applications. Brass offers excellent corrosion resistance in many environments, but it is not suitable for high-pressure applications.
Stainless Steel: Resistant to both corrosion and extreme temperatures, stainless steel couplings are ideal for applications where harsh chemicals or seawater are present. They are also highly durable and can withstand higher pressures than brass.
Aluminum: Lightweight and corrosion-resistant, aluminum couplings are used in applications where weight savings are essential, such as aviation. However, they are not suitable for high-pressure applications due to their lower strength.
Environmental Factors
When selecting materials, it’s essential to consider temperature extremes, fluid compatibility, and corrosive environments. For instance, stainless steel couplings might be preferred in chemical plants, while brass may be more suitable for general-purpose pneumatic tools.
Selecting Quick Couplings for Specific Applications
Mobile Equipment (Construction, Agriculture)
Mobile equipment in construction and agriculture places unique demands on hydraulic systems due to the harsh environments, heavy loads, and frequent equipment changeovers. Quick couplings play a crucial role in ensuring the efficiency and reliability of these machines by enabling fast and secure connections between hydraulic hoses and attachments.
Flat-face couplings vs. Ball-check couplings:
In mobile machinery, flat-face couplings are generally preferred over ball-check couplings. Flat-face couplings offer several advantages that are critical in outdoor environments, including reduced spillage and contamination risk. Since these couplings eliminate internal cavities where dirt or debris could enter, they help maintain system cleanliness, which is vital when working in dusty or dirty environments, such as construction sites or agricultural fields.
On the other hand, ball-check couplings may be used in less demanding mobile applications where cost is a factor, but they are more prone to leaks and contamination. The ball or poppet design creates flow restrictions and increases the risk of internal wear from contaminants, making them less reliable in mobile equipment exposed to rough conditions.
Best choice: Flat-face couplings are ideal for mobile equipment due to their durability, spill-free operation, and ability to handle the high-flow demands of hydraulic systems in construction and agriculture.
High-Pressure Hydraulic Systems
In high-pressure hydraulic systems, such as those operating at 5,000 psi or higher, quick coupling selection becomes even more critical to ensure safety and system integrity. These systems are often found in heavy-duty industrial equipment, oil and gas operations, and specialized machinery that requires precise control under extreme pressure.
Choosing the right quick coupling:
For high-pressure systems, thread-to-connect couplings are typically the best choice. Their threaded design allows for a secure and leak-free connection that can withstand extreme pressures. These couplings prevent accidental disconnection, which is crucial in environments where pressure surges could lead to catastrophic failures.
Safety considerations:
When specifying quick couplings for high-pressure applications, it’s essential to match the pressure rating of the coupling with that of the system. Using a coupling with a lower pressure rating than the rest of the hydraulic system can lead to system failures, fluid leaks, and potential safety hazards, such as oil injection injuries. Additionally, selecting couplings with safety features like sleeve locks or pressure-relief valves can further reduce the risk of failure.
Another critical factor is minimizing pressure drops. Pneumatic systems are sensitive to pressure losses, so couplings designed for minimal air loss during disconnection, such as flat-face or non-spill designs, are ideal. These designs help maintain consistent air pressure throughout the system, ensuring that tools and machinery perform at optimal levels.
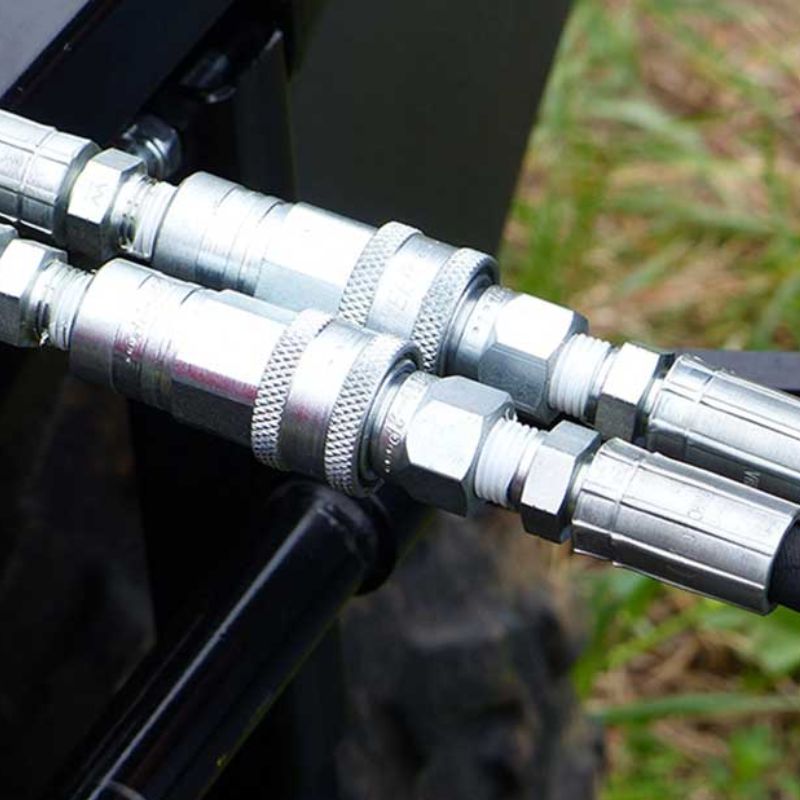
Frequent Connection and Disconnection Applications
Certain industries, such as testing, medical equipment, and food processing, require quick couplings that can handle frequent cycling without compromising system integrity. In these applications, couplings need to be highly durable and easy to connect and disconnect multiple times a day.
Industries requiring rapid connections:
Testing facilities: In industries where hydraulic or pneumatic testing is common, such as automotive or aerospace, operators frequently connect and disconnect hoses to perform various tests. Quick couplings that are easy to operate and maintain under repeated use are essential in these settings.
Medical equipment: In medical environments, non-spill quick couplings are critical to prevent contamination and ensure that fluids such as oxygen or sterilized air are not exposed to external contaminants during disconnection.
Food processing: Cleanliness and ease of disconnection are vital in food processing. Quick couplings that can be quickly cleaned and reconnected help streamline production while maintaining safety standards.
Best coupling types for frequent cycling:
Non-spill designs and flat-face couplings are ideal for applications that require frequent connection and disconnection. These couplings ensure minimal fluid or air loss, reduce contamination risks, and provide durable, long-lasting performance even under high-frequency usage. In industries where hygiene and precision are critical, such as medical or food processing, non-spill designs offer the added benefit of preventing fluid spills that could compromise the cleanliness of the operation.
Common Mistakes When Specifying Quick Couplings
Choosing the right quick coupling for a hydraulic or pneumatic system requires careful consideration of multiple factors. However, several common mistakes can lead to reduced performance, system failures, or even safety hazards.
1. Undersizing Couplings
A common mistake when specifying quick couplings is matching the size of the coupling to the hose diameter, rather than the system’s flow requirements. While it might seem intuitive to choose a coupling based on the size of the hose, this approach can lead to flow restrictions. The coupling’s internal design often dictates how much fluid or air can pass through, and undersized couplings may create bottlenecks in the system.
For example, a 3/8-inch coupling might have an internal flow capacity of 4 GPM at a certain pressure, but the system may demand higher flow rates that require a larger coupling. By matching couplings solely to the hose size, operators may inadvertently limit flow efficiency, causing increased backpressure and strain on the system.
Solution: Always select couplings based on the flow capacity needed for the application, considering both fluid type and operational pressure. Manufacturers provide flow ratings for couplings, making it easier to match the coupling’s performance to the system’s needs.
2. Ignoring Pressure Ratings
Another critical error is mismatching the pressure rating of the quick coupling with that of the system. Hydraulic and pneumatic systems often operate under specific pressure conditions, and if a coupling cannot handle the system’s maximum pressure, it can fail catastrophically.
For example, using a coupling rated for 3,000 psi in a system that operates at 5,000 psi can lead to coupling failure, resulting in fluid leaks, equipment damage, or safety hazards such as fluid injection injuries. In pneumatic systems, pressure mismatches can cause air leaks and create hose whip, which poses serious risks to operators.
Solution: Always verify the system’s maximum operating pressure and ensure that the couplings have a pressure rating equal to or greater than the system’s pressure. Overestimating safety margins by selecting higher-rated couplings is often a wise choice in high-pressure environments.
3. Selecting Based on Cost Alone
Cost is a significant factor when choosing quick couplings, but prioritizing cheaper options over performance can lead to long-term issues. Lower-cost couplings may use inferior materials that are prone to corrosion, wear, and leaks. In mobile or outdoor applications, for example, cheaper couplings made from low-grade materials can rust quickly or fail under constant use, resulting in frequent replacements and costly downtime.
Cheaper couplings may also have poor sealing mechanisms, increasing the risk of leaks. These leaks can reduce system efficiency, increase maintenance costs, and in some cases, pose environmental or safety risks, especially if the system handles hazardous fluids.
Solution: While cost is an important factor, it’s essential to consider the long-term performance of the coupling. Investing in high-quality couplings made from durable materials, such as stainless steel for corrosive environments, may offer better value over time by reducing maintenance costs and improving system reliability.
4. Failure to Consider Environmental Factors
When specifying quick couplings, many users overlook environmental factors that can affect performance, such as temperature, corrosion, and fluid compatibility. In harsh environments—such as chemical plants, construction sites, or food processing facilities—couplings are often exposed to extreme conditions that can degrade materials over time.
For instance, using a standard steel coupling in a marine environment can lead to rapid corrosion, while operating at extreme temperatures may cause seals to fail if they aren’t made from suitable materials like Viton or Teflon. Similarly, some fluids may react with the materials used in the coupling, leading to contamination or degradation of the coupling itself.
Solution: Always assess the environmental conditions in which the coupling will operate. Corrosion-resistant materials such as stainless steel or aluminum should be used in corrosive environments, while specialized seals may be required for high-temperature or chemically aggressive fluids. Additionally, ensure that the coupling materials are compatible with the specific fluid used in the system.
Conclusion
Choosing the wrong quick coupling can lead to costly inefficiencies, leaks, or even dangerous system failures. By thoroughly evaluating the unique requirements of your system and considering the factors discussed—such as size, pressure, material, and environmental compatibility—you can ensure that your system operates at peak efficiency. Remember, quick couplings are not one-size-fits-all components, and attention to detail in the specification process will prevent future issues.
FAQ
What are quick couplings used for?
Quick couplings are used in hydraulic and pneumatic systems to connect and disconnect fluid lines quickly without the need for tools. They prevent leaks and ensure efficient fluid transfer, especially in mobile equipment, high-pressure systems, and industrial machinery.
How do I choose the right size for a quick coupling?
Choose the coupling size based on the flow capacity required, not just the hose diameter. Undersized couplings can restrict flow, creating pressure drops and reducing system efficiency. Always check the flow rating provided by the manufacturer.
What is the significance of pressure ratings in quick couplings?
The pressure rating of a quick coupling must match or exceed the system’s operating pressure. Using a coupling with a lower pressure rating can result in leaks, system failure, or safety hazards, especially in high-pressure hydraulic systems.
What materials are commonly used in quick couplings, and how do I choose?
Quick couplings can be made from steel, brass, stainless steel, or aluminum. The choice depends on the operating environment—for example, stainless steel is ideal for corrosive or high-temperature applications, while brass is more suited for general pneumatic systems.
What are flat-face couplings, and why are they popular?
Flat-face couplings are designed to prevent fluid spillage during connection and disconnection. They are ideal for high-pressure systems, mobile machinery, and environments where contamination control is essential.
Can I use the same quick coupling for hydraulic and pneumatic systems?
While some quick couplings can be used in both systems, it is crucial to ensure that the coupling is rated for the specific pressure, flow, and fluid type of each system. Pneumatic systems typically operate at lower pressures and may require different sealing mechanisms than hydraulic systems.