Common issues with hydraulic cylinder fittings include leaks, corrosion, wear and tear, and improper sealing. These problems can lead to decreased system pressure, fluid loss, and inefficient operation, often requiring immediate repair or replacement to avoid further damage to the hydraulic system.
Signs You Need a Hydraulic Cylinder Fitting Repair
Recognizing Hydraulic Fitting Leaks
One of the most common signs that your hydraulic cylinder fitting needs repair is the presence of leaks. Leaking hydraulic fluid can often be seen around the fitting area or noticed as wet spots on the ground beneath the equipment. A decrease in fluid levels can also indicate a leak, which, if left untreated, can severely affect the system’s pressure and performance.
Performance Loss in Hydraulic Systems
If your hydraulic equipment is experiencing slower operation, inconsistent movements, or reduced force output, this could signal an issue with the cylinder fittings. Performance loss often occurs when fittings fail to maintain proper fluid pressure, leading to inefficient system operation. This may result in your machinery working harder, consuming more energy, and producing less effective results.
Visual Indicators of Wear and Tear on Hydraulic Fittings
Over time, hydraulic fittings are exposed to high pressure, temperature fluctuations, and harsh environmental conditions. Inspecting the fittings for visible signs of damage such as cracks, corrosion, or wear on the seals can indicate the need for repair. Discoloration, rust, or swelling around the fitting area are clear indicators that the fitting is no longer functioning properly and requires attention.
Step 1 – Identifying the Issue with Your Hydraulic Cylinder Fitting
How to Detect Hydraulic Fitting Leaks
The first step in identifying an issue with your hydraulic cylinder fitting is detecting any leaks. Start by visually inspecting the fittings for wet spots or visible signs of hydraulic fluid around the connection points. You can also use a piece of clean paper or cloth to wipe around the fittings; if it comes away damp, a leak is likely present. Another effective method is to use a leak detection dye or UV light to spot even the smallest leaks, especially in hard-to-see areas. Listening for a hissing sound, which indicates escaping air or fluid, can also help pinpoint the source of the leak.
Troubleshooting Hydraulic Cylinder Problems
Once a leak or fitting issue is suspected, the next step is troubleshooting the hydraulic cylinder. Check for any irregularities in system pressure, temperature fluctuations, or sluggish movements of the hydraulic cylinder. These signs often point to problems with the hydraulic fluid flow, which is directly affected by the condition of the fittings. Performing a pressure test using a gauge can help assess whether the hydraulic system is maintaining the required pressure. Additionally, listen for abnormal sounds, such as whining or grinding, which may indicate a faulty fitting or damaged cylinder components.
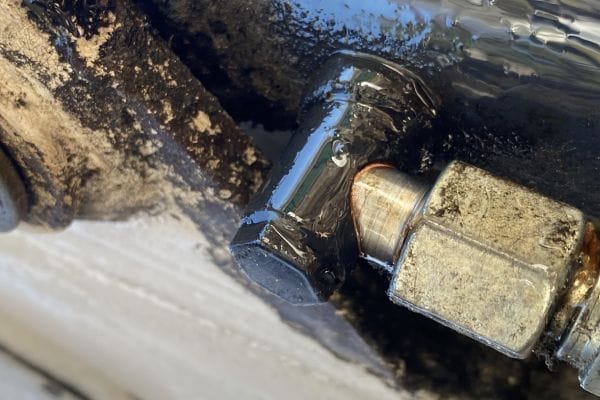
Assessing the Severity of the Fitting Issue
Once you’ve identified the potential problem, it’s important to assess how severe the issue is. Minor leaks might be fixed with a simple tightening or sealing, while more significant leaks or visible cracks in the fitting may require replacement. Check the condition of the seals and O-rings to determine if they have worn out or cracked, as this is often the root cause of leaks. If the hydraulic cylinder is experiencing a major loss of performance or if the fittings show signs of severe wear, it’s crucial to address the issue immediately to prevent further damage to the entire system. Keep in mind that early detection and repair can help avoid costly downtime and extensive repairs down the line.
Step 2 – Disassembling the Hydraulic Cylinder Fitting
How to Properly Disassemble Hydraulic Cylinder Fittings
Disassembling hydraulic cylinder fittings requires careful attention to avoid causing additional damage to the parts. Start by relieving the pressure in the hydraulic system to ensure safety. Disconnect the hydraulic hose from the cylinder, making sure the fluid is drained or contained properly to prevent spills. Use the appropriate wrenches or sockets to loosen the fittings, starting with the outer components and working your way inward. Always take note of the order in which parts are removed, as this will help during reassembly. If the fitting is stubborn, use penetrating fluid to ease the disassembly process without damaging the threads or seals.
The Right Tools for Safe Disassembly
Having the right tools is essential for a safe and efficient disassembly process. Common tools needed for hydraulic cylinder fitting disassembly include:
Hydraulic wrenches or spanners: For loosening large or tightly secured fittings.
Torque wrenches: To ensure that fittings are removed with the correct force, preventing thread damage.
Pliers or pipe wrenches: For gripping and loosening smaller components.
Seal pick or scraper: For carefully removing old seals without scratching the fitting or cylinder surfaces.
Penetrating oil or lubricant: To loosen stuck fittings and prevent corrosion.
Hydraulic fluid container: To safely drain and store hydraulic fluid during the disassembly process.
Ensure that all tools are in good condition and suitable for the specific size and type of fittings you’re working with. Using the correct tools will make the process safer and more efficient, while reducing the risk of damaging critical components.
What to Look for While Disassembling Hydraulic Cylinders
As you disassemble the hydraulic cylinder fittings, inspect the components for signs of wear or damage. Look for:
Worn or damaged seals: Cracked, hardened, or deteriorated seals are a common cause of leaks.
Corrosion or rust: Any signs of rust or corrosion on the fittings or cylinder should be noted, as they can compromise the hydraulic system’s performance.
Cracks or fractures in the fitting: Check for visible cracks or deformation in the fitting parts, which can lead to failure during reassembly or operation.
Thread damage: Examine the threads on both the fittings and the cylinder to ensure they are not stripped or damaged. Thread issues can cause improper sealing or difficulty in reassembly.
Debris or contaminants: Make sure that no dirt, debris, or old sealant remains inside the fitting area, as this can affect the functionality of the hydraulic system and lead to further damage.
Step 3 – Inspecting Hydraulic Cylinder Parts
Common Problems Found in Hydraulic Cylinder Fittings
When inspecting hydraulic cylinder fittings, several common issues can arise, leading to inefficiencies or system failure:
Leaking Fittings: The most frequent issue is leakage, which can occur due to improper sealing or worn-out O-rings. Leaking fittings reduce the system’s pressure and performance, leading to fluid loss and potential system failure.
Corrosion and Rust: Exposure to moisture, chemicals, or harsh environments can cause corrosion on the fitting surfaces. This can weaken the fittings, lead to leaks, and cause them to fail prematurely.
Cracks and Fractures: Over time, hydraulic fittings can develop small cracks due to stress, excessive pressure, or fatigue. Cracks are particularly dangerous, as they can cause catastrophic failure of the system.
Clogging and Debris: Dirt, debris, or old sealant left behind can block fluid flow or cause increased wear on the fitting surfaces. These obstructions can affect system performance and result in overheating or excessive wear.
Excessive Wear on Threads: Frequent disassembly and assembly can cause thread damage, making it difficult to properly seal the fitting. Worn threads can also compromise the connection between the fitting and the hydraulic cylinder.
Identifying Worn or Damaged Hydraulic Seals
Seals play a crucial role in maintaining a leak-proof connection and ensuring proper fluid flow within hydraulic systems. Here’s how to identify worn or damaged seals:
Cracked or Brittle Seals: Over time, seals made from rubber or elastomers can dry out, crack, or become brittle, particularly if exposed to high heat, extreme pressure, or chemicals. A cracked seal will no longer provide an effective barrier against fluid leakage.
Deformation or Swelling: Seals that appear swollen, misshapen, or out of place could indicate that they have been over-extended, exposed to high temperatures, or exposed to incompatible fluids. Such seals should be replaced immediately to prevent leaks.
Visible Gaps or Tears: Examine the seals for any visible tears, gaps, or breakage. Even minor cuts or deformities can cause significant leaks and loss of hydraulic pressure. These damaged seals will need to be replaced to maintain system integrity.
Compression Set: If the seals appear compressed and no longer bounce back to their original shape, it may indicate they have become “set” from prolonged exposure to pressure or heat. This reduces their sealing capability and necessitates a replacement.
Step 4 – Repairing or Replacing Damaged Fittings
How to Repair Hydraulic Cylinder Fittings
Repairing hydraulic cylinder fittings involves addressing any damage, wear, or leaks in the components to restore the system’s integrity. Here’s how to approach the repair process:
Clean the Fitting Area: Before starting the repair, ensure the fitting and surrounding area are thoroughly cleaned of dirt, debris, or old sealant. This prevents contaminants from interfering with the repair and ensures a proper seal when reassembling.
Tighten Loose Fittings: If the issue is a loose connection causing a leak, use the correct torque settings to tighten the fitting. Over-tightening can damage the threads or cause other components to crack, so always follow manufacturer specifications for torque.
Replace Worn Seals: One of the most common causes of hydraulic fitting failure is damaged or worn seals. Use a seal pick to carefully remove the old seals and replace them with new, compatible ones. Ensure that the new seals are installed correctly and seated evenly to avoid leaks.
Patch Minor Cracks or Surface Damage: If the fitting shows signs of minor surface wear or small cracks, you may be able to use a special hydraulic repair adhesive or patch to seal the cracks temporarily. However, this is not a permanent solution and should only be done for short-term fixes until the fitting can be replaced.
Use Hydraulic Thread Sealant: For leaking threaded connections, apply a quality hydraulic thread sealant to ensure a tight seal. Be sure to follow the manufacturer’s instructions on the sealant, and avoid over-applying, as excess sealant can block fluid flow or create obstructions.
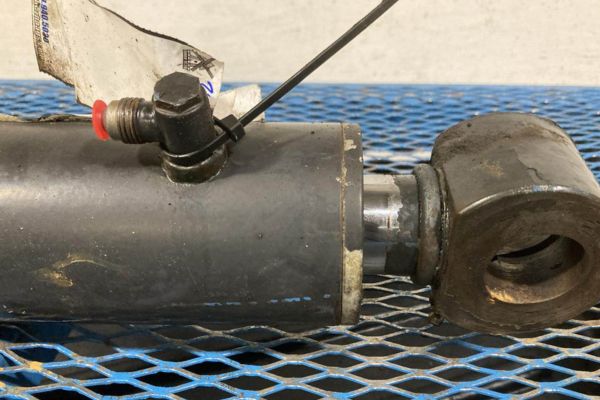
When to Replace a Hydraulic Cylinder Fitting
While repairing hydraulic cylinder fittings is possible, there are cases where replacement is necessary. Here’s when to consider replacing a fitting rather than repairing it:
Severe Cracks or Fractures: If the fitting has visible cracks or fractures, it’s likely beyond repair. Cracks can compromise the fitting’s structural integrity, causing future leaks or even catastrophic failure, making replacement the best option.
Significant Corrosion or Rust: Corroded fittings that are beyond cleaning or buffing should be replaced immediately. Corrosion weakens the metal and compromises the fitting’s ability to withstand high pressure, making it unsafe to use.
Excessive Thread Damage: If the threads on the fitting are stripped, damaged, or have worn down significantly, they may no longer create a secure seal. In such cases, the fitting should be replaced to maintain the system’s reliability.
Repeated Leaks or Persistent Performance Issues: If you’ve already attempted a repair, such as replacing seals or tightening fittings, but the leak persists or performance issues remain, replacement is often the most cost-effective solution. Continuing to repair a repeatedly failing fitting may lead to bigger issues down the road.
Outdated or Obsolete Fittings: Older fittings may no longer meet current safety standards or could be incompatible with modern hydraulic components. In this case, replacing outdated fittings with newer, more efficient models is necessary to keep the system running smoothly.
Step 5 – Sealing Hydraulic Fittings Properly
Best Practices for Sealing Hydraulic Fittings to Avoid Leaks
Properly sealing hydraulic fittings is critical to maintaining the integrity of the hydraulic system and preventing leaks that can cause performance issues or equipment damage. Here are the best practices for sealing hydraulic fittings effectively:
Use the Correct Seal Type: Always ensure that you use the appropriate seals for the type of hydraulic fitting you are working with. O-rings, flat seals, and backup rings are common choices, each designed for specific applications and pressures. Verify the material of the seals to ensure compatibility with the hydraulic fluid and operating conditions (e.g., temperature, pressure, and chemical exposure).
Clean Surfaces Before Sealing: Ensure that the sealing surfaces of both the fitting and the cylinder are free of debris, dirt, and old sealant. Contaminants can compromise the seal, causing leaks. Use a solvent and a clean cloth to wipe the surfaces clean before applying new seals or sealant.
Lubricate the Seals: Apply a light coating of hydraulic fluid or a compatible lubricant to the new seals before installation. Lubrication prevents damage during installation and helps the seals form a tight, leak-proof barrier. Avoid over-lubricating, as excess lubricant can create a mess and potentially cause contaminants to enter the system.
Install Seals Correctly: Ensure that the seals are installed in the correct orientation. For O-rings, this means ensuring the ring sits evenly in the groove without being pinched or twisted. Flat seals should be placed squarely in the sealing area, and backup rings should be oriented in the direction that prevents extrusion.
How to Apply Hydraulic Sealants Effectively
In some cases, using hydraulic sealant in addition to seals can provide an extra layer of protection against leaks. Here’s how to apply hydraulic sealants effectively:
Choose the Right Sealant: Select a sealant designed for hydraulic systems. There are different types of hydraulic sealants, including thread sealants, anaerobic sealants, and gasket sealants, each suitable for specific applications. Ensure the sealant is compatible with the hydraulic fluid and operating conditions.
Clean the Fitting and Thread: Before applying sealant, clean the threads and surfaces of the fitting thoroughly to remove any dirt, grease, or old sealant. This ensures the sealant bonds properly and does not trap contaminants that could damage the system.
Apply Sealant Sparingly: When applying sealant to threaded connections, apply a thin, even layer to the male threads of the fitting. Be careful not to over-apply, as excess sealant can block fluid flow and potentially damage the system. For flat seals or gasketed areas, apply sealant to both surfaces evenly.
Allow Sealant to Cure: Some hydraulic sealants require curing time to achieve full bonding strength. Follow the manufacturer’s instructions regarding curing time before pressurizing the system. Rushing this step can lead to premature failure of the seal.
Conclusion
In conclusion, repairing hydraulic cylinder fittings is a critical task that ensures the efficiency and longevity of your hydraulic system. By following the step-by-step process—identifying issues, disassembling the fittings, inspecting parts, and properly sealing the system—you can address leaks and performance issues effectively.
FAQ
What are the common signs that my hydraulic cylinder fitting needs repair?
Look out for hydraulic fluid leaks, a decrease in system performance, unusual noises, or visible wear and tear around the fittings.
Can I repair hydraulic cylinder fittings myself?
Yes, with the right tools and knowledge, you can perform DIY hydraulic fitting repairs. However, ensure you follow safety protocols and use quality parts.
How often should hydraulic cylinder fittings be inspected?
It’s recommended to inspect hydraulic cylinder fittings regularly—ideally every 6 to 12 months—depending on usage, to identify early signs of wear or leaks.
What tools are needed for hydraulic cylinder fitting repair?
Common tools include wrenches, seal pickers, torque wrenches, thread sealants, cleaning solvents, and new seals or O-rings.
How can I prevent leaks in hydraulic cylinder fittings?
Regularly check for wear, replace seals as needed, use proper sealant, and ensure all fittings are tightly secured with correct torque.
When should I replace a hydraulic cylinder fitting instead of repairing it?
Replace the fitting if it has visible cracks, significant corrosion, severe thread damage, or repeated leaks that can’t be fixed through regular repairs.