Hydraulic cylinders are the powerhouses of industry, delivering essential force and precision. However, operational shock and vibration pose significant threats, risking damage, downtime, and inaccuracy. High-precision, shock-resistant cylinders provide resilience for demanding applications where standard solutions fail. This article explores the advanced design principles, critical applications, and inherent benefits of these specialized components, demonstrating how robust engineering conquers harsh conditions to ensure optimal performance, safety, and longevity in modern hydraulic systems.
Understanding Shock and Vibration in Hydraulic Systems
Defining Shock and Vibration
Shock refers to a sudden, transient application of force or acceleration, disrupting equilibrium. Vibration involves oscillatory motion around an equilibrium point. Both introduce unwanted energy, challenging system stability and integrity, particularly detrimental in high-precision applications.
Common Sources
Destructive forces rarely stem from a single origin but often a combination of operational factors and external influences:
- Inertial Forces: Rapid acceleration or deceleration of large masses generates significant shock forces through the cylinder and machine structure.
- Rapid Valve Actuation: Fast-acting valves, while precise, can cause sudden pressure changes (hydraulic shock/water hammer), sending pressure spikes and mechanical jolts.
- Load Fluctuations: Abrupt external load changes (e.g., hitting obstructions, sudden load release) induce significant shock.
- End-of-Stroke Impact: Without adequate cushioning, the piston impacting the end cap, especially at high speeds, is a predictable yet damaging source.
- External Impacts & Environmental Vibration: Mobile machinery encounters impacts from terrain or collisions; stationary equipment can experience transmitted vibrations.
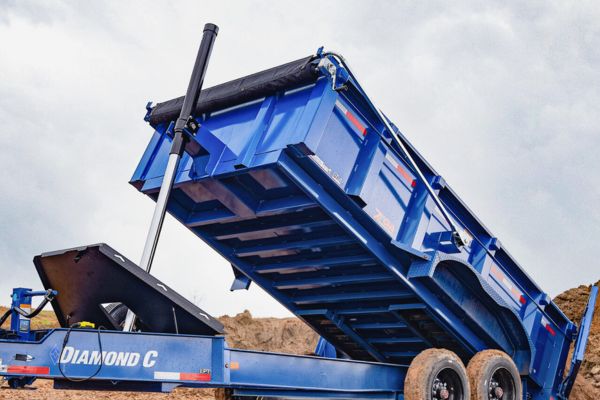
Detrimental Consequences
Unmitigated shock and vibration initiate a cascade of damaging effects compromising performance, reliability, and safety:
- Component Fatigue and Failure: Repeated stress cycles fatigue materials, causing failure in rods (bending/fracture), barrels (cracking), mounts (wear), and especially seals (wear, extrusion, leakage).
- System Pressure Spikes: Shock often coincides with pressure surges exceeding ratings, potentially damaging pumps, valves, hoses, and fittings.
- Fluid Leakage: Damaged seals and stressed connections lead to leaks, causing efficiency loss, environmental concerns, and hazards.
- Reduced Precision and Control: Even minor vibrations degrade accuracy in high-precision tasks (CNC, robotics), affecting quality.
- Noise and Vibration Issues: Excessive noise/vibration indicates problems and causes operator fatigue.
- Safety Hazards: Uncontrolled movements or component failures pose serious risks (e.g., aerial platforms, cranes).
- Increased Operational Costs: Cumulative effects include more maintenance, downtime, parts consumption, and reduced OEE.
The Precision Imperative
While basic cushioning suffices for some tasks, high-precision applications demand more. They require absorbing major impacts and minimizing micro-vibrations, ensuring consistent deceleration profiles under varying conditions. Standard cylinders often lack the refined design, tight tolerances, and advanced control to prevent shock from degrading the precise positioning and smooth motion critical to these applications, necessitating specialized, high-precision, shock-resistant designs.
Core Principles of Shock-Resistant Hydraulic Cylinder Design
Mitigating shock and vibration requires a multi-faceted approach integrating robust materials, structural ingenuity, and sophisticated damping. Designing a high-precision, shock-resistant cylinder involves meticulous engineering choices.
Material Selection: The Foundation of Resilience
The first defense is inherent material strength and durability.
High-Strength Steels
The barrel, piston rod, and end caps bear the brunt of forces. High-tensile, quenched and tempered alloy steels (e.g., AISI 4140) offer superior resistance to fatigue, impact, and pressure stresses compared to standard carbon steels, crucial for these components.
Advanced Surface Treatments
The piston rod is vulnerable. Induction hardening creates a deep, wear-resistant outer layer while maintaining core toughness. Hard chrome plating provides corrosion resistance and low friction. Alternatives like nitriding or specialized coatings enhance durability or corrosion protection in specific environments.
Seal Materials and Design
Seals often fail first under shock/pressure spikes. High-performance elastomers (advanced PU) or engineered plastics (filled PTFE blends) offer superior extrusion/wear resistance and resilience over wider temperature/pressure ranges than standard NBR or FKM. Seal geometry (e.g., anti-extrusion rings) is vital for handling pressure peaks.
Structural Integrity: Engineering for Endurance
Physical construction and configuration are vital for absorbing and distributing shock loads.
Robust Construction Methods
Finite Element Analysis (FEA) optimizes barrel wall thickness, end cap geometry, and port reinforcements to withstand peak pressures (including intensification) and stresses without yielding or fatiguing.
Design Configurations
Tie-rod cylinders offer ease of maintenance and some energy absorption via rod stretch but risk fatigue/loosening. Welded/mill-type cylinders provide rigidity, better impact resistance, and higher pressure ratings, though repair is complex. Choice depends on application demands (rigidity, pressure, serviceability).
Rod Buckling Prevention
Long strokes or high compressive loads risk rod buckling. Applying Euler’s column formula with safety factors is essential. Often, preventing buckling under shock necessitates a larger rod diameter than static calculations require, increasing bending resistance.
Mounting Integrity
Proper mounting is critical for force transfer and shock absorption. Incorrect mounting concentrates stress. Selecting appropriate styles (centerline lug, trunnion, flange) and ensuring rigid, aligned surfaces are paramount. Spherical bearings can accommodate misalignment, reducing dynamic stress.
Advanced Cushioning Techniques: Taming End-of-Stroke Impacts
Cushioning provides controlled deceleration, preventing piston-end cap impact, essential in high-speed/inertia applications.
The Cushioning Concept
As the piston nears stroke end, a component (spear/piston) enters a restricted chamber, limiting fluid outflow and creating back pressure for smooth deceleration before metallic contact.
Spear-Type Cushions
Common in tie-rod cylinders, using a spear entering a pocket. Can be fixed (predetermined orifice) or adjustable (needle valve tunes deceleration). Adjustability offers flexibility but risks improper setting, galling, unpredictable performance (parallel flow paths), and requires space.
Piston-Type Cushions
Favored in welded/mill-type cylinders for compactness/predictability. Integrate cushioning into the piston (drilled orifices, floating ring). Typically non-adjustable, ensuring consistency and preventing tampering. Advanced designs include “fast start-up” features.
Progressive/Multi-Stage Cushioning
For variable loads/speeds or requiring exceptionally smooth deceleration. Utilize profiled spears or multiple orifices/valves for gradual restriction changes, providing a smoother curve than simple designs.
External Shock Absorbers
For extreme impact energy, mid-stroke impacts, or external sources where integrated cushioning is insufficient. Mounted externally to absorb energy.
Cushion Sizing and Selection
Effective cushioning requires correct sizing. Engineers calculate kinetic energy and determine required cushion pressure/stroke to dissipate energy safely. Load, speed, pressure, viscosity, and desired deceleration time are critical inputs.
Pressure Intensification: The Hidden Danger
A critical consideration, especially during cushioning.
Explanation of Phenomenon
During extension cushioning, restricting rod-side outflow causes pressure intensification. Due to the smaller rod-side annular area, the pressure resisting the extending force becomes significantly higher than system inlet pressure (Inlet Pressure x Area Ratio). This peak pressure is contained within the cylinder.
Design Considerations
This phenomenon must be calculated. Cylinder components (barrel, end cap, seals, rod) must be designed to withstand these potentially much higher peak pressures without failure. Ignoring intensification is a common cause of seal failure or cylinder rupture.
Elevating Performance: High-Precision Aspects in Shock-Resistant Design
Robust shock resistance is the bedrock; true high precision demands further refinement for exacting accuracy, smooth control, and consistency in dynamic environments.
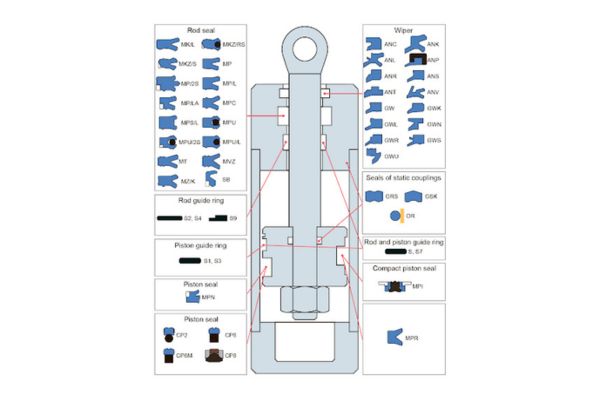
Defining Precision in Hydraulic Cylinders
High precision encompasses tight positional tolerances, minimal backlash/hysteresis, smooth low-friction movement (preventing stick-slip), consistent velocity control, and long-term repeatability. Specific requirements vary by application.
Key Enablers of Precision
Several factors contribute to this elevated performance:
Tight Manufacturing Tolerances
Precision starts here. Extremely tight tolerances on bore, piston, rod diameters, gland clearances, and concentricity minimize internal leakage, reduce side-loading effects, and ensure consistent seal performance for predictable movement.
Advanced Sealing Systems
Beyond resisting pressure spikes, seals need low friction and minimal ‘stiction’. Specialized low-friction materials/profiles, often with wear bands/guide rings (filled PTFE), ensure smooth movement and prevent metal contact, even under shock-exacerbated side loads.
Integrated Position Feedback
Closed-loop control requires accurate, real-time feedback. Integrated Linear Displacement Transducers (LDTs – e.g., magnetostrictive) offer robust, accurate solutions. Design must protect sensors from shock/vibration via specialized mounting/damping.
Refined Cushioning Control
High-precision cushioning aims for highly predictable, repeatable deceleration. This involves finely tuned fixed orifices, sophisticated progressive profiles, or electro-hydraulic solutions with active control based on feedback.
Fluid Cleanliness and Filtration
Precision components are sensitive to contamination. Maintaining high fluid cleanliness via appropriate filtration is crucial for the longevity/performance of seals, valves, and sensors.
Thermal Stability Management
Temperature affects fluid viscosity and dimensions. Designs may need to account for thermal expansion; system-level temperature control might be needed for utmost precision.
Application Spotlight: Where Precision Meets Power Under Pressure
Mobile Machinery (Construction, Mining, Forestry)
Key Demands: Mobile machinery used in construction, mining, and forestry must endure intense conditions. These environments often expose hydraulic cylinders to high impact forces, dirt, and vibrations, making shock resistance a priority. Moreover, these cylinders must function reliably in harsh conditions while offering precise control to ensure safe and efficient operation.
Examples:
- Excavator Arms: Hydraulic cylinders control the motion of excavator arms, where high precision and impact resistance are necessary for digging through solid materials.
- Bulldozer Blades: These machines need reliable cylinders to adjust blade positions with precision, even under heavy load.
- Crane Booms: Cranes must have highly reliable hydraulic cylinders that can handle heavy lifting with smooth, controlled motions.
- Harvester Heads: Forestry equipment, such as harvester heads, relies on hydraulic cylinders for precise cutting and positioning of trees.
Impact of Failure: If the hydraulic cylinders in mobile machinery fail, the entire operation could be jeopardized. For example, a failure in an excavator’s arm could lead to loss of control, causing damage to the machine or surrounding area. Furthermore, operator safety may be compromised if cushioning or control fails during operation.
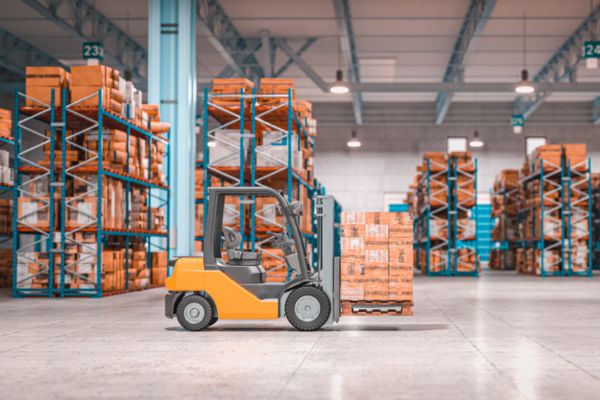
Material Handling and Logistics
Key Demands: In material handling and logistics, hydraulic cylinders are crucial for smooth motion, repeatability in positioning, and the durability needed for high-cycle operations. Given the high-volume and repetitive nature of tasks in these industries, cylinders must offer reliability without sacrificing speed or performance.
Examples:
- Automated Guided Vehicles (AGVs): AGVs in warehouses require precise and reliable hydraulic control for tasks like lifting, lowering, or moving materials.
- Stacker Cranes: These cranes, which move large stacks of goods, rely on hydraulic cylinders to ensure smooth, repeatable motion to prevent damage to the cargo.
- Conveyors: Complex conveyor systems that require hydraulic cylinders for loading, unloading, and height adjustments also depend on durability for prolonged use.
Impact of Failure: Any malfunction in material handling equipment can result in production delays or costly damage to goods. For instance, if a cylinder fails on an AGV, it could cause misalignment or stalling, leading to costly downtime and disrupted operations. Additionally, inaccurate positioning can damage goods, lowering the company’s overall efficiency.
Manufacturing and Automation
Key Demands: In manufacturing, particularly in automation and robotics, hydraulic cylinders must meet specific requirements for high cycle speeds, shock resistance, and precision. The need for repeatability and low vibration is essential, as these cylinders play a central role in high-speed assembly lines and press machines.
Examples:
- Industrial Presses: These presses require cylinders that can withstand high-impact forces while maintaining precise positioning throughout each cycle.
- Robotic Arms: In assembly lines, robotic arms with hydraulic cylinders ensure accurate and quick movements for tasks like picking, placing, or welding.
- Automated Assembly Lines: For fast-paced production lines, cylinders must function seamlessly to maintain operational efficiency while withstanding wear and tear.
Impact of Failure: Failures in cylinders used in industrial automation can halt production, damaging both machinery and products. For example, if a cylinder in a press fails to hold the correct position, it could lead to improperly manufactured parts, affecting product quality. Furthermore, a failure in robotic arms could cause the robot to malfunction, potentially damaging the assembly line or the finished products.
Energy Sector (Oil & Gas, Renewables)
Key Demands: The energy sector, especially in oil & gas and renewable energy industries, operates in some of the harshest environments. Cylinders used in these industries must be corrosion-resistant, capable of handling high loads, and reliable over long service intervals. The precision of control is often needed for processes such as pipeline tensioning or wind turbine adjustments.
Examples:
- Offshore Drilling Equipment: Hydraulic cylinders power equipment used to drill offshore, where they must resist saltwater corrosion and operate under high pressure.
- Pipeline Tensioners: These cylinders adjust the tension in pipelines, ensuring that they are safely installed or repaired under high-stress conditions.
- Wind Turbine Pitch Control: Cylinders in wind turbines adjust the blades’ pitch, requiring precision and the ability to work in varying weather conditions.
Impact of Failure: Failures in the energy sector can result in significant downtime, environmental hazards, and increased operational costs. For example, if a cylinder in offshore drilling equipment fails, it could halt operations, leading to financial losses and even environmental damage if the equipment is part of an oil spill containment system.
Conclusion
Shock and vibration severely challenge hydraulic systems. For high-precision tasks, robust shock resistance is non-negotiable. Advanced engineering, integrating superior materials, structural integrity, and sophisticated cushioning, provides the necessary resilience. High-precision features further enhance accuracy and control. Investing in hydraulic cylinders specifically designed for demanding applications ensures operational efficiency, enhances safety, extends equipment life, and ultimately delivers significant long-term value and reliability where standard solutions fail.
Are you faced with cylinder failure, system vibration or the challenge of maintaining accuracy in dynamic applications? Are you looking to optimize the performance and service life of your hydraulic equipment? Contact us today to discuss your needs and let us help you design the best solution!
References
- Ever-Power Industry. (2024, June 4) . Impact And Shock Resistance Of Standard Tie-Rod Hydraulic Cylinders. Retrieved from https://www.ever-power.net/impact-and-shock-resistance-of-standard-tie-rod-hydraulic-cylinders/
- Hydroline. (n.d.) . How to design a hydraulic cylinder? Retrieved from https://hydroline.fi/blogs/how-to-design-a-hydraulic-cylinder/
- Innovative Hydraulics. (2024, February 2) . Hydraulic Cylinder Cushion Designs. Retrieved from https://innovativehyd.com/hydraulic-cylinder-design-cushions/
- IQS Directory. (n.d.) . Types, Configurations & Applications for Hydraulic Cylinders. Retrieved from https://www.iqsdirectory.com/articles/hydraulic-cylinder.html
- Made-in-China Insights. (2025, March 16) . Hydraulic Cylinders Unveiled: Design Principles and User-Centric Considerations. Retrieved from https://insights.made-in-china.com/Hydraulic-Cylinders-Unveiled-Design-Principles-and-User-Centric-Considerations_FAgTSxEbqJIh.html
FAQ
What is shock resistance in hydraulic cylinders?
Shock resistance in hydraulic cylinders refers to their ability to withstand sudden, high-impact forces during operation.
Why is shock resistance important in hydraulic cylinders?
It prevents damage to the cylinder and hydraulic system during high-impact operations, ensuring reliability and safety.
How is shock resistance achieved in hydraulic cylinders?
Shock resistance is achieved through reinforced materials, dampening mechanisms, and robust design features that absorb impact forces.
What are common applications for shock-resistant hydraulic cylinders?
They are commonly used in construction equipment, aerospace systems, material handling, and heavy-duty industrial machinery.
How do shock-resistant hydraulic cylinders improve safety?
They help prevent sudden failures and accidents by ensuring smooth operation under high-impact conditions.
What maintenance is required for shock-resistant hydraulic cylinders?
Regular inspection, seal replacement, and hydraulic fluid checks are essential to maintain shock resistance and prevent failure.