Hydraulic hose failure is a common and serious issue that can occur in various forms, most notably through bursting and excessive wear. Preventing hose failures not only minimizes costly downtime but also extends the lifespan of equipment.
Understanding Hydraulic Hose Failure
A. Common Types of Failures
Hydraulic hoses are susceptible to various types of failures, each with unique characteristics and consequences. Among the most prevalent are bursting and excessive wear, two issues that account for the majority of hose malfunctions. Bursting is a sudden and often catastrophic event where the hose fails under pressure, releasing fluid rapidly and violently. This type of failure is dangerous and can lead to significant equipment damage, fluid contamination, and potential injury to personnel. Bursting typically occurs when the hose is subjected to pressure levels beyond its design limits, often without prior warning, making it a critical issue that requires immediate attention and repair.
On the other hand, excessive wear is a more gradual form of degradation. It develops over time as the hose material breaks down due to factors such as abrasion, chemical exposure, or improper handling. Unlike bursting, excessive wear is usually detectable through visual signs like cracks, fraying, or thinning of the hose walls. Although less dramatic than bursting, excessive wear can still lead to system inefficiency, leaks, and eventual hose failure if not addressed promptly. Understanding the distinction between these two failure modes—sudden bursting and gradual wear—is key to implementing effective maintenance and prevention strategies.
B. Causes of Hydraulic Hose Failure
Hydraulic hose failure is often the result of a combination of internal and external factors that compromise the hose’s integrity over time. Internal factors include issues like fluid incompatibility, where the hose material reacts negatively to the hydraulic fluid being used, leading to deterioration from within. Extreme fluid temperatures, whether too hot or too cold, can also cause the hose material to weaken or become brittle, accelerating failure. Excessive internal pressure, particularly pressure spikes or surges that exceed the hose’s rated capacity, can place undue stress on the hose and contribute to bursting.
External factors play an equally important role in hydraulic hose failure. Improper installation is a leading cause, as hoses that are bent too sharply, twisted, or routed in ways that create undue stress points are more prone to failure. Mechanical damage, such as abrasion from contact with other components or external objects, is another common issue, gradually wearing down the hose’s protective outer layers. Additionally, environmental factors such as exposure to UV rays, ozone, or corrosive substances can degrade the hose material over time. Understanding these internal and external contributors to hydraulic hose failure is essential for taking preventive measures and ensuring the longevity of the hose within a hydraulic system.
Hydraulic Hose Bursting: Causes and Effects
A. What is a Hydraulic Hose Bursting?
Hydraulic hose bursting occurs when the hose suddenly fails under extreme pressure, causing the hose to rupture violently. This failure can result in a rapid release of pressurized hydraulic fluid, leading to significant safety hazards, equipment damage, and operational disruptions. During a burst, the hose can split or tear apart, with fluid escaping uncontrollably. This type of failure is often unpredictable, making it one of the most dangerous issues in hydraulic systems.
Several warning signs can indicate that a hose is at risk of bursting. These include visible swelling or bulging along the hose’s length, which suggests that the hose walls are weakening due to internal pressure buildup. Additionally, the presence of leaks or fluid seepage around fittings may signal that the hose is being subjected to stresses beyond its capacity. Another key indicator is hose deformation, such as flattening or kinking, which can precede a burst if the hose is not replaced or reinstalled properly.
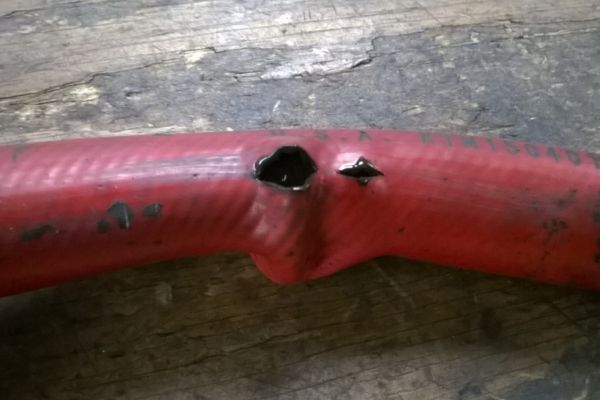
B. Key Causes of Hose Bursting
Pressure Surges and Over-Pressurization
Sudden pressure spikes or surges within the hydraulic system are a primary cause of hose bursting. When hydraulic systems experience rapid increases in pressure that exceed the hose’s rated capacity, the hose is forced to bear stresses beyond its design limits. Over time, this can cause the hose to weaken and ultimately burst under pressure.
Inadequate Hose Rating
Using a hose that is not rated for the specific pressure demands of the hydraulic system is another common cause of bursting. When a hose with a lower pressure rating is installed in a high-pressure system, it is continuously subjected to stresses that it cannot withstand. This mismatch between hose rating and system requirements increases the risk of failure, as the hose is more likely to burst under normal operating conditions.
Environmental Stressors
External environmental factors such as extreme heat, UV radiation, and exposure to chemicals can degrade the hose material over time. High temperatures can cause the hose to lose its flexibility, becoming brittle and prone to cracking or bursting under pressure. Similarly, prolonged exposure to UV radiation can weaken the hose’s outer layers, making it more susceptible to failure. Corrosive chemicals or exposure to oil and contaminants can also erode the hose material, leading to weakening and potential bursting.
Incorrect Hose Installation
Improper installation is another significant contributor to hose bursting. Hydraulic hoses must be installed with the correct routing, avoiding sharp bends, twists, or excessive stretching. When hoses are installed with tight bends or are twisted during installation, stress points are created, increasing the likelihood of a burst. Incorrect installation also puts strain on the hose at the fittings, leading to potential failure at the connection points.
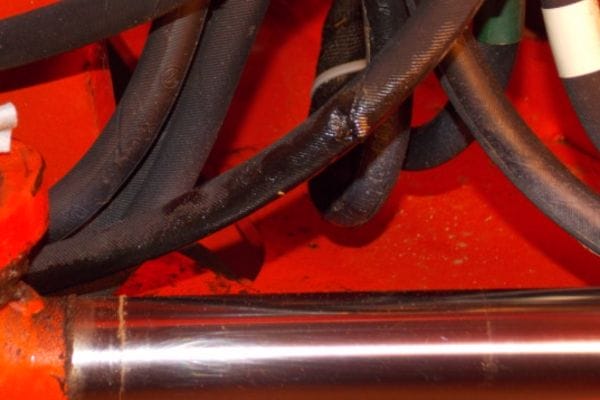
Consequences of Hose Bursting
Immediate Safety Risks
When a hydraulic hose bursts, the sudden release of high-pressure fluid can pose immediate dangers to personnel in the vicinity. The force of the escaping fluid can cause injuries such as burns, cuts, or even more severe trauma. Additionally, the fluid itself may be hot or corrosive, further increasing the risk of harm. The unpredictability of a burst makes it a serious safety concern in any hydraulic system.
System Downtime and Operational Delays
A burst hose leads to immediate system failure, resulting in downtime and operational delays. In industrial settings, this can halt production lines, delay construction projects, or immobilize heavy machinery. The downtime associated with a burst hose can be costly, as repairs, replacements, and cleanup efforts must be undertaken before operations can resume.
Damage to Equipment and the Surrounding Environment
The violent nature of a hydraulic hose burst can also cause damage to nearby equipment. High-pressure fluid can contaminate other components, leading to further mechanical failures or the need for extensive cleaning and repairs. In addition, hydraulic fluid leaks can cause environmental damage, particularly if the fluid is not properly contained or cleaned up, potentially leading to contamination of soil, water sources, or other areas of the facility.
Excessive Wear in Hydraulic Hoses: Causes and Prevention
A. What is Excessive Wear?
Excessive wear refers to the gradual deterioration of hydraulic hoses over time due to continuous exposure to external factors like abrasion, heat, and environmental conditions. While some level of wear and tear is inevitable in any hydraulic system, excessive wear can be prevented with proper maintenance, correct installation, and careful monitoring. If left unchecked, excessive wear can weaken the hose, making it vulnerable to failure during operation. Visual indicators of excessive wear include abrasions or scuff marks on the hose’s outer surface, cracks in the hose material, and exposed reinforcement layers beneath the protective covering. These signs serve as early warnings that the hose is nearing the end of its functional lifespan and needs attention before failure occurs.
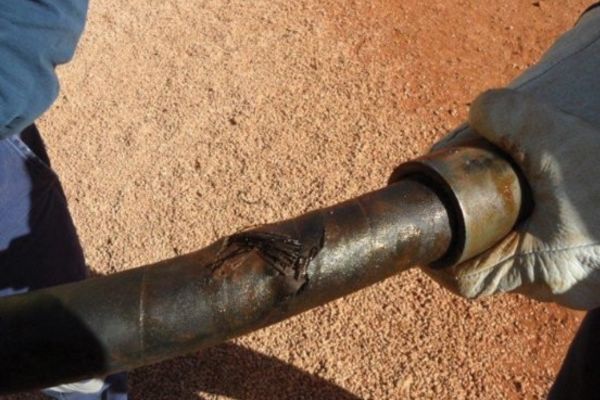
B. Causes of Excessive Wear
Abrasion from External Surfaces
Hydraulic hoses are often routed through areas where they come into contact with sharp edges, rough surfaces, or moving parts. Continuous friction between the hose and these surfaces can lead to abrasions, wearing down the protective outer layer. Over time, this can expose the hose’s internal reinforcement layers, making it more susceptible to failure. Abrasion is one of the most common causes of excessive wear, particularly in environments where hoses are subjected to frequent movement or vibration.
Inadequate Hose Support and Clamps
When hydraulic hoses are not properly supported or secured with clamps, they are prone to excessive movement during system operation. This movement causes the hoses to rub against surfaces or other components, accelerating wear. Unsupported hoses may also bend in ways that create additional strain on the material, increasing the likelihood of wear and eventual failure. Proper support and clamping can significantly reduce the wear caused by this type of movement.
Fluid Compatibility Issues
Incompatible hydraulic fluids can cause internal wear in hoses, degrading the hose material from within. Certain chemicals in the fluid may react with the hose’s inner lining, causing it to become brittle, swell, or crack. Over time, this chemical degradation weakens the hose’s structural integrity, contributing to excessive wear. Ensuring fluid compatibility with the hose material is essential to avoid this issue and extend the hose’s lifespan.
Improper Hose Selection
Hydraulic hoses are available in a variety of materials, each designed for specific operating environments. Failing to select hoses that are resistant to abrasion in harsh conditions can result in accelerated wear. For example, standard hoses may not withstand the rigors of heavy industrial or construction applications, where hoses are more likely to be exposed to abrasive materials, chemicals, or extreme temperatures.
C. Long-Term Impact of Excessive Wear
Reduction in Hose Lifespan
Excessive wear significantly reduces the lifespan of a hydraulic hose. As wear accumulates, the hose becomes more prone to leaks, ruptures, or complete failure, requiring replacement sooner than anticipated. This reduction in lifespan increases the frequency of hose replacements, leading to higher costs and operational disruptions.
Gradual Performance Degradation
As hydraulic hoses wear down, their performance begins to degrade. Worn hoses are less capable of maintaining consistent pressure and flow rates, which can negatively impact the efficiency of the hydraulic system. Gradual wear may also result in small leaks that reduce system performance and increase the need for regular maintenance.
Increased Maintenance and Replacement Costs
Excessive wear leads to a higher frequency of maintenance checks, repairs, and hose replacements, driving up operational costs. The need to replace worn hoses more often not only increases material costs but also results in additional labor expenses and downtime. Preventing excessive wear through proper hose selection, installation, and maintenance can help mitigate these long-term costs and keep the hydraulic system running efficiently.
Preventing Hydraulic Hose Bursting and Excessive Wear
A. Proper Hose Selection
One of the most effective ways to prevent both hydraulic hose bursting and excessive wear is by selecting the correct hose for the specific application. Hoses must be rated for the appropriate pressure levels that the system will experience, taking into account both the normal operating pressure and potential pressure surges. Additionally, hoses should be chosen based on the temperature conditions they will be exposed to, as well as the chemical composition of the hydraulic fluids they will carry. Ensuring that the hose material is compatible with these environmental factors will help extend the hose’s lifespan and reduce the risk of failure.
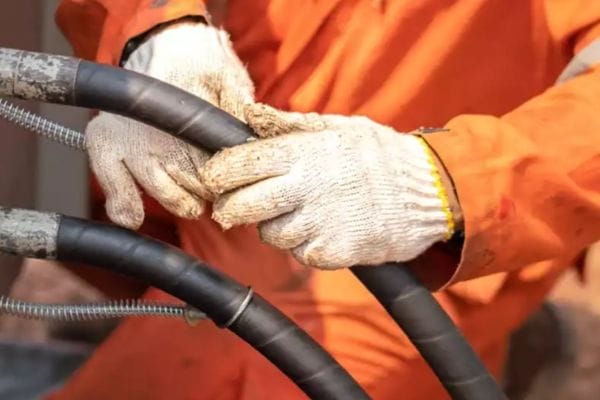
B. Best Practices for Hose Installation
Proper Routing and Bend Radius
Correct routing is essential to ensuring the longevity and safety of hydraulic hoses. Hoses should be installed in a manner that avoids tight bends, kinks, or twists, which can place unnecessary stress on the hose material. Adhering to the manufacturer’s recommended minimum bend radius prevents over-stressing the hose, which can weaken it over time and increase the likelihood of bursting or excessive wear.
Clamping and Securing Hoses
Using proper clamps and supports is vital to prevent hose movement during operation. When hoses are allowed to move freely or vibrate, they are more likely to rub against other surfaces, leading to abrasion and wear. Properly securing hoses with clamps that allow for controlled movement helps prevent damage and ensures that the hoses stay in place, reducing the risk of both excessive wear and bursts.
Protecting Hoses from External Damage
In environments where hoses are exposed to abrasive surfaces or potential impacts, installing protective covers or sleeves is a proactive measure. These protective devices shield the hoses from contact with sharp edges, rough materials, or extreme temperatures, extending the hose’s life and preventing wear. In high-abrasion applications, using specially designed abrasion-resistant sleeves can provide an additional layer of defense against external damage.
C. Regular Maintenance and Inspection
Scheduled Replacements
Even with the best maintenance practices, hydraulic hoses have a finite lifespan. To avoid unexpected failures, it is essential to replace hoses proactively before they reach the end of their service life. Scheduled replacements based on manufacturer recommendations, system usage, and environmental conditions can help prevent sudden bursts and reduce downtime. By maintaining a record of hose replacements and keeping track of service intervals, operators can ensure that hoses are replaced on time.
Pressure and Fluid Monitoring
Implementing sensors and monitoring systems to track hose pressure and fluid quality adds an extra layer of protection against failure. These systems can alert operators to potential issues such as pressure spikes, fluid contamination, or temperature changes that could compromise hose integrity. Early detection of these problems allows for timely intervention, reducing the likelihood of hose failure and keeping the system operating efficiently.
Conclusion
Proactive maintenance is key to maintaining the integrity and efficiency of hydraulic systems. By establishing a routine for regular inspections, scheduled replacements, and monitoring pressure and fluid quality, you can stay ahead of potential issues and ensure that hoses are performing optimally. Preventive measures not only help avoid catastrophic failures but also reduce long-term costs associated with frequent hose replacements and system downtime. Investing in proactive maintenance ultimately leads to more reliable systems and safer working environments.
FAQ
What are the most common causes of hydraulic hose failure?
The most common causes include excessive pressure, improper installation, abrasion, incompatible fluids, extreme temperatures, and wear over time.
How can I prevent my hydraulic hose from bursting?
To prevent bursting, ensure proper hose selection for pressure and temperature ratings, avoid pressure surges, and follow correct installation practices with appropriate routing and support.
What are the warning signs of hydraulic hose wear?
Warning signs include visible abrasions, cracks, bulging, fluid leaks, and exposed reinforcement layers.
How often should I inspect my hydraulic hoses?
It’s recommended to visually inspect hoses regularly, depending on usage—ideally every week for high-demand systems and at least monthly for less-demanding operations.
What should I do if I notice a damaged hydraulic hose?
Replace the hose immediately to prevent failure. It’s crucial to address issues early to avoid sudden breakdowns or bursts.
Can hydraulic hoses be repaired, or should they always be replaced?
In most cases, damaged hydraulic hoses should be replaced rather than repaired, as repairs may not restore full integrity and can be unsafe.