In hydraulic systems, selecting hose materials is critical to ensuring both performance and safety. The right material not only affects the efficiency of fluid transfer but also plays a significant role in the system’s overall integrity. Improper material choices can lead to failures that may result in leaks, system downtime, or even catastrophic accidents, underscoring the importance of careful selection.
Understanding Hose Materials
In hydraulic systems, selecting the appropriate hydraulic hose material is crucial for performance and safety. The most common materials used in hydraulic hoses include rubber, thermoplastic, and metal. Each material type has unique properties, advantages, and disadvantages that make it suitable for specific applications.
Types of Hose Materials
Rubber
Description: Rubber hoses are highly flexible and commonly used in low-pressure applications. They can handle various hydraulic fluids and are generally easy to work with.
Properties:
Flexibility: Excellent flexibility, allowing for easy routing in confined spaces.
Tensile Strength: Moderate tensile strength, adequate for many applications but can be prone to wear.
Temperature Resistance: Typically suitable for a wide temperature range, though specific grades may vary.
Thermoplastic
Description: Thermoplastic hoses are lightweight and provide good resistance to chemicals and abrasions. They are increasingly used in hydraulic applications due to their versatility.
Properties:
Flexibility: While flexible, they may not match rubber in extreme bending applications.
Tensile Strength: Generally, high tensile strength can be beneficial in high-pressure environments.
Temperature Resistance: Often limited to lower temperatures compared to rubber and metal hoses.
Metal
Description: Metal hoses, typically made from stainless steel or other alloys, are known for their durability and resistance to high pressure and extreme temperatures.
Properties:
Flexibility: Less flexible than rubber or thermoplastic hoses, making installation more challenging.
Tensile Strength: High tensile strength, suitable for high-pressure applications.
Temperature Resistance: Excellent temperature resistance, suitable for extreme conditions.
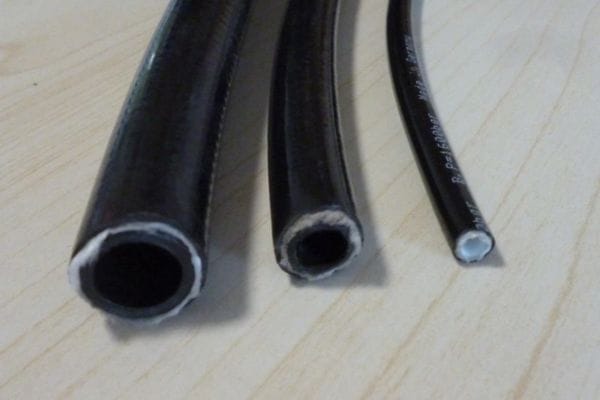
Advantages and Disadvantages
Rubber Hoses
Advantages:
Versatility: Suitable for a range of hydraulic fluids and applications.
Cost-Effectiveness: Generally less expensive than metal hoses, making them a popular choice for many systems.
Ease of Handling: Lightweight and easy to cut and assemble.
Disadvantages:
Chemical Degradation: Susceptible to damage from certain chemicals and UV exposure.
Limited Pressure Ratings: Not ideal for high-pressure systems, as they can burst under extreme conditions.
Thermoplastic Hoses
Advantages:
Chemical Resistance: Strong resistance to various chemicals, making them suitable for harsher environments.
Lightweight: Easier to handle and install compared to rubber or metal.
Good Pressure Ratings: Capable of handling moderate to high pressures.
Disadvantages:
Durability Issues: May not withstand extreme temperatures or conditions as well as rubber or metal.
Bending Limitations: Can be less flexible in extreme bending situations, potentially leading to kinking.
Metal Hoses
Advantages:
High Pressure and Temperature Resistance: Ideal for high-pressure and high-temperature applications, providing excellent durability.
Chemical Compatibility: Resistant to most chemicals, making them suitable for a wide range of fluids.
Longevity: Typically have a longer lifespan compared to rubber or thermoplastic hoses.
Disadvantages:
Weight: Heavier than rubber or thermoplastic options, which can complicate installation and routing.
Cost: Generally more expensive than rubber and thermoplastic hoses, which may not be feasible for all applications.
The Role of Chemical Compatibility
Definition and Importance
Chemical compatibility refers to the ability of a material to resist degradation when exposed to specific chemicals or fluids. In hydraulic systems, ensuring that hose materials are compatible with the fluids they will carry is critical. Incompatible materials can lead to chemical reactions that result in swelling, cracking, or complete failure of the hose, which can compromise system integrity, safety, and performance.
The importance of chemical compatibility cannot be overstated. Hydraulic fluids often contain a mix of additives that can be aggressive towards certain materials. For instance, oils, solvents, and hydraulic fluids can vary significantly in composition and reactivity. If a hose is made from a material that is not compatible with the fluid it carries, it can lead to:
Leaking and Failures: Chemical breakdown of the hose can result in leaks, leading to loss of hydraulic pressure and potential system failure.
Safety Hazards: Leaking fluids can pose serious safety risks, including fire hazards and environmental contamination.
Increased Maintenance Costs: Frequent replacements and repairs due to compatibility issues can lead to increased operational costs and downtime.
Reduced Efficiency: Degraded hoses may not perform effectively, affecting the overall efficiency of hydraulic systems.
Thus, understanding and assessing chemical compatibility is a foundational aspect of hose material selection, ensuring both operational reliability and safety.
Assessing Compatibility
To evaluate chemical compatibility effectively, several methods and tools can be utilized:
Chemical Resistance Charts: These charts provide a comprehensive overview of how various materials react when exposed to specific chemicals. They typically categorize materials based on their resistance to swelling, cracking, or other forms of degradation when in contact with various fluids. When using these charts, it is crucial to select materials that are rated as compatible or highly resistant to the fluids in question. Users should note that these charts may vary between manufacturers, so it’s essential to consult the appropriate references.
Material Safety Data Sheets (MSDS): MSDS are detailed documents that provide information on the properties of materials, including their chemical compatibility. They outline hazards, handling instructions, and emergency measures related to the material. Reviewing the MSDS of both the hose material and the hydraulic fluid can provide insights into potential compatibility issues.
Manufacturer Recommendations: Most hose manufacturers provide guidelines regarding compatible fluids and operating conditions for their products. These recommendations are based on extensive testing and should be considered when selecting hose materials. Engaging directly with manufacturers can yield valuable information regarding specific applications and compatibility data.
Laboratory Testing: In some cases, especially for critical applications, conducting laboratory tests may be necessary to determine compatibility. This can involve exposing hose samples to the fluids they will carry under controlled conditions and observing for signs of degradation over time. While this method is more resource-intensive, it can provide definitive data for unique or particularly challenging applications.
Field Experience and Case Studies: Drawing from real-world experiences and documented case studies can offer insights into compatibility issues that may not be covered in charts or MSDS. Understanding how certain materials performed in specific applications can guide future material selection and help avoid repeating past mistakes.
Consultation with Experts: Engaging with materials scientists or chemical engineers can provide deeper insights into compatibility issues. Their expertise can help interpret data from resistance charts and MSDS, and they may offer guidance on innovative materials or practices to mitigate compatibility risks.
Factors Influencing Material Selection
Selecting the appropriate hose material for hydraulic systems involves careful consideration of several critical factors, including operating conditions, fluid properties, and mechanical stress requirements. Each of these aspects plays a vital role in determining the best material for a specific application, ensuring both performance and safety.
Operating Conditions
1. Temperature: The operational temperature range significantly influences material selection. Each hose material has specific temperature limits beyond which its properties may degrade. For instance:
Rubber hoses typically perform well within a moderate temperature range, usually up to 200°F (93°C), but can deteriorate if exposed to high heat or extreme cold, leading to cracks or loss of flexibility.
Thermoplastic hoses generally handle lower temperatures than rubber, often up to about 140°F (60°C) depending on the specific material. They may become brittle in cold environments, limiting their applications.
Metal hoses excel in high-temperature environments, often functioning effectively at temperatures exceeding 400°F (204°C). Their robust nature makes them suitable for extreme conditions where other materials may fail.
2. Pressure: The operating pressure is another crucial factor. Hose materials must withstand not only the maximum working pressure but also any surges that may occur during operation. For example:
Rubber hoses are suitable for low to medium-pressure applications, typically not exceeding 3000 psi. They may burst if subjected to pressures beyond their ratings.
Thermoplastic hoses can handle moderate to high pressures (up to 6000 psi in some cases) but require careful selection based on the specific type of thermoplastic used.
Metal hoses are ideal for high-pressure applications, with many capable of withstanding pressures of 10,000 psi or more without failing.
3. Environmental Conditions: The surrounding environment, including factors like exposure to chemicals, UV light, ozone, and physical abrasions, can affect hose performance. For instance:
Hoses exposed to UV light and ozone can suffer from premature aging and cracking. Rubber hoses, in particular, may degrade quickly under such conditions, while thermoplastics and metals generally offer better resistance.
Chemical exposure can lead to compatibility issues, as previously discussed. It’s crucial to choose materials that resist degradation from specific chemicals present in the environment or the fluid being transported.
Hoses operating in abrasive conditions may require additional protection, such as external covers or coatings, to enhance durability and extend service life.
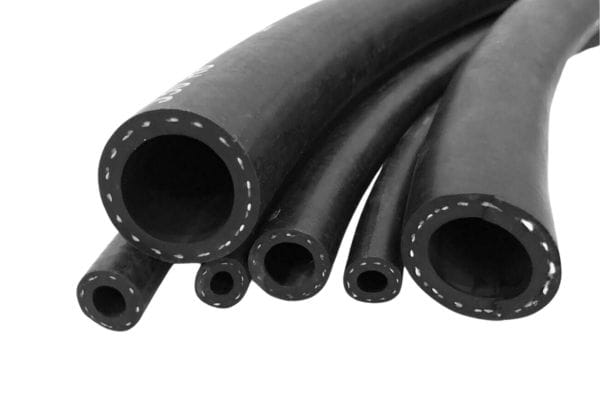
Fluid Properties
1. Viscosity: The viscosity of the hydraulic fluid is an essential consideration. Viscosity affects the ease with which the fluid flows through the hose, impacting the required pressure and the hose’s overall performance:
High-viscosity fluids can exert more pressure on the hose walls, necessitating stronger materials that can withstand this added stress. Rubber and metal hoses are often preferred for applications involving viscous fluids due to their strength and resistance to deformation.
Low-viscosity fluids might be accommodated by a wider range of materials, including lighter thermoplastic hoses, as the pressure exerted on the hose is lower.
2. Chemical Composition: The specific chemical makeup of the fluid also impacts material selection. Some fluids contain additives, solvents, or corrosive elements that can react adversely with certain hose materials. For example:
Hydraulic oils may have additives that can degrade rubber hoses over time, while thermoplastic materials might offer better resistance.
Aqueous solutions, such as water-based fluids, may interact differently with materials compared to oil-based fluids. Understanding the chemical composition is critical for preventing unexpected failures.
Mechanical Stress and Flexibility Requirements
1. Mechanical Stress: Hoses are often subjected to various mechanical stresses, including bending, twisting, and tension during operation. The expected mechanical stress levels must be factored into material selection:
Flexible hoses are essential in applications where space constraints require tight bends. Rubber and certain thermoplastic hoses excel in flexibility, allowing for tight routing without kinking.
Metal hoses, while durable, may be less flexible and better suited for straight runs where significant movement is not expected.
2. Flexibility Requirements: The need for flexibility can vary greatly depending on the application. For example:
In applications with high mobility, such as robotics or machinery with moving parts, flexible hoses are necessary to accommodate movement without causing strain.
In fixed installations, where hoses are secured in place, less flexible materials may be acceptable, prioritizing durability and pressure resistance.
Performance and Durability
In hydraulic systems, the selection of hose materials plays a pivotal role in determining both performance and safety. Choosing the right material not only affects how efficiently the system operates but also has significant implications for its longevity and reliability.
Impact of Material Selection
1. Enhanced System Performance: The correct hose material contributes to optimal hydraulic performance in several ways:
Pressure Resistance: Hoses made from materials designed for high-pressure applications can maintain consistent fluid flow and reduce the risk of pressure drops. For instance, metal hoses can handle extreme pressures without failure, ensuring that hydraulic systems operate smoothly under demanding conditions.
Flow Efficiency: Different materials offer varying levels of flexibility and internal smoothness, which can influence fluid flow. For example, rubber hoses typically provide smooth inner surfaces that minimize turbulence, facilitating better flow rates compared to more rigid materials.
Temperature Management: Selecting hoses with suitable temperature ratings ensures that they can withstand the thermal demands of the system. This capability helps maintain optimal operating conditions, preventing overheating or freezing of fluids, which could lead to system inefficiencies or failures.
2. Improved Safety: The right hose material directly enhances safety in hydraulic systems:
Failure Prevention: Using materials that resist degradation from the fluids they transport minimizes the risk of leaks and ruptures. For example, thermoplastic hoses often exhibit excellent chemical resistance, reducing the likelihood of material breakdown and subsequent system failures.
Reduced Maintenance Needs: Durable hose materials require less frequent replacement, which lowers maintenance costs and minimizes the risk of accidents caused by worn or damaged hoses. A well-chosen hose can lead to fewer emergency repairs, ensuring safer operations.
Environmental Resistance: Materials selected for their resistance to environmental factors—such as UV exposure, abrasion, and chemicals—can help ensure that hoses maintain their integrity over time. This resilience is crucial for applications where hoses are exposed to harsh conditions.
Durability Comparison
The durability of hose materials can significantly impact their lifespan and overall performance. Here’s a comparative analysis of the most commonly used hose materials in hydraulic applications:
1. Rubber Hoses
Lifespan: Typically lasts between 5 to 10 years, depending on usage and environmental conditions.
Resistance to Wear: Moderate abrasion resistance; may degrade from UV exposure and certain chemicals. Regular inspection is necessary to identify signs of wear and prevent failures.
2. Thermoplastic Hoses
Lifespan: Generally have a lifespan of 3 to 7 years. Their longevity can be influenced by the specific thermoplastic material used and the environmental conditions.
Resistance to Wear: Good chemical resistance and lighter weight contribute to better wear resistance in many applications. However, they may not perform as well in extreme temperatures or heavy abrasion scenarios compared to rubber or metal hoses.
3. Metal Hoses
Lifespan: Can last 10 years or more, especially in high-pressure and high-temperature applications.
Resistance to Wear: Exceptional durability and wear resistance; metal hoses can withstand extreme conditions without degrading. However, they are more rigid and may not be suitable for applications requiring significant flexibility.
Conclusion
The selection of hose materials is a critical factor in ensuring the safety and efficiency of hydraulic systems. Choosing the right material directly impacts not only the performance of the system but also its durability and reliability. Incompatible materials can lead to leaks, ruptures, and catastrophic failures, jeopardizing both personnel safety and equipment functionality. Thus, understanding the properties and compatibility of various materials is essential for maintaining the integrity of hydraulic systems.
FAQ
What is the most commonly used material for hydraulic hoses?
Rubber is the most common material for hydraulic hoses, known for its flexibility and good performance in low-pressure applications.
How do I know if a hose material is compatible with my hydraulic fluid?
Consult chemical resistance charts, MSDS, or manufacturer recommendations to assess compatibility with specific fluids.
What factors should I consider when selecting a hose material?
Key factors include operating temperature, pressure ratings, fluid properties (viscosity and chemical composition), and environmental conditions.
How long do hydraulic hoses typically last?
The lifespan of hydraulic hoses varies by material: rubber hoses last 5-10 years, thermoplastic hoses 3-7 years, and metal hoses can exceed 10 years.
What are the signs of hose wear or failure?
Look for cracks, leaks, swelling, discoloration, or decreased flexibility, which can indicate that the hose is wearing out and may need replacement.
Can I use the same hose for different hydraulic fluids?
Not always. It is crucial to ensure that the hose material is compatible with all fluids it will carry to prevent degradation and failures.