One of the most significant factors to consider when working with hydraulic hoses is their pressure capacity. Pressure capacity refers to the maximum pressure that a hose can safely handle during operation without failure. This is crucial because exceeding the specified pressure rating can lead to hose ruptures, leaks, and potentially catastrophic equipment failures. Understanding the pressure capacity ensures safety and optimizes system performance and longevity.
Understanding Hydraulic Hose Pressure Capacity
A. Definition of Pressure Capacity
Pressure capacity is defined as the maximum amount of internal pressure that a hydraulic hose can safely withstand without failing. This capacity is determined during the hose manufacturing process and is based on various factors, including the materials used, the hose’s construction, and its intended application. Understanding this capacity is essential for ensuring the safety and reliability of hydraulic systems. Using a hose beyond its rated pressure can lead to catastrophic failures, such as bursting or leaking, which can pose serious risks to both equipment and personnel.
B. How Pressure is Measured
Pressure is typically measured in units such as pounds per square inch (PSI) or bars.
Pounds per Square Inch (PSI): This is the most common unit used in the United States and is defined as the force of one pound applied to an area of one square inch. Hydraulic hoses have pressure ratings specified in PSI, which indicates the maximum pressure the hose can safely handle.
Bar: In many other parts of the world, pressure is measured in bars, where one bar is approximately equal to 14.5 PSI. This unit is often used in international specifications and standards.
Both PSI and bar are crucial for understanding hose specifications, and converting between these units is essential when comparing different hoses or systems. For instance, a hose rated for 3,000 PSI is equivalent to about 206.8 bar, highlighting the importance of knowing which unit of measure applies in a given context.
C. Importance of Adhering to Pressure Ratings
Adhering to pressure ratings is vital for several reasons:
Safety: Operating a hose beyond its rated pressure can result in dangerous failures, potentially causing injuries or fatalities. Maintaining pressure within the specified limits ensures the safety of operators and nearby personnel.
Equipment Integrity: Hydraulic systems are designed to work within specific pressure ranges. Exceeding these limits can lead to not only hose failure but also damage to connected components such as pumps, valves, and actuators. This can lead to costly repairs and extended downtime.
Performance Optimization: Operating within the pressure capacity ensures that hydraulic systems perform optimally. When hoses are used according to their specifications, the efficiency of fluid transfer improves, leading to better overall system performance.
Longevity of Components: Regularly exceeding pressure ratings can lead to premature wear and tear on hoses and associated components. By adhering to these ratings, users can significantly extend the lifespan of their hydraulic systems, reducing the need for frequent replacements.
Compliance with Standards: Many industries are governed by strict safety regulations and standards. Using hoses within their specified pressure ratings helps ensure compliance with these regulations, reducing the risk of legal repercussions or fines.
Types of Hydraulic Hoses
A. Overview of Common Types
Hydraulic hoses come in various designs and constructions, each suited to specific applications and pressure requirements. Understanding the different types can help in selecting the right hose for particular hydraulic systems. Here are some common types:
1-Wire Hoses
Construction: 1-wire hoses are typically reinforced with a single layer of steel wire. They are often made from high-quality rubber or thermoplastic materials, which provide flexibility and resilience.
Applications: These hoses are ideal for low to medium pressure applications. Common uses include general hydraulic systems, agricultural machinery, and construction equipment.
Pressure Ratings: Generally, 1-wire hoses can handle pressures up to 3,000 PSI, making them suitable for many standard applications but limiting their use in high-pressure systems.
2-Wire Hoses
Construction: As the name implies, 2-wire hoses feature two layers of steel wire reinforcement. This design significantly enhances their strength and pressure capacity while maintaining flexibility.
Applications: These hoses are commonly used in more demanding hydraulic applications, such as in heavy machinery, mobile equipment, and industrial hydraulic systems.
Pressure Ratings: 2-wire hoses typically handle pressures ranging from 3,000 to 6,000 PSI, making them a versatile choice for various applications where higher pressure resistance is required.
4-Wire Hoses
Construction: 4-wire hoses are the most robust type, featuring four layers of steel wire reinforcement. This design provides maximum strength and durability, allowing the hoses to withstand extreme conditions.
Applications: These hoses are primarily used in high-pressure hydraulic systems, such as those found in mining, oil and gas applications, and large-scale industrial machinery.
Pressure Ratings: 4-wire hoses can handle pressures upwards of 6,000 PSI, making them suitable for the most demanding applications where safety and reliability are paramount.
Specialty Hoses
Construction: Specialty hoses encompass a wide range of designs tailored for specific applications. These can include thermoplastic hoses, high-temperature hoses, and hoses designed to handle particular fluids (e.g., chemical resistance).
Applications: Depending on their design, specialty hoses can be used in various fields, including chemical processing, food and beverage, and aerospace. They are engineered to meet specific environmental and operational requirements.
Pressure Ratings: Pressure capacities for specialty hoses vary widely, often dependent on their specific application and construction materials.

B. Comparison of Pressure Capacities Among Different Types
When comparing the pressure capacities of these hydraulic hoses, several factors come into play, including their construction, intended application, and material properties.
1-Wire vs. 2-Wire Hoses
Pressure Capacity: While 1-wire hoses are typically rated for up to 3,000 PSI, 2-wire hoses can handle pressures up to 6,000 PSI. This difference makes 2-wire hoses more suitable for medium to high-pressure applications.
Flexibility: 1-wire hoses are generally more flexible, making them easier to install in tight spaces, whereas 2-wire hoses, while still flexible, maybe bulkier due to additional reinforcement.
2-Wire vs. 4-Wire Hoses
Pressure Capacity: 2-wire hoses are suitable for pressures ranging from 3,000 to 6,000 PSI, while 4-wire hoses can handle pressures of 6,000 PSI and above. This makes 4-wire hoses the choice for the most demanding hydraulic systems.
Durability: The additional layers of reinforcement in 4-wire hoses provide enhanced durability, making them less susceptible to damage under extreme conditions.
Specialty Hoses
Pressure Capacity: Specialty hoses can vary greatly in pressure capacity, often designed to meet specific requirements. For instance, high-temperature hoses may have lower pressure ratings due to the materials used, while others designed for chemicals might prioritize compatibility over pressure handling.
Application-Specific Ratings: It’s essential to consider the intended application when selecting specialty hoses, as their performance metrics can differ significantly from standard hoses.
Factors Affecting Pressure Capacity
A. Hose Construction Materials
The materials used in the construction of hydraulic hoses play a vital role in determining their pressure capacity, durability, and overall performance. Here are the primary materials involved:
Rubber
Properties: Rubber hoses are known for their flexibility, resilience, and ability to withstand abrasion. They are often used in various applications due to their affordability and ease of handling.
Limitations: However, rubber can be sensitive to environmental factors, such as UV light and ozone, which can degrade its properties over time. Additionally, rubber hoses may have lower pressure ratings compared to hoses made from synthetic materials.
Thermoplastic
Properties: Thermoplastic hoses are lightweight, flexible, and resistant to chemicals and UV radiation. They are often used in applications where flexibility and chemical compatibility are crucial.
Limitations: While thermoplastic hoses can offer higher pressure ratings than rubber hoses, they may not withstand extreme temperatures as effectively. The specific type of thermoplastic used can significantly impact the hose’s overall performance and pressure capacity.
Steel Wire Reinforcement
Properties: Steel wire reinforcement is a critical component in many hydraulic hoses, providing the necessary strength to withstand high pressures. The configuration of the steel wire (e.g., single, double, or quadruple layers) directly affects the hose’s pressure capacity.
Limitations: While steel reinforcement enhances durability, it can also make hoses less flexible. The choice of wire type (e.g., carbon steel, stainless steel) and the method of reinforcement will impact the hose’s overall performance, including its resistance to kinking and abrasion.
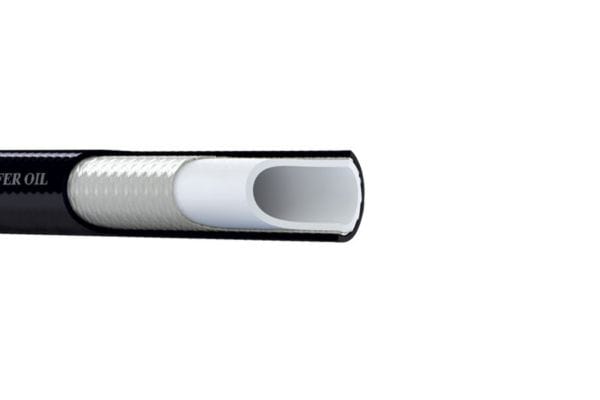
B. Bending Radius and Its Effect on Pressure
The bending radius of a hydraulic hose refers to the minimum radius the hose can be bent without compromising its integrity. This factor is crucial for ensuring optimal performance and longevity.
Impact on Pressure Capacity:
Bending a hose too tightly can significantly reduce its pressure capacity. When a hose is bent beyond its recommended radius, it can create stress points that weaken the hose material, potentially leading to failure under pressure.
Each hose type will have specific bending radius specifications provided by the manufacturer. Adhering to these guidelines is essential for maintaining the hose’s pressure rating and preventing premature wear or failure.
Installation Considerations:
During installation, it is vital to plan hose routing to minimize bends and avoid sharp turns. Using proper fittings and supports can help maintain the recommended bending radius, ensuring the hose operates within its designed pressure limits.
C. Temperature Influences on Hose Performance
Temperature is another critical factor that affects the pressure capacity and overall performance of hydraulic hoses.
Effects of High Temperatures:
Exposure to high temperatures can weaken hose materials, particularly rubber and thermoplastics. Elevated temperatures can lead to softening, resulting in reduced pressure ratings and increased susceptibility to abrasion and rupture.
Many hoses have a maximum temperature rating, and exceeding this can lead to rapid degradation of the hose material. For instance, standard rubber hoses may have a maximum temperature rating of around 200°F (93°C), while thermoplastic hoses may vary widely depending on the specific material used.
Effects of Low Temperatures:
Conversely, low temperatures can also impact hose performance. At low temperatures, materials may become brittle, increasing the risk of cracking or failing under pressure.
Some hoses are designed to operate in extreme cold, but care must be taken to ensure that they are not subjected to rapid temperature changes, which can create additional stress.
Temperature Fluctuations:
Frequent temperature changes can also lead to hose fatigue, as materials expand and contract with heating and cooling cycles. This can ultimately affect the hose’s pressure capacity and lifespan.
To mitigate these effects, selecting hoses designed for specific temperature ranges and applications is essential, as well as implementing proper thermal insulation where necessary.
Selecting the Right Hose for Your Application
Selecting the right hydraulic hose is crucial for ensuring the safety, efficiency, and longevity of hydraulic systems. This process involves a thorough assessment of various factors, including the working environment, system pressure requirements, application needs, and fluid compatibility. Here’s a detailed breakdown of these considerations:
A. Assessing the Working Environment
The working environment plays a significant role in determining the appropriate hydraulic hose for a specific application. Key factors to consider include:
Temperature Conditions:
Evaluate the typical and extreme temperature ranges in which the hose will operate. High temperatures can lead to material degradation, while low temperatures may cause brittleness. Selecting hoses rated for the specific temperature range is essential to avoid premature failure.
Environmental Hazards:
Identify any environmental hazards that may affect the hose, such as exposure to UV light, ozone, chemicals, or moisture. For instance, hoses used outdoors may require UV-resistant materials to prevent degradation over time. Additionally, hoses exposed to chemicals must be selected based on their chemical compatibility.
Physical Obstructions:
Consider the physical layout of the installation area, including any potential obstructions that may lead to kinking or bending. Proper routing is essential to maintain the hose’s integrity and pressure capacity.
Flexibility Requirements:
The flexibility of the hose is important, particularly in applications where tight bends are necessary. Assess whether the hose needs to withstand frequent movement or vibrations, and choose a design that provides the required flexibility without compromising performance.
B. Understanding System Pressure Requirements
Accurate knowledge of the hydraulic system’s pressure requirements is critical for selecting the right hose:
Maximum Operating Pressure:
Determine the maximum operating pressure of the hydraulic system. This is often specified by the equipment manufacturer. Ensure that the selected hose has a pressure rating that meets or exceeds this requirement to prevent failures.
Pressure Spikes:
Consider potential pressure spikes that may occur during operation, such as those caused by rapid system cycling or shock loads. The hose should be capable of handling these transient pressure conditions to ensure safety and reliability.
Safety Margins:
It is advisable to include a safety margin when selecting hoses. This means choosing a hose rated for higher pressures than the maximum operating pressure, providing additional protection against unforeseen circumstances.
C. Choosing Hoses Based on Application Needs
Each hydraulic application has unique requirements that influence hose selection:
Type of Hydraulic Fluid:
Different hydraulic fluids have varying viscosities and chemical properties. Ensure that the hose material is compatible with the specific fluid to prevent degradation and maintain performance.
Flow Rate:
Assess the required flow rate for the application. This can impact the hose diameter and design. Larger diameters may be necessary for higher flow rates to minimize pressure drops and ensure efficient fluid transfer.
Special Requirements:
Some applications may require specialty hoses, such as those designed for high temperatures, extreme pressures, or specific chemical applications. Understanding these unique needs is essential for making the right selection.
D. Importance of Compatibility with Fluids
Fluid compatibility is a critical consideration in hose selection:
Chemical Resistance:
The hose material must be compatible with the hydraulic fluid being used. Chemicals can degrade certain materials, leading to leaks or ruptures. Manufacturers often provide compatibility charts to assist in selecting appropriate hoses.
Fluid Temperature:
The temperature of the fluid can also affect compatibility. Some materials may perform well at room temperature but degrade at elevated temperatures. It’s essential to consider both the fluid type and the temperature range during operation.
Contaminants:
Assess the potential for contaminants in the hydraulic system, such as dirt, water, or other particles. Choosing hoses with appropriate filters or barriers can prevent damage and ensure long-lasting performance.
Conclusion
Understanding pressure capacity is not just a technical requirement; it is fundamental to the safe and effective operation of hydraulic systems across various industries. By prioritizing this knowledge, professionals can make informed decisions that enhance both operational efficiency and safety. The right hose, selected with care and maintained diligently, can significantly contribute to the overall performance and longevity of hydraulic systems, reinforcing the critical nature of this often-overlooked component.
FAQ
What is hose pressure capacity?
Hydraulic hose pressure capacity is the maximum internal pressure a hose can safely withstand during operation without failing.
How is pressure measured in hydraulic systems?
Pressure is commonly measured in pounds per square inch (PSI) or bars, where 1 bar is approximately equal to 14.5 PSI.
What types of hydraulic hoses are available?
Common types include 1-wire hoses, 2-wire hoses, 4-wire hoses, and specialty hoses, each designed for different pressure capacities and applications.
What factors affect the pressure capacity of a hydraulic hose?
Key factors include hose construction materials, bending radius, temperature conditions, and compatibility with hydraulic fluids.
Why is it important to choose the right hydraulic hose?
Selecting the correct hose ensures safety, reliability, and efficiency in hydraulic systems, preventing failures and reducing maintenance costs.
How often should hydraulic hoses be inspected?
Hydraulic hoses should be inspected regularly for wear, damage, and leaks to ensure they remain safe and functional throughout their lifespan.