At the heart of these systems lies the hydraulic hose, a vital component that facilitates fluid transfer under pressure. Proper selection of hydraulic hoses is essential, as it directly impacts the system’s performance, safety, and longevity. Choosing the wrong hose can lead to catastrophic failures, downtime, and costly repairs, making it imperative for buyers to understand the factors contributing to an informed purchase.
Understanding Hydraulic Hoses
A. Definition and Function of Hydraulic Hoses
Hydraulic hoses are flexible tubes designed to transport hydraulic fluid within a hydraulic system. Their primary function is to transmit power generated by the hydraulic fluid, which is often oil, from one component to another, such as from a pump to an actuator. The efficient transfer of fluid is crucial for the operation of machinery, as it enables precise control of movement and force. Hydraulic hoses are engineered to withstand high pressures and diverse environmental conditions, making them essential for maintaining the safety and efficiency of hydraulic systems.
B. Types of Hydraulic Hoses
Hydraulic hoses are categorized into two main types: standard hoses and specialty hoses, each serving specific applications.
Standard Hoses: Standard hydraulic hoses are commonly used in a variety of industrial applications. They are designed to meet general requirements for pressure, flexibility, and temperature. These hoses are often made from synthetic rubber or thermoplastic materials, providing a balance of durability and flexibility. Typical applications include construction equipment, manufacturing machinery, and agricultural equipment. Standard hoses come in various sizes and pressure ratings, making them versatile for many uses.
Specialty Hoses: Specialty hydraulic hoses are designed for specific applications that require unique properties. These hoses can be constructed to withstand extreme temperatures, aggressive chemicals, or high levels of abrasion. For example, hoses used in food processing must meet strict sanitation standards, while those in the aerospace industry may require materials that resist fuel and oil degradation. Specialty hoses ensure that hydraulic systems operate efficiently in challenging environments, addressing needs that standard hoses may not fulfill.
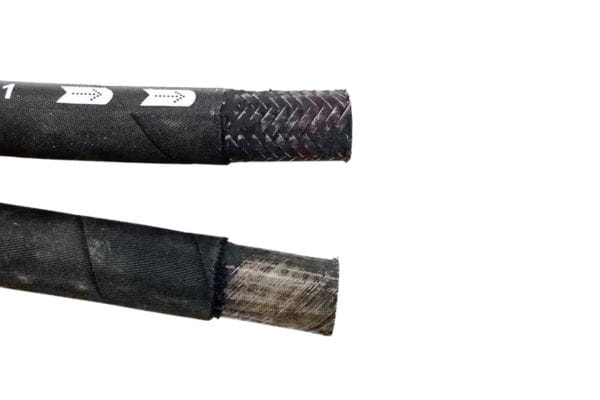
C. Key Components and Terminology
Understanding the anatomy of hydraulic hoses is crucial for selecting the right one for your application. Here are the key components and terminology associated with hydraulic hoses:
Inner Tube: The inner tube is the core component of the hydraulic hose that directly contacts the hydraulic fluid. It is typically made from synthetic rubber, thermoplastic, or other materials that can withstand the fluid’s properties. The material must be compatible with the specific hydraulic fluid to prevent degradation or failure. The inner tube is designed to handle the pressure exerted by the fluid, which is critical for the hose’s overall performance.
Reinforcement Layers: Surrounding the inner tube are reinforcement layers, which provide structural integrity and strength. These layers are made from materials such as textile or steel wire, offering resistance to pressure and external forces. The number and type of reinforcement layers determine the hose’s pressure rating and flexibility. A well-reinforced hose can handle higher pressures and is less likely to collapse or burst under strain, ensuring reliability in demanding applications.
Cover Material: The outer cover of a hydraulic hose protects the inner components from external damage, including abrasion, UV exposure, and chemicals. The cover is typically made from rubber or thermoplastic, designed to withstand environmental hazards while maintaining flexibility. The choice of cover material is critical, especially in applications exposed to harsh conditions, as it contributes to the hose’s longevity and performance.
Common Pitfalls in Hydraulic Hose Purchases
A. Choosing the Wrong Type of Hose
One of the most significant pitfalls in purchasing hydraulic hoses is selecting the wrong type. This can lead to performance issues, safety hazards, and increased maintenance costs.
Material Compatibility: Different hydraulic fluids have specific chemical compositions that can react adversely with certain hose materials. For instance, using a rubber hose with oil-based fluids might lead to degradation of the hose over time, resulting in leaks or ruptures. It’s crucial to verify that the hose material is compatible with the hydraulic fluid intended for use. This consideration is particularly vital in applications involving aggressive chemicals or high temperatures, where the wrong material choice can lead to rapid hose failure.
Pressure Ratings: Every hydraulic hose is designed to operate under specific pressure conditions. Choosing a hose with an inadequate pressure rating for the intended application can be catastrophic. If the operating pressure exceeds the hose’s rated limit, it can lead to bursting, causing equipment damage and posing safety risks. It’s essential to consider both the maximum working pressure and the potential for pressure spikes during operation when selecting a hose. Always opt for hoses that exceed the expected maximum pressure to ensure safety and reliability.
B. Ignoring Environmental Conditions
Environmental factors play a crucial role in the performance and longevity of hydraulic hoses. Ignoring these conditions can lead to premature failure and operational inefficiencies.
Temperature Extremes: Hydraulic hoses must be able to withstand the temperature ranges in which they will operate. Extreme heat can cause hoses to soften or warp, while extreme cold can make them brittle, leading to cracks and leaks. Additionally, temperature fluctuations can affect the viscosity of the hydraulic fluid, impacting system performance. It’s important to select hoses rated for the specific temperature ranges of the intended application, taking into account both operational and ambient temperatures.
Chemical Exposure: Hydraulic hoses may be exposed to various chemicals, including oils, solvents, and cleaning agents. If the hose material is not resistant to these chemicals, it can deteriorate quickly, leading to leaks and system failures. Assessing the chemical environment and choosing hoses specifically designed to resist those chemicals is vital. For example, hoses used in industries like agriculture or food processing may need to meet stringent regulatory standards for chemical resistance to ensure safety and compliance.
C. Inadequate Sizing and Fitting Considerations
Another common mistake is failing to properly size hydraulic hoses and fittings. Incorrect sizing can lead to inefficiencies, increased wear, and potential hazards.
Diameter and Length Issues: The diameter of a hydraulic hose significantly impacts flow rate and system efficiency. Using a hose that is too small can restrict fluid flow, leading to decreased performance and increased pump wear. Conversely, a hose that is too large may create turbulence and reduce overall efficiency. Additionally, the length of the hose matters; longer hoses can lead to increased pressure drops. It’s crucial to calculate the appropriate diameter and length based on system requirements to maintain optimal flow and efficiency.
Fitting Types and Compatibility: Hydraulic hoses require specific fittings to connect to components, and compatibility is key. Using the wrong fitting type can result in leaks or equipment damage. It’s essential to ensure that the fittings match the hose size and type and that they are appropriate for the application. This includes considering factors such as the connection style (threaded, quick-disconnect), material compatibility, and pressure ratings. Proper installation and sealing are equally important to prevent failures, which can occur due to improper fittings or misalignment during assembly.
How to Avoid These Pitfalls
To ensure a successful hydraulic hose purchase and to avoid common pitfalls, a proactive approach is necessary. Here are strategies to help buyers make informed decisions:
A. Conducting Thorough Research
Understanding Application Requirements: Before making any purchase, it’s essential to fully understand the specific requirements of your application. This includes knowing the type of hydraulic fluid used, the operating pressure and temperature ranges, and any special conditions that may affect performance. Gathering this information helps in selecting the right hose type and ensures that it meets all operational criteria. Creating a checklist of requirements can aid in the decision-making process and provide a clear framework for evaluation.
Consulting with Experts: Engaging with industry experts, such as hydraulic specialists or engineers, can provide invaluable insights. These professionals can offer guidance based on their experience, helping to identify suitable hose options and best practices. Additionally, consulting manufacturers’ representatives can provide access to technical resources, product specifications, and recommendations tailored to specific applications. Leveraging expert knowledge not only enhances the selection process but also mitigates the risk of making costly mistakes.
B. Properly Assessing Environmental Factors
Identifying Potential Hazards: Assessing the environment where the hydraulic hose will be used is critical. Consider factors such as exposure to extreme temperatures, UV radiation, moisture, and chemicals. Conducting a risk assessment can help identify potential hazards that the hose may face. This information is vital for selecting hoses designed to withstand these conditions, ensuring durability and performance over time.
Choosing Appropriate Materials: Once the environmental conditions have been assessed, selecting hoses made from materials suited to those conditions becomes paramount. For instance, if the hose will be exposed to chemicals, choose materials that are known for their chemical resistance. Similarly, for high-temperature applications, select hoses rated for elevated temperatures. Understanding the properties of different materials, such as rubber, thermoplastic, and composite options, will aid in making informed selections that enhance reliability and safety.
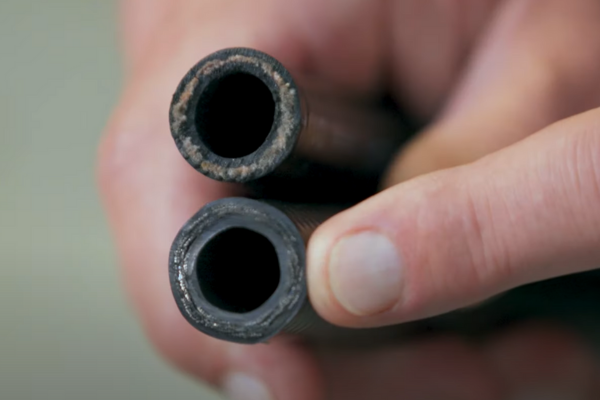
C. Ensuring Correct Sizing and Fitting
Tools for Measurement: Accurate measurement is crucial when selecting hydraulic hoses and fittings. Using tools like calipers or hose measurement kits can help determine the correct diameter and length needed for your application. Additionally, using pressure gauges can ensure that the selected hose can handle the expected pressure. Taking precise measurements before purchasing can prevent issues related to improper sizing, ensuring that hoses fit correctly and function effectively within the system.
Guidelines for Selection: Following established guidelines for hose selection can streamline the process. Start by referring to manufacturer specifications, which often outline recommended hose types for specific applications. Familiarize yourself with industry standards, such as those set by the Society of Automotive Engineers (SAE) and the International Organization for Standardization (ISO), as these provide benchmarks for hose performance and safety. When selecting fittings, ensure they are compatible with the hose and the components they connect to, considering factors like thread types, sizes, and pressure ratings.
Best Practices for Purchasing Hydraulic Hoses
Selecting the right hydraulic hose is only part of the equation; choosing the right vendor and ensuring adherence to industry standards are equally crucial. Here are the best practices to guide the purchasing process:
A. Vendor Selection
Evaluating Suppliers: Choosing a reliable supplier is essential for obtaining quality hydraulic hoses. Start by researching potential vendors, looking for those with a solid reputation in the industry. Check customer reviews, testimonials, and case studies to gauge their reliability and customer service. Engaging with multiple suppliers can provide insights into their product offerings, pricing, and delivery times. Building relationships with reputable vendors can lead to better service and support over time.
Importance of Quality Assurance: Quality assurance is paramount when it comes to hydraulic hoses. Ensure that the supplier follows rigorous quality control processes throughout production. Inquire about their manufacturing practices and whether they comply with relevant standards. Suppliers that prioritize quality assurance are more likely to provide hoses that meet or exceed performance expectations, ultimately reducing the risk of failure and enhancing system reliability.
B. Reviewing Certifications and Standards
Industry Standards (SAE, ISO): Familiarize yourself with industry standards relevant to hydraulic hoses, such as those set by the Society of Automotive Engineers (SAE) and the International Organization for Standardization (ISO). These standards provide guidelines for performance, safety, and compatibility. Ensuring that the hoses you purchase meet these standards is crucial for operational safety and efficiency. Always ask for certification documentation from your supplier to verify compliance.
Manufacturer Warranties: Warranties are an important consideration when purchasing hydraulic hoses. A strong warranty indicates that the manufacturer stands behind their product’s quality and performance. Review the warranty terms, including coverage duration and conditions, to ensure adequate protection against defects and failures. A good warranty can provide peace of mind and financial protection, especially in critical applications where hose failure can lead to costly downtime.
C. Importance of After-Sales Support
Technical Assistance: After purchasing hydraulic hoses, having access to technical support can significantly enhance the overall experience. Choose vendors that offer comprehensive technical assistance, including guidance on installation, maintenance, and troubleshooting. This support can help address any issues that arise post-purchase, ensuring that you get the most out of your hoses and minimize operational disruptions. Vendors that provide accessible technical resources demonstrate a commitment to customer satisfaction.
Replacement and Repair Services: Over time, even the best hydraulic hoses may require replacement or repair. Opt for suppliers that offer robust after-sales services, including replacement parts and repair options. A vendor that provides these services can save you time and money in the long run, as they will understand the specific needs of your system and can supply compatible replacements quickly. Additionally, having a reliable repair service can reduce downtime and keep your operations running smoothly.
Conclusion
Note that choosing a quality hydraulic hose is more than just focusing on price, it’s about focusing on practicality. If you have any hydraulic hose needs, please feel free to contact Topa, we can provide you with the best quality products.
FAQ
What is the primary function of hydraulic hoses?
Hydraulic hoses transport hydraulic fluid under pressure to facilitate the operation of machinery and equipment in hydraulic systems.
How do I know which type of hydraulic hose to choose?
Consider factors such as the type of hydraulic fluid, operating pressure, temperature range, and any environmental conditions the hose will face.
What are the consequences of using the wrong hydraulic hose?
Using the incorrect hose can lead to leaks, ruptures, reduced efficiency, and safety hazards, potentially resulting in costly repairs and downtime.
Why is material compatibility important in hydraulic hose selection?
Different materials react differently to various fluids. Ensuring compatibility prevents degradation and extends the hose’s lifespan.
What should I check when evaluating a hose supplier?
Look for a supplier’s reputation, quality assurance processes, industry certifications, and after-sales support, including technical assistance.
How can I ensure proper sizing of hydraulic hoses?
Use precise measuring tools to determine the necessary diameter and length, and consult manufacturer guidelines to confirm compatibility with fittings and system requirements.