When hydraulic hoses are compromised due to wear, improper installation, or incorrect selection, the entire system is at risk. The consequences of neglecting hydraulic hose safety are severe. In addition to costly repairs and extended downtime, a failed hose can lead to hazardous leaks that harm the environment or even cause workplace injuries. Ensuring proper hydraulic hose maintenance and safety protocols is not just a matter of operational efficiency; it is a critical aspect of safeguarding workers, protecting equipment, and maintaining the environmental integrity of the workplace.
Mistake #1: Incorrect Hose Selection
Explanation of the Mistake
Selecting the wrong hydraulic hose for an application is a common mistake in hydraulic system design and maintenance. This can involve choosing hoses not meet the system’s specific pressure rating, temperature range, or fluid compatibility requirements. For example, a hose designed for low-pressure applications may be mistakenly used in a high-pressure environment, leading to overstressing. In other cases, a hose that is incompatible with certain hydraulic fluids may deteriorate over time. Additionally, the hose’s flexibility and ability to withstand harsh environmental conditions, such as UV exposure or chemical exposure, are often overlooked, which can further contribute to premature failure.
Consequences
The consequences of using an incorrect hose extend beyond inefficiency. Premature hose failure is a serious issue that can cause fluid leakage, leading to contamination and system inefficiency. Moreover, unexpected hose bursts or leaks can result in serious accidents, posing a significant safety hazard to operators and maintenance workers. Beyond personnel safety, improper hose selection can also lead to damage to equipment, resulting in costly repairs and lengthy downtime. In extreme cases, it can even lead to environmental damage through fluid spills, causing regulatory issues and cleanup expenses.
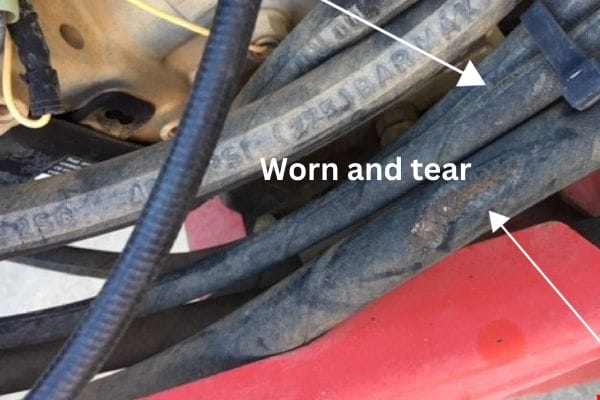
Best Practices
Use the STAMPED Method: The STAMPED method (Size, Temperature, Application, Media, Pressure, Ends, Delivery) provides a systematic approach to hose selection:
Size: Ensure the hose has the correct internal and external diameter for the system.
Temperature: Select a hose rated for the operational temperature range.
Application: Match the hose to the specific mechanical and environmental demands.
Media: Ensure the hose material is compatible with the fluid being transported.
Pressure: Verify the hose’s pressure rating meets or exceeds system pressure requirements.
Ends: Choose appropriate connectors and fittings for a secure attachment.
Delivery: Consider factors like hose length and routing to ensure proper delivery of hydraulic fluid.
Collaboration with Experts: Always consult with trusted suppliers or hydraulic specialists when selecting hoses. Their expertise can help ensure that the chosen hose meets all operational demands and is suitable for the specific system and application.
Mistake #2: Improper Hose Installation
Explanation of the Mistake
Improper hose installation is a frequent issue in hydraulic systems and often results from a lack of attention to detail or a misunderstanding of the system’s requirements. Common installation errors include improper routing, where hoses are either too tight or too loose in their pathways, resulting in over-bending or twisting. Twisting can weaken the hose’s structure, making it more susceptible to leaks and bursts. Using inappropriate connectors that don’t match the hose’s specifications further exacerbates these problems, leading to poor sealing and potentially dangerous conditions. Additionally, failing to account for system movement or vibration places added stress on the hose, increasing wear and reducing its operational life.
Consequences
Incorrect installation places excessive strain on hoses and their fittings, accelerating wear and tear. Over time, this can lead to premature failure in the form of leaks, bursts, or other malfunctions, disrupting operations and creating safety hazards for personnel. Even a minor leak can cause a drop in system efficiency, increase operating costs, and lead to unnecessary repairs. In more severe cases, a hose burst can lead to system shutdowns, expensive repairs, and injury to workers due to high-pressure fluid release.
Best Practices
Follow Manufacturer Guidelines: Adhering to manufacturer recommendations for installation is critical. Pay close attention to the minimum bend radius, as exceeding this can cause the hose to kink or collapse, reducing flow and increasing wear. Also, ensure correct routing paths that prevent over-bending or sharp angles.
Use Clamps and Supports: To mitigate the effects of movement, vibration, and bending, it is essential to install clamps, supports, or guides. These components help to secure the hose in place, reducing the amount of flexing and movement that can lead to early failure. Proper support will also minimize the impact of external forces on the hose’s integrity.
Install Hose Protection Sleeves: Adding protection sleeves can help to shield hoses from external abrasions, particularly in environments where contact with sharp objects or rough surfaces is common. These sleeves act as a barrier, extending the hose’s lifespan and preventing surface damage that can lead to leaks or bursts.
Mistake #3: Failure to Inspect and Maintain Hoses Regularly
Explanation of the Mistake
Regular inspections and maintenance of hydraulic hoses are often overlooked or delayed, which can leave critical issues such as wear, cracks, abrasions, and leaks unnoticed. Over time, hydraulic hoses naturally degrade due to exposure to pressure, temperature variations, and environmental factors like UV radiation or chemicals. When inspections are skipped or maintenance is deferred, these minor issues can escalate into major problems, putting the entire hydraulic system at risk.
Consequences
The consequences of neglecting regular inspection and maintenance are severe. Undetected damage can lead to sudden hose failures, causing system breakdowns, increased downtime, and significant productivity losses. Not only do these failures result in expensive repairs, but they also raise safety risks for personnel, as leaks or bursts under pressure can lead to serious injuries. Additionally, leaks pose environmental hazards, especially if harmful fluids are involved, potentially leading to costly cleanup efforts and regulatory fines.
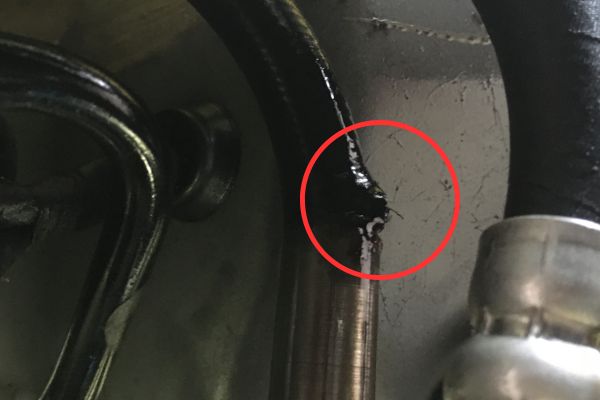
Best Practices
Establish a Routine Inspection Schedule:
Implement a consistent inspection routine based on the operating conditions and manufacturer recommendations. Visual checks should look for signs of wear, abrasions, cracking, or deformation. By scheduling these inspections regularly, operators can catch potential problems early, preventing catastrophic failures.
Monitor for Fluid Leaks:
Regularly check for any signs of fluid leakage, which can indicate hose damage. Leaks should be addressed immediately, and damaged hoses must be replaced as soon as they are detected. Depending on the operational environment and the types of fluids in use, small leaks can quickly turn into dangerous spills or lead to a complete system shutdown.
Replace Hoses at Recommended Intervals:
Even if no visible damage is detected, hoses should be replaced at intervals recommended by the manufacturer. Hydraulic hoses have a finite lifespan, and proactive replacement reduces the risk of unexpected failures.
Mistake #4: Over-Pressurizing the Hose
Explanation of the Mistake
Operating hydraulic hoses at pressures beyond their rated capacity is a common but dangerous error that can have serious consequences. Pressure spikes during equipment startup, shutdown, or due to sudden system changes are often overlooked. These spikes can exceed the hose’s pressure rating, leading to overstressing of the hose material. Hydraulic hoses are designed with specific pressure ratings, and exceeding these limits, even briefly, can weaken the hose structure, causing it to fail prematurely.
Consequences
Over-pressurization of hoses can cause catastrophic failures such as hose bursts, which pose significant safety risks to personnel working near hydraulic systems. High-pressure hydraulic fluid escaping from a ruptured hose can lead to severe injuries and even fatalities in extreme cases. Additionally, hose bursts can result in system failures, causing costly downtime and requiring expensive repairs or replacements of damaged components. Beyond the direct costs, over-pressurization can also lead to indirect costs, such as equipment damage and environmental hazards due to fluid spills.
Best Practices
Ensure Proper Pressure Ratings:
Always ensure that the hydraulic hoses selected for a system match the pressure requirements of the operating environment, with an appropriate safety margin. This includes considering not only the regular operating pressure but also the potential for pressure spikes.
Use Pressure Relief Valves and Regulators:
Installing pressure relief valves and regulators within the hydraulic system can help control operating pressures and prevent spikes from exceeding the hose’s rated capacity. These devices act as safeguards by automatically releasing pressure when it exceeds safe levels, protecting both the hoses and the system as a whole.
Monitor System Pressure:
Continuous monitoring of system pressure is essential for identifying and addressing overpressurization early. Using pressure gauges or automated sensors, operators can keep track of real-time pressure levels. If any anomalies are detected, immediate corrective action can be taken to prevent hose damage.
Mistake #5: Neglecting Hose Compatibility with Fluids
Explanation of the Mistake
One of the most commonly overlooked mistakes in hydraulic system management is failing to ensure that the hoses used are compatible with the specific fluids they will carry. Hydraulic systems often operate with a variety of fluids, such as petroleum-based oils, synthetic fluids, or water-based solutions. Each type of fluid has unique chemical properties that interact differently with the materials used to manufacture hydraulic hoses. When hose compatibility is not properly verified, these interactions can lead to internal chemical degradation of the hose material. This degradation may go unnoticed because it typically occurs within the hose, making it difficult to detect until it becomes a significant issue, potentially resulting in sudden hose failure during operation.
For instance, a hose that is designed to carry petroleum-based fluids might degrade rapidly when exposed to synthetic or water-based fluids. Over time, this internal deterioration weakens the hose’s structure, compromising its ability to maintain proper pressure and flow. Left unchecked, this can lead to a catastrophic failure, such as a burst hose, which can cause a loss of hydraulic fluid, damage to the system, and pose serious safety risks to personnel.
Consequences
The consequences of neglecting fluid compatibility can be severe. When an incompatible fluid is used, the hose material may become brittle, swell, or crack, leading to leaks or even complete rupture. These leaks can introduce contaminants into the hydraulic system, reducing efficiency and causing mechanical issues that hinder performance. As the system’s integrity is compromised, operators may experience reduced productivity due to the inefficiency of the hydraulic system. In more extreme cases, the failure of a critical hose can bring the entire operation to a halt, requiring costly repairs or replacements and leading to extended periods of downtime.
Furthermore, leaking hydraulic fluids can create hazardous working conditions for personnel. High-pressure fluid escaping from a compromised hose can result in serious injuries, including burns or puncture wounds, depending on the type of fluid and the system pressure. Environmental damage is another major concern, particularly if the fluid involved is hazardous or toxic. Fluid spills can result in significant cleanup costs, potential fines for environmental violations, and damage to the company’s reputation, particularly if the spill affects nearby ecosystems or communities.
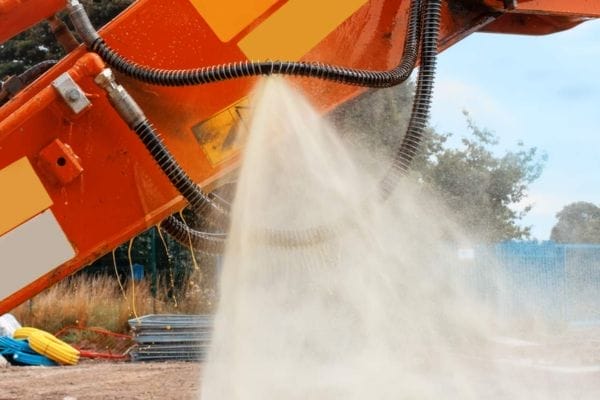
Best Practices
Verify Fluid Compatibility:
It is critical to verify that the hydraulic hoses selected for a system are fully compatible with the specific fluids they will carry. Whether the system operates on petroleum-based oils, synthetic fluids, or water-based solutions, the chemical resistance and durability of the hose material must align with the fluid’s properties. Compatibility should be assessed during the hose selection process, and any changes in fluid type should trigger a reevaluation of the hose’s suitability. This proactive approach helps to prevent unexpected hose degradation and potential system failures.
Consult Manufacturer Recommendations:
Manufacturers provide valuable resources, such as fluid compatibility charts, that detail which hose materials are best suited for different types of fluids. These charts, along with manufacturer guidelines, should be used to guide the selection process. Consulting these resources ensures that the chosen hoses will not degrade due to chemical reactions with the fluid in use. In some cases, it may also be necessary to collaborate with the hose manufacturer or a hydraulic expert to confirm that the selected hose meets all the specific operational requirements for a given application.
Test Before Implementing New Fluids:
Before introducing any new fluids into an existing hydraulic system, it is essential to test the fluid compatibility with the hoses currently in use. This involves conducting controlled tests to observe how the fluid interacts with the hose material over time. Testing fluid compatibility before full implementation can identify and resolve potential issues before they result in operational disruptions or system failures. This proactive approach not only protects the system’s integrity but also ensures that all components will function safely and efficiently with the new fluid.
Conclusion
Take a proactive approach to hydraulic system safety by auditing your equipment for any signs of these common mistakes today. Identifying and rectifying these issues now can help you safeguard your operations, minimize costly downtime, and protect your workers and environment from potential hazards.
FAQ
How often should I inspect my hydraulic hoses?
It’s recommended to inspect hydraulic hoses regularly, depending on the operating conditions. For most systems, a monthly visual inspection is a good starting point, along with scheduled maintenance checks at recommended intervals.
What causes hydraulic hoses to burst?
Hydraulic hoses can burst due to several factors, including over-pressurization, incorrect hose selection, improper installation, wear from abrasion, and fluid incompatibility.
Can I use any fluid with my hydraulic hoses?
No, not all hydraulic hoses are compatible with every fluid. You must ensure that the hose material is suited for the specific fluid in use by consulting manufacturer guidelines or fluid compatibility charts.
What are the signs that a hydraulic hose needs to be replaced?
Common signs include visible wear and tear, cracks, leaks, blisters, and kinks. If any of these signs are present, the hose should be replaced immediately to avoid failure.
How can I prevent hydraulic hose failure?
To prevent hydraulic hose failure, ensure correct hose selection using the STAMPED method, follow proper installation procedures, conduct regular inspections and maintenance, and verify fluid compatibility.
What is the STAMPED method?
The STAMPED method stands for Size, Temperature, Application, Media, Pressure, Ends, and Delivery. It’s a systematic approach used to select the correct hydraulic hose for a specific application.