Hydraulic swivel fittings, also known as live swivels, are essential components in modern hydraulic systems, enabling fluid transfer between stationary and rotating parts without leakage. They prevent hose twisting, reduce wear, and extend equipment lifespan by ensuring smooth movement in demanding environments. Crucial in industries like construction, agriculture, and aerospace, these fittings optimize machine design, minimize downtime, and enhance safety by maintaining seal integrity under high pressure, varying temperatures, and rotational stress. With ongoing advancements in materials and sealing technologies, hydraulic swivel fittings are at the heart of efficient, reliable, and compact hydraulic systems.
Working Principles and Classification of Hydraulic Swivel Fittings
Effective hydraulic swivel fitting operation depends on a well-engineered design that allows relative motion between components while maintaining a high-integrity seal for the hydraulic fluid. Understanding these principles and classifications aids in selecting the appropriate fitting for specific applications, ensuring optimal system performance and longevity.
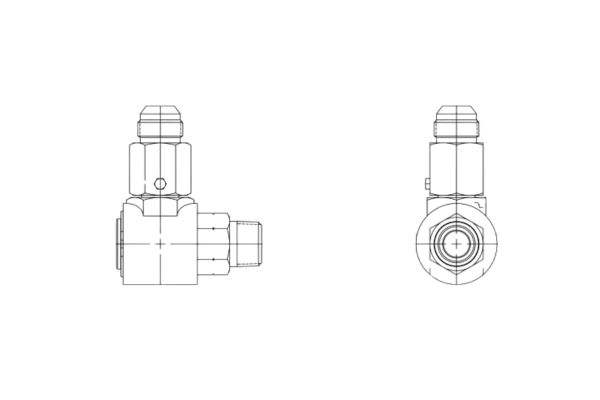
Fundamental Working Principles
The fundamental working principle involves a stationary component (housing) and a rotating component (shaft or spindle). These parts are precisely machined with internal chambers and passages that align to allow fluid flow from an inlet on one component to an outlet on the other, even during rotation. Critical elements are the bearing system (ball, roller, or plain bearings) and the sealing system. Bearings support rotational loads, ensure smooth movement, and maintain precise alignment, which is crucial for seal effectiveness. The sealing system (O-rings, lip seals, mechanical face seals) is strategically placed to prevent fluid leakage from pressurized internal passages and cross-port leakage in multi-passage swivels. As the shaft rotates, seals maintain contact with sealing surfaces. Designs must also account for hydraulic balance to minimize forces on seals and bearings, reducing friction, wear, and rotational torque, especially in high-pressure applications. Some designs use fluid pressure to counteract forces that could displace seals or increase friction. The complexity of internal passages varies from single-passage to intricate multi-passage units handling several independent hydraulic circuits, and sometimes other media like electrical signals.
Classification Based on Design and Application
Hydraulic swivel fittings are classified by criteria including design, number of flow paths, pressure ratings, mounting configurations, and specific application requirements.
Single-Passage vs. Multi-Passage Swivels
A primary classification is by the number of independent fluid paths. Single-passage swivels have one inlet and one outlet for a single hydraulic line, common in simpler applications like hose reels or single-acting cylinders. Multi-passage swivels are more complex, accommodating two or more independent hydraulic circuits through one unit. These are essential for applications needing multiple functions on a rotating component, such as controlling several actuators on an excavator boom or complex industrial machinery. They require intricate internal machining and sealing to keep fluid paths separate and prevent cross-contamination.
Classification by Pressure Rating
Swivels are categorized by maximum working pressure. Low-pressure swivels suit return lines or auxiliary systems. Medium-pressure swivels are common in general industrial and mobile applications. High-pressure and ultra-high-pressure swivels are for demanding applications like heavy construction equipment or offshore drilling, often using advanced sealing and robust materials for pressures exceeding several hundred bar. Pressure rating significantly influences design, material selection, and cost.
Classification by Mounting Configuration
Mounting configuration is another differentiator. Inline swivels install directly into a hydraulic line, with threaded or flanged connections. 90-degree (elbow) swivels provide a right-angle connection, useful for space constraints or specific routing. Cartridge-style swivels integrate directly into a manifold or machine component, offering a compact installation. Flange-mounted and base-mounted swivels provide specific interfaces for secure attachment to machine structures. The choice depends on machine design, space, and load conditions.
Key Technical Parameters of Hydraulic Swivel Fittings
Selecting the right hydraulic swivel fitting requires careful consideration of technical parameters defining its performance, compatibility, and suitability. These ensure the fitting withstands operational demands and integrates seamlessly.
Performance Parameters
Performance parameters dictate operational limits and efficiency.
Working Pressure: Maximum continuous hydraulic pressure (bar or psi) the swivel can safely handle. Exceeding this can cause seal failure or structural damage. Dynamic pressure spikes and cycles also affect fatigue life.
Rotational Speed: Maximum continuous or intermittent speed (RPM) without compromising seal integrity or causing excessive heat. High-speed applications need specialized bearings and seals. Permissible speed can be influenced by pressure and fluid type.
Flow Rate: Volume of fluid (LPM or GPM) passing through without excessive pressure drop or velocity. Undersizing leads to energy loss, heat, and sluggish performance. Internal passage design and port sizes are key.
Temperature Range: Minimum and maximum ambient and fluid temperatures for reliable operation. Temperature affects fluid viscosity, seal properties, and bearing lubrication. Materials must be compatible with the expected range.
Connection and Compatibility Parameters
These ensure correct installation and compatibility with system fluid and environment.
Connection Type and Size: Hydraulic port types (NPT, BSPP, SAE O-ring boss, JIC, flanges) and nominal dimensions (e.g., 1/4″, M22x1.5). Correct selection ensures a leak-proof, sound interface.
Fluid Compatibility: Types of hydraulic fluids compatible with internal components, especially seals (mineral oils, synthetics, water-glycol). Incompatibility leads to seal degradation and failure. Fluid viscosity and filtration requirements are also important.
Durability and Reliability Parameters
These relate to expected lifespan and robustness.
Material Selection: Body, shaft, bearings, and seals chosen for strength, wear resistance, corrosion resistance, and compatibility. Common body/shaft materials include carbon steel (often coated) and stainless steel. Seal materials vary widely.
Seal Life and Leak Rate: Expected operational life of seals (hours/rotations) and maximum permissible leak rate. Modern designs aim for near-zero leakage.
Environmental Resistance: Ability to withstand dust, water ingress (IP rating), corrosive atmospheres, vibration, and shock loads. Protective coatings and robust designs contribute to this.
Sealing Technologies and Materials in Hydraulic Swivel Fittings
The sealing system is arguably the most critical aspect, dictating the fitting’s ability to contain high-pressure fluid during rotation, its lifespan, and reliability. Innovations in sealing technologies and materials are central to advancing performance.
Overview of Sealing Technologies
Various sealing technologies, often combined, achieve effective static and dynamic sealing.
Static Sealing Technologies: Used at non-moving interfaces (e.g., body to port connectors). Common static seals include O-rings, metal-to-metal face seals, or bonded seals. Thread seals (tapered threads with sealant) are also used at connection points.
Dynamic Sealing Technologies: Essential for sealing between the rotating shaft and stationary housing. Lip seals (U-cups, V-rings, spring-energized PTFE seals) are widely used, their flexible lips energized by fluid pressure. Mechanical face seals (two precision-lapped flat surfaces) offer excellent sealing for high-pressure, high-speed applications but are more complex. Combination seals integrate multiple elements for enhanced performance and redundancy. Labyrinth seals (non-contact) may protect primary seals from contaminants.
Pressure-Balanced Designs: In high-pressure applications, fluid pressure can cause high seal friction and wear. Pressure-balanced designs route fluid pressure to act on both sides of the seal, largely canceling out the net force, reducing contact pressure, friction, and wear, extending seal life and allowing higher operating pressures/speeds.
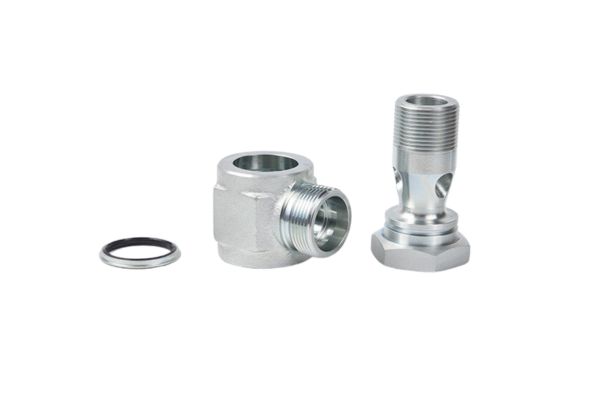
Common Sealing Materials
Material choice depends on fluid compatibility, temperature, pressure, speed, and cost.
Elastomers: Widely used for flexibility. Nitrile Rubber (NBR) is common for standard hydraulic oils (good oil resistance, low cost) but has temperature limitations. Fluoroelastomers (FKM, Viton®) offer excellent resistance to high temperatures and chemicals but are costlier and may have poorer low-temperature flexibility. Ethylene Propylene Diene Monomer (EPDM) suits water-based fluids. Polyurethane (PU) provides excellent abrasion resistance for high-pressure dynamic applications.
Plastics and Thermoplastics: Offer low friction and chemical inertness. Polytetrafluoroethylene (PTFE) is widely used for dynamic seals, often in filled grades (carbon, glass, bronze) to improve wear and creep resistance. Polyether Ether Ketone (PEEK) is a high-performance thermoplastic for extreme strength, wear, and temperature capability, but is expensive. Acetal (POM) or Nylon (PA) may be used for backup rings or specific components.
Composite Materials: Such as carbon-fiber or glass-fiber reinforced PTFE, enhance mechanical properties like wear resistance and dimensional stability. Bronze-filled PTFE improves thermal conductivity. These are found in high-performance fittings for arduous conditions.
Failure Analysis and Solutions for Hydraulic Swivel Fittings
Despite robust designs, swivel fittings can fail. Understanding common failure modes, root causes, and corrective actions is crucial for maintaining system reliability and safety.
Common Failure Types and Symptoms
Failures manifest in several ways.
Leakage Issues: Most common. External leakage is visible fluid escape. Internal leakage (fluid bypassing seals between passages) is harder to detect but causes functional anomalies like slow actuator movement or overheating.
Mechanical Issues: Abnormal noise (whining, grinding) indicates bearing wear, poor lubrication, or interference. Increased rotational resistance or seizure can result from bearing failure, contamination, or severe seal damage.
Performance Degradation: Reduced flow rate (blockages, internal leakage) leads to slow system response. Pressure fluctuations can indicate internal seal bypass or issues with pressure balancing.
Temperature Anomalies: Overheating indicates excessive friction (failing bearings/seals), high ambient temperatures, or fluid flow problems, accelerating degradation.
Root Cause Analysis of Failures
Identifying the root cause is essential.
Causes of Leakage: Seal failure (normal wear, abrasive contaminants, poor lubrication, exceeding limits, aging, installation damage), installation errors (misalignment, incorrect torque), or operating beyond specified limits.
Causes of Mechanical Problems: Mechanical interference (thermal expansion, deformation, foreign objects), material/manufacturing defects, or bearing failure (contamination, inadequate lubrication, overload, fatigue).
Causes of Performance Degradation: Flow channel blockage (contaminants, sludge, corrosion), or system-related issues like highly contaminated fluid or improper pressure settings.
Diagnostic Techniques
A systematic approach is key.
Visual and Sensory Inspections: Check for external leaks, fluid condition, visible damage, abnormal noises, and hot spots or excessive vibration.
Measurement and Testing: Pressure testing (monitoring fluctuations, holding tests), flow testing (measuring rates), temperature monitoring (infrared thermometers/thermal cameras), and vibration analysis (detecting bearing faults/imbalance). Disassembly inspection allows detailed examination of internal components.
Solutions and Preventive Measures
Addressing failures involves corrective actions and preventive strategies.
Corrective Actions: For leakage, seal replacement with OEM-quality seals and proper installation procedures. For mechanical issues, bearing replacement, alignment correction, or contaminant removal. If defects are found, component replacement or redesign might be needed.
Preventive Maintenance: Scheduled inspections for leaks, noise, temperature. Regular hydraulic fluid analysis and maintaining cleanliness through filtration. Adhering to lubrication schedules. Training operators. Implementing predictive maintenance (vibration analysis, thermal imaging). Operating within design specifications is fundamental.
Market Analysis and Future Outlook for Hydraulic Swivel Fittings
The hydraulic swivel fitting market is a dynamic segment within the fluid power industry, influenced by global economic trends, technological advancements, and evolving end-user needs.
Global Market Size and Growth Trends
Market research indicates consistent growth, linked to industries like construction machinery, industrial automation, and mining. The global hydraulic/pneumatic swivel joint market was ~$326 million in 2024, projected to $468 million by 2031 (CAGR ~5.5%). The broader swivel joint market (all types) was ~$3.33 billion in 2024, expected to reach ~$5.48 billion by 2034 (CAGR ~5.1%), underscoring sustained demand.
Regional Distribution: Asia-Pacific leads (~40%, China dominant), driven by industrialization. North America (~25%) demands high-technology swivels (aerospace, defense). Europe (~20%) emphasizes eco-friendliness and standards. Other regions (~15%) grow with infrastructure, mining, and oil & gas.
Key Application Segments: Construction equipment (~35%) is dominant. Injection molding/die casting machinery (~25%) is fueled by demand for plastic and lightweight metal parts. General hydraulic systems (~20%) and oil & gas equipment (~15%) are also significant. Niche applications include renewable energy and medical devices.
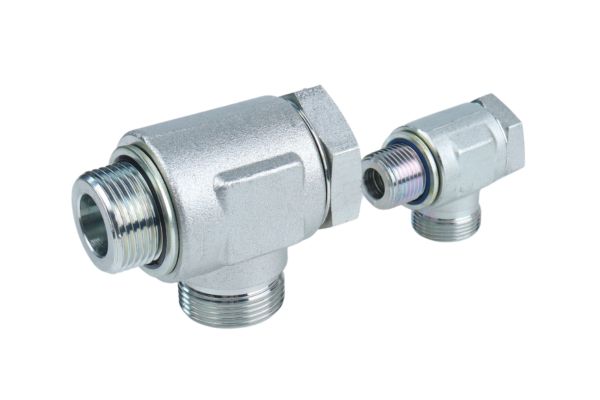
Key Market Drivers
Several forces propel market growth.
Rising Demand for Industrial Automation: Industry 4.0 and smart manufacturing require advanced, reliable fluid transmission components, including high-precision swivels for automated lines and robotics.
Focus on Energy Efficiency and Environmental Performance: Sustainability concerns push for low-friction designs, advanced sealing to minimize leakage, eco-compliant materials, and extended lifespan to reduce waste.
Accelerated Industrialization in Emerging Markets: Rapid industrial growth in developing regions (Asia, Latin America, Africa) fuels demand for hydraulic systems and components.
Technological Advancements: Innovations in materials (composites, advanced elastomers) and engineering (CFD/CAD tools, precision machining) elevate performance and application range.
Market Challenges and Restraints
The market faces certain challenges.
Price Sensitivity and Competition: The standard swivel market can be price-sensitive, with competition from global and regional manufacturers. Differentiation through quality and features is crucial.
Raw Material Price Volatility: Fluctuations in prices of steel, alloys, and polymers impact manufacturing costs. Supply chain disruptions also pose challenges.
Rise of Alternative Technologies: Electrification and electro-mechanical actuators are alternatives in some niches, potentially moderating growth in specific segments.
Future Trends and Opportunities
Emerging trends shape the market’s future.
Smart and IoT-Enabled Swivel Fittings: Growing interest in integrating sensors for condition monitoring and predictive maintenance, providing data for optimizing schedules and preventing failures.
Customization and Application-Specific Solutions: Increasing demand for swivels tailored to specific needs (unique space constraints, extreme conditions, combined fluid/electrical transmission).
Enhanced Durability and Maintenance-Free Designs: End-users seek longer service lives and reduced maintenance to minimize downtime and total cost of ownership.
Focus on Compactness and Higher Power Density: Trend towards more compact machinery necessitates swivels handling higher pressures/flows in smaller envelopes, requiring design and material innovation.
Conclusion
With advancements in materials, sealing technologies, and manufacturing, they continue to drive innovation in industries from construction to automation. As global industrialization and automation progress, the demand for energy-efficient solutions further accelerates their growth. While challenges like price competition and alternative technologies remain, the future of hydraulic swivel fittings looks bright, with smart swivels and tailored designs offering new opportunities. For a deeper dive into this topic, email Topa for a comprehensive white paper on hydraulic swivel fittings.