Hydraulic and pneumatic systems are integral to a wide array of industries, enabling efficient power transmission and automation. Hydraulic systems utilize incompressible liquids, typically oil, to transmit force and motion. They are renowned for their ability to handle heavy loads and generate high pressure, making them ideal for applications like construction equipment and industrial machinery. In contrast, pneumatic systems rely on compressed air to achieve similar tasks. While they are generally lighter and simpler, they excel in applications requiring rapid movement and flexibility, such as packaging and assembly lines.
Understanding Hydraulic Systems
Definition and Functionality
Hydraulic systems are mechanisms that use pressurized liquids to transmit power. At their core, they operate on Pascal’s principle, which states that pressure applied to a confined fluid is transmitted undiminished in all directions. This allows for the efficient transfer of force, enabling machinery to lift heavy loads, operate tools, and perform various mechanical functions. By using hydraulic fluid—commonly oil—these systems can generate significant force in a compact design, making them essential in applications requiring high power density.
Common applications of hydraulic systems span various industries, with a notable presence in the construction, manufacturing, and automotive sectors. In construction, hydraulic excavators and lifts utilize these systems for digging, lifting, and material handling. Manufacturing plants employ hydraulic presses for shaping materials and assembling components, while automotive workshops utilize hydraulic jacks and lifts for vehicle maintenance. The versatility and effectiveness of hydraulic systems in managing heavy-duty tasks make them indispensable across many sectors.
Components of Hydraulic Systems
Hydraulic systems consist of several key components that work together to create a functional network. The primary elements include:
Pumps: These devices generate flow by converting mechanical energy into hydraulic energy, creating pressure within the system. They are crucial for maintaining fluid movement.
Actuators: Actuators convert hydraulic energy back into mechanical energy, often in the form of linear or rotary motion. Common types include hydraulic cylinders and motors.
Valves: Valves control the flow and direction of hydraulic fluid within the system. They regulate pressure and ensure that the actuators operate correctly, allowing for precise movement control.
Fittings: These are connectors that link various components of the hydraulic system, ensuring a secure and leak-proof connection. Proper fittings are essential for maintaining system integrity and efficiency.
The importance of fittings cannot be overstated, as they directly impact system performance. A well-designed fitting prevents leaks and maintains pressure, contributing to overall system reliability. Inadequate fittings can result in fluid loss, reduced efficiency, and potential damage to other components.
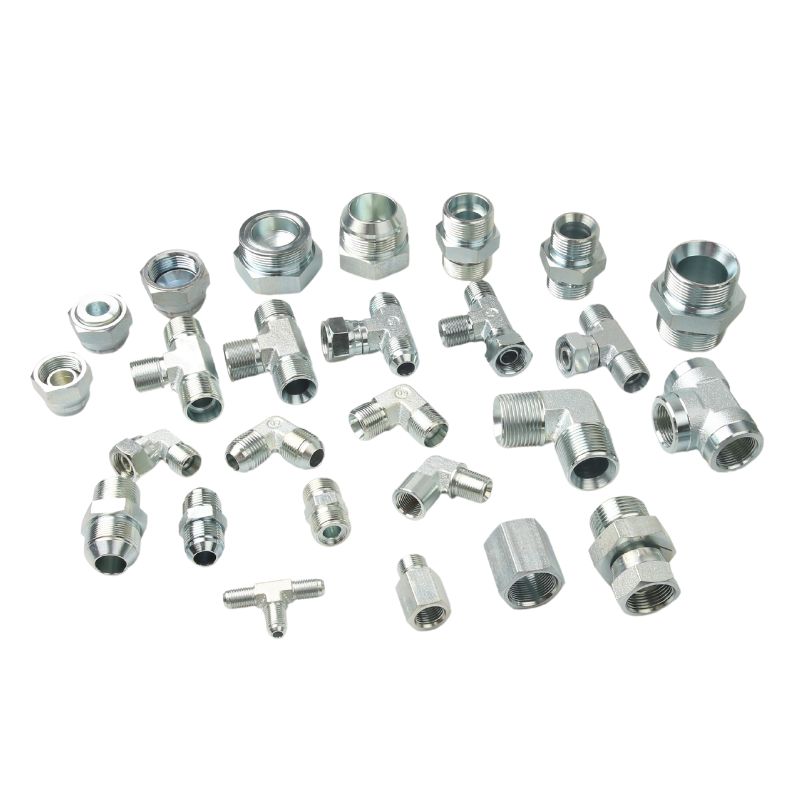
Types of Hydraulic Fittings
Hydraulic fittings come in various types, each suited for specific applications and environments. The most common types include:
O-ring Fittings: These fittings use a rubber O-ring to create a seal, preventing leaks at connection points. They are popular in high-pressure applications due to their reliability.
Flare Fittings: Flare fittings involve a conical-shaped end that creates a tight seal when tightened. They are commonly used in fuel and hydraulic lines, offering excellent resistance to vibration and thermal expansion.
Quick Couplings: These fittings allow for rapid connection and disconnection of hoses and components without the need for tools. They are essential in applications requiring frequent changes or maintenance.
Material choice for hydraulic fittings is also critical. Common materials include:
Steel: Known for its strength and durability, steel fittings are suitable for high-pressure applications but can be susceptible to corrosion.
Stainless Steel: This material offers excellent corrosion resistance, making it ideal for applications involving harsh environments or fluids.
Plastic: Lightweight and resistant to corrosion, plastic fittings are often used in low-pressure applications and environments where metal fittings may corrode.
Understanding Pneumatic Systems
Definition and Functionality
Pneumatic systems are mechanical systems that use compressed air to transmit power. They operate on the principles of fluid dynamics, where the movement of air or gas is harnessed to create motion. Compressed air serves as the medium to transfer energy, enabling the actuation of various tools and machinery. Pneumatic systems are characterized by their ability to provide rapid movement and flexibility, making them suitable for tasks requiring quick and precise actions.
Common applications of pneumatic systems are prevalent in various industries, particularly in automation, packaging, and material handling. In automated production lines, pneumatic systems control robotic arms and conveyors, facilitating efficient movement and assembly of products. In the packaging industry, pneumatic mechanisms are employed for filling, sealing, and labeling products. Their versatility allows them to excel in tasks such as clamping, gripping, and transporting items, all while minimizing energy consumption and wear on machinery.
Components of Pneumatic Systems
Pneumatic systems consist of several essential components that work in concert to create a functional network. The primary components include:
Compressors: These devices are responsible for compressing air and storing it in a tank, generating the pressure needed for the system. Compressors can be powered by electricity, gasoline, or diesel, depending on the application.
Actuators: Actuators in pneumatic systems convert compressed air into mechanical energy, producing linear or rotary motion. Common types include pneumatic cylinders and rotary actuators, which are used to drive tools or manipulate objects.
Valves: Valves control the flow of compressed air within the system, directing it to specific components based on operational needs. They play a crucial role in regulating pressure and ensuring the proper functioning of actuators.
Fittings: Similar to hydraulic systems, fittings connect various components in a pneumatic system, ensuring airtight connections that prevent leaks. They are vital for maintaining system pressure and efficiency.
The role of fittings in pneumatic systems is critical; they facilitate quick and secure connections while minimizing the risk of air leaks. Properly selected fittings can significantly enhance the performance and reliability of the entire system.
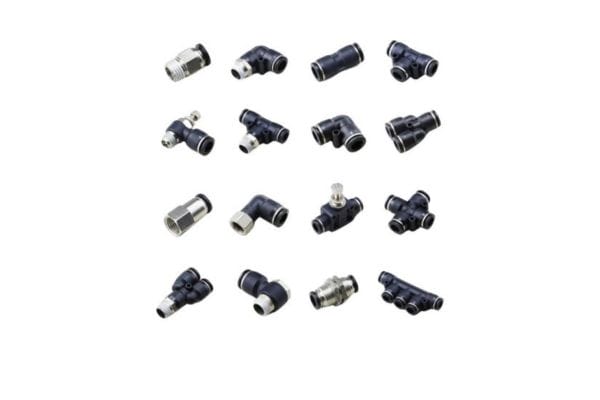
Types of Pneumatic Fittings
Pneumatic fittings come in various forms, designed to cater to specific needs and installation requirements. The most common types include:
Push-to-Connect Fittings: These fittings allow for easy and quick connections by simply pushing the tubing into the fitting. They are popular in applications where frequent disconnections are necessary, offering convenience and speed.
Threaded Fittings: Threaded fittings create a secure connection by screwing together, providing a strong and reliable seal. They are typically used in applications that require high pressure or durability.
Barbed Fittings: Barbed fittings feature protrusions that grip the tubing when inserted, creating a friction fit. They are often used in low-pressure applications where flexibility and ease of installation are priorities.
Material selection for pneumatic fittings is essential for performance and durability. Common materials include:
Aluminum: Lightweight and corrosion-resistant, aluminum fittings are suitable for a variety of applications and offer excellent strength-to-weight ratios. They are often used in environments where weight savings are essential.
Plastic: Plastic fittings are typically used in low-pressure applications due to their lightweight nature and resistance to corrosion. They are easy to install and often used in applications where environmental factors may lead to metal degradation.
Key Differences Between Hydraulic vs Pneumatic Fittings
Pressure Levels
One of the most significant differences between hydraulic and pneumatic systems lies in their operating pressure levels. Hydraulic systems typically operate at much higher pressures, often ranging from 1,500 to over 5,000 psi, depending on the application and system design. This high-pressure capability allows hydraulic systems to lift heavy loads and perform demanding tasks, making them suitable for applications such as construction and heavy machinery.
In contrast, pneumatic systems operate at significantly lower pressures, usually between 80 to 120 psi. While this lower pressure range makes pneumatic systems less powerful compared to hydraulic systems, it also allows for lighter components and quicker response times. The implications for fitting selection are substantial: hydraulic fittings must be designed to withstand high pressures, often using robust materials and specialized designs to prevent leaks or failures. Pneumatic fittings, on the other hand, can be made from lighter materials and may incorporate simpler designs due to the lower operational stress.
Medium Used
The medium used in hydraulic and pneumatic systems also differentiates the two. Hydraulic systems utilize incompressible liquids—typically oil—as the transmission fluid, while pneumatic systems use compressed air or gas. This difference in medium has profound effects on fitting design and material selection.
Hydraulic fittings must create a tight, leak-proof seal because any fluid leakage can lead to loss of pressure and fluid. Consequently, hydraulic fittings are often constructed from durable materials such as steel or stainless steel, which can withstand the chemical properties of hydraulic fluids and the high pressures involved.
Pneumatic fittings, by contrast, are designed to handle air and do not require the same level of sealing strength as hydraulic fittings. While leaks can still result in inefficiencies, the consequences are generally less severe. Pneumatic fittings are frequently made from lighter materials such as plastic or aluminum, which provide sufficient durability while minimizing weight.
Applications and Suitability
The applications and suitability of hydraulic versus pneumatic fittings highlight their distinct strengths. Hydraulic fittings are best suited for applications requiring significant force and power, such as:
Construction: Hydraulic systems in excavators and cranes utilize hydraulic fittings to manage heavy lifting and precision tasks.
Manufacturing: Hydraulic presses are essential for shaping materials, where high pressure is crucial.
Pneumatic fittings shine in applications where speed and flexibility are paramount. Common use cases include:
Automation: In assembly lines, pneumatic systems control robotic arms, requiring quick responses and lightweight fittings.
Packaging: Pneumatic systems efficiently handle filling and sealing operations, benefiting from rapid cycle times.
Industry-specific examples further illustrate these differences. For instance, in the automotive sector, hydraulic fittings are used in brake systems due to their need for precise control under high pressure, while pneumatic fittings are employed in air tools for quick, repetitive tasks.
Performance and Efficiency
When comparing the performance and efficiency of hydraulic and pneumatic systems, several factors come into play. Hydraulic systems generally provide higher power output due to their ability to handle heavier loads. This high power makes them ideal for tasks that demand consistent force over time. However, the energy consumption of hydraulic systems can be significant, especially in applications with frequent cycling, which may lead to increased operational costs.
In contrast, pneumatic systems often consume less energy during operation, making them more efficient for tasks requiring rapid movement with lower force requirements. They are particularly advantageous in applications with intermittent use, where their quick startup and response times can enhance overall system efficiency.
Maintenance requirements also differ between the two systems. Hydraulic systems often necessitate regular checks for fluid leaks and contamination, as well as maintenance of pumps and valves to ensure optimal performance. This can lead to higher maintenance costs over time. Pneumatic systems, while generally simpler, still require periodic checks to ensure proper air compression and fitting integrity, but they typically involve less complexity and fewer components.
Factors to Consider When Choosing Fittings
Application Requirements
When selecting fittings for hydraulic or pneumatic systems, application requirements are paramount. Key factors include load capacity, operational speed, and environmental conditions.
Load Capacity: Understanding the maximum load that the fitting must support is crucial. Hydraulic fittings must be capable of handling high pressure and heavy loads, making material choice and design critical. Conversely, pneumatic fittings, which handle lighter loads, can be designed with less robust materials but still require careful consideration of pressure limits.
Speed: The operational speed of the system also influences fitting selection. Pneumatic systems are often chosen for their quick response times, so fittings must facilitate rapid airflow. Hydraulic systems, while slower in response, require fittings that can efficiently handle fluid flow without creating bottlenecks.
Environmental Factors: The environment in which the system operates plays a significant role in fitting selection. Factors such as temperature, humidity, and exposure to chemicals can affect material durability. For instance, stainless steel fittings may be preferred in corrosive environments, while plastic fittings might suffice in less demanding conditions. Understanding these requirements helps ensure the reliability and longevity of the fittings used.
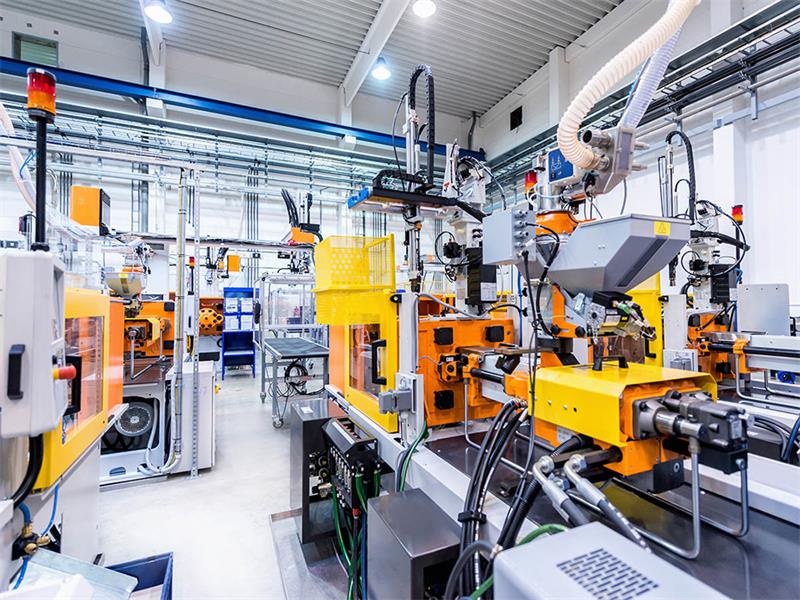
Cost Considerations
Cost is a significant factor when choosing fittings, encompassing both initial investment and long-term maintenance costs.
Initial Investment: While hydraulic fittings tend to be more expensive due to their robust design and materials, they may be necessary for high-performance applications. In contrast, pneumatic fittings are typically more affordable, making them attractive for lower-stress applications.
Long-term Maintenance Costs: It’s essential to consider the total cost of ownership, including maintenance and potential replacement costs. Hydraulic systems often require more frequent maintenance due to fluid leaks and contamination, leading to higher long-term costs. Pneumatic systems, being simpler and typically using air, may have lower maintenance costs but can still incur expenses if fittings fail or leak.
Conducting a cost-effectiveness analysis helps users make informed decisions by comparing initial costs with expected maintenance and operational costs over time. This analysis reveals that investing in higher-quality fittings may lead to lower overall costs through reduced downtime and maintenance.
Compatibility and Standards
Adhering to industry standards and ensuring compatibility among components is vital for the efficient operation of hydraulic and pneumatic systems.
Importance of Adhering to Industry Standards: Standards set by organizations such as ISO, SAE, and ANSI help ensure that fittings are manufactured to specific tolerances and performance criteria. Using fittings that meet these standards ensures compatibility and reliability within the system, reducing the risk of leaks and failures.
Cross-Compatibility of Fittings: It’s also important to consider the cross-compatibility of fittings from different manufacturers. While some fittings may appear similar, slight variations in design or specifications can lead to incompatibility issues. Therefore, selecting fittings from reputable manufacturers that adhere to the same standards can enhance compatibility and performance.
Conclusion
In summary, choosing between hydraulic and pneumatic fittings is not just a matter of preference, but requires careful analysis of specific application requirements and operating environments. We encourage you to further research and consult with Topa’s experts to deepen your understanding of these systems and their components.
FAQ
What is the main difference between hydraulic and pneumatic systems?
Hydraulic systems use incompressible fluids (usually oil) for power transmission, while pneumatic systems rely on compressed air or gas.
What applications are best suited for hydraulic fittings?
Hydraulic fittings are ideal for applications requiring high pressure and heavy loads, such as construction machinery and industrial equipment.
When should I choose pneumatic fittings instead of hydraulic fittings?
Pneumatic fittings are preferable for tasks needing quick response times and lighter loads, like automation in packaging and assembly lines.
What materials are commonly used for hydraulic and pneumatic fittings?
Hydraulic fittings are often made from steel or stainless steel, while pneumatic fittings can be made from lighter materials like aluminum or plastic.
How do I determine the right fitting for my application?
Consider factors such as load capacity, operational speed, environmental conditions, and compatibility with existing components.
Are there industry standards for fittings?
Yes, adhering to standards set by organizations like ISO and SAE ensures compatibility and reliability, reducing the risk of leaks and failures.