The conductivity of hydraulic hoses can significantly impact their performance and the safety of the environments in which they are used. Conductive hoses allow electric current to pass through, making them suitable for applications where grounding is necessary. However, in scenarios where electrical shock poses a risk—such as near high-voltage equipment or in wet environments—nonconductive hoses are preferred. These hoses are specifically engineered to prevent the flow of electricity, providing a safer alternative for operators and equipment alike.
Understanding Hydraulic Hose Basics
Types of Hydraulic Hoses
Hydraulic hoses come in various types, each designed for specific applications and performance requirements. The most common types include:
R1 and R2 Hoses: These are single and double-wire braided hoses used for medium to high-pressure applications, suitable for hydraulic systems in mobile equipment.
R7 and R8 Hoses: Made from thermoplastic materials, these hoses are lightweight and flexible, ideal for low-pressure applications, including agricultural and construction equipment.
Wire-Reinforced Hoses: Typically used in high-pressure applications, these hoses feature multiple layers of steel wire to enhance durability and resistance to bursting.
Nonconductive Hoses: Specifically designed to prevent electrical conductivity, these hoses are essential in applications near high-voltage equipment, ensuring operator safety.
Common materials used in hydraulic hoses include rubber and thermoplastics. Rubber hoses are known for their flexibility and durability, while thermoplastic hoses offer lightweight characteristics and resistance to abrasion, making them suitable for a range of environments.

Key Components of Hydraulic Hoses
A hydraulic hose consists of several critical components that contribute to its functionality:
Inner Tube: This is the layer that directly transports the hydraulic fluid. It is typically made from materials resistant to oil and other fluids, ensuring a secure flow without leakage.
Reinforcement Layers: These layers provide strength and prevent the hose from collapsing under pressure. Reinforcement can include steel wire braids or spirals, depending on the hose’s design and intended pressure rating.
Outer Cover: The outer layer protects the hose from external elements such as abrasion, chemicals, and weather conditions. This cover is usually made from durable rubber or thermoplastic materials, designed to withstand harsh environments.
Each component plays a vital role in the hose’s overall performance, ensuring it can handle pressure, resist wear, and maintain a reliable flow of hydraulic fluid.
Common Applications for Hydraulic Hoses
Hydraulic hoses are widely used across numerous industries due to their versatility and effectiveness. Key applications include:
Construction: Hydraulic hoses are integral in operating machinery such as excavators, bulldozers, and cranes, facilitating the lifting and moving of heavy loads.
Agriculture: In farming equipment, hydraulic hoses are essential for powering tractors, harvesters, and irrigation systems, helping to streamline various agricultural processes.
Manufacturing: Hydraulic systems are used in assembly lines and machinery to enhance productivity. Hoses facilitate the transfer of fluids necessary for operations like clamping and pressing.
Automotive: In automotive applications, hydraulic hoses are critical for systems such as brakes, power steering, and lifts in service stations.
Conductive Hydraulic Hoses
Definition and Characteristics
Conductive hydraulic hoses are designed to allow the flow of electric current, making them suitable for applications where grounding is essential. These hoses are typically constructed using materials that exhibit conductive properties, such as rubber blended with conductive fillers or wire reinforcement. The primary characteristic of conductive hoses is their ability to safely dissipate static electricity and prevent the buildup of electrical charges, which is crucial in environments where sparks could lead to hazards.
These hoses often feature reinforced structures that can withstand high pressures while maintaining electrical conductivity. The materials used include various types of rubber, thermoplastic elastomers, and sometimes metallic wire, providing durability and flexibility along with their conductive capabilities. Conductive hoses are generally subjected to specific industry standards to ensure their performance meets safety requirements.
Benefits and Applications
The use of conductive hydraulic hoses offers several benefits, especially in applications involving electrical equipment. They are particularly effective in environments where static electricity could accumulate, such as:
Mining: In underground mining operations, equipment is often exposed to flammable materials. Conductive hoses help prevent static discharge that could ignite dust or gas, enhancing safety.
Manufacturing: Many manufacturing processes involve volatile chemicals or materials. Using conductive hoses mitigates the risk of static buildup, ensuring a safer working environment for operators.
Oil and Gas: In the oil and gas industry, where equipment is frequently exposed to hazardous conditions, conductive hoses can safely ground equipment to prevent electrical shock and static discharge.
When selecting conductive hoses, it’s essential to consider the specific requirements of the application, including pressure ratings, fluid compatibility, and environmental conditions. Using the right type of hose can significantly enhance operational safety and efficiency.
Risks and Considerations
While conductive hydraulic hoses offer distinct advantages, they also present potential risks that must be carefully managed. One primary concern is the risk of electrical shock if hoses are damaged or improperly used. Conductive hoses can carry electric current, which may pose dangers in the event of a hose rupture or wear.
Another consideration is the compatibility of the hose materials with the hydraulic fluids being transported. Some conductive hoses may degrade when exposed to certain chemicals, compromising their structural integrity and increasing the risk of leaks or failure.
To ensure safe use of conductive hoses, several guidelines should be followed:
Regular Inspections: Conduct routine inspections to check for signs of wear, abrasion, or damage. Replace hoses that show any deterioration.
Proper Grounding: Ensure that all equipment using conductive hoses is correctly grounded to prevent static buildup. This is especially critical in explosive environments.
Follow Manufacturer Specifications: Adhere to the specifications provided by the hose manufacturer regarding maximum pressure, temperature, and fluid compatibility to prevent hose failure.
Nonconductive Hydraulic Hoses
Definition and Characteristics
Nonconductive hydraulic hoses are specifically designed to prevent the passage of electric current, making them essential in applications where electrical hazards could pose significant risks. These hoses are engineered to isolate electrical charges, thereby providing a crucial layer of safety for both operators and equipment in environments with potential electrical exposure. Commonly used materials for nonconductive hoses include nylon and polyester, which offer excellent nonconductive properties while maintaining flexibility, durability, and resistance to abrasion.
The construction of nonconductive hoses typically lacks metal reinforcements, ensuring that the hose remains electrically nonconductive even under high pressure. The outer layers may feature weather-resistant coatings, enhancing their performance in outdoor conditions while ensuring longevity. These design characteristics make nonconductive hoses ideal for various demanding applications.
Benefits and Applications
The primary advantages of nonconductive hydraulic hoses are safety and reliability. In scenarios where workers may be exposed to high-voltage equipment or power lines, these hoses minimize the risk of electrical shock. This protective feature is particularly important in industries such as:
Aerial Lifts: Nonconductive hoses are widely used in hydraulic systems for aerial lifts. Operators often work at heights near electrical lines, and using nonconductive hoses ensures safety by preventing electrical current flow in case of hose damage.
Rescue Tools: In emergencies, such as vehicle extrication, hydraulic rescue tools often utilize nonconductive hoses. These hoses are critical for ensuring operator safety, as they prevent electrical hazards while providing the necessary hydraulic power.
Agriculture: In agricultural machinery, nonconductive hoses are employed to safeguard operators working near high-voltage equipment or power lines, ensuring safe operation in fields.
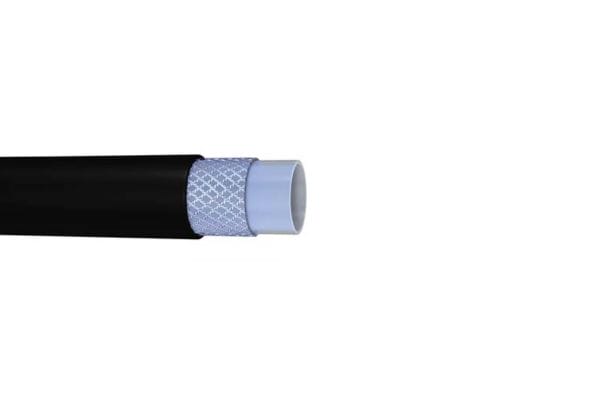
Standards and Testing
To ensure the safety and effectiveness of non-conductive hydraulic hoses, several industry standards govern their manufacturing and testing. One of the key standards is the SAE J517, which specifies requirements for various types of hydraulic hoses, including those designed to be non-conductive. This standard outlines performance criteria, such as pressure ratings and environmental resistance.
Testing processes for ensuring nonconductivity typically involve subjecting hoses to high-voltage tests to verify that they do not conduct electricity under specified conditions. These tests assess the hose’s insulation properties, ensuring compliance with safety regulations. Manufacturers often perform routine quality checks and tests to confirm that each batch of hoses meets or exceeds the required standards for nonconductivity.
Comparative Analysis
Nonconductive vs Conductive Hoses: Key Differences
In the world of hydraulic hoses, understanding the differences between conductive and nonconductive hoses is crucial for ensuring safety and performance. The following comparison highlights key features, benefits, and applications of each type:
Feature/Aspect | Conductive Hoses | Mining, manufacturing, oil and gas |
Conductivity | Allows electric current to pass through | Prevents the flow of electric current |
TypicalMaterials | Nylon, polyester, synthetic fibers | Rubber with conductive fillers, metal |
Applications | Varies, often suitable for moderate pressures | Aerial lifts, rescue tools, agriculture |
Safety Concerns | Risk of electrical shock if improperly used | Enhanced safety in high-voltage environments |
Pressure Ratings | Generally high-pressure capabilities | Varies,often suitable for moderate pressures |
Weight | Typically heavier due to metal reinforcements | Generally lighter and more flexible |
Choosing the Right Hose for Your Application
When deciding between conductive and nonconductive hoses, several critical factors must be considered to ensure optimal performance and safety:
Environment: Analyze the surrounding conditions where the hose will be used. If the application involves high voltage or proximity to electrical equipment, non conductive hoses are preferable to minimize the risk of electrical shock. Conversely, in environments where grounding is necessary, such as industrial manufacturing or mining, conductive hoses may be more appropriate.
Voltage Exposure: Determine the voltage levels the hose will be exposed to. Conductive hoses are suitable for environments where electrical grounding is required, helping to prevent static buildup. However, caution is necessary in high-voltage situations, as conductive hoses can pose a safety hazard if not managed properly. Understanding the specific voltage conditions will guide you in selecting the appropriate hose type.
Fluid Compatibility: Ensure the hose material is compatible with the hydraulic fluid being used. Different fluids can have varying effects on hose materials, influencing their longevity and performance. For instance, certain oils or chemicals can degrade rubber, while thermoplastics may withstand harsher conditions. It’s essential to consult manufacturer specifications and compatibility charts when making your selection.
By considering these factors, users can make informed decisions that align with safety standards and operational requirements.
Misconceptions and Myths
There are several common myths surrounding conductive and nonconductive hoses that can lead to misunderstandings:
Myth 1: “All rubber hoses are nonconductive.”
Clarification: This is not true; rubber can vary widely in conductivity depending on its formulation. Some rubber hoses may be conductive, especially if they contain metal reinforcements or specific additives that alter their electrical properties. Therefore, it’s crucial to verify the specifications of any rubber hose to understand its conductivity characteristics.
Myth 2: “Conductive hoses are always unsafe.”
Clarification: Conductive hoses are safe when used correctly in environments designed for them. They are essential for grounding in certain applications, such as those involving flammable materials or static-sensitive environments. However, their use must be evaluated carefully against environmental risks. When proper protocols and safety measures are followed, conductive hoses can be an integral part of a safe hydraulic system.
Myth 3: “Nonconductive hoses can be used in any application.”
Clarification: While nonconductive hoses enhance safety near electrical hazards, they may not be suitable for high-pressure applications without proper testing and certification. Users must ensure that nonconductive hoses meet the necessary pressure ratings and material standards for their specific applications. Misapplication can lead to failures, so it’s essential to consult guidelines and manufacturer recommendations before use.
Best Practices and Maintenance
Installation Tips
Proper installation of hydraulic hoses is crucial for ensuring their effectiveness and safety. Adhering to these guidelines can help prevent common issues:
Avoid Twists and Kinks: Ensure hoses are routed without twists or kinks. Kinks can restrict fluid flow and create pressure points that may lead to premature hose failure. It’s advisable to plan the hose layout carefully before installation.
Use Correct Fittings: Always select fittings that are compatible with the hose type and size. Mismatched fittings can lead to leaks or failures under pressure. Consult manufacturer specifications to confirm compatibility.
Secure Properly: Use appropriate clamps and supports to secure hoses along their routing path. Ensure hoses do not come into contact with sharp edges or hot surfaces that could cause abrasion or heat damage. Properly secured hoses are less likely to suffer from mechanical wear and tear.
Maintenance Procedures
Regular maintenance is essential for extending the lifespan of hydraulic hoses. Implementing key procedures can significantly enhance performance and reliability:
Visual Inspections: Conduct regular visual checks for signs of wear, such as abrasions, cracks, or bulges. Pay close attention to connection points and fittings, where leaks are most likely to occur. Identifying issues early can prevent costly breakdowns.
Pressure Testing: Periodically conduct pressure tests to ensure hoses can handle their rated pressures without failure. This practice helps to verify the integrity of the hose and its connections. Testing should be done following manufacturer guidelines to ensure accurate results.
Cleaning: Keep hoses free from dirt and debris, particularly at connection points. Contaminants can enter the hydraulic system and compromise fluid quality, leading to system failures. Use appropriate cleaning agents that do not harm hose materials.
To prolong hose lifespan, store hoses in a cool, dry environment away from direct sunlight. Exposure to UV light and extreme temperatures can degrade hose materials over time. Additionally, avoid storing hoses in areas with exposure to harsh chemicals that could compromise their integrity.
When to Replace Hoses
Timely replacement of hydraulic hoses is vital for maintaining safety and performance. Be vigilant for the following signs that indicate a hose needs replacement:
Visible Damage: Any signs of wear, such as cracks, cuts, or blisters, necessitate immediate replacement. Even minor damage can worsen under pressure and lead to catastrophic failures.
Leaks: Frequent leaks at fittings or along the hose itself indicate deterioration. Even small leaks should be addressed promptly, as they can escalate and cause system failures.
Age: Hoses should be replaced based on manufacturer recommendations, typically every 5-10 years, regardless of appearance. Age-related degradation can compromise hose integrity, making routine replacement critical for safety.
Conclusion
Selecting the appropriate hose is not just a matter of performance; it directly impacts the safety of operators and the integrity of equipment. Therefore, it is crucial to prioritize safety and compliance with industry standards when making your choice. Regular maintenance, timely inspections, and proper installation can further enhance hose longevity and reliability. By understanding the specific requirements of your application and adhering to best practices, you can significantly reduce risks and ensure a safer working environment.
FAQ
What are hydraulic hoses used for?
Hydraulic hoses are used to transport hydraulic fluid in various machinery and equipment across industries like construction, agriculture, and manufacturing.
What is the difference between conductive and nonconductive hoses?
Conductive hoses allow electric current to pass through, making them suitable for grounding, while nonconductive hoses prevent electrical flow, enhancing safety in high-voltage environments.
How do I know which hose to choose for my application?
Consider factors such as the environment, voltage exposure, and compatibility with hydraulic fluids when selecting the appropriate hose type.
What materials are commonly used in nonconductive hoses?
Nonconductive hoses are typically made from nylon and polyester, which provide flexibility, durability, and resistance to abrasion.
How often should I inspect my hydraulic hoses?
Regular visual inspections should be conducted at least monthly, with more frequent checks recommended in high-use or harsh environments.
When should I replace a hydraulic hose?
Replace a hose if you notice visible damage, such as cracks or leaks, or if it fails pressure tests, as timely replacement is crucial for safety.