When O-rings fail, the implications can be severe. Leaks resulting from O-ring failures can lead to operational inefficiencies, where hydraulic systems may not function at optimal performance levels, causing delays and increased energy consumption. Furthermore, the safety hazards associated with hydraulic fluid leaks can be significant; pressurized fluid can create dangerous working conditions, risking injury to personnel.
Understanding O-rings
A. Definition and Functionality
O-rings are circular sealing devices made from flexible materials, designed to fit into grooves and create a seal between two or more parts in a hydraulic system. When compressed, O-rings deform to fill the gap between mating surfaces, preventing fluid leakage and maintaining pressure. Their effectiveness relies on several factors, including material properties, groove design, and the specific application environment. O-rings can operate in a variety of conditions, effectively sealing both static and dynamic joints, making them essential for maintaining the integrity of hydraulic systems.
B. Types of O-rings
O-rings come in various materials and designs, each suited for specific applications and environmental conditions.
Nitrile (Buna-N): Known for its excellent resistance to petroleum-based fluids, nitrile is the most commonly used O-ring material in hydraulic applications. It offers good flexibility and is suitable for moderate temperatures.
Fluorocarbon (Viton): This material is highly resistant to chemicals and high temperatures, making it ideal for aggressive hydraulic fluids and environments. Fluorocarbon O-rings maintain their elasticity and sealing capabilities even under extreme conditions.
Polyurethane: Offering superior abrasion resistance, polyurethane O-rings are used in applications where wear and tear are significant concerns. They are also suitable for low-temperature applications.
Silicone: While not typically used for dynamic sealing due to lower tensile strength, silicone O-rings excel in high-temperature environments and are often found in applications where flexibility and thermal stability are crucial.
EPDM: Ethylene Propylene Diene Monomer O-rings are excellent for water and steam applications due to their exceptional weather resistance and ability to withstand heat.
Understanding these materials helps in selecting the right O-ring for specific hydraulic system needs.
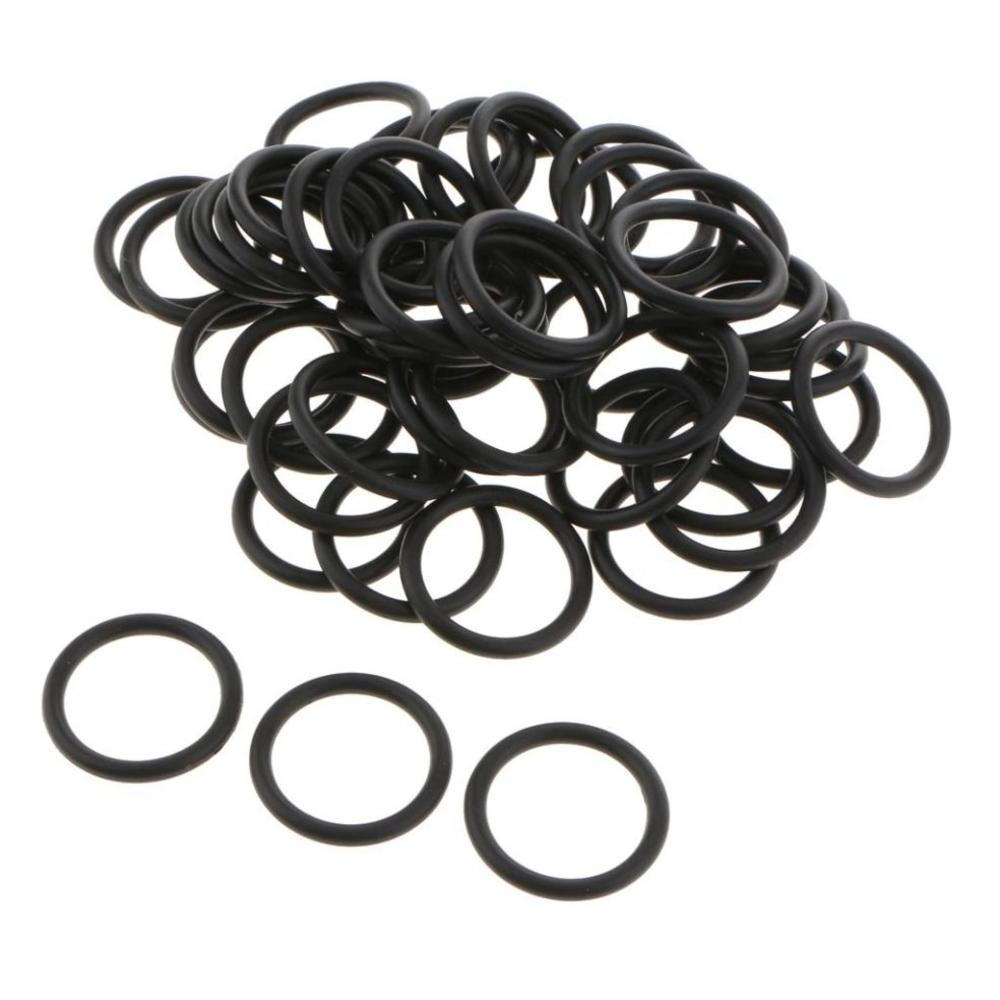
C. Common Applications in Hydraulic Systems
O-rings are utilized across a wide range of industries, reflecting their versatility and critical role in hydraulic systems. Some common applications include:
Automotive: O-rings are used in various automotive hydraulic systems, such as brakes and power steering, to ensure fluid containment and system reliability.
Manufacturing: Hydraulic presses and machinery rely on O-rings to prevent fluid leaks, which can disrupt operations and lead to costly downtime.
Construction: Equipment like excavators and backhoes utilize O-rings in hydraulic cylinders to maintain sealing integrity under high pressure.
Oil and Gas: O-rings play a vital role in subsea equipment, pipelines, and hydraulic fracturing applications, where they must withstand harsh environmental conditions and aggressive chemicals.
Identifying O-ring Failures
A. Common Signs of O-ring Failure
Identifying O-ring fails early is crucial to preventing significant system issues. Common visual indicators include:
Wear: Over time, O-rings can show signs of wear such as thinning or flat spots, indicating they are no longer providing an effective seal. This is often a result of excessive friction or improper installation.
Cracking: O-rings may develop cracks or splits due to exposure to harsh chemicals, extreme temperatures, or aging. Cracks can compromise the integrity of the seal, leading to leaks.
Deformation: If an O-ring appears squished, flattened, or misshapen, it may have been subjected to excessive compression or improper groove design. Deformed O-rings can lose their ability to seal effectively, causing fluid leakage.
Discoloration: Color changes can signal chemical degradation. For instance, O-rings made from nitrile may turn brown or harden when exposed to oil or heat, indicating potential failure.
Fluid Leakage: Visible fluid leaking from the connection points is one of the most obvious signs of O-ring failure. This indicates that the O-ring has lost its sealing capability.
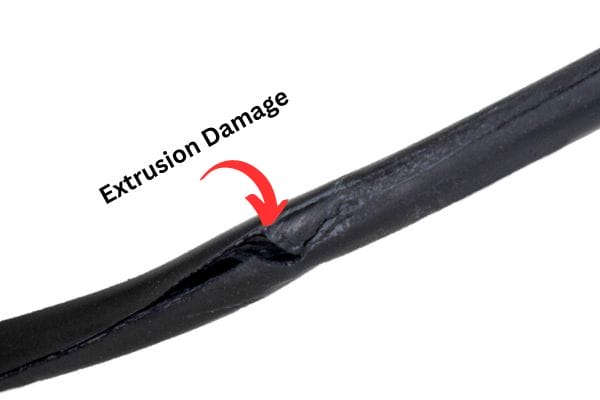
B. Performance Issues Linked to O-ring Fail
O-ring fails can lead to various performance issues in hydraulic systems, including:
Reduced Efficiency: Leaks resulting from O-ring fails to cause a loss of hydraulic fluid, leading to decreased system pressure and efficiency. This can slow down machinery and reduce overall productivity.
Increased Maintenance Costs: Frequent O-ring fails necessitate regular inspections and replacements, increasing operational costs and downtime. This not only affects budgets but also impacts project timelines.
Safety Hazards: Leaking hydraulic fluid poses safety risks, especially in environments where flammable materials are present. Moreover, reduced hydraulic pressure can lead to equipment malfunctions, endangering personnel.
System Contamination: Leaks can introduce contaminants into the hydraulic system, leading to premature wear of components and system failure. Contaminated fluid can affect the performance of pumps, valves, and actuators.
Temperature Fluctuations: Inadequate sealing can lead to changes in system temperature, which can further exacerbate the degradation of O-rings and other components.
Causes of O-ring Failure
A. Improper Installation Techniques
The installation of O-rings is critical to their performance and longevity. Common mistakes during installation that can lead to failures include:
Incorrect Sizing: Using an O-ring that is too large or too small for the groove can prevent a proper seal. An oversized O-ring may not fit snugly, while an undersized O-ring may stretch excessively, leading to leaks.
Lack of Lubrication: Failing to lubricate the O-ring before installation can cause it to twist or pinch during assembly. Lubrication helps reduce friction and makes it easier to slide the O-ring into place without damaging it.
Misalignment: If the O-ring is not aligned properly within its groove, it may become pinched or compressed unevenly. Misalignment can lead to localized stress points, increasing the likelihood of cracks or deformations.
Over-tightening: Applying excessive torque during assembly can compress the O-ring beyond its elastic limits, leading to deformation and eventual failure. It’s essential to follow manufacturer specifications for torque settings.
Using Improper Tools: Using sharp or abrasive tools during installation can nick or damage the O-ring, compromising its sealing ability. Specialized tools should be used to handle O-rings safely.
Ignoring Groove Design: Each O-ring groove is designed with specific dimensions and shapes to accommodate the O-ring. Ignoring these specifications can lead to ineffective sealing and premature failure.
B. Environmental Factors
Environmental conditions play a significant role in O-ring performance and longevity. Key factors include:
Temperature Extremes: O-rings are sensitive to temperature fluctuations. High temperatures can cause elastomers to harden, while low temperatures can make them brittle. Operating outside the recommended temperature range can lead to loss of elasticity and increased wear.
Pressure Variations: Hydraulic systems often operate under high pressure. If the pressure exceeds the O-ring’s specifications, it can lead to extrusions or blowouts, compromising the seal.
Chemical Exposure: Certain chemicals can degrade O-ring materials. For example, exposure to hydrocarbons can cause nitrile O-rings to swell, while aggressive solvents can lead to cracking or dissolution. It’s crucial to select O-ring materials that are compatible with the operating environment.
Moisture and Humidity: High humidity can contribute to the degradation of certain O-ring materials, especially if they are not designed to handle moisture. Additionally, moisture can facilitate corrosion in metal components, affecting overall system integrity.
Ozone Exposure: Ozone can cause oxidation and degradation of rubber materials, leading to cracks and failures. O-ring materials should be chosen to resist ozone effects, particularly in outdoor applications.
C. Material Compatibility Issues
Material selection is critical in preventing O-ring fails. Issues can arise from:
Incorrect Material Choice: Selecting an O-ring material that does not match the application requirements can lead to rapid degradation. For instance, using a standard rubber O-ring in an application with high temperatures or chemical exposure will likely fail.
Incompatibility with Fluids: Different fluids have varying impacts on O-ring materials. Nitrile O-rings, for example, are excellent for petroleum-based fluids but may degrade in the presence of water or certain acids.
Inclusion Content: The presence of foreign materials or impurities in the O-ring can weaken its structure. For example, inclusions in the rubber can create stress points that lead to cracking or failure.
Processing Variability: The manufacturing process of O-rings can affect their performance. Variations in curing times, temperatures, and material blends can lead to inconsistencies in hardness and resilience.
Aging: Over time, all materials undergo aging, which can affect performance. For instance, prolonged exposure to oxygen and heat can result in hardening and loss of elasticity, leading to seal failure.
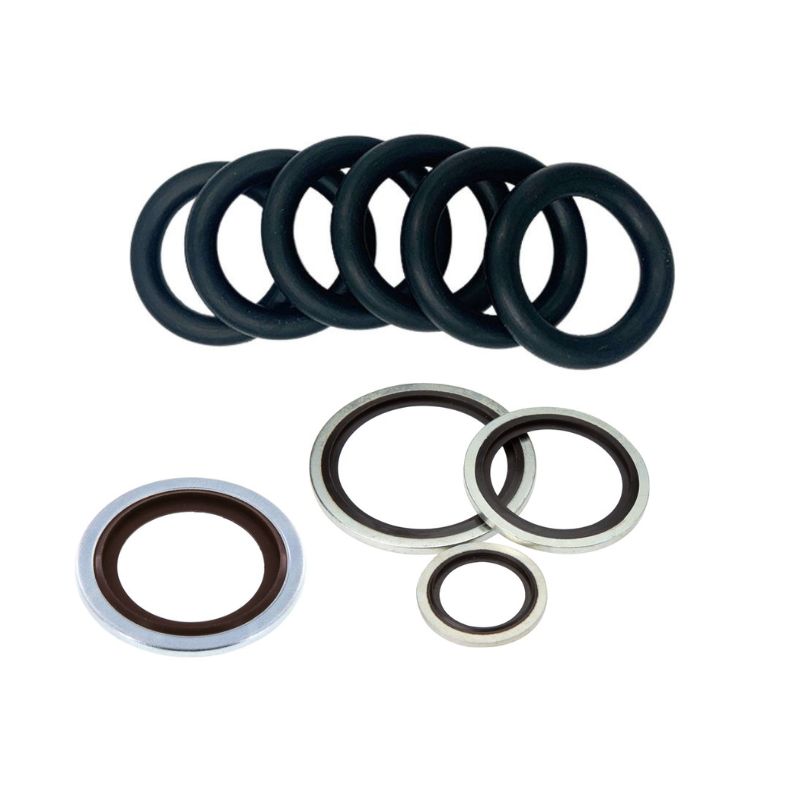
D. Aging and Wear Over Time
O-rings experience natural wear and aging, which can compromise their sealing capabilities. Key points to consider include:
Cyclic Fatigue: O-rings in dynamic applications are subject to cyclic stresses that can lead to fatigue over time. Repeated compression and decompression can cause cracks and wear.
Environmental Aging: Exposure to UV light, oxygen, and other environmental factors accelerates the aging process. O-rings can harden, crack, or become discolored, indicating that they are reaching the end of their useful life.
Wear from Movement: In dynamic seals, movement against a surface can wear down the O-ring material. This wear can create gaps in the seal, leading to leaks.
Maintenance Neglect: Regular inspections and timely replacements are crucial. Neglecting maintenance can lead to unnoticed wear and eventual failure, resulting in costly downtimes.
Storage Conditions: Improper storage of O-rings can lead to premature aging. Exposure to heat, light, and moisture during storage can compromise their integrity before they are even installed.
Troubleshooting O-ring Issues
A. Systematic Approach to Diagnosing O-ring Problems
A structured approach to diagnosing O-ring problems can help identify the root causes effectively. Here’s a step-by-step guide:
Visual Inspection: Begin with a thorough visual examination of the O-ring and surrounding components. Look for obvious signs of wear, damage, or contamination. Check for cracks, deformation, or discoloration.
Check Installation: Confirm that the O-ring was installed correctly. Ensure it is seated properly in its groove without any twists or pinches. Verify that the correct size and material were used for the application.
Evaluate Operating Conditions: Review the operating conditions, including temperature, pressure, and fluid compatibility. Compare these conditions against the O-ring specifications to identify any discrepancies that could lead to failure.
Identify Performance Issues: Look for symptoms of O-ring failure, such as leaks or performance drops in the hydraulic system. Document any changes in pressure, fluid levels, or operational efficiency that may indicate a problem.
Conduct Pressure Testing: If leaks are suspected, perform pressure testing to confirm the presence of leaks. Use a pressure gauge to monitor changes in system pressure, which can indicate where a failure may be occurring.
Consult Historical Data: Review any maintenance records or historical data on the specific hydraulic system. Previous failures or replacements can provide insights into recurring issues or patterns that may help diagnose the current problem.
Engage with Manufacturers or Experts: If the issue remains unresolved, consult with the O-ring manufacturer or hydraulic system experts. They can provide specialized knowledge and insights based on similar cases.
B. Tools and Techniques for Detection
Utilizing the right tools and techniques can streamline the leak detection process and assess O-ring conditions effectively:
Leak Detection Fluids: These specialized fluids can be applied to suspected leak areas. Bubbles will form at the site of a leak, allowing for easy identification of O-ring failure points.
Ultrasonic Detectors: These devices can detect the high-frequency sound waves produced by escaping fluids. Ultrasonic detectors are especially useful in noisy environments where traditional detection methods may be hindered.
Pressure Gauges: Monitoring system pressure with gauges helps identify inconsistencies that may indicate O-ring issues. Sudden pressure drops can signal a leak or failure in the sealing system.
Borescopes and Endoscopes: These inspection tools allow for visual examination of hard-to-reach areas within the hydraulic system. They can help identify O-ring conditions in tight spaces without disassembly.
Thermal Imaging Cameras: These cameras can detect temperature variations caused by fluid leaks, as escaping fluids often exhibit different thermal profiles compared to the surrounding components.
Torque Wrenches: Using a torque wrench ensures that the O-ring connections are tightened to the specified levels. Over or under-torquing can compromise the seal, so proper tool usage is essential.
Micrometers and Calipers: Measuring tools can verify O-ring dimensions, ensuring they meet specifications and are not experiencing undue wear.
C. When to Replace O-rings
Determining when to replace O-rings rather than attempt repairs is crucial for maintaining system integrity. Consider the following guidelines:
Visible Damage: If the O-ring exhibits cracks, severe deformation, or significant wear, replacement is necessary. Damaged O-rings cannot provide an effective seal and pose a risk of leaks.
Signs of Aging: O-rings that have become hard, brittle, or discolored due to aging should be replaced. These changes indicate that the material properties have deteriorated, compromising the seal.
Repeated Failures: If an O-ring fails multiple times in a short period, it may be indicative of an underlying issue rather than a simple fault. In such cases, replacing the O-ring with a new one and addressing the root cause is essential.
Unacceptable Leak Rates: If the O-ring is leaking at a rate that exceeds acceptable levels, it is time for replacement. Conduct leak tests to quantify leakage and determine if the O-ring can be salvaged.
Environmental Changes: If the application environment has changed (e.g., higher temperatures or exposure to new chemicals), it may be necessary to replace O-rings with materials better suited for the new conditions.
Installation Mistakes: If improper installation has occurred, such as pinching or misalignment, the O-ring should be replaced. Attempting to reuse an improperly installed O-ring can lead to repeated failures.
Conclusion
Proactive measures, such as regular inspections, adherence to installation guidelines, and environmental considerations, can significantly mitigate the risk of leaks. Understanding the conditions that lead to O-ring degradation allows for informed decisions regarding material selection and operational practices. By prioritizing O-ring maintenance, operators can enhance safety, reduce downtime, and minimize operational costs associated with leaks.
FAQ
What is an O-ring, and what role does it play in hydraulic systems?
An O-ring is a circular sealing element made from elastomeric materials. It is used to create a seal between two parts, preventing leaks and maintaining system pressure in hydraulic applications.
What are common signs of O-ring failure?
Common signs include visible wear, cracking, deformation, and leaks around the sealing area. Reduced system performance and increased noise may also indicate O-ring issues.
What causes O-ring failures?
O-ring fails can result from improper installation, environmental factors (such as temperature and pressure), material compatibility issues, and natural aging or wear over time.
How can I troubleshoot O-ring problems in my hydraulic system?
Start with a systematic approach: inspect the O-ring visually for damage, check for proper installation, assess environmental conditions, and use tools like leak detection fluids or pressure gauges to identify issues.
When should I replace an O-ring instead of repairing it?
Replace an O-ring if it shows significant wear, cracking, or deformation that compromises the seal. If the O-ring has failed multiple times or is incompatible with the fluid, replacement is advisable.
What best practices can help prevent O-ring fails?
To prevent failures, ensure proper installation techniques, select compatible materials, conduct regular inspections, and maintain appropriate environmental conditions around the O-rings.