Over-bending occurs when a hose is curved beyond its recommended bend radius, leading to various issues such as kinking, abrasion, and ultimately, failure of the hose. This can result in costly downtimes, safety hazards, and equipment damage.
Understanding Interlocked Hoses
A. Definition and Construction of Interlocked Hoses
Interlocked hoses are specialized flexible hoses designed to provide enhanced durability and flexibility for transporting various fluids and gases. Unlike traditional hoses, which are typically made from rubber or synthetic materials, interlocked hoses consist of interwoven metal strips that create a series of overlapping segments. This unique construction allows the hose to maintain its shape while providing a high degree of flexibility and resistance to external pressures.
The design of interlocked hoses enables them to expand and contract with movement, making them particularly suitable for applications where there is significant vibration or thermal cycling. The interlocked structure helps prevent kinking and crushing, ensuring that the flow of material is uninterrupted. Additionally, these hoses often feature a smooth inner surface, which reduces turbulence and minimizes the risk of abrasion, further enhancing their performance.
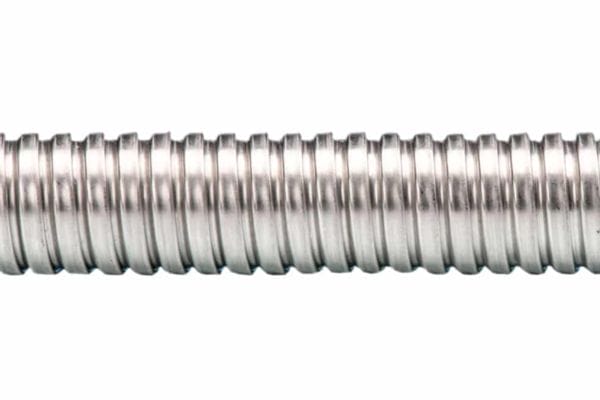
B. Common Materials Used in Interlocked Hoses
Interlocked hoses are typically constructed from various materials, each chosen for its specific properties and suitability for different applications. The most common materials include:
Stainless Steel: Stainless steel is the most prevalent material used in interlocked hoses due to its excellent corrosion resistance and mechanical strength. Grades such as 304 and 316 are frequently used, with 316 offering superior resistance to chloride environments.
Aluminum: Lightweight and resistant to corrosion, aluminum interlocked hoses are often used in applications where weight savings are critical. However, they may not provide the same level of strength as stainless steel.
Specialty Alloys: For high-performance applications, hoses made from specialty alloys (such as Inconel or Monel) are available. These materials are designed to withstand extreme temperatures and corrosive environments, making them ideal for industries like aerospace and chemical processing.
The choice of material depends on several factors, including the type of fluid being transported, temperature, pressure, and environmental conditions. Proper material selection is crucial to ensuring the longevity and reliability of the hose in its specific application.
C. Typical Applications and Environments for Interlocked Hoses
Interlocked hoses are versatile and can be found in a wide range of applications across various industries. Some typical uses include:
Oil and Gas: Interlocked hoses are commonly used in the oil and gas sector for transporting crude oil, natural gas, and other hydrocarbons. Their ability to withstand high pressures and harsh environmental conditions makes them suitable for this demanding industry.
Manufacturing: In manufacturing environments, interlocked hoses are used for vacuum applications, as well as for transferring bulk materials like granules and powders. Their flexibility allows for easy routing around machinery and other obstacles.
Construction: In construction, these hoses are used for transferring concrete, slurry, and other materials. Their durability and flexibility make them ideal for navigating complex job sites.
Food and Beverage: Some interlocked hoses are designed to meet food safety standards, allowing for the safe transport of food and beverage products. Their smooth inner surfaces reduce the risk of contamination and facilitate cleaning.
The Mechanics of Bending
A. Explanation of Hose Bending Principles
Understanding the mechanics of bending is crucial for the effective use of interlocked hoses. When a hose is bent, the curvature affects how the materials within the hose respond to stress and strain. Each hose has a specified bend radius, which is the minimum radius the hose can be bent without compromising its structural integrity. This radius is influenced by the hose’s diameter, construction materials, and internal components.
When bending occurs, several forces act on the hose:
Tensile Stress: On the outer side of the bend, the material is stretched, which can lead to elongation. If the tensile stress exceeds the material’s yield strength, permanent deformation can occur.
Compressive Stress: On the inner side of the bend, the material is compressed. This compression can lead to buckling or kinking if the bending is excessive.
Shear Stress: The forces acting across the cross-section of the hose create shear stress, which can weaken the material over time, particularly at points of connection or within the interlocked structure.
To maintain optimal performance, it is essential to adhere to the manufacturer’s specifications regarding the bend radius and to ensure that hoses are routed properly during installation. Understanding these principles helps users avoid situations where the hose may be subject to stresses beyond its designed limits.
B. What Constitutes Over-Bending in Interlocked Hoses
Overbending occurs when a hose is subjected to a bend radius that is smaller than the manufacturer’s recommended minimum. For interlocked hoses, this situation can arise in various scenarios, such as improper installation, inadequate support, or unintentional manipulation during operation.
Key indicators of over-bending include:
Tight Curves: If the hose is forced into a sharp turn that exceeds the recommended bend radius, it is at risk of over-bending.
Kinks or Twists: Visible kinks or twists in the hose indicate that it has been bent beyond its limits. This can significantly compromise the flow characteristics and lead to damage.
Pressure Drops: A noticeable drop in the pressure of the material flowing through the hose may indicate that the hose has been compromised due to over-bending.
It is vital to regularly inspect hoses for signs of over-bending and ensure that installation practices prioritize adequate routing and support to avoid such issues.
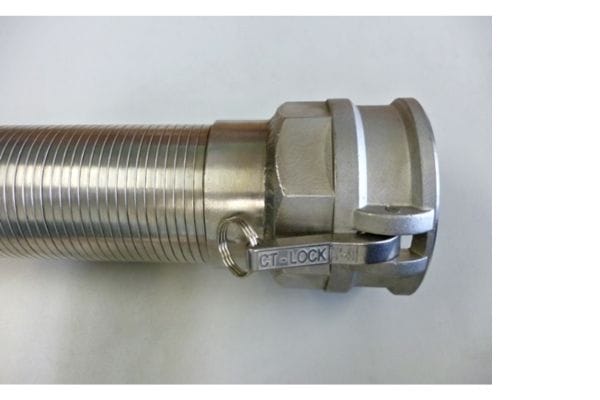
C. Consequences of Over-Bending on Hose Performance
Over-bending interlocked hoses can have serious repercussions, affecting both performance and safety. The consequences include:
Kinking and Crimping: One of the most immediate effects of over-bending is kinking, which can completely block the flow of material. In severe cases, crimping can occur, permanently damaging the hose and necessitating replacement.
Increased Wear and Tear: Bending beyond the recommended radius can cause increased abrasion on the inner surfaces of the hose, leading to premature wear. Over time, this can create leaks and reduce the overall lifespan of the hose.
Loss of Flexibility: Over-bent hoses may become rigid and lose their inherent flexibility. This can result in difficulties when routing the hose and can lead to further bending or damage during operation.
Pressure Complications: Excessive bending can cause localized pressure increases within the hose, leading to potential ruptures or bursts. This not only compromises the integrity of the hose but can also pose significant safety hazards to personnel and equipment.
Fluid Contamination: If a hose develops cracks or leaks due to over-bending, there is a risk of fluid contamination. This is particularly critical in applications involving food, pharmaceuticals, or sensitive chemicals, where contamination can have severe consequences.
Operational Downtime: The need to replace damaged hoses or address leaks can lead to significant operational downtime, resulting in lost productivity and increased costs.
Identifying Over-Bending
A. Signs of Over-Bending in Interlocked Hoses
Recognizing the signs of over-bending in interlocked hoses is critical for preventing failures and ensuring safe operation. Key indicators include:
Visible Kinks and Twists: One of the most obvious signs of over-bending is the presence of kinks or twists along the length of the hose. These deformations not only obstruct the flow of fluids but can also lead to permanent damage if not addressed promptly.
Abnormal Wear Patterns: Inspecting the hose for uneven wear or abrasion is essential. Over-bending often leads to localized wear on the inner surfaces, which may appear as shiny or polished areas. This is a clear indication that the hose is experiencing undue stress.
Pressure Fluctuations: Monitoring the pressure within the hose is crucial. If there are sudden drops in pressure or irregular pressure readings, it may suggest that the hose is not allowing for proper flow due to over-bending.
Cracks or Fractures: Regularly examining the hose for cracks, especially at bends, is important. Over-bending can lead to micro-fractures that grow over time, compromising the hose’s integrity.
Increased Resistance: If the hose feels stiff or requires more force to manipulate than usual, it may be an indication that the hose has been over-bent and is no longer maintaining its flexibility.
Fluid Leaks: Any signs of fluid leakage are serious and often point to damage caused by over-bending. Leaks can occur at kinks or bends where the hose material has weakened.
B. Common Failure Modes Resulting from Over-Bending
Understanding the failure modes associated with over-bending is vital for effective management and prevention. Common failure modes include:
Kinking and Pinching: When the hose is bent too sharply, it can kink, completely blocking the flow path. This can result in immediate system failure, as materials cannot pass through the hose.
Abrasion and Wear: Excessive bending can lead to increased friction against the inner walls of the hose, causing significant wear over time. This wear can create thin spots that may eventually rupture under pressure.
Brittle Fracture: Particularly in colder environments or with certain materials, over-bending can lead to brittle failure, where the material fractures suddenly without warning. This is especially concerning in stainless steel hoses.
Reduced Pressure Ratings: Over-bending often leads to reduced pressure ratings due to compromised structural integrity. This can pose significant safety risks in high-pressure applications.
Fluid Contamination: If a hose develops leaks due to over-bending, there is a high risk of contaminating the fluids being transported, which can have serious implications for health, safety, and product quality.
Preventing Over-Bending
A. Best Practices for Installation and Handling
To prevent over-bending of interlocked hoses, it is essential to adopt best practices during both installation and ongoing handling. These practices include:
Follow Manufacturer Guidelines: Always adhere to the specifications provided by the manufacturer, including the recommended bend radius and installation instructions. This ensures the hose operates within its designed limits.
Use Appropriate Tools: Utilize proper tools for installation and maintenance to avoid excessive force. For example, using a hose clamp or support bracket can help maintain the correct position and prevent bending beyond the recommended radius.
Train Personnel: Ensure that all personnel involved in the handling and installation of hoses are adequately trained. They should understand the importance of avoiding over-bending and recognize the signs of potential issues.
Conduct Regular Inspections: Regularly inspect hoses for signs of wear, kinking, or other deformation. Early detection of these issues can prevent more significant problems down the line.
Implement a Maintenance Schedule: Establish a routine maintenance schedule to assess hose condition and ensure that installation practices remain effective over time. This includes checking for any environmental changes that might affect the hose’s positioning.
B. Importance of Proper Routing and Support
Proper routing and support are critical components in preventing over-bending of interlocked hoses. Key considerations include:
Avoid Sharp Turns: When routing hoses, ensure that they do not have sharp turns or bends. Instead, create gentle curves that respect the manufacturer’s specified bend radius. This helps maintain the hose’s structural integrity and flexibility.
Use Support Brackets: Employ support brackets or hangers to secure the hose along its length. This prevents sagging and keeps the hose in a stable position, reducing the risk of kinking or over-bending.
Minimize Tension: Ensure that hoses are not subjected to excessive tension during operation. Tension can pull the hose into tighter bends, leading to over-bending. Utilize slack in the hose where possible to accommodate movement.
Consider Environmental Factors: Be aware of environmental factors, such as temperature fluctuations and mechanical vibrations, which may impact hose positioning. Use protective measures, such as insulating sleeves or vibration dampers, to reduce the impact of these factors.
Plan for Movement: If the hose will be part of a system that experiences movement or flexing, design the installation to allow for this movement without putting stress on the hose. Flexible connections, such as swivel joints, can help accommodate motion while reducing the risk of over-bending.
C. Guidelines for Measuring and Determining Bend Radius
Accurate measurement and determination of bend radius are vital in preventing over-bending of interlocked hoses. Here are some guidelines to follow:
Understand Bend Radius Specifications: Familiarize yourself with the hose’s bend radius specifications as provided by the manufacturer. This is the minimum radius the hose can be bent without incurring damage.
Use a Bend Radius Template: When planning installations, consider using a bend radius template or guide to visualize the appropriate bend radius. This can help prevent unintentional sharp bends during installation.
Measure Before Installation: Before installation, measure the intended route of the hose to ensure it adheres to the recommended bend radius. Use a flexible measuring tape to determine the distances and angles accurately.
Account for Fittings: When measuring for bends, remember that fittings (like elbows or connectors) can affect the overall bend radius. Be sure to consider these components in your measurements to avoid tight turns.
Conclusion
Proper installation practices, effective routing, and adequate support play a critical role in preventing over-bending and ensuring the hose operates within its designed limits. Moreover, regular maintenance and inspections are vital for early detection of potential issues. By prioritizing these practices, you can enhance the reliability and safety of their hose systems, ultimately leading to more efficient operations across various industries.
FAQ
What is over-bending in interlocked hoses?
Over-bending occurs when a hose is bent beyond its specified minimum bend radius, leading to kinks, twists, or permanent deformation.
How can I identify signs of over-bending?
Signs include visible kinks, abrasion marks on the hose surface, reduced flexibility, and pressure drops in the system.
What are the consequences of over-bending?
Consequences can include reduced flow, increased wear, potential leaks, and even hose rupture, which can pose safety risks.
How can I prevent over-bending?
Prevent over-bending by following manufacturer guidelines, using proper routing and support, and regularly inspecting hoses for signs of stress.
What should I consider when measuring for bend radius?
Always consult manufacturer specifications, account for fittings and connections, and use templates or guides to ensure proper bend radius during installation.
When should I consult a professional about my hoses?
Consult a professional if you encounter persistent issues, require installation assistance, or need tailored advice for specific applications or environments.