One of the most common issues faced by hydraulic systems is the occurrence of hose leaks. Hydraulic hoses are vital components that carry pressurized fluid, and leaks can arise from various factors such as wear and tear, improper installation, or exposure to harsh environmental conditions. These leaks not only compromise the efficiency of the hydraulic system but can also pose serious safety risks to personnel and equipment. Identifying and addressing these leaks promptly is essential to maintain system integrity and performance.
Understanding Hydraulic Hose Leaks
A. Definition of Hydraulic Hose Leaks
Hydraulic hose leaks occur when hydraulic fluid escapes from the hose, which is designed to transport pressurized fluid throughout a hydraulic system. These leaks can manifest as visible fluid seepage or may occur at a microscopic level, making them difficult to detect. In either case, the consequences can be significant, affecting system performance and posing potential safety risks. Understanding the nature of these leaks is crucial for implementing effective preventive measures.
B. Causes of Hydraulic Hose Leaks
Wear and Tear Over time, hydraulic hoses are subjected to constant pressure and movement, leading to wear and tear. Factors such as age, fatigue, and exposure to abrasive materials can weaken the hose material, resulting in cracks, splits, or other forms of degradation. Regular inspection and timely replacement of hoses are essential to mitigate this risk.
Incorrect Installation
Improper installation is a leading cause of hydraulic hose leaks. This can include issues such as incorrect torque on fittings, misalignment during installation, or using incompatible hose and fitting materials. When hoses are not installed according to manufacturer specifications, they can experience undue stress, leading to leaks. Ensuring that technicians are trained and knowledgeable about proper installation techniques is vital.
Environmental Factors
Hydraulic hoses are often exposed to various environmental conditions that can contribute to leaks. Temperature extremes, moisture, UV radiation, and chemical exposure can all degrade hose materials over time. For instance, excessive heat can cause hoses to become brittle, while moisture can lead to corrosion of metal fittings. Protecting hoses from harsh conditions through proper routing, shielding, and selection of appropriate materials is critical for longevity.
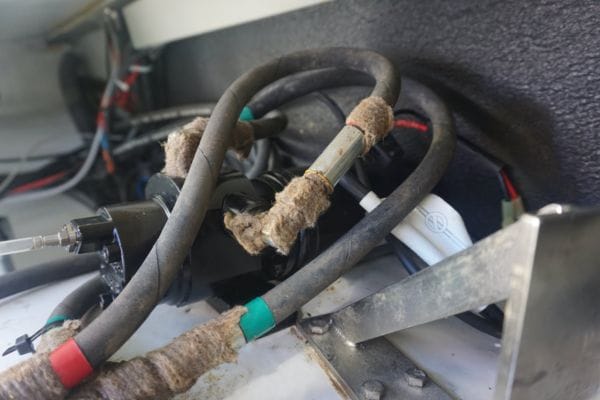
C. Impact of Leaks on Operations and Safety
The impact of hydraulic hose leaks extends beyond the immediate loss of hydraulic fluid. Operations can be significantly affected in several ways:
Reduced Efficiency: A leaking hose leads to a drop in hydraulic pressure, which can impair the performance of machinery and equipment. This reduction in efficiency can result in slower operations and increased energy consumption.
Increased Costs: Leaks can lead to increased maintenance costs due to the need for frequent repairs and replacements. Additionally, the lost fluid must be replenished, further driving up operational expenses.
Safety Hazards: Hydraulic fluid can be hazardous, posing risks such as slips and falls, fires, and environmental contamination. Leaks can also compromise the integrity of machinery, leading to malfunctions that could endanger operators and nearby personnel.
Downtime: Unplanned downtime caused by hose leaks can disrupt production schedules, leading to missed deadlines and lost revenue. Addressing leaks promptly and efficiently is essential to maintain operational continuity.
Identifying Potential Leak Points
A. Key Areas to Inspect Regularly
Connectors and Fittings
Connectors and fittings are critical junctions in hydraulic systems where hoses connect to pumps, valves, and other components. Regular inspection of these areas is vital, as they are common sites for leaks. Look for signs of fluid accumulation around fittings, which can indicate a compromised seal or connection. Check for any visible damage, such as cracks or wear, and ensure that all connections are tight and secure according to manufacturer specifications. Using the appropriate torque settings during installation can prevent future issues.
Hose Material and Condition
The hose itself is subject to wear and degradation over time. Inspect the hose material for any signs of aging, such as cracking, swelling, or bulging. Pay attention to any abrasions caused by friction or contact with sharp objects. Additionally, check for kinks or bends that could restrict flow and create stress points. If the hose appears discolored or has lost flexibility, it may be time for replacement. Regularly scheduled inspections can help catch these issues early, preventing leaks before they develop.
Mounting and Routing
Proper mounting and routing of hydraulic hoses are essential for preventing leaks. Hoses should be secured in a manner that minimizes movement and friction against other components. Check that hoses are routed away from sharp edges, moving parts, and heat sources. Ensure that they are not twisted or compressed, as this can lead to premature failure. Using protective sleeves or shields can help safeguard hoses from external damage. Regularly review hose routing during maintenance checks to ensure compliance with best practices.
B. Tools for Leak Detection
Visual Inspection
One of the simplest yet most effective methods for identifying leaks is through visual inspection. Regularly examine all hydraulic components, looking for signs of fluid leakage. This includes checking for wet spots, pooled fluid, or residue around connectors and fittings. Visual inspections should be part of routine maintenance and should be conducted by trained personnel who can recognize potential problem areas. Documenting findings can help track the condition of hoses and fittings over time.
Pressure Tests
Pressure testing is a more advanced method for detecting leaks. By subjecting the hydraulic system to a controlled pressure, technicians can identify weaknesses in hoses and connections. This method often involves using a pressure gauge to monitor any pressure drops, which can indicate a leak. Pressure tests should be conducted by safety protocols to prevent accidents. It’s important to use the appropriate test pressure as specified by the manufacturer to avoid damaging the system during the test.
Ultrasonic Leak Detectors
Ultrasonic leak detectors are specialized tools that can detect high-frequency sounds produced by escaping hydraulic fluid. These devices are particularly useful for identifying leaks that may not be visible to the naked eye. By scanning the hydraulic system with an ultrasonic detector, technicians can pinpoint the exact location of a leak, even in noisy environments. This technology is effective in detecting small leaks before they become significant problems, allowing for timely maintenance and repairs.
Best Practices for Hydraulic Hose Maintenance
A. Regular Inspection Schedules
Establishing a regular inspection schedule is crucial for maintaining hydraulic hose integrity. Inspections should be conducted at intervals based on operational demands, the environment, and manufacturer recommendations. A typical approach involves performing inspections daily, weekly, and monthly:
Daily Inspections: Before the start of operations, conduct a quick visual check for signs of leaks, wear, or damage. Look for fluid accumulation around hoses and fittings, ensuring connections are secure.
Weekly Inspections: Take a more thorough look at all hydraulic components, focusing on connectors, hose conditions, and mounting. Check for abrasions or exposure to harsh conditions and document any findings for future reference.
Monthly Inspections: Conduct detailed inspections, including pressure tests and checking the overall routing of hoses. This is an opportunity to assess the system’s performance and identify areas that may require attention or upgrades.
Implementing these schedules not only enhances reliability but also helps in early detection of issues, preventing costly downtimes and ensuring safety.
B. Proper Cleaning Techniques
Keeping hydraulic hoses clean is essential for preventing contamination and extending their lifespan. Dirt, debris, and fluid residues can compromise hose integrity and lead to failures. Here are some best practices for cleaning:
Use Appropriate Cleaning Solutions: Select cleaning agents that are compatible with hydraulic fluids and hose materials. Avoid harsh chemicals that can degrade the hose.
Gentle Cleaning Methods: Use soft cloths or brushes to clean hoses and fittings. Avoid abrasive materials that can scratch or damage the surface. For stubborn residues, consider using a non-abrasive scrub pad.
Prevent Contamination: Ensure that when cleaning hoses, no debris enters the system. Cover open fittings and hose ends with clean caps or plugs during maintenance to prevent contamination from dust and dirt.
Regular cleaning not only maintains the appearance of hydraulic hoses but also helps ensure that the system operates smoothly without unnecessary wear.
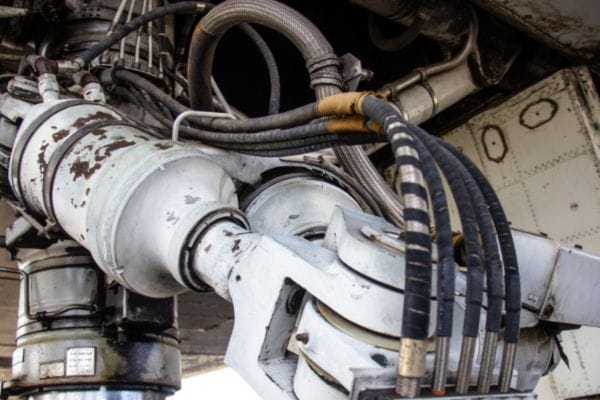
C. Correct Storage Methods
Proper storage of hydraulic hoses is essential for preventing damage when they are not in use. Following these guidelines will help maintain their integrity:
Store in a Controlled Environment: Hoses should be stored in a clean, dry area away from extreme temperatures, humidity, and UV exposure. Excessive heat can cause hoses to become brittle, while moisture can promote corrosion.
Avoid Overlapping or Kinking: When coiling hoses, ensure that they are not kinked or overlapped in a manner that creates stress points. Store hoses in a manner that allows them to lay flat or be coiled without tension.
Label and Organize: If multiple hoses are stored together, label them for easy identification and organization. This practice reduces the risk of selecting the wrong hose during installation and ensures efficient retrieval.
By following these storage methods, organizations can significantly extend the life of their hydraulic hoses, reducing the need for replacements.
D. Replacement vs. Repair: When to Act
Knowing when to repair or replace a hydraulic hose is essential for effective maintenance. Here are guidelines to help make this decision:
Assessing Damage: Minor abrasions or surface damage may be repairable if the hose is otherwise in good condition. However, if there are signs of significant wear, cracking, or structural compromise, replacement is often the safer option.
Severity of Leaks: If a leak is detected, assess its size and location. Small, easily accessible leaks may be repairable, but larger leaks, especially those at critical junctions, typically necessitate a full hose replacement.
Age of the Hose: Hydraulic hoses have a finite lifespan, often dictated by usage, pressure cycles, and environmental conditions. Even if a hose appears to be in good condition, it may be prudent to replace it if it approaches the end of its recommended lifespan.
Manufacturer Recommendations: Always refer to manufacturer guidelines regarding hose replacement intervals and repair protocols. Adhering to these recommendations can prevent failures and ensure system reliability.
Installation Techniques to Prevent Leaks
A. Selecting the Right Hose and Fittings
The foundation of a reliable hydraulic system starts with selecting the appropriate hose and fittings. Different applications require specific hose types based on factors such as pressure rating, fluid compatibility, temperature range, and environmental conditions. Here are key considerations:
Hose Type: Select hoses designed for the specific type of hydraulic fluid being used. Common materials include rubber, thermoplastic, and metal-reinforced options. Ensure the hose can withstand the pressures and temperatures it will encounter in operation.
Fitting Compatibility: Choose fittings that match the hose size and type, ensuring compatibility with the hydraulic system. Incompatible fittings can lead to leaks due to improper sealing or stress on the hose.
Pressure Ratings: Always select hoses and fittings that exceed the maximum pressure requirements of the system. This ensures they can handle unexpected pressure spikes without failure.
By carefully considering these factors during the selection process, organizations can significantly reduce the likelihood of leaks stemming from improper components.
B. Proper Installation Procedures
Proper installation techniques are crucial to ensuring that hydraulic hoses and fittings perform effectively. Key aspects include:
Torque Specifications
Proper torque is essential for ensuring a tight seal between hoses and fittings. Each fitting comes with manufacturer-specified torque values, which should be strictly adhered to during installation. Over-tightening can damage the hose or fitting while under-tightening can lead to leaks. Using a torque wrench to achieve the correct specifications ensures optimal sealing and helps prevent future failures.
Alignment and Support
Correct alignment of hoses and fittings during installation is critical. Misalignment can create undue stress on the hose, leading to premature wear or failure. Ensure that hoses are routed smoothly without sharp bends or kinks, which can restrict fluid flow and increase pressure on the fittings. Additionally, providing adequate support for hoses through brackets or clamps can help maintain alignment and reduce movement, further preventing leaks.
C. Importance of Using Quality Materials
The quality of materials used in hydraulic systems plays a vital role in preventing leaks and ensuring overall system integrity. Here’s why:
Durability: High-quality hoses and fittings are designed to withstand harsh operating conditions, including temperature extremes, high pressures, and exposure to chemicals. Investing in durable materials reduces the likelihood of wear and subsequent leaks.
Reliability: Quality components undergo rigorous testing to ensure they meet industry standards. Using reputable brands or certified products can help guarantee reliability, giving operators confidence in the system’s performance.
Long-Term Cost Efficiency: While high-quality materials may involve a higher initial investment, they can lead to significant savings over time. Reduced maintenance costs, fewer replacements, and decreased downtime due to leaks contribute to the overall efficiency of operations.
Environmental Considerations
A. Effects of Temperature and Humidity on Hoses
Temperature and humidity play significant roles in the performance and longevity of hydraulic hoses. High temperatures can cause hoses to become brittle, leading to cracks and leaks, especially if they are not rated for such conditions. Conversely, extreme cold can make hoses rigid and less flexible, increasing the risk of fractures during operation. Humidity can introduce moisture into the system, promoting corrosion in metal fittings and degrading the hose material over time. It is essential to select hoses that can withstand the expected temperature and humidity ranges of the operating environment to ensure reliability.
B. Protecting Hoses from External Damage
Protecting hydraulic hoses from external damage is crucial for preventing leaks and maintaining system integrity. This involves several strategies:
Routing and Installation: Hoses should be routed away from sharp edges, moving parts, and potential sources of abrasion. Proper installation techniques, such as using protective sleeves or conduits, can shield hoses from mechanical damage.
Environmental Shields: For hoses exposed to harsh environmental conditions, consider using covers or shields to protect them from UV radiation, extreme temperatures, and chemical spills. These protective measures can significantly extend the lifespan of hoses.
Regular Inspections: Conduct routine inspections to identify any signs of wear or damage early. This proactive approach allows for timely maintenance or replacement, reducing the risk of leaks caused by external factors.
C. Adapting to Seasonal Changes
Seasonal changes can impact hydraulic hose performance and should be considered in maintenance practices. In winter, cold temperatures can stiffen hoses, while summer heat can accelerate wear. Organizations should adapt their maintenance schedules to account for these fluctuations:
Winter Preparation: Inspect hoses for flexibility and signs of brittleness before colder months. Consider using anti-freeze hydraulic fluids if applicable and ensure that hoses are adequately protected from freezing temperatures.
Summer Adjustments: In hot weather, increased temperatures can lead to hose expansion and a higher likelihood of leaks. Regularly check for signs of wear and ensure proper ventilation in areas where hydraulic systems operate.
Conclusion
Preventing hydraulic hose leaks is crucial for maintaining the efficiency and safety of hydraulic systems across various industries. Leaks can lead to significant operational disruptions, increased maintenance costs, and safety hazards, making it essential to address this issue proactively. By understanding the common causes of leaks, regularly inspecting components, and employing best practices in installation and maintenance, organizations can safeguard their operations. The cumulative impact of these efforts not only extends the lifespan of hydraulic hoses but also enhances overall system reliability.
FAQ
What are the common causes of hydraulic hose leaks?
Common causes include wear and tear, incorrect installation, environmental factors, and damage from external sources.
How often should hydraulic hoses be inspected?
Hoses should be inspected regularly, with daily visual checks, weekly thorough inspections, and monthly detailed assessments recommended.
What materials should I choose for hydraulic hoses and fittings?
Select hoses and fittings made from durable materials compatible with your specific hydraulic fluid, considering pressure and temperature ratings.
How can I protect hydraulic hoses from damage?
Use protective sleeves, ensure proper routing away from sharp edges, and conduct regular inspections to identify any signs of wear early.
When should I repair or replace a hydraulic hose?
Replace hoses that show significant wear, cracking, or leaks. Minor abrasions may be repairable, but assess the overall condition before deciding.
What installation practices help prevent leaks?
Follow manufacturer torque specifications, ensure proper alignment and support, and prevent contamination during installation for optimal sealing.