Tangled hoses not only disrupt the smooth functioning of hydraulic systems but can also lead to increased downtime, costly repairs, and potential safety hazards. Kinks in hoses can restrict fluid flow, causing pressure imbalances that may damage components or reduce the overall efficiency of the system.
Understanding Hydraulic Hose Tangles
A. Definition and Causes of Hose Tangles
Hydraulic hose tangles refer to the entanglement or twisting of hoses that can occur during operation or storage. This problem is particularly common in dynamic applications where hoses are frequently moved or flexed. Tangling often results from poor routing, inadequate support, or the inherent flexibility of the hoses themselves. Several factors contribute to hose tangles:
Improper Installation: Hoses that are not installed correctly may experience excessive movement, leading to tangles as they interact with other equipment or themselves.
Insufficient Support: Lack of adequate support or guidance mechanisms can allow hoses to shift position, especially in mobile applications, increasing the likelihood of tangling.
Environmental Conditions: In environments with limited space or high levels of activity, hoses are more prone to getting caught on other components, resulting in tangles.
Material Fatigue: Over time, hoses can become worn or stiff, losing their flexibility. This fatigue can exacerbate the tendency to tangle, particularly if they are frequently repositioned.
Understanding these causes is crucial for developing strategies to mitigate hose tangles and ensure the smooth operation of hydraulic systems.
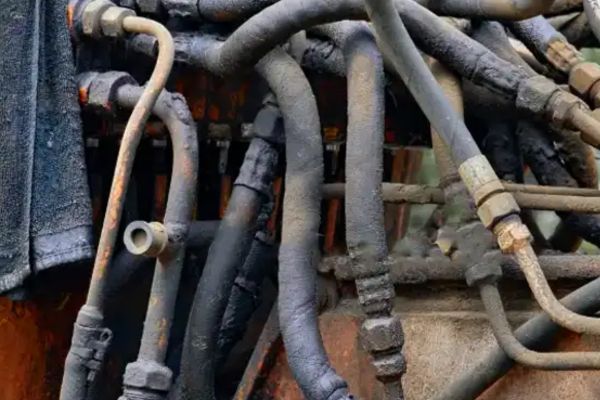
B. Effects of Tangles on System Performance
The presence of tangled hoses can significantly affect the performance of hydraulic systems in several ways:
Reduced Efficiency:
Tangles restrict the flow of hydraulic fluid, leading to pressure drops and inefficient system operation. When hoses are kinked or twisted, the pump must work harder to maintain pressure, resulting in increased energy consumption.
Additionally, reduced efficiency can manifest in slower response times for hydraulic actuators, affecting overall productivity.
Increased Wear and Tear:
The friction created by tangled hoses can lead to accelerated wear on both the hoses themselves and other system components. This wear may result in leaks or complete hose failure, necessitating costly repairs or replacements.
Frequent tangling and subsequent repositioning can also cause damage to fittings and connectors, leading to further maintenance issues and downtime.
Potential Safety Hazards:
Tangled hoses can pose serious safety risks in the workplace. They may obstruct pathways, increasing the risk of tripping or falling hazards for personnel.
In extreme cases, a hose failure due to tangling can lead to high-pressure fluid leaks, creating dangerous conditions for workers and damaging equipment.
Furthermore, the unpredictable nature of hose movement can make it difficult for operators to control machinery, heightening the risk of accidents.
Types of Hydraulic Hoses
A. Overview of Common Hose Materials
Hydraulic hoses are constructed from various materials, each offering unique advantages suited to specific applications. The three most common types of hydraulic hose materials are rubber, thermoplastic, and metal.
Rubber:
Rubber hoses are widely used in hydraulic applications due to their excellent flexibility and ability to withstand high pressures. They can handle a range of temperatures and are often reinforced with textile or steel braiding to enhance strength.
Thermoplastic:
Thermoplastic hoses are made from polymer materials and are known for their lightweight and flexibility. They are resistant to abrasion and chemicals, making them suitable for applications where exposure to harsh environments is a concern.
Metal:
Metal hoses, often made from stainless steel or other alloys, provide exceptional durability and resistance to extreme temperatures and pressures. They are ideal for high-stress applications, but their rigidity can limit flexibility compared to rubber or thermoplastic hoses.
B. Characteristics of Each Type
Each type of hydraulic hose material possesses distinct characteristics that influence its performance and suitability for various applications:
Flexibility:
Rubber: Highly flexible, allowing for easier routing and installation in tight spaces.
Thermoplastic: Offers good flexibility, though it may be less flexible than rubber in extreme temperatures.
Metal: Generally rigid, which can limit flexibility but provides stability in high-pressure situations.
Durability:
Rubber: Durable but may degrade over time due to exposure to UV light, ozone, or certain chemicals. Regular maintenance is essential to extend lifespan.
Thermoplastic: Highly resistant to abrasion and chemicals, leading to a longer lifespan in harsh environments.
Metal: Extremely durable and resistant to wear, making it suitable for demanding applications but heavier and less maneuverable.
Pressure Rating:
Rubber: Typically designed to handle moderate to high pressures, depending on construction and reinforcement.
Thermoplastic: Available in a range of pressure ratings, often used for lower-pressure applications.
Metal: Capable of handling very high pressures, making it suitable for extreme hydraulic applications where other materials may fail.
C. Choosing the Right Hose for Your Application
Selecting the appropriate hydraulic hose is critical to ensuring optimal system performance and longevity. Consider the following factors when making your choice:
Application Requirements:
Assess the specific needs of your application, including pressure, temperature, and environmental conditions. High-pressure applications may require metal hoses, while flexible routing in tight spaces may necessitate rubber or thermoplastic options.
Chemical Compatibility:
Ensure that the hose material is compatible with the fluids it will carry. Certain chemicals can degrade rubber hoses, while thermoplastic and metal hoses may offer better resistance.
Installation and Maintenance:
Consider the installation environment and the ease of maintenance. Hoses that are easier to install and maintain can lead to reduced downtime and lower long-term costs.
Budget:
Evaluate your budget while considering the long-term costs associated with hose performance and replacement. Investing in higher-quality hoses may reduce maintenance and replacement needs over time.
Hose Carrier Solutions
A. Introduction to Hose Carriers
Hose carriers are specialized systems designed to organize, support, and protect hydraulic hoses and cables across a variety of applications. They are essential in maintaining the functionality of hydraulic systems by preventing tangles and kinks, which can disrupt fluid flow and lead to system failures. By effectively managing hose placement, hose carriers not only enhance the longevity of hoses but also improve the overall efficiency and safety of hydraulic operations.
The importance of hose carriers is particularly pronounced in environments where movement and flexibility are critical. As hydraulic systems evolve, the integration of advanced hose carrier solutions becomes necessary for optimizing system performance and ensuring reliability. Selecting the appropriate type of hose carrier is essential, as it can greatly influence the system’s operational efficiency, maintenance needs, and safety protocols.
B. Types of Hose Carriers
Metal Link Carriers:
Description: Metal link carriers consist of interlocking metal links that form a flexible chain. This design provides high flexibility while offering robust support for hydraulic hoses.
Applications: Ideal for applications requiring a high load-bearing capacity, such as industrial machinery and heavy equipment. They are particularly useful in environments where high pressure and heavy loads are common.
Advantages: These carriers are durable and can withstand harsh environmental conditions, making them suitable for heavy-duty applications. Their design allows for significant movement, accommodating the dynamic nature of hydraulic systems.
Enclosed Metal Carriers:
Description: Enclosed metal carriers feature a closed design that completely encases the hoses, protecting them from debris and physical damage. They typically come with removable covers for easy access during maintenance.
Applications: These carriers are particularly useful in environments where hoses are exposed to contaminants, such as construction sites or manufacturing facilities. They provide an extra layer of protection in harsh conditions.
Advantages: The enclosed design enhances protection against environmental hazards, significantly reducing the risk of tangling and damage. This makes them a preferred choice for critical applications where hose integrity is paramount.
Nonmetallic Link Carriers:
Description: Made from materials like plastic or composite, nonmetallic link carriers offer flexibility and lightweight properties. They are designed to be adaptable and efficient.
Applications: Commonly used in applications where weight reduction is critical, such as robotics, automotive manufacturing, or mobile equipment. Their lightweight nature allows for easier handling and installation.
Advantages: These carriers are resistant to corrosion and chemicals, making them suitable for a variety of environments, including those that may expose hoses to harsh substances. They also provide a cost-effective solution for weight-sensitive applications.
Nonmetallic Tube Carriers:
Description: Nonmetallic tube carriers consist of a rigid tube design that houses hoses, providing a protected pathway for their movement. This design is effective for linear routing.
Applications: Frequently used in applications requiring guided movement along a predetermined path, such as conveyor systems, automated machinery, and packaging lines. Their design ensures consistent and efficient operation.
Advantages: These carriers prevent tangles while allowing for linear movement, and maintaining hose integrity. Their structured design minimizes the risk of damage during operation, making them suitable for sensitive applications.
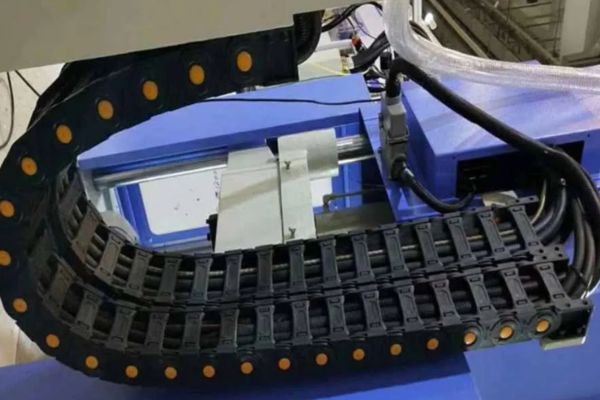
C. Benefits of Using Hose Carriers
Preventing Tangles:
Hose carriers are specifically designed to organize hoses, minimizing the risk of tangling. By providing a structured path for hoses to follow, they keep them securely in place, significantly reducing the likelihood of kinks and twists. This organizational aspect is critical in dynamic environments where hoses are frequently moved or adjusted. Moreover, preventing tangles helps maintain optimal fluid flow, ensuring the efficiency of hydraulic systems.
Enhancing Mobility and Flexibility:
Many hose carriers allow for natural movement of the hoses, accommodating shifts in position without compromising the integrity of the system. This flexibility is especially important in mobile applications, such as construction or manufacturing, where equipment must be maneuvered frequently. Hose carriers facilitate smooth transitions, allowing for greater ease of operation and reducing the risk of accidental damage to hoses during movement. The ability to adapt to changing positions also supports dynamic processes in production lines.
Reducing Maintenance Costs:
By preventing hose tangles and reducing wear and tear, hose carriers can lead to lower maintenance costs over time. With fewer instances of hose damage or failure, organizations can experience decreased downtime and repair expenses. The organized nature of hoses also simplifies maintenance procedures, making inspections and replacements quicker and more efficient. Furthermore, by extending the lifespan of hoses through proper management, companies can achieve significant cost savings in terms of materials and labor.
Improving Safety:
Hose carriers contribute to a safer working environment by minimizing the risk of hose-related accidents. Organized hoses reduce tripping hazards in the workplace, thereby enhancing overall safety for personnel. Additionally, the protection offered by hose carriers helps prevent leaks and spills, which can pose serious safety risks. By ensuring that hoses are well-managed, organizations can foster a culture of safety that is crucial for operational integrity.
Best Practices for Hose Management
A. Proper Routing and Installation
Effective hose management begins with the proper routing and installation of hydraulic hoses. This foundational step is crucial in preventing tangles and ensuring the longevity of the system.
Avoiding Sharp Bends and Kinks:
Guidelines: Hoses should be routed in a manner that avoids sharp bends or kinks, which can restrict fluid flow and lead to premature wear. A general rule of thumb is to maintain a minimum bend radius as specified by the hose manufacturer.
Installation Techniques: Use brackets, clamps, and supports to secure hoses in place. These supports should be positioned to allow for natural movement without putting stress on the hoses. Proper routing not only helps in avoiding tangles but also minimizes abrasion and damage from friction against other surfaces.
Using Proper Fittings and Connectors:
Compatibility: Ensure that the fittings and connectors used are compatible with the hose material and size. Using mismatched components can lead to leaks and system failures.
Secure Connections: All fittings should be installed according to the manufacturer’s specifications, ensuring that connections are tight but not over-tightened, which can cause damage. Consider using thread sealants or O-rings where applicable to prevent leaks.
Accessibility: Position hoses and connectors in inaccessible locations for future maintenance and inspections. Proper placement can save time and reduce the risk of accidental damage during service.
B. Regular Maintenance and Inspection
Regular maintenance and inspection are essential to prolonging the lifespan of hydraulic hoses and preventing potential failures.
Checking for Wear and Damage:
Visual Inspections: Conduct regular visual inspections to check for signs of wear, such as abrasions, cracks, or bulges in the hose. Any visible damage should be addressed immediately to avoid further issues.
Pressure Testing: Periodically perform pressure tests to ensure that hoses can handle their intended operating pressures without leakage or failure. This can help identify potential weak points before they lead to catastrophic failures.
Cleaning and Replacing Hoses as Needed:
Cleaning: Keep hoses clean and free from debris that could cause abrasion or contamination. Use appropriate cleaning methods that do not damage the hose material.
Replacement Protocols: Establish a replacement schedule based on the manufacturer’s recommendations and the operating conditions. Hoses subjected to extreme conditions may require more frequent replacement. Maintaining a stock of replacement hoses can minimize downtime during critical repairs.
C. Training Personnel on Best Practices
Training is a vital component of effective hose management. Ensuring that all personnel are knowledgeable about best practices can significantly reduce the likelihood of errors that lead to hose tangles and failures.
Training Programs: Implement regular training sessions that cover topics such as hose routing, installation techniques, and maintenance protocols. Hands-on training can be particularly effective, allowing personnel to practice proper techniques in a controlled environment.
Safety Awareness: Educate staff about the potential hazards associated with improper hose management, including safety risks related to leaks and equipment failures. Understanding these risks can foster a culture of safety and accountability.
Documentation and Resources: Provide accessible resources, such as manuals and quick-reference guides, that outline best practices for hose management. Encouraging personnel to consult these resources can reinforce learning and ensure adherence to established protocols.
Feedback Mechanism: Establish a feedback mechanism where personnel can report issues or suggest improvements related to hose management. This can lead to continuous improvement and foster a collaborative environment focused on operational efficiency.
Conclusion
As you reflect on the content of this article, we encourage you to assess your hydraulic systems critically. Take the time to evaluate your hose routing, installation techniques, and maintenance schedules. Are your hoses positioned correctly? Are there any signs of wear or damage that need immediate attention? By implementing the strategies discussed, you can mitigate the risks associated with hose tangles and contribute to the overall efficiency and safety of your operations.
FAQ
What is a hose carrier?
A hose carrier is a specialized system designed to organize, support, and protect hydraulic hoses and cables, preventing tangles and kinks that can disrupt fluid flow.
What types of hose carriers are available?
Common types include metal link carriers, enclosed metal carriers, nonmetallic link carriers, and nonmetallic tube carriers, each suited for different applications and environments.
How do hose carriers prevent tangles?
Hose carriers provide a structured path for hoses, keeping them securely in place and minimizing the risk of kinks and twists, especially in dynamic environments.
What are the benefits of using hose carriers?
Benefits include preventing tangles, enhancing mobility and flexibility, reducing maintenance costs, and improving safety in the workplace.
Where are hose carriers typically used?
Hose carriers are used in various applications, including industrial machinery, construction sites, manufacturing facilities, and automated systems, where organized hose management is essential.
How can I choose the right hose carrier for my application?
Consider factors such as the type of environment, load-bearing requirements, flexibility needs, and whether the hoses will be exposed to contaminants to select the appropriate hose carrier type.