Downtime eats profits—fast. Yet, most procurement managers still see hydraulic hose fittings as low-value parts, focusing only on their small price tags instead of their true impact on operations. Here’s a wake-up call: the latest data shows hydraulic system failures cause nearly a quarter of all unplanned downtime in major industries, and almost 40% of those failures start with the humble hose fitting. These parts may cost less than 5% of the entire system, but when a single $20 fitting gives out, the ripple effects can send losses soaring—think thousands lost every hour, skyrocketing emergency labor bills, damaged machinery, even safety and compliance headaches. If your team isn’t factoring the full cost of a fitting failure into your bottom line, you’re missing out on one of the biggest opportunities to slash downtime costs by up to 35%. In the next sections, we’ll break down exactly how a smarter approach to buying hose fittings can turn a small investment into major, measurable savings.
The Real Numbers: Insights from Industry Data
Industry research and real-world operational data provide compelling evidence of the relationship between fitting quality and system reliability. Let’s examine the key findings from authoritative sources:
Failure Rate and Downtime Impact
According to BOA Hydraulics, forestry companies have calculated downtime costs of approximately $20 per minute when equipment is non-operational during working hours. This can quickly escalate when considering that remote operations may wait in excess of 2-4 hours for repairs.
The forestry industry alone loses over $130 million annually in productivity due to hydraulic hose failures, with the average forestry crew losing 10-15 hours per month at an average cost of $1,200 per hour.
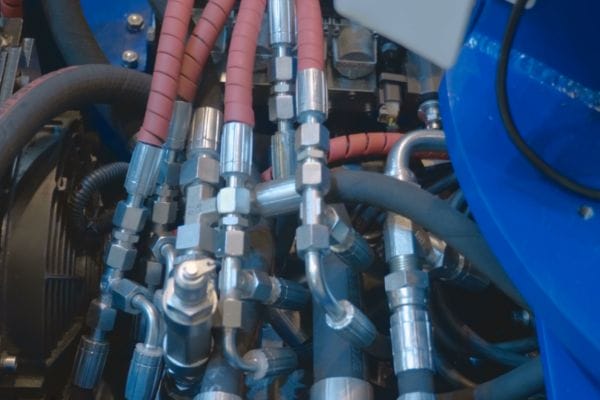
Cost Impact Analysis by Industry
Based on industry data, we can estimate the financial impact of fitting-related downtime across different sectors:
Forestry
- Average downtime cost: $1,200 per hour
- Average monthly downtime: 10-15 hours
- Monthly cost impact: $12,000-$18,000
- Annual cost impact: $144,000-$216,000
Mining
- Higher equipment costs and production values
- Remote locations with longer repair wait times
- Environmental remediation costs for oil spills
- Potential regulatory penalties
Construction
- Project deadline impacts
- Equipment rental extension costs
- Labor idle time expenses
- Contract penalty risks
Manufacturing
- Production line stoppage costs
- Product quality issues from interrupted processes
- Delivery schedule impacts
- Customer satisfaction effects
Key Performance Indicators Affected by Fitting Quality
Industry experts have identified several critical KPIs directly influenced by hydraulic fitting quality:
- Equipment Uptime: Premium fittings contribute to significant improvements in overall equipment availability
- Mean Time Between Failures (MTBF): Higher quality fittings substantially extend the time between system failures
- Maintenance Labor Hours: Quality fittings reduce maintenance requirements and emergency repairs
- Safety Incidents: Better fittings minimize the risk of catastrophic failures and associated safety hazards
- Environmental Compliance: Reduced leakage and failures help maintain environmental standards and avoid remediation costs
Understanding Your True Costs: The Real Impact of Hydraulic System Failures
When evaluating the financial impact of hydraulic hose fitting failures, procurement and financial professionals must look beyond the immediate replacement cost of components.
Direct Operational Costs
Production Losses
The most significant cost associated with hydraulic system failures is typically lost production. According to BOA Hydraulics research, forestry operations face costs of approximately $1,200 per hour of downtime. In mining operations, these costs can escalate dramatically due to higher equipment values and production rates.
For example, a four-hour repair window for a hydraulic hose failure in forestry operations translates to $4,800 in lost production alone. When considering that BOA Hydraulics data shows forestry crews experience 10-15 hours of downtime monthly due to hydraulic issues, the annual production loss can exceed $170,000 for a single crew.
Emergency Repair Labor
Unplanned hydraulic failures often require immediate attention, frequently involving:
- Overtime labor costs (typically 1.5x standard rates)
- Multiple technicians diverted from scheduled tasks
- Travel time to remote locations (particularly in mining, forestry, and construction)
A standard repair might require two technicians working four hours at overtime rates ($75/hr + $37.50 overtime premium), resulting in $900 in labor costs alone—significantly higher than planned maintenance labor costs for the same work.
Replacement Components
Beyond the failed fitting itself, hydraulic failures often damage adjacent components:
- Contamination of hydraulic fluid requiring system flushing
- Damage to pumps from air introduction or contamination
- Collateral damage to nearby components from high-pressure fluid release
What begins as a $25 fitting replacement can quickly escalate to several hundred dollars in component costs.
Equipment Rental and Substitution
When critical equipment is disabled, operations often require temporary replacements:
- Daily rental costs for substitute equipment
- Transportation costs for equipment delivery
- Reduced efficiency with unfamiliar rental equipment
For construction operations, a single day’s rental of replacement equipment can easily exceed $1,200, not including delivery and setup costs.
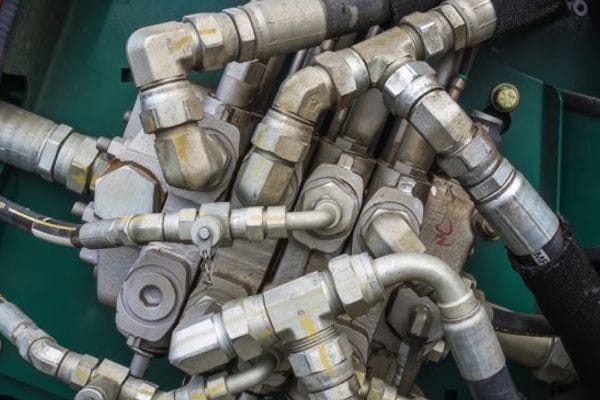
Hidden and Indirect Costs
Project Timeline Impacts
Particularly in construction and project-based industries, hydraulic failures create cascading schedule effects:
- Missed project milestones and deadlines
- Rescheduling of dependent activities
- Contract penalties for timeline extensions
As noted by industry experts, these schedule impacts often exceed the direct costs of the failure itself, especially in time-sensitive projects with contractual deadlines.
Quality and Rework Expenses
When hydraulic systems fail during critical operations, quality issues frequently result:
- Incomplete or improper material processing
- Surface finish or tolerance problems in manufacturing
- Rework requirements for affected materials
Manufacturing operations report that quality-related costs from interrupted processes can reach thousands of dollars per incident, particularly when precision work is affected.
Environmental Remediation
Hydraulic fluid releases create environmental liabilities:
- Cleanup costs for contaminated soil or water
- Regulatory reporting and compliance expenses
- Potential fines for environmental violations
According to industry case studies, even minor hydraulic fluid spills can result in remediation costs exceeding $5,000, with major spills in environmentally sensitive areas potentially costing hundreds of thousands.
Safety Incidents and Liability
High-pressure hydraulic failures present significant safety risks:
- Medical costs for injuries from high-pressure fluid injection
- Workers’ compensation claims and lost time
- Increased insurance premiums following incidents
- Potential regulatory penalties for safety violations
The average cost of a recordable safety incident related to hydraulic failure can exceed $45,000 when all direct and indirect costs are considered.
Industry-Specific Cost Considerations
Forestry Operations
- Remote locations with limited access for repair services
- Weather-dependent harvesting windows that cannot be recovered
- Average monthly downtime of 10-15 hours per crew
- Industry-wide annual productivity losses exceeding $130 million
Mining Operations
Mining faces some of the highest costs from hydraulic failures:
- Extremely high hourly production values
- Environmental sensitivity and regulatory scrutiny
- Remote locations with difficult access
- High-value equipment with specialized components
Manufacturing
Manufacturing operations experience distinct impacts:
- Production line interdependencies that amplify downtime effects
- Quality control challenges from interrupted processes
- Customer delivery commitments with limited flexibility
- Reputation damage from missed deliveries
Construction
Construction projects face time-sensitive challenges:
- Contractual deadlines with financial penalties
- Coordination dependencies with other contractors
- Weather and season constraints on project timelines
- Equipment rental costs during downtime
Comparative Cost Analysis: Standard vs. Premium Components
When comparing the total cost impact of standard versus premium hydraulic fittings, the data reveals a compelling case for quality:
Standard Components
- Lower initial purchase price
- Higher failure frequency (industry data suggests 35-50% more failures)
- Longer average repair times due to more catastrophic failure modes
- Higher annual maintenance costs
- Greater risk of collateral damage
Premium Components
- Higher initial purchase price (typically 20-40% premium)
- Significantly reduced failure rates
- Shorter repair times when failures do occur
- Lower annual maintenance costs
- Reduced risk of catastrophic failures and collateral damage
Using the data showing forestry crews experience 10-15 hours of downtime monthly with standard components, a conservative estimate of 35% downtime reduction with premium components yields:
- Standard components: 12 hours monthly downtime × $1,200/hr × 12 months = $172,800 annual cost
- Premium components: 7.8 hours monthly downtime × $1,200/hr × 12 months = $112,320 annual cost
- Annual savings: $60,480
This $60,480 annual savings dwarfs the typical price premium of $3,000-$5,000 for upgrading to premium hydraulic fittings across an entire forestry operation.
Long-term Financial Perspective
Financial and procurement professionals must consider several additional factors when evaluating the true cost impact:
Asset Lifecycle Extension
- Premium components typically extend overall system life
- Reduced stress on pumps, valves, and actuators
- Fewer major overhauls and rebuilds required
Maintenance Resource Optimization
- Planned vs. emergency maintenance allocation
- Reduced overtime requirements
- More efficient use of technical personnel
Operational Reliability Benefits
- Improved customer satisfaction and retention
- Enhanced reputation for reliability
- Competitive advantage in time-sensitive markets
- Improved employee morale from reduced emergency repairs
By thoroughly understanding these direct, indirect, and long-term cost factors, procurement and financial professionals can make truly informed decisions about hydraulic component quality that reflect the complete financial reality rather than simply the initial purchase price.
The Five Key Factors That Determine Hydraulic Fitting Value
Choosing the right hydraulic fitting is never just about ticking a box or picking the lowest price from a catalog. For anyone tasked with keeping operations running smoothly—and budgets in check—these five factors can make or break your downtime math. Let’s break down what really determines the value behind every fitting you buy.
Material Quality: The Backbone of Long-Term Reliability
Not all fittings are created equal—especially when it comes to what’s inside. Premium hydraulic fittings start with top-tier materials, such as 316 stainless steel, that stand up to harsh chemicals, moisture, and relentless use. These high-grade alloys don’t just fight off rust. They shrug off vibration and resist fatigue far better than cheaper alternatives. For buyers in marine, chemical, or outdoor environments, this isn’t just a preference—it’s a necessity. Skimping on material quality may save a few dollars upfront, but it often leads to early failures, leaks, and expensive replacements long before the system’s lifecycle should end.
Manufacturing Precision: Where Microns Make Millions
Precision is not just a buzzword in the hydraulic world—it’s the foundation of system integrity. Fittings made to tight tolerances create a more reliable seal, minimizing the risk of leaks and blowouts that could halt your line in an instant. Consistent, well-cut threads mean connections go together smoothly, torque specifications are met, and fittings don’t loosen over time. Surface finishes, often overlooked, play a huge role in sealing and corrosion resistance. A smooth, uniform finish ensures O-rings or sealing surfaces work as intended, keeping your system leak-free and efficient for longer.
Design Engineering: Smarter Shapes, Stronger Systems
Modern fittings aren’t just chunks of metal—they’re the result of engineering that considers real-world stress, fluid flow, and longevity. Look for features like advanced sealing geometries that spread pressure more evenly, minimizing the risk of cracks or leaks at stress points. Flow-optimized internal passages reduce turbulence and pressure drop, making your system more energy-efficient. Reinforcements in high-stress zones mean your fittings can handle spikes in pressure or vibration without failing—giving you peace of mind in even the toughest jobs.
Testing and Certification: Proof, Not Promises
Would you trust a critical hydraulic connection on a test result from just a single sample? High-quality suppliers go beyond the bare minimum. They conduct rigorous batch testing to catch hidden defects, provide full traceability documentation (vital in safety-critical or regulated industries), and maintain industry certifications that demonstrate compliance and reliability. Certifications for sectors like mining, offshore, or food processing aren’t just paperwork—they’re an extra layer of assurance that every fitting will perform as expected, every time.
Supplier Support: Your Partner in Performance
Fittings are only as good as the support that comes with them. The best suppliers offer real application advice for their products, helping you choose the right fitting for each use case. Most importantly, should a problem arise, they will step in quickly to provide technical help, spare parts and keep downtime to an absolute minimum. It’s this type of partnership that separates the truly value-oriented supplier from the one that just boxes and ships.
Implementation Strategy: How to Capture the 35% Downtime Reduction
Achieving the full 35% downtime reduction potential requires more than simply purchasing premium fittings. Successful organizations implement a comprehensive strategy:
Phase 1: Assessment and Baseline Establishment (1-2 months)
Document current hydraulic system performance metrics:
- Failure frequency by component type
- Average downtime duration
- Cost impact per incident
- Current fitting specifications and suppliers
Identify critical systems where reliability improvements would deliver maximum value
Establish clear KPIs for measuring improvement:
- Reduction in unplanned downtime hours
- Decrease in emergency maintenance events
- Improvement in equipment uptime
- Reduction in total maintenance costs
Phase 2: Strategic Implementation (3-6 months)
Develop tiered fitting specifications based on application criticality:
- Critical systems: Premium fittings with comprehensive certification
- Standard systems: Mid-tier fittings with appropriate safety factors
- Non-critical systems: Standard fittings meeting basic requirements
Implement pilot program on highest-impact systems:
- Replace fittings during scheduled maintenance
- Document installation procedures and torque values
- Establish monitoring protocol for performance tracking
Train maintenance personnel on:
- Proper installation techniques
- Early failure detection methods
- Documentation requirements for ROI validation
Phase 3: Expansion and Optimization (6-12 months)
- Analyze pilot program results and adjust specifications as needed
- Expand implementation to additional systems based on priority ranking
- Negotiate supplier agreements leveraging volume commitments for improved pricing
- Implement predictive maintenance protocols for hydraulic systems
Conclusion
The numbers speak for themselves: organizations that choose parts based on real value, not just price, see up to 35% less downtime, reduced maintenance needs, safer workplaces, and more reliable equipment. Not only are these improvements worthwhile, the return is often ten times the investment in better accessories. In a market where every inch counts, this is a strategic move that procurement and finance teams cannot afford to overlook.
If you are in need of the highest quality hydraulic hoses and fittings, contact Topa, we are ready!
FAQ
How much impact does hydraulic hose failure have on equipment operation?
Hydraulic hose failures cause about 37% of unplanned downtime, leading to significant monthly losses and potential safety, environmental, and equipment risks.
What is the ROI of investing in high-quality hydraulic fittings?
Premium hydraulic fittings can reduce downtime by 35%, often delivering a return of over 10:1 compared to their higher initial cost.
What are the main causes of hydraulic hose fitting failures?
Common causes include excessive pressure, poor routing, incompatible materials, hose aging, environmental damage, and low-quality manufacturing.
How do you evaluate the true cost of hydraulic system failures?
Consider lost production, emergency labor, replacement parts, rental costs, project delays, quality issues, environmental and safety costs, and reputation damage.
How do you select the right hydraulic fitting for a specific application?
Choose fittings based on material quality, precision, engineering design, certifications, supplier support, and system criticality.
How do you implement a hydraulic system reliability improvement plan?
Start by benchmarking failures and downtime, identify key systems, implement upgrades in phases, train staff, monitor results, and continually optimize.
References
- BOA Hydraulics. (2022). True Costs of Machine Downtime. Retrieved from https://boahydraulics.com/articles/true-costs-of-machine-downtime
- Power & Motion. (2010 ). Hose monitoring prevents costly downtime. Retrieved from https://www.powermotiontech.com/hydraulics/hose-tubing/article/21884609/hose-monitoring-prevents-costly-downtime