The salt spray test involves exposing materials, typically metals and coatings, to a fine mist of salt water inside a controlled chamber. This accelerated exposure simulates long-term environmental conditions, helping to determine the material’s resistance to corrosion. By observing how materials degrade or react under constant spray, manufacturers can make informed decisions about product durability.
Understanding Corrosion and the Need for Testing
Corrosion is a natural, chemical process that occurs when materials, typically metals, degrade due to their interaction with environmental elements like oxygen, moisture, or salt. Over time, this deterioration can lead to serious damage, affecting both the appearance and functionality of products. In industries where reliability is key, understanding corrosion and how to prevent it is essential to ensure product safety, performance, and longevity.
What is Corrosion and How Does it Affect Materials?
Corrosion is the gradual breakdown of materials, most commonly metals, as they react with external elements such as air, water, or chemicals. The process can result in rust, pitting, or structural failure, depending on the material and environment. For example, when iron or steel reacts with oxygen and moisture, it forms iron oxide (rust), which weakens the material. The damage can occur slowly over time, but when left unchecked, it can compromise the integrity of a product, leading to higher maintenance costs, potential failures, and even hazardous situations.
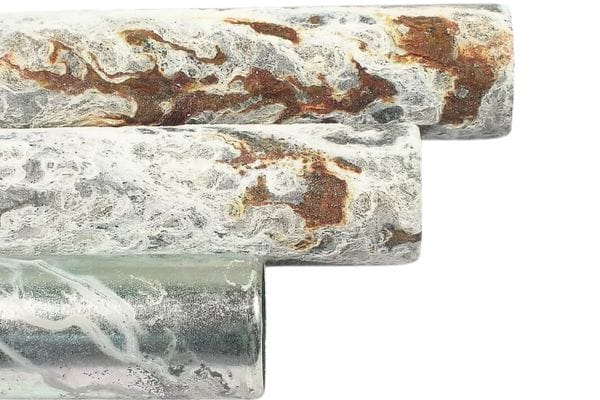
The Role of Corrosion Resistance in Product Durability
Corrosion resistance is the ability of a material or coating to withstand the damaging effects of corrosion. It is a critical factor in determining how long a product can perform reliably in various environments. Products exposed to moisture, humidity, or salt air—such as automotive parts, marine equipment, or construction materials—must have sufficient corrosion resistance to ensure they don’t degrade prematurely. The higher the resistance, the longer the material will remain functional, reducing the need for repairs and replacements, and ultimately extending the product’s lifespan.
Why Corrosion Testing is Crucial for Manufacturing
Corrosion testing is a vital step in the manufacturing process because it allows companies to predict how their products will hold up in real-world conditions. By simulating corrosive environments in a controlled setting, manufacturers can identify potential weaknesses in materials or coatings before products hit the market. This proactive approach not only helps prevent failures and costly repairs but also ensures that products meet industry standards and safety regulations.
How the Salt Spray Test Works
The salt spray test is a controlled and standardized method used to accelerate the process of corrosion. By exposing materials to a fine mist of salt water in a specialized chamber, manufacturers can evaluate how their products will fare in environments with high levels of salt and moisture. The test is designed to simulate long-term exposure, providing valuable insights into material performance and corrosion resistance.
The Salt Spray Chamber: The Heart of the Test
At the core of the salt spray test is the salt spray chamber—a specially designed enclosed space that ensures consistent exposure of materials to a saline mist. The chamber is equipped with a mechanism that atomizes a salt solution, creating a fine spray that circulates throughout the chamber. It is essential for maintaining uniform test conditions, such as constant humidity, temperature, and salt concentration. The chamber’s design allows for precise control over environmental factors, ensuring the test is reliable and reproducible.
Types of Salt Solutions Used in Testing
The solution used in the salt spray test typically consists of a mixture of sodium chloride (NaCl), or common salt, and water. The concentration of salt in the solution plays a significant role in determining the severity of the test. The most commonly used solution is a 5% NaCl solution, which is intended to replicate the corrosive effects of sea spray. In some cases, variations of the solution may be used, such as acidified salt spray solutions for testing materials that will face more aggressive environmental conditions. The composition and preparation of the solution must meet specific standards to ensure consistency in testing results.
Key Variables in Salt Spray Testing
Several variables affect the outcome of the salt spray test, and controlling them is critical for obtaining reliable and accurate results. Key factors include:
Temperature: The test chamber is typically maintained at temperatures between 35°C (95°F) and 50°C (122°F). The temperature affects the rate of corrosion and the condensation of saltwater on the material being tested.
Humidity: The chamber’s humidity levels are kept high to simulate the moist conditions that materials would face in coastal or humid environments. The humidity helps to accelerate corrosion by promoting the formation of rust.
Salt Concentration: The concentration of salt in the mist influences how severe the corrosion will be. A higher concentration leads to a more aggressive test, causing faster degradation of materials.
pH Levels: For certain tests, especially in aggressive environments, the pH of the salt solution may be adjusted to simulate more extreme conditions.
Test Duration and Exposure Cycles Explained
Test duration and exposure cycles are crucial for determining how long a product can withstand corrosive conditions. The typical salt spray test lasts anywhere from 24 hours to several weeks, depending on the material being tested and the desired level of corrosion. Manufacturers may use exposure cycles, which alternate between periods of spraying the salt solution and drying to mimic real-world environmental conditions (e.g., cycles of wet and dry conditions). These cycles help to better simulate how materials will behave under the fluctuating conditions they face in the field. The duration of exposure is often determined by industry standards or specific product requirements, and the longer the exposure, the more severe the corrosion observed.
Standardization and Guidelines for Salt Spray Testing
To ensure consistency, accuracy, and comparability of salt spray test results, a range of established standards and guidelines are followed. These standards provide a framework for performing tests and interpreting results, helping manufacturers meet industry requirements and ensure the reliability of their products. Adhering to these guidelines is essential for maintaining the integrity of testing procedures and ensuring that materials meet the necessary durability and corrosion resistance levels.
ASTM B117: The Gold Standard for Salt Spray Testng
ASTM B117 is widely regarded as the gold standard for salt spray testing. Published by ASTM International, this standard specifies the requirements for conducting the Salt Spray (Fog) Test, outlining the procedures for preparing and testing materials in a salt fog environment. ASTM B117 provides clear guidelines on test chamber design, solution preparation, temperature and humidity control, and exposure duration, ensuring that tests are conducted consistently. This standard is used across various industries, including automotive, aerospace, and manufacturing, to assess the corrosion resistance of materials and coatings. Many manufacturers rely on this standard to meet quality control and product testing requirements.
ISO 9227: International Guidelines for Corrosion Testing
ISO 9227 is the international counterpart to ASTM B117, offering a set of guidelines for conducting corrosion tests in salt mist environments. Like ASTM B117, ISO 9227 provides comprehensive instructions for the preparation of salt solutions, chamber conditions, and test duration. It also outlines different types of corrosion testing, including neutral salt spray tests, cyclic corrosion testing, and accelerated tests. ISO 9227 is recognized globally and serves as the benchmark for testing corrosion resistance in a wide range of industries. While ASTM B117 focuses primarily on the salt spray aspect, ISO 9227 covers a broader range of testing methods and conditions, making it applicable to more diverse environments.
Other Industry Standards for Salt Spray Testing
In addition to ASTM B117 and ISO 9227, several other industry standards and guidelines may be relevant to specific applications or regions. Some of these include:
MIL-STD-810G: This military standard specifies environmental test methods for military equipment, including corrosion testing. It includes a salt fog test method similar to the salt spray test, tailored to military-grade materials and components.
JIS Z 2371: The Japanese Industrial Standard for salt spray test, JIS Z 2371, provides guidelines for testing materials and coatings under salt fog conditions. It is widely used in Japan and other parts of Asia for evaluating corrosion resistance.
SAE J2334: The Society of Automotive Engineers (SAE) standard focuses on the testing of automotive components in accelerated corrosion environments, including salt spray exposure. It’s especially relevant for parts exposed to road salts and harsh weather conditions.
What the Salt Spray Test Can Tell You About Hydraulic Fittings
The salt spray test is a powerful tool for evaluating the durability and corrosion resistance of materials, particularly for components like hydraulic fittings that are exposed to harsh environments. For hydraulic systems, where reliability and safety are critical, understanding how fittings perform under corrosion stress is essential. The salt spray test simulates the corrosive conditions these components may face, providing manufacturers and engineers with valuable insights into how well their products will perform over time.
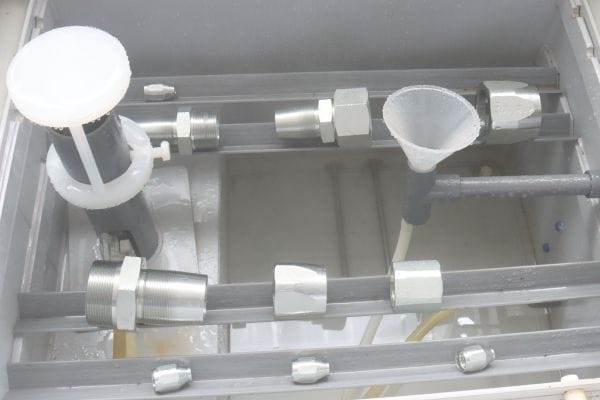
Evaluating Corrosion Resistance and Product Longevity
One of the most important aspects the salt spray test reveals is a material’s corrosion resistance, which directly impacts the longevity of hydraulic fittings. Hydraulic fittings, often made from metals such as steel or brass, are susceptible to rust and degradation when exposed to moisture, salt, or chemicals. The salt spray test accelerates the corrosion process, allowing manufacturers to observe how quickly corrosion develops and how effective coatings or treatments are at preventing damage.
For hydraulic fittings that will be used in environments with exposure to water, marine conditions, or even road salt, the test helps predict how long these parts will remain functional before showing signs of degradation. By assessing corrosion resistance, manufacturers can make informed decisions about the materials and coatings to use for optimal performance and durability, ensuring a longer lifespan for hydraulic systems.
Understanding the Corrosion Rate of Materials
The corrosion rate is a key metric in determining how quickly a material or fitting will degrade under exposure to corrosive environments. The salt spray test can help calculate this rate by tracking the progression of rust or surface degradation over time. For hydraulic fittings, understanding this rate is essential for determining the expected service life of components and scheduling maintenance or replacement intervals.
During the salt spray test, the rate of corrosion can be influenced by factors such as the material type, coating thickness, and exposure cycles. For example, a hydraulic fitting made from stainless steel will likely exhibit a slower corrosion rate compared to one made from carbon steel. The salt spray test provides measurable data on how these materials perform under salt exposure, allowing manufacturers to choose materials and designs that minimize corrosion over time.
How the Test Helps Predict Real-World Performance
While the salt spray test is conducted in a controlled environment, it provides valuable insights into real-world performance. Hydraulic fittings often face a combination of factors, such as moisture, chemicals, and pressure, that can accelerate corrosion in actual use. By simulating these conditions through the test, manufacturers can predict how their fittings will perform in challenging environments, helping them assess the suitability of different materials and protective coatings.
Additionally, the test helps to identify weak points in design or manufacturing that might not be evident in normal conditions but could lead to premature failure in corrosive environments. For example, the test might reveal vulnerabilities in the sealing materials or threading of hydraulic fittings that could compromise their effectiveness over time. This predictive insight allows engineers to make design improvements or choose more durable materials before products are released to the market, ensuring that hydraulic systems maintain reliability and performance over their expected lifespan.
Interpreting Salt Spray Test Results
Interpreting the results of the salt spray test is crucial to understanding how well a material, coating, or component will perform in real-world conditions. The test provides valuable insights into the corrosion resistance of materials, but those results need to be properly assessed to guide decision-making. In this section, we’ll break down how to decode test failures, understand pass/fail criteria, and identify specific signs of corrosion damage.
Decoding Test Failure: What Does It Mean?
A test failure in the salt spray test typically indicates that the material or coating being tested is not sufficiently resistant to corrosion in harsh environments. When failure occurs, it often means that the protective coating has been compromised, or the base material itself is not durable enough for the conditions it is expected to endure.
Common signs of failure include:
Peeling or flaking of coatings: This suggests that the protective layer is not adhering properly to the surface, which can lead to rapid corrosion of the underlying material.
Rust or oxidation: This indicates that the base material has begun to corrode due to insufficient corrosion resistance or ineffective coatings.
Pitting or localized corrosion: Small, concentrated areas of damage suggest that the material is vulnerable to localized attacks, which can compromise the integrity of the component.
Test failure can also occur if the exposure cycle or environmental conditions were not properly simulated or if the test was not conducted according to established standards. In these cases, it’s important to reassess the testing procedure to ensure accuracy. Failure highlights the need for design changes or the application of stronger corrosion-resistant coatings.
Pass or Fail: Understanding Pass/Fail Criteria
The pass/fail criteria are used to evaluate whether the material or product being tested meets industry standards for corrosion resistance. These criteria are based on the extent of corrosion observed after a specific duration of exposure to the salt fog environment.
Pass: A material or component is considered to have passed the test if it shows minimal or no signs of corrosion. Typically, this means no more than a few small rust spots or slight discoloration after the designated exposure period. The material should retain its structural integrity and performance characteristics.
Fail: A failure occurs when there is significant corrosion, such as widespread rust, peeling coatings, or pitting. These signs indicate that the material will not perform adequately in corrosive environments over the long term. If the component shows signs of significant damage or a breakdown in protective coatings, it has failed to meet the necessary corrosion resistance standards.
The pass/fail threshold can vary depending on the industry and specific material requirements. For example, the automotive industry may allow for slight surface discoloration but require no active rust formation, while industries such as aerospace may require zero corrosion after testing. The specific ASTM B117 or ISO 9227 guidelines outline detailed criteria that should be followed for various materials and components.
How to Identify Corrosion Damage in the Test Results
Identifying corrosion damage in salt spray test results requires careful observation and knowledge of the types of corrosion that can occur. Here’s how you can recognize common forms of damage:
General corrosion: This is the most common form of corrosion observed in the salt spray test, characterized by a uniform loss of material across the surface. It usually results in rust or discoloration. It indicates poor corrosion resistance but is often less dangerous than localized corrosion.
Pitting corrosion: Pitting creates small, deep holes or cavities in the surface and is a more dangerous form of corrosion. Even small pits can severely weaken the material, especially if they are concentrated around critical areas like threaded connections or welds.
Blistering or peeling: If a coating starts to peel off or form blisters, it indicates poor adhesion or protection. This type of damage can lead to rapid deterioration of the underlying metal once the protective barrier is broken.
Filiform corrosion: This type of corrosion appears as thread-like formations that spread beneath the surface coating, often leading to extensive damage in a localized area. It usually occurs when there is inadequate sealing or coating around edges and joints.
Rust streaks or staining: If rust is visible on the surface but hasn’t deeply penetrated, it may indicate early-stage corrosion. This could be a sign that the material or coating will degrade further over time, especially in the presence of moisture or salts.
Conclusion
By combining salt spray tests with other quality control and materials testing methods, manufacturers can produce products that not only meet industry standards but also exceed customer expectations in terms of service life and reliability. Topa can salt spray test and report on your hydraulic fittings to meet your needs!
FAQ
What is the salt spray test?
The salt spray test is a corrosion testing method where materials are exposed to a fine mist of saltwater in a controlled chamber to evaluate their resistance to corrosion.
Why is the salt spray test important?
It helps manufacturers predict how materials and coatings will perform in corrosive environments, ensuring long-term durability and performance of products exposed to moisture, salt, and humidity.
How long does the salt spray test take?
Test durations can vary, but typically the salt spray test lasts from 24 hours to several weeks, depending on the material and the required level of corrosion resistance.
What materials are tested in a salt spray test?
Commonly tested materials include metals like steel, aluminum, and brass, as well as coatings, surface treatments, and protective layers used on these materials.
What does a “pass” or “fail” mean in the test results?
A “pass” means the material shows minimal or no corrosion after the test, while a “fail” indicates significant corrosion, such as rust, pitting, or peeling of coatings, showing that the material isn’t suitable for exposure to corrosive environments.
How is the salt spray test different from other corrosion tests?
Unlike other methods, the salt spray test is an accelerated test that mimics the effects of long-term salt exposure in a short amount of time, offering a fast way to assess corrosion resistance.