In the world of hydraulic and pneumatic systems, hoses play a critical role in ensuring smooth and efficient operation. Two of the most commonly used hose types are steel braided hoses and rubber hoses. Each type has its distinct construction, advantages, and limitations, making it crucial to select the right hose for specific applications. The incorrect choice can lead to increased maintenance costs, equipment failures, or even hazardous situations. Therefore, understanding the specific characteristics and benefits of each hose type is crucial for making an informed decision.
Understanding Hose Types
Steel Braided Hoses
Definition and Construction
Steel braided hoses are a type of high-performance hose designed for demanding applications. They consist of a flexible inner core made from various materials like rubber or synthetic compounds, reinforced with a braided layer of stainless steel wire. This braided layer provides significant strength, resistance to pressure, and protection against abrasion and impact. The steel braid acts as a supportive framework, enabling the hose to withstand high pressures without bursting or deformation.
Typical Applications
Steel braided hoses are commonly used in industries where high pressure and durability are crucial. They are widely employed in hydraulic systems, aerospace, automotive, and manufacturing applications. In hydraulic systems, these hoses transfer fluids under high pressure, such as in machinery and equipment. In automotive applications, they are used for brake lines, fuel lines, and coolant systems. Their ability to withstand extreme temperatures and pressures makes them suitable for environments where safety and performance are paramount.
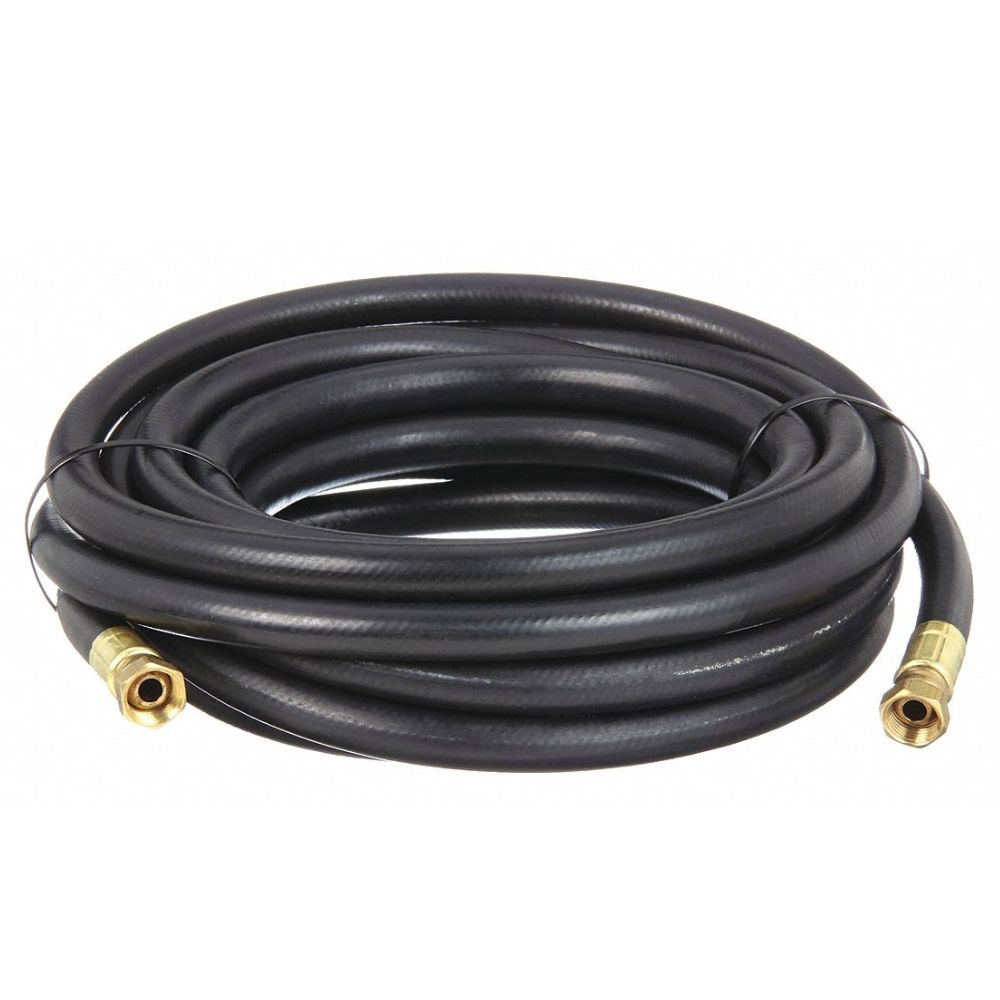
Rubber Hoses
Definition and Construction
Rubber hoses are made from a variety of rubber compounds, often combined with reinforcing materials like textile or synthetic fibers. The inner tube is designed to convey fluids or gases, while the outer cover protects against environmental factors. Rubber hoses are flexible and can be manufactured in various diameters and lengths to suit different applications. The rubber material provides a degree of elasticity, allowing the hose to bend and flex without kinking.
Common Uses and Limitations
Rubber hoses are widely used in industries where flexibility and cost-effectiveness are essential. Common applications include automotive cooling systems, garden hoses, air compressors, and various industrial processes. They are suitable for moderate pressure and temperature ranges and are often used where the hose needs to move or flex frequently.
However, rubber hoses have several limitations. They are more susceptible to damage from environmental factors such as UV radiation, extreme temperatures, and chemical exposure. Over time, rubber can degrade, leading to cracks, leaks, or bursts. Rubber hoses also tend to have lower pressure ratings compared to steel braided hoses, which can be a significant drawback in high-pressure applications. Proper maintenance and timely replacement are crucial to avoid failures and ensure continued performance.
Performance Comparison
Durability and Lifespan
How Steel Braided Hoses Outlast Rubber Hoses
Steel braided hoses generally outlast rubber hoses due to their robust construction. The stainless steel braid provides superior protection against abrasion, punctures, and mechanical damage. Unlike rubber hoses, which can degrade due to environmental exposure and wear over time, the steel braid resists these conditions and maintains its structural integrity longer. The resistance to external forces and pressure variations makes steel braided hoses more reliable in demanding applications, reducing the frequency of replacements and maintenance.
Factors Affecting Hose Longevity
Several factors influence the lifespan of both hose types. For steel braided hoses, the quality of the steel braid, the inner core material, and the hose’s design are critical. Proper installation and maintenance practices also play a significant role. For rubber hoses, environmental factors such as exposure to UV rays, high temperatures, and chemicals can accelerate degradation. Additionally, mechanical stresses like bending and twisting can contribute to wear and tear. Regular inspections and proper handling are essential for extending the lifespan of rubber hoses and ensuring they perform effectively.
Pressure and Temperature Tolerance
Maximum Pressure Ratings
Steel braided hoses are designed to handle significantly higher pressure ratings compared to rubber hoses. The steel braid provides additional strength and support, enabling these hoses to withstand pressures that could cause rubber hoses to burst. Typical steel braided hoses can handle pressures ranging from a few thousand to over ten thousand psi, depending on their construction and intended application. In contrast, rubber hoses generally have lower pressure ratings, with most designed for moderate pressures. They are more likely to fail under extreme pressure conditions, making them unsuitable for high-pressure applications.
Temperature Resistance and Implications for Different Environments
Steel braided hoses excel in temperature resistance, capable of operating effectively across a broad range of temperatures. The stainless steel braid protects the inner core from high heat, while the core material often includes additional heat-resistant properties. This makes steel braided hoses suitable for environments with extreme temperatures, whether high or low. In contrast, rubber hoses have limited temperature resistance. High temperatures can cause rubber to degrade, leading to cracks and leaks. Cold temperatures can make rubber brittle, reducing its flexibility and increasing the risk of failure. As a result, rubber hoses are generally used in environments with moderate temperature fluctuations.
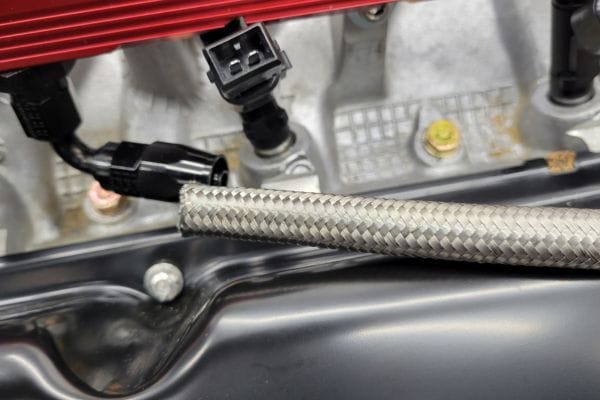
Flexibility and Handling
Bend Radius and Flexibility of Each Type
Rubber hoses are known for their superior flexibility and ease of handling. They can bend and twist without compromising their functionality, making them ideal for applications requiring frequent movement or tight routing. The flexibility of rubber hoses allows them to navigate complex installations and tight spaces with ease. However, this flexibility comes at a cost, as excessive bending or twisting can lead to kinking and reduced performance over time.
Steel braided hoses, while highly durable, are less flexible compared to rubber hoses. The steel braid limits the extent to which these hoses can bend, and they generally have a larger bend radius. This rigidity can be advantageous in maintaining hose integrity under high pressure but may pose challenges in applications where tight bends and frequent movement are required.
Suitability for Tight Spaces and Complex
Installations In tight spaces and complex installations, rubber hoses often outperform steel braided hoses due to their flexibility. They can be routed through confined areas and around obstacles more easily, reducing the need for additional fittings or complex arrangements. Steel braided hoses, due to their rigidity, may require more space for installation and might need additional support or custom fittings to accommodate tight bends.
Factors to Consider When Choosing a Hose
Application Requirements
Matching Hose Type to Specific Needs When selecting a hose, it’s essential to match its type to the specific requirements of the application. Key factors include pressure, temperature, and environmental conditions:
Pressure: Determine the maximum pressure the hose will experience in the application. Steel braided hoses are ideal for high-pressure environments due to their robust construction and high pressure ratings. Rubber hoses are suitable for moderate pressure applications but can fail under extreme conditions.
Temperature: Assess the operating temperature range of the application. Steel braided hoses offer superior temperature resistance and can handle both high and low extremes without significant degradation. Rubber hoses have limited temperature tolerance and are best used in environments with moderate temperature fluctuations.
Environment: Consider environmental factors such as exposure to chemicals, UV radiation, and abrasive conditions. Steel braided hoses provide better resistance to chemical exposure and physical damage. Rubber hoses are more prone to wear and degradation in harsh environments but are often more flexible for applications requiring frequent movement.
Installation Considerations
Ease of Installation and Maintenance The ease of installation and ongoing maintenance are critical factors to consider:
Installation: Rubber hoses are generally easier to install due to their flexibility, which allows them to navigate tight spaces and complex routing without additional fittings. Steel braided hoses, while more robust, may require additional support or custom fittings to accommodate their less flexible nature.
Maintenance: Rubber hoses require regular inspections and maintenance to ensure they are not subjected to excessive wear or environmental damage. Steel braided hoses, although durable, also require periodic checks to ensure the integrity of the braid and the absence of leaks. The initial installation might be more complex for steel braided hoses, but they often require less frequent replacements due to their longer lifespan.
Budget Constraints
Long-term Cost vs. Initial Investment When budgeting for hose selection, consider both the initial cost and long-term value:
Initial Investment: Rubber hoses generally have a lower upfront cost compared to steel braided hoses. This can be advantageous for applications where cost is a primary concern and the performance requirements are within the limits of rubber hoses.
Long-term Cost: Although steel braided hoses have a higher initial cost, their durability and extended lifespan can result in lower long-term costs. They typically require fewer replacements and less maintenance, which can lead to cost savings over time. Additionally, their ability to withstand harsh conditions can reduce the risk of costly downtime and repairs.
In summary, selecting the right hose involves evaluating the specific requirements of the application, considering installation and maintenance factors, and balancing initial costs with long-term benefits. By understanding these factors, you can make an informed decision that ensures optimal performance and cost-efficiency for your needs.
Tips for Proper Hose Maintenance and Installation
Maintenance Practices
Regular Inspections and Care for Both Hose Types
Maintaining hoses is crucial to ensure their longevity and optimal performance. Regular inspections help identify potential issues before they lead to failure:
Visual Inspections: Routinely check hoses for signs of wear, such as cracks, bulges, or abrasions. For rubber hoses, look for signs of deterioration due to environmental factors like UV exposure or chemical contact. For steel braided hoses, inspect the braid for signs of corrosion or damage.
Leak Checks: Regularly examine hose connections and joints for leaks. Use appropriate leak detection methods, such as pressure testing or visual inspection, to ensure that the hose and its fittings are secure and functioning correctly.
Cleaning and Care: Clean hoses as recommended by the manufacturer to prevent the buildup of debris or contaminants that could affect performance. For rubber hoses, avoid using harsh chemicals that could degrade the material. For steel braided hoses, ensure that the braid remains intact and free from external damage.
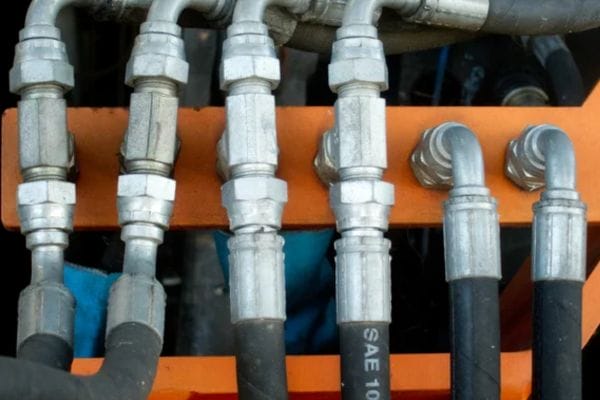
Installation Best Practices
Guidelines for Ensuring Optimal Performance and Longevity
Proper installation is key to maximizing the performance and lifespan of both rubber and steel braided hoses:
Correct Sizing: Ensure that the hose is the correct size for the application. An improperly sized hose can lead to issues such as pressure drop, reduced flow, or increased wear.
Proper Routing: Avoid sharp bends, kinks, or excessive tension during installation. Follow the recommended bend radius for each type of hose to prevent damage. For steel braided hoses, provide adequate support to prevent stress on the fittings and connections.
Secure Fittings: Use appropriate fittings and clamps to secure hoses in place. Ensure that connections are tight but not over-torqued, as excessive force can damage the hose or fittings. For steel braided hoses, ensure that the braid is properly aligned and supported.
Temperature and Environment Considerations: Install hoses in environments that match their specifications. For instance, protect rubber hoses from extreme temperatures and harsh chemicals, and ensure that steel braided hoses are shielded from potential sources of abrasion or mechanical damage.
By following these maintenance and installation tips, you can enhance the performance and extend the service life of both rubber and steel braided hoses. Regular attention and adherence to best practices will help prevent premature failure and ensure reliable operation in your applications.
Conclusion
For the best results, consult with industry experts to ensure that the selected hose type aligns with your specific application needs. Their guidance can help you make an informed decision, ensuring optimal performance and safety. By carefully evaluating your requirements and considering expert advice, you can choose the most appropriate hose for your application, ultimately enhancing efficiency and reducing long-term costs.
FAQ
What are the main differences between steel braided and rubber hoses?
Steel braided hoses offer higher durability, better pressure and temperature resistance, and longer lifespan. Rubber hoses are more flexible and cost-effective, suitable for moderate pressure applications and less extreme conditions.
Can steel braided hoses handle higher pressures than rubber hoses?
Yes, steel braided hoses are designed to withstand significantly higher pressures compared to rubber hoses. They are reinforced with braided steel wire, providing greater strength and pressure tolerance.
How do temperature changes affect steel braided and rubber hoses?
Steel braided hoses are generally more resistant to temperature fluctuations and can handle extreme temperatures better than rubber hoses. Rubber hoses may degrade or become brittle when exposed to high temperatures over time.
Are steel braided hoses more resistant to abrasion and damage?
Yes, steel braided hoses are less prone to abrasion and external damage due to their robust construction, which includes a protective steel braid. Rubber hoses can be more vulnerable to cuts, abrasions, and environmental wear.
What maintenance is required for steel braided hoses compared to rubber hoses?
Both types require regular inspections for leaks, wear, and damage. Steel braided hoses should be checked for braid integrity and corrosion, while rubber hoses need to be inspected for cracks, bulges, and deterioration due to environmental factors.
How do I determine the right hose type for my application?
Consider factors such as the pressure and temperature requirements, environmental conditions, and flexibility needs.