Ball valves are essential for fluid control due to their reliable and efficient operation, offering quick opening and closing with just a quarter turn. They are known for their excellent sealing properties, preventing leaks even under high pressure or extreme conditions.
The Basic Components of a Ball Valve
The Valve Body: The Core of the Valve Mechanism
The valve body is the outer casing that holds all of the internal components of the ball valve together. It is responsible for directing the flow of the fluid through the valve. Made from materials like stainless steel, brass, or plastic, the body is designed to withstand the pressure and temperature of the system it’s used in. The valve body is also critical in determining the type of flow path, whether it’s a full-port, reduced-port, or V-port design.
The Valve Ball: The Heart of the Operation
The ball valve ball is the central element that controls the flow of fluid. The spherical ball has a hole or port through its center, and when it rotates, the port aligns with the pipeline to either allow or block fluid flow. The smooth surface of the ball helps to create an effective seal against the valve seat, preventing leaks when the valve is in the closed position. The ball is often made of durable materials like stainless steel, ceramic, or chrome-plated metal to ensure longevity and resistance to wear.
The Valve Stem: Connecting the Ball to the Actuator
The valve stem is the component that connects the valve ball to the actuator or manual handle. This stem rotates the ball when the actuator or handle is turned. The stem must be strong enough to handle the forces applied during operation and is typically made of stainless steel or similar materials. It also features a sealing mechanism to prevent fluid from leaking along the stem’s shaft, maintaining the integrity of the valve system.
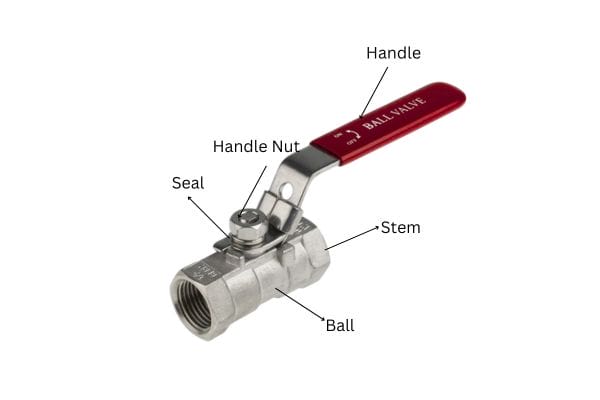
Valve Seat and Sealing: Preventing Leaks and Ensuring Tightness
The valve seat is a crucial part of the ball valve that provides a tight seal when the ball is in the closed position. It is usually made from elastomeric or plastic materials such as PTFE, which are designed to withstand high pressure and temperature while offering a reliable seal. The sealing mechanism ensures that no fluid escapes through the valve body when the ball valve is not in operation, helping to maintain system efficiency and preventing leaks.
The Valve Actuator: Manual vs. Automated Control
The actuator is the mechanism used to open and close the ball valve. It can be manual, such as a lever or handle, or automated, using electric, pneumatic, or hydraulic systems. Manual actuators are typically used in simpler systems or where frequent adjustments aren’t required. Automated actuators, on the other hand, offer the advantage of remote control and precision, making them ideal for complex systems that need constant flow adjustments or where operator safety is a concern. Automated actuators can be integrated into larger control systems for greater operational efficiency and safety.
The Working Principle of a Ball Valve
How the Ball Valve Controls Flow
The ball valve controls fluid flow through the rotation of its spherical ball, which features a hole or port through the center. When the ball rotates, the port either aligns with the pipeline to allow fluid to flow or rotates perpendicular to the flow path, blocking it. This action ensures precise control over the flow of liquids or gases, making it an effective tool for applications requiring fast, reliable flow regulation.
The Quarter-Turn Operation: Simple, Fast, and Efficient
The quarter-turn operation is one of the key advantages of the ball valve. By rotating the valve handle or actuator just 90 degrees, the ball valve either opens or closes the flow passage. This simple, fast, and efficient operation makes the ball valve ideal for situations where quick response times are critical. The design eliminates the need for complicated adjustments, providing a reliable method of controlling flow in a wide range of industrial systems.
Fluid Flow and the Valve’s Position: Open, Closed, or Regulated
The ball valve’s position determines the flow of fluid through the system. When the valve is fully open, the port of the ball aligns with the pipeline, allowing unrestricted flow. When the valve is closed, the ball rotates 90 degrees, cutting off the flow completely. Some ball valves, such as V-port ball valves, allow for partial opening, which provides more precise flow regulation, making them suitable for applications that require fine control over the flow rate.
The Role of the Valve Seat in Flow Regulation
The valve seat plays a crucial role in regulating flow and ensuring a tight seal when the valve is closed. Made from materials like PTFE or other elastomers, the seat provides a sealing surface that conforms to the shape of the ball, preventing leaks even under high pressure. In addition to ensuring a secure seal, the valve seat helps to cushion the ball’s movement, preventing damage and improving the overall lifespan and performance of the valve.
Installation and Assembly of Ball Valves
How to Properly Install a Ball Valve in Your System
Installing a ball valve correctly is crucial for ensuring optimal performance and preventing leaks. Start by choosing the appropriate ball valve for your system based on the fluid type, pressure, and temperature requirements. When installing, ensure the valve is positioned in the correct flow direction, as indicated by the flow arrow on the valve body. Clean the pipe ends thoroughly before attaching the valve to ensure a tight seal. Use appropriate seals and gaskets to prevent leaks, and tighten the valve connections using the correct tools to avoid over-tightening, which could damage the valve or pipe threads. For automated systems, ensure the actuator is properly aligned and connected to the valve stem.
Understanding Valve Assembly: Step-by-Step Process
Valve assembly involves putting together the key components of the ball valve, including the valve body, ball, stem, seat, and actuator (if applicable). Begin by placing the valve ball into the valve body, ensuring it is correctly aligned with the valve seat. Insert the valve stem through the body and attach it to the ball’s rotation mechanism. Secure the valve seat in place, ensuring a proper seal is formed around the ball. If the valve is automated, attach the actuator to the valve stem and ensure all connections are properly aligned and secure. Finally, check that all components move smoothly and the valve functions correctly before proceeding with installation.
Common Installation Mistakes to Avoid
Incorrect Flow Direction: Always check the flow direction marked on the valve to ensure it matches the flow path of your system. Installing the valve backward can cause improper operation.
Inadequate Pipe Preparation: Failing to clean pipe ends and remove debris can lead to poor sealing, leaks, or damage to the valve components.
Over-tightening: Applying excessive force when tightening valve connections can strip threads, damage seals, or crack the valve body.
Wrong Valve Type: Choosing a ball valve that doesn’t match your system’s pressure, temperature, or fluid type can cause malfunction or failure.
Neglecting to Test: After installation, always perform a pressure test to ensure there are no leaks and the valve operates as intended.
Choosing the Right Ball Valve for Your System Design
Selecting the right ball valve involves understanding the specific needs of your system. Consider factors such as:
Flow Rate: Choose a valve that allows for the desired flow rate and pressure. Full-port ball valves offer less resistance to flow than reduced-port valves.
Fluid Type: Different fluids (liquids, gases, or slurries) may require different materials for the valve body, ball, and seals.
Pressure and Temperature: Ensure the valve can handle the operating pressure and temperature of your system. Some materials, such as stainless steel, are better suited for high-pressure applications.
Manual or Automated Control: Decide whether you need a manual valve or an automated system for remote operation. Automated valves require actuators and additional components.
Size and Compatibility: Make sure the valve size matches the pipe dimensions in your system and is compatible with other components like actuators and control systems.
The Role of Ball Valves in Pressure Regulation and Safety
How Ball Valves Contribute to Pressure Control
Ball valves play a significant role in maintaining consistent pressure within a system. By controlling the flow of fluids, they can help regulate pressure, ensuring that it stays within safe operating limits. When fully open, ball valves provide minimal resistance to flow, allowing for smooth passage of fluid without excessive pressure build-up. In contrast, when closed or partially opened, they can help manage pressure by restricting the flow, which helps control pressure downstream. In combination with other pressure control devices, ball valves can effectively support the regulation of system pressure.
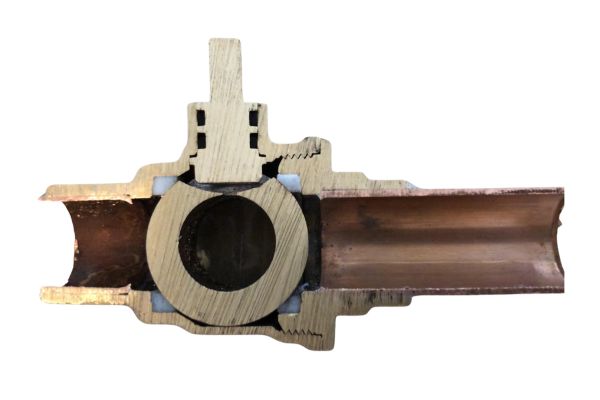
Preventing Pressure Spikes and System Failures
Pressure spikes can occur in systems due to sudden changes in flow, pump surges, or valve malfunctions. Ball valves help mitigate these spikes by quickly responding to changes in flow demand, reducing the chances of pressure surges. By providing precise control over the flow and being able to shut off completely, ball valves help protect sensitive equipment downstream from excessive pressure. In systems with automated valves, integrated pressure monitoring can further ensure that ball valves function properly to prevent dangerous pressure fluctuations that might otherwise lead to equipment failure or system breakdowns.
Safety Considerations for High-Pressure Systems
In high-pressure applications, ball valves are designed to withstand extreme forces, but safety considerations are paramount. Proper selection of materials that can handle high pressures, such as stainless steel or specialized alloys, is critical for preventing valve failure. Additionally, valve bodies are often reinforced to handle the stress of high-pressure environments. It’s essential to ensure the valve is rated for the specific pressure levels of the system to avoid leaks, bursting, or valve damage. Ball valves also provide a level of safety because they are easy to operate, with their quick-opening and quick-closing design allowing for rapid emergency shutdown if necessary.
Pressure Testing and Valve Safety Mechanisms
Pressure testing is an important step in ensuring that a ball valve can handle the pressures it will encounter in the system. This process involves testing the valve under the conditions it will be subjected to during operation, including maximum pressure and temperature levels. Pressure testing helps identify any weaknesses or potential failure points in the valve before it is installed. Additionally, ball valves are often equipped with safety mechanisms such as pressure relief devices, over-pressure protection, and redundant sealing to ensure that if a valve fails or becomes damaged, it doesn’t compromise the safety of the entire system. Regular maintenance and testing of these safety features are essential to maintaining reliable and safe operation in pressure-sensitive systems.
Conclusion
Choosing the right ball valve is crucial for optimizing your fluid control system’s efficiency and reliability. Factors such as the type of fluid, operating pressure and temperature, flow requirements, and whether manual or automated control is needed should all be considered. Proper installation, regular maintenance, and a clear understanding of how the valve operates within your system are essential for maximizing valve lifespan and preventing costly downtime.
FAQ
What is a ball valve?
A ball valve is a type of valve that uses a spherical ball with a hole to control the flow of liquids or gases. When the ball is rotated, the hole aligns with the pipeline to allow flow, or it blocks the flow when turned 90 degrees.
How does a ball valve work?
A ball valve operates by rotating a ball inside the valve body. When the ball’s port aligns with the pipe, fluid can flow; when the ball is rotated 90 degrees, the port is perpendicular to the flow, blocking the passage.
What are the advantages of using a ball valve?
Ball valves provide quick and efficient flow control with a simple quarter-turn operation. They offer excellent sealing capabilities, making them ideal for high-pressure applications, and they have minimal wear and tear due to their durable design.
Can ball valves be used in both high-pressure and low-pressure systems?
Yes, ball valves can be used in both high-pressure and low-pressure systems. However, it is important to select the appropriate valve material and pressure rating for your specific application to ensure safety and efficiency.
How do I install a ball valve?
To install a ball valve, ensure the flow direction aligns with the valve’s markings, clean the pipe ends, and secure the valve using proper fittings. Follow manufacturer instructions and ensure the valve is properly sealed to prevent leaks.
What is the lifespan of a ball valve?
The lifespan of a ball valve depends on factors such as the materials used, the operating conditions (pressure, temperature, fluid type), and maintenance. With proper installation and regular maintenance, ball valves can last many years.