Passivation is a chemical treatment process that enhances the corrosion resistance of metals, particularly stainless steel, by creating a protective oxide layer on their surfaces. This process is crucial in various industries, especially in hydraulic systems, where fittings are subjected to harsh conditions that can lead to significant degradation over time. The formation of this oxide layer helps to mitigate the effects of corrosive elements, ensuring the longevity and reliability of hydraulic fittings.
The Need for Passivation in Hydraulic Fittings
A. Corrosion Prevention
Corrosion is a significant threat to hydraulic systems, leading to premature failure and costly repairs. In hydraulic applications, common types of corrosion include:
Galvanic Corrosion: Occurs when two dissimilar metals are in electrical contact in the presence of an electrolyte, causing one metal to corrode faster than the other. This is particularly relevant in hydraulic systems that utilize multiple metal components.
Pitting Corrosion: Characterized by the formation of small pits or holes on the metal surface. This localized corrosion can be extremely damaging, as it often goes unnoticed until significant material loss has occurred.
Crevice Corrosion: Develops in confined spaces where stagnant fluid can become trapped, leading to the depletion of oxygen and creating a corrosive environment. This type of corrosion is prevalent in fittings and joints.
Uniform Corrosion: Affects the entire surface area of the metal evenly. While it may seem less severe initially, uniform corrosion can compromise structural integrity over time.
The impact of corrosion on hydraulic systems is profound. It can lead to leaks, reduced efficiency, and even catastrophic failures, which pose safety risks and disrupt operations. Regular passivation treatment is essential to prevent these issues, ensuring that hydraulic fittings maintain their integrity under challenging conditions.
B. Enhancing Durability and Performance
Passivation significantly enhances the durability and performance of hydraulic fittings.
Longevity of Fittings: By creating a protective oxide layer, passivation extends the lifespan of hydraulic components. This protective barrier helps resist environmental factors such as moisture and chemicals, reducing wear and tear. For example, properly passivated stainless steel fittings can last significantly longer than untreated components, leading to fewer replacements and reduced downtime.
Cost Implications of Corrosion: The financial implications of corrosion are substantial. Repairing or replacing corroded fittings incurs direct costs, including labor and materials, as well as indirect costs such as downtime and potential safety hazards. Investing in passivation not only protects the fittings but also leads to cost savings over time by minimizing maintenance and replacement needs.
C. Compliance with Industry Standards
Compliance with industry standards is critical for hydraulic fitting manufacturers.
Regulatory Requirements: Various industries are subject to strict regulations regarding material performance and safety. For example, aerospace and automotive sectors often require fittings to meet specific passivation standards to ensure reliability and safety. Non-compliance can result in costly fines and damage to a company’s reputation.
Quality Assurance in Manufacturing: Passivation is often part of a broader quality assurance process in manufacturing. By adhering to recognized standards for passivation, manufacturers demonstrate their commitment to producing high-quality, reliable components. This not only enhances customer trust but also opens opportunities for contracts that require compliance with stringent industry specifications.
Types of Passivation Methods
A. Nitric Acid Passivation
Process Overview
Nitric acid passivation involves immersing stainless steel components in a nitric acid solution, typically with a concentration of around 20-30%. The process aims to remove free iron and other contaminants from the metal surface, followed by the formation of a protective oxide layer. The solution is often heated to enhance the passivation reaction, which usually takes 30 minutes to several hours, depending on the thickness of the oxide layer desired.
Advantages:
Effective Corrosion Resistance: Nitric acid passivation is highly effective in creating a stable and uniform oxide layer that significantly improves corrosion resistance.
Standardization: This method is widely recognized and accepted in many industries, making it easier to comply with existing regulations and specifications.
Disadvantages:
Environmental Concerns: Nitric acid is a hazardous material that requires careful handling and disposal, posing environmental risks.
Surface Finish Impact: The process can lead to a dull surface finish, which may not be desirable for aesthetic applications.
Cost and Complexity: The need for controlled environments and specialized equipment can increase operational costs.
B. Citric Acid Passivation
Process Overview
Citric acid passivation employs a citric acid solution, usually in concentrations ranging from 4-10%, to remove contaminants from stainless steel surfaces. The process typically occurs at ambient temperatures and can be completed more quickly than nitric acid methods, often within 15 to 30 minutes. The citric acid reacts with free iron and other surface impurities, promoting the formation of a protective oxide layer.
Advantages:
Environmentally Friendly: Citric acid is biodegradable and non-toxic, making it a safer alternative to nitric acid for both operators and the environment.
Enhanced Aesthetics: The process often results in a brighter and more polished surface, appealing for applications where appearance matters.
Lower Costs: Generally, citric acid passivation is less expensive to implement due to simpler equipment and lower handling risks.
Disadvantages:
Effectiveness Variability: While effective for most applications, citric acid passivation may not be as universally effective as nitric acid for certain aggressive environments.
Shorter Duration of Protection: The oxide layer formed may not be as robust as that from nitric acid, requiring careful consideration for high-stress applications.
C. Comparison of Methods
When evaluating passivation methods, it is crucial to consider various factors, including environmental impact, effectiveness, and application suitability.
Environmental Impact
Nitric acid presents significant environmental challenges, including hazardous waste management and air pollution concerns due to fumes. Conversely, citric acid is a more sustainable choice, as it is derived from natural sources and poses minimal environmental risks.
Effectiveness and Application Suitability
Effectiveness: Nitric acid passivation is often preferred in applications where high corrosion resistance is critical, such as aerospace and food processing. In contrast, citric acid passivation is gaining popularity for general-purpose applications, particularly in industries focused on sustainability.
Application Suitability: The choice between these methods may also depend on specific operational requirements. For instance, if a bright finish is essential for aesthetic appeal, citric acid might be favored. On the other hand, for components exposed to harsh chemicals or extreme environments, nitric acid may be the better choice.
The Passivation Process
A. Preparation of Fittings
The preparation of fittings is a critical first step in the passivation process, ensuring that the metal surfaces are free from contaminants that could compromise the effectiveness of the treatment.
Cleaning Procedures
Before passivation, fittings must be thoroughly cleaned to remove oils, grease, dirt, and other contaminants. Common cleaning methods include:
Ultrasonic Cleaning: This method utilizes high-frequency sound waves in a liquid cleaning solution to remove impurities from the surface of the fittings. It is effective for complex geometries and intricate designs.
Chemical Cleaning: Solvent-based cleaners or alkaline solutions can be applied to remove oils and other residues. This often involves soaking the fittings in the cleaning solution or applying it through a spray.
Mechanical Cleaning: Techniques such as sandblasting or wire brushing can be used for heavier contaminants, particularly for older or heavily tarnished fittings. However, care must be taken to avoid damaging the metal surface.
Surface Preparation Techniques
After cleaning, further surface preparation may involve:
Rinsing: Thorough rinsing with deionized water ensures that no cleaning residues remain on the fittings.
Drying: Air drying or using heated drying methods can help eliminate moisture, which is crucial before the passivation treatment.
Inspection: A final inspection of the cleaned surfaces can help identify any residual contaminants or damage that may need addressing before proceeding.
B. Passivation Treatment
Once the fittings are adequately prepared, the next step is the passivation treatment itself.
Chemical Solutions Used
The choice of chemical solution depends on the passivation method selected. For nitric acid passivation, a solution typically contains 20-30% nitric acid. For citric acid passivation, a solution with 4-10% citric acid is used. Both solutions may also include additional chemicals to enhance effectiveness, such as surfactants to improve wetting and removal of contaminants.
Treatment Durations and Temperatures
The effectiveness of passivation is influenced by both treatment duration and temperature:
Duration: Nitric acid treatments generally last from 30 minutes to several hours, while citric acid treatments can be completed in as little as 15-30 minutes. The specific duration may vary based on the desired thickness of the oxide layer and the condition of the fittings.
Temperature: Passivation treatments can be performed at room temperature, but heating the solution can accelerate the chemical reactions involved. For nitric acid treatments, heating to around 60-80°C can enhance efficacy. Citric acid solutions are often effective at ambient temperatures, making them more user-friendly.
C. Post-Treatment Inspection and Testing
Following the passivation treatment, it is essential to conduct thorough inspection and testing to ensure the success of the process.
Methods of Assessment
Several methods can be employed to assess the effectiveness of passivation:
Visual Inspection: A straightforward method to check for any visible defects, such as discoloration or surface roughness, indicating inadequate passivation.
Copper Sulfate Test: This qualitative test assesses the effectiveness of passivation by applying a copper sulfate solution to the metal surface. If copper deposits form, it indicates that free iron is present and passivation has not been successful.
Salt Spray Test: A more rigorous quantitative assessment that subjects the passivated fittings to a controlled salt fog environment. The duration until corrosion appears on the surface indicates the corrosion resistance achieved.
Importance of Verification
Verification is a critical aspect of the passivation process. It ensures that the fittings meet the required corrosion resistance specifications and perform reliably in their intended applications. In industries with stringent quality standards, such as aerospace or pharmaceuticals, proper documentation of passivation results is essential for regulatory compliance and quality assurance.
In summary, the passivation process involves meticulous preparation, careful treatment, and thorough post-treatment inspection. By following these steps, manufacturers can effectively enhance the corrosion resistance of hydraulic fittings, ensuring their performance and longevity in demanding applications.
Best Practices for Passivation in Hydraulic Fittings
A. Selecting the Right Method for Specific Applications
Choosing the appropriate passivation method is crucial for ensuring the long-term performance and reliability of hydraulic fittings. Several factors should be considered when making this decision:
Material Type: The base material of the fittings plays a significant role in determining the suitable passivation method. For instance, stainless steels with high chromium content may benefit more from nitric acid passivation due to its ability to create a dense oxide layer. In contrast, citric acid passivation can be effective for lower alloy grades or where a more environmentally friendly approach is desired.
Operating Environment: Consider the conditions under which the hydraulic fittings will operate. If the fittings are exposed to harsh chemicals, elevated temperatures, or extreme pressure, nitric acid passivation may provide better corrosion resistance. Conversely, for general-purpose applications, citric acid passivation may suffice.
Aesthetic Requirements: For applications where appearance is important, such as in visible installations or decorative fittings, citric acid passivation is often preferred due to the brighter finish it imparts.
Regulatory Compliance: Depending on the industry, specific standards may dictate the choice of passivation method. Aerospace and medical industries, for example, often have stringent requirements that necessitate using certain methods or certifications.
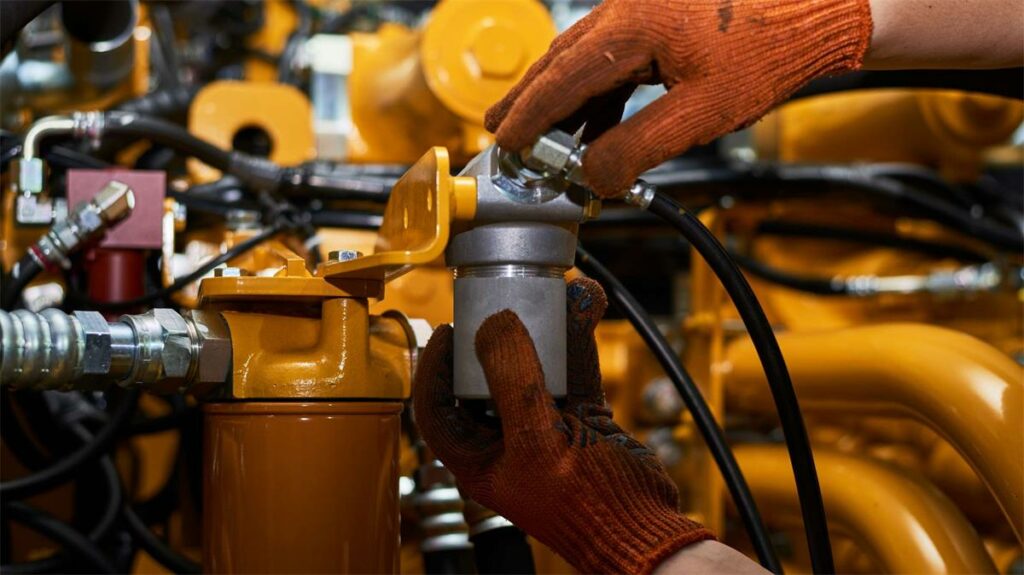
B. Quality Control Measures
Implementing robust quality control measures throughout the passivation process is vital for ensuring consistent results. Key practices include:
Standard Operating Procedures (SOPs): Establishing clear SOPs for the cleaning and passivation processes helps standardize practices and minimizes variability. This includes detailed instructions for cleaning methods, chemical concentrations, treatment times, and temperatures.
Regular Calibration of Equipment: Equipment used for cleaning and passivation, such as ultrasonic cleaners and temperature controls, should be regularly calibrated to ensure optimal performance. Regular maintenance checks can help identify potential issues before they affect the process.
Documentation and Traceability: Keeping thorough records of each passivation batch, including the materials used, treatment times, and inspection results, enhances traceability and accountability. This documentation is essential for audits and compliance with industry regulations.
Training Personnel: Ensuring that all personnel involved in the passivation process are adequately trained in the techniques and safety protocols minimizes the risk of errors. Regular training sessions and updates on best practices can help maintain high standards.
C. Maintenance and Monitoring After Passivation
Post-passivation maintenance and monitoring are essential for preserving the effectiveness of the protective oxide layer and ensuring the continued performance of hydraulic fittings. Best practices include:
Regular Inspections: Implement a schedule for routine inspections of hydraulic fittings to check for signs of corrosion, wear, or damage. Early detection of issues can prevent more significant problems down the line.
Environmental Controls: Monitor the operating environment of hydraulic systems to ensure conditions remain within specified limits. Factors such as temperature, humidity, and exposure to corrosive agents should be controlled to minimize the risk of corrosion.
Preventive Maintenance: Develop a preventive maintenance program that includes cleaning and re-passivating fittings as necessary, particularly in aggressive environments. This approach helps extend the lifespan of components and maintain their integrity.
Common Challenges and Solutions
A. Issues in the Passivation Process
The passivation process, while essential for enhancing the corrosion resistance of hydraulic fittings, can present several challenges that manufacturers must address.
Incomplete Passivation
One of the most significant issues is incomplete passivation, which can occur due to insufficient cleaning, improper treatment times, or inadequate chemical concentrations. When the surface contaminants are not entirely removed or the treatment conditions are not optimal, the protective oxide layer may fail to form correctly, leaving the fittings vulnerable to corrosion.
Environmental Factors
Environmental factors can also affect the passivation process. High humidity, temperature fluctuations, and contamination from airborne particles can impede the formation of the oxide layer. For instance, moisture on the fittings during passivation can lead to uneven treatment results, while dust or grease can interfere with the cleaning process, resulting in inadequate passivation.
B. Troubleshooting Strategies
To effectively address these challenges, manufacturers should implement troubleshooting strategies aimed at identifying and rectifying issues promptly.
Identifying Problems
Visual Inspections: Regularly conduct visual inspections of passivated fittings to identify signs of incomplete passivation, such as pitting, discoloration, or corrosion spots. These early warning signs can help diagnose issues before they escalate.
Testing Methods: Utilize qualitative tests, such as the copper sulfate test or salt spray test, to assess the effectiveness of passivation. Poor performance in these tests can indicate problems with the passivation process.
Process Audits: Regularly audit the cleaning and passivation processes to identify deviations from established procedures. This includes reviewing chemical concentrations, treatment times, and environmental conditions to ensure compliance with standard operating procedures.
Effective Solutions
Enhanced Cleaning Protocols: To combat incomplete passivation, ensure that cleaning protocols are robust and thoroughly followed. Implementing ultrasonic cleaning or adopting multi-stage cleaning processes can improve surface cleanliness, ensuring that contaminants do not hinder passivation.
Optimizing Treatment Conditions: Review and optimize treatment conditions by adjusting chemical concentrations, temperatures, and durations based on material specifications and environmental factors. Continuous monitoring and adjustment can enhance the efficacy of the passivation process.
Controlling Environmental Conditions: Establish controls for the environment where passivation occurs. Maintaining stable temperatures and humidity levels, as well as ensuring a clean workspace, can significantly improve outcomes.
Conclusion
As we move forward, it is important for industry professionals to engage in discussions about best practices, share experiences, and explore innovations in passivation. For those looking to deepen their knowledge or seek guidance on specific applications, I encourage you to reach out for further inquiry.
FAQ
What is passivation?
Passivation is a chemical treatment process that enhances the corrosion resistance of metals, particularly stainless steel, by removing surface contaminants and forming a protective oxide layer.
Why is passivation important for hydraulic fittings?
Passivation is crucial for hydraulic fittings as it prevents corrosion, extends the lifespan of components, and ensures the reliable performance of hydraulic systems under demanding conditions.
What are the common methods of passivation?
The two most common methods are nitric acid passivation and citric acid passivation. Nitric acid is effective for high corrosion resistance, while citric acid is more environmentally friendly and suitable for general applications.
How long does the passivation process take?
The duration of the passivation process varies; nitric acid treatments typically take 30 minutes to several hours, while citric acid treatments can be completed in 15 to 30 minutes.
What factors can affect the effectiveness of passivation?
Factors such as surface cleanliness, treatment time, chemical concentration, and environmental conditions (e.g., humidity and temperature) can all impact the success of the passivation process.
How can I ensure my hydraulic fittings are properly passivated?
Regular inspections, testing methods like the copper sulfate test, and adherence to established cleaning and passivation protocols