Valves play a crucial role in fluid control systems, acting as the gatekeepers of flow. Whether in industrial machinery, residential plumbing, or complex hydraulic systems, valves are essential for regulating the movement of liquids, gases, and other fluids. Their importance cannot be overstated, as they ensure that systems operate smoothly, safely, and efficiently. From controlling water in a municipal supply to managing fuel in an oil refinery, valves are integral to maintaining fluid pressure, preventing backflow, and ensuring proper distribution across a wide range of applications.
What Is a Ball Valve?
A ball valve is a type of quarter-turn valve that uses a spherical ball with a hole or port drilled through its center to control the flow of fluids, gases, or other media through a pipeline. The valve opens or closes as the ball rotates 90 degrees (a quarter turn) within the valve body, allowing for quick shut-off or flow initiation. This simple yet effective design makes ball valves a popular choice for applications requiring reliable isolation of flow with minimal effort. Ball valves are known for their durability, leak-proof performance, and ability to handle high pressures and temperatures, making them suitable for use in a wide variety of industries such as oil and gas, chemical processing, water management, and more.
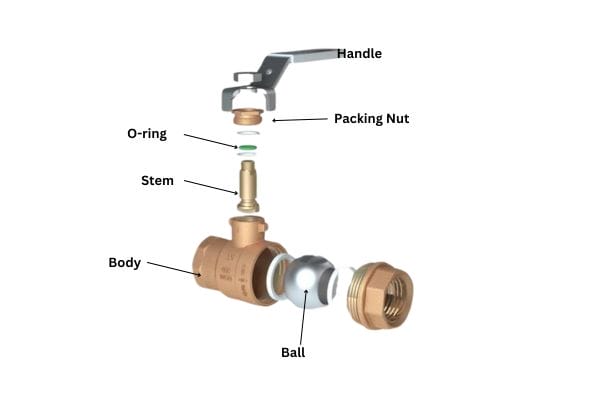
Design and Structure
Ball valves are designed with a few key components that work together to control fluid flow:
Ball: The spherical component of the valve, typically made from metal or plastic, has a hole (called a port) through its center. When the port is aligned with the valve’s inlet and outlet, fluid flows through; when rotated 90 degrees, the flow is blocked.
Handle: The handle or lever is connected to the ball and allows the operator to manually rotate the ball within the valve body. The quarter-turn motion of the handle opens or closes the valve.
Body: The main outer casing that houses the ball and other internal components. The body is designed to withstand pressure and prevent leaks.
Seals: Typically made of materials like rubber, PTFE, or other elastomers, the seals ensure that the valve is leak-proof when closed by creating a tight seal around the ball.
How It Works
The working mechanism of a ball valve is straightforward:
Open Position: When the ball is rotated so that the port (hole) aligns with the pipeline, fluid is allowed to flow freely through the valve.
Closed Position: By turning the handle 90 degrees, the ball rotates to block the flow. In this position, the solid side of the ball prevents fluid from passing through the valve, effectively sealing the line.
Intermediate Position (Throttle Control): While ball valves are generally not designed for flow regulation, some applications may involve positioning the ball partially open to throttle or control flow. However, this can lead to increased wear and tear.
Types of Ball Valves Based on Design
Ball valves come in different designs, each optimized for specific uses and environments. Here are the main types based on design:
Floating Ball Valve:
In a floating ball valve, the ball is not rigidly connected to the valve stem. Instead, it is held in place by the compression of two elastomeric seats on either side of the ball. This design allows the ball to “float” slightly, meaning that when pressure is applied, the ball pushes against the downstream seat, creating a tight seal.
Applications: Commonly used in low- to medium-pressure systems, floating ball valves are suitable for water, air, oil, and gas applications.
Trunnion-Mounted Ball Valve:
In a trunnion-mounted design, the ball is supported by additional mechanical anchoring at both the top and bottom. This design reduces the torque required to operate the valve, making it ideal for larger or high-pressure applications.
Applications: Trunnion-mounted ball valves are frequently used in high-pressure systems and larger pipe diameters, such as in oil and gas pipelines.
Full-Port vs. Reduced-Port Ball Valves:
Full-Port Ball Valve: The port (opening) in the ball is the same size as the pipeline, meaning there is no restriction in flow when the valve is open. Full-port ball valves are preferred for applications where maintaining maximum flow is critical, such as in slurry or viscous fluids.
Reduced-Port Ball Valve: In reduced-port ball valves, the port is smaller than the pipeline. This creates some flow restrictions, but the design is more compact and typically less expensive. Reduced-port valves are suitable for systems where a slight reduction in flow is acceptable.
Key Features of a Ball Valve
Ball valves are widely used in various industries due to their distinct features that make them reliable and efficient for fluid control. Here, we explore the key features that set ball valves apart from other valve types and why they are a preferred choice for both high-pressure and general-purpose applications.
Durability
One of the standout features of ball valves is their durability. These valves are made from robust materials such as stainless steel, brass, or plastic, each suited for specific environments and applications. For instance:
Stainless Steel: Known for its excellent corrosion resistance and strength, stainless steel ball valves are ideal for harsh industrial environments, such as chemical plants and oil refineries, where exposure to corrosive fluids and extreme temperatures is common.
Brass: Brass ball valves are typically used in plumbing, water systems, and low-pressure applications due to their affordability and good corrosion resistance in non-corrosive fluids.
Plastic (PVC, CPVC): These ball valves are lightweight, resistant to chemical corrosion, and often used in chemical processing, water treatment, and food and beverage industries.
Regardless of the material, ball valves are designed to withstand tough conditions, providing a long service life and requiring minimal maintenance over time. The simple design, fewer moving parts, and use of high-quality materials help prevent wear and tear, making ball valves a cost-effective choice in the long run.
Tight Sealing
Ball valves are renowned for their leak-proof sealing capabilities, even in high-pressure systems. The ball within the valve rotates to open or close the flow, creating a tight seal between the ball and the seats (usually made of materials like PTFE or other elastomers). This design ensures there is minimal or no leakage, even under extreme pressures or temperature fluctuations.
The tight seal provided by ball valves makes them suitable for critical applications where even a small leak could lead to costly consequences or safety hazards, such as in:
Oil and gas pipelines: Preventing leakage in high-pressure fluid transmission systems.
Chemical processing: Ensuring the safe handling of hazardous or reactive chemicals.
Water supply systems: Maintaining the integrity of water distribution networks.
This feature is especially important in zero-leakage applications, where reliability is a top priority. The self-cleaning motion of the ball (rotating during operation) also helps reduce the buildup of particles that could potentially compromise the seal.
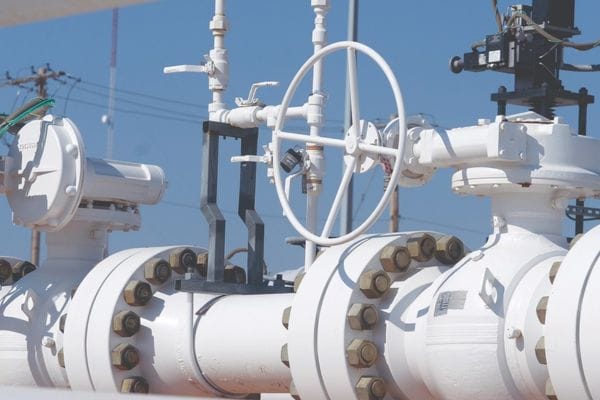
Low Torque Requirement
Another key feature of ball valves is the low torque requirement, which refers to the minimal effort needed to turn the valve handle and operate the valve. Ball valves require a quarter-turn (90-degree rotation) to go from fully open to fully closed, making them quick and easy to operate compared to other types of valves, like gate or globe valves that require multiple turns to fully open or close.
This low torque requirement reduces operator fatigue in manual systems and allows for the integration of automated systems, such as electric or pneumatic actuators. In large-scale industrial settings, the ability to automate ball valve operations with minimal power input can significantly improve efficiency and reduce costs. Moreover, in systems where valves must be frequently opened and closed, the low operational effort of ball valves is a practical advantage.
Quick Operation
Quick shut-off and opening is a major advantages of ball valves. Due to their quarter-turn design, they can instantly stop or allow fluid flow, making them highly efficient for applications where rapid response is required. This quick operation is critical in situations where immediate isolation of flow is needed to prevent accidents, damage, or contamination.
Some common scenarios where quick operation is vital include:
Emergency shut-offs: In industrial systems where fluid flow must be stopped immediately to prevent system failure or safety incidents.
Flow regulation in pipelines: In processes where timing is crucial, such as in chemical mixing or fuel distribution.
Ball valves’ swift action provides a reliable solution in both manual and automated systems, where time-sensitive control is necessary.
Versatility
One of the reasons ball valves are so widely used across industries is their versatility. These valves can handle a wide range of fluids, including liquids, gases, steam, and even slurries. This makes ball valves suitable for a broad spectrum of applications, from residential plumbing to industrial processing.
Key points of versatility include:
Handling Different Fluids: Ball valves can manage various types of media—water, oil, gas, chemicals, or even steam—without compromising performance.
Temperature and Pressure Ranges: They can withstand high pressures and extreme temperatures, depending on the material used in the valve body and seals.
Industrial Applications: In sectors like oil and gas, power generation, water treatment, chemical processing, food and beverage, and more, ball valves are valued for their adaptability.
This versatility allows operators to use ball valves in a variety of environments, ensuring reliable performance in both high-demand and everyday applications.
Compact and Lightweight
Ball valves are often compact and lightweight, making them ideal for installations where space is limited or weight is a consideration. This is particularly beneficial in industries like automotive, aerospace, or small-scale machinery where larger, heavier valves would be impractical.
Compact Design: The streamlined design of ball valves allows them to fit easily into tight spaces or systems where minimal disruption to flow is required. This compactness is especially useful in multi-valve systems, where space is at a premium.
Lightweight Construction: Plastic and certain metal ball valves offer the benefit of being lightweight while still maintaining high performance. This feature is particularly important in applications where weight is a key factor, such as in mobile equipment or piping systems that need to be flexible or portable.
How to Select the Right Ball Valve for Your Application
Choosing the right ball valve for your system involves several key considerations to ensure optimal performance and longevity. Ball valves are used in a wide range of applications, from simple residential plumbing to complex industrial systems, and selecting the appropriate valve depends on factors like pressure, temperature, fluid type, and system design.
Key Considerations
Pressure Rating
The pressure rating of a ball valve refers to the maximum pressure it can withstand without failure. This is critical in applications where high pressure is involved, such as in oil and gas pipelines or industrial fluid systems. Be sure to choose a valve that can handle the maximum pressure of your system. Valves made from materials like stainless steel are often preferred for high-pressure applications due to their strength and durability.
Temperature Compatibility
The temperature of the fluid in your system plays a significant role in determining the right ball valve. For example, if your system handles extremely hot or cold fluids, you will need to select a valve made from materials that can withstand these conditions without losing integrity. Stainless steel or brass valves are typically used for high-temperature applications, while plastic valves (such as PVC) are better suited for lower temperature ranges.
Material Selection (Based on Media and Environment)
The material of the ball valve must be compatible with the media flowing through it to avoid corrosion, degradation, or contamination. Common materials include:
Stainless Steel: Best for corrosive environments or high-pressure applications.
Brass: Suitable for water, air, and non-corrosive fluids.
Plastic (PVC, CPVC): Ideal for chemical processing or water treatment in low-pressure systems.
Consider the working environment—if the valve is exposed to corrosive chemicals, saltwater, or extreme temperatures, material selection becomes even more critical.
Port Size and Design (Full Port vs. Reduced Port)
Full Port: The internal diameter of the valve matches the diameter of the pipe, ensuring maximum flow with no restriction. Full-port ball valves are ideal for applications requiring minimal pressure loss or where maintaining high flow rates is essential.
Reduced Port: The valve’s internal diameter is smaller than the pipe, which restricts flow slightly. Reduced-port valves are more compact and less expensive, making them suitable for systems where some reduction in flow is acceptable.
The choice between full port and reduced port depends on your system’s flow requirements and the type of media being handled.
End Connections (Threaded, Welded, Flanged)
Threaded: Common for small-diameter valves and systems where ease of assembly and disassembly is required. Suitable for low- to medium-pressure systems.
Welded: Provides a permanent, leak-proof connection, often used in high-pressure applications.
Flanged: Offers secure connections in high-pressure systems and allows for easy maintenance and removal. Commonly used in industrial applications.
The selection of end connections depends on your system’s assembly needs and whether disassembly for maintenance is required.
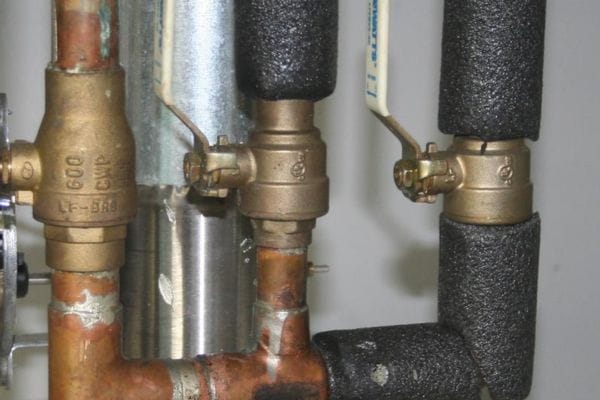
Tips for Matching the Right Ball Valve to Your System
Fluid Type
The nature of the fluid in your system is one of the most important factors when selecting a ball valve. For example, chemical compatibility is crucial in chemical processing systems to prevent corrosion. In the case of water or air systems, brass or PVC valves may suffice, while oil and gas applications typically require high-strength stainless steel valves.
Operational Frequency
Consider how often the valve will be operated. If the valve is part of a frequently used system, such as in industrial processes, it’s essential to choose a ball valve that offers smooth, low-torque operation and can withstand wear from frequent use. Automated or actuated valves may also be preferable for applications requiring frequent or remote operation.
Space Constraints
The installation space available can dictate the type and size of the ball valve you need. Compact or lightweight ball valves are ideal for systems with limited space, such as in mobile equipment or tight machinery setups. A three-piece valve might also be preferred in systems where easy maintenance is required without the need to remove the entire valve from the pipeline.
Conclusion
For those looking to explore ball valves further or seeking expert guidance on choosing the right one, feel free to reach out to us. We are here to help with any inquiries, offer advice on product selection, and provide top-quality solutions to meet your fluid control needs. Contact us today to learn more about how ball valves can enhance your systems!
FAQ
What is a ball valve?
A ball valve is a type of valve that controls the flow of fluid using a rotating ball with a hole through the center. It operates with a quarter-turn motion to open or close the valve.
What are the main materials used for ball valves?
Ball valves are typically made from materials such as stainless steel, brass, or plastic (PVC/CPVC), depending on the application and the fluids they handle.
What’s the difference between full-port and reduced-port ball valves?
A full-port ball valve has a larger port size that matches the pipeline, allowing for maximum flow. A reduced-port valve has a smaller port, restricting the flow slightly.
Can ball valves handle high pressure?
Yes, ball valves are designed to handle high-pressure systems, especially those made from durable materials like stainless steel.
Are ball valves suitable for controlling flow?
While ball valves are primarily used for on/off control, some specialized types like V-port ball valves can regulate flow with more precision.
How do I choose the right ball valve for my application?
Consider the fluid type, pressure and temperature ratings, material compatibility, port size, and required end connections to ensure the right match for your system.