Hydraulic couplers are essential components in a wide range of industries, including agriculture, construction, and manufacturing. These industries depend heavily on hydraulic systems for their efficiency and productivity. However, when these couplers become difficult to connect, it doesn’t just create a minor inconvenience—it can lead to significant downtime, increased operational costs, and even potential safety hazards. Understanding why hydraulic couplers sometimes refuse to connect is not just a matter of convenience; it’s critical to maintaining the smooth operation of your equipment and ensuring the success of your projects.
Understanding Hydraulic Couplers
A. Definition and Function
Hydraulic quick couplers are specialized connectors used to quickly and efficiently connect and disconnect hydraulic lines in various applications. These small but essential components serve as the interface between different sections of a hydraulic system, allowing for the transfer of fluid power from one part of the system to another. Hydraulic couplers are designed to maintain a secure and leak-free connection, ensuring that hydraulic fluid flows smoothly between hoses, pumps, cylinders, and other components. Their primary function is to enable quick changes in equipment or tools without the need for extensive downtime, making them invaluable in industries where efficiency and speed are paramount.
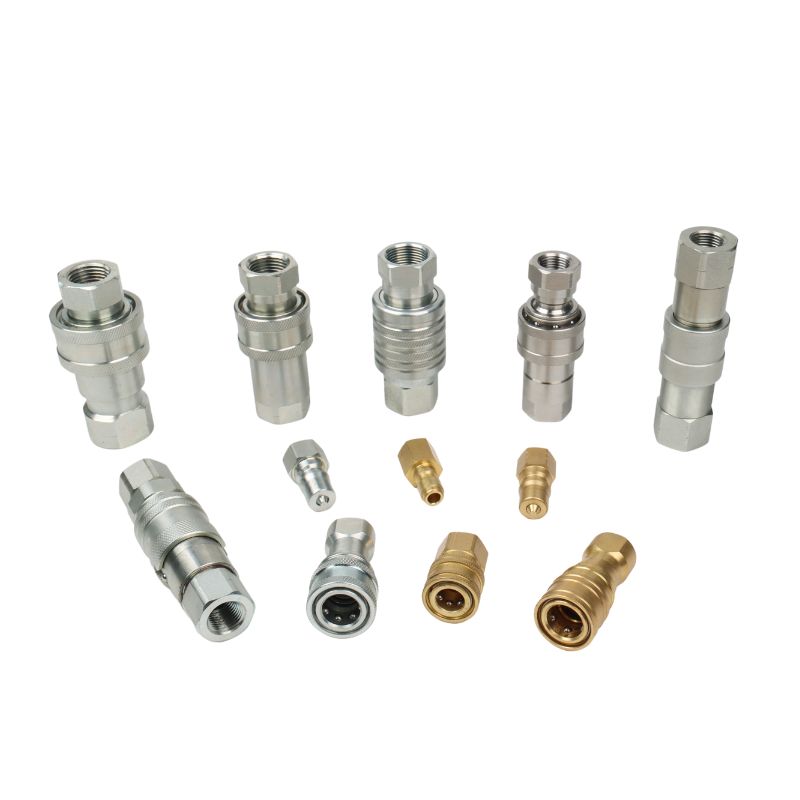
B. Types of Hydraulic Couplers
There are several types of hydraulic couplers, each designed for specific applications and operating conditions.
Flat Face Couplers:
Flat face couplers are known for their easy cleaning and reduced fluid loss during connection and disconnection. They are commonly used in applications where cleanliness is crucial, such as in construction and agricultural machinery. Their flat surface design minimizes the risk of contamination and makes them ideal for environments where dirt and debris are prevalent.
Poppet Couplers:
Poppet couplers feature a poppet valve that opens to allow fluid flow when connected. They are widely used in high-pressure applications and are valued for their durability and ability to maintain a tight seal under demanding conditions. Poppet couplers are often found in hydraulic circuits that require quick and reliable connections, such as in industrial machinery and mobile equipment.
Screw-to-Connect Couplers:
Screw-to-connect couplers offer a more secure connection through a threaded design. This type of coupler is ideal for applications where vibration or movement could cause a standard coupler to disconnect. The screw mechanism ensures a firm and stable connection, making these couplers suitable for heavy-duty applications such as oil and gas drilling, mining, and other high-pressure environments.
Each type of hydraulic coupler is designed to meet specific requirements, and selecting the right one is essential for ensuring optimal performance and longevity of the hydraulic system.
C. Importance of Proper Connection
A proper connection in hydraulic systems is not just a matter of convenience; it is critical for both system efficiency and safety. An improperly connected coupler can lead to leaks, pressure drops, and even complete system failure, which can have serious consequences, especially in high-stakes environments like construction sites or manufacturing plants. Leaks caused by faulty connections can result in wasted hydraulic fluid, increased operational costs, and environmental hazards. Moreover, inadequate connections can compromise the safety of the equipment operators, as unexpected disconnections or pressure bursts can lead to accidents and injuries.
Ensuring a proper connection involves not only choosing the right type of coupler but also regular maintenance and inspection to prevent issues such as wear, contamination, and misalignment. By understanding the role and function of hydraulic couplers, as well as the importance of maintaining a secure connection, operators can significantly reduce the risk of downtime and enhance the overall efficiency and safety of their hydraulic systems.
Common Reasons for Difficult Connections
A. Pressure Issues
Residual Pressure in the Lines: Residual pressure in hydraulic lines is a common cause of connection difficulties. When the system is turned off, hydraulic fluid can remain pressurized within the lines, especially if the machinery was recently in use or if there’s a lack of adequate pressure relief mechanisms. This residual pressure can prevent the male and female ends of a hydraulic coupler from easily connecting, as the pressurized fluid resists the coupling process. In some cases, the force required to connect the coupler may exceed what can be applied manually, leading to frustration and potential damage to the equipment. To mitigate this issue, it’s important to ensure that the system is properly depressurized before attempting to connect or disconnect couplers. Using manual pressure relief valves or activating the machine’s pressure release function can help alleviate this problem.
Inadequate Pressure Relief: Pressure relief valves are critical components in hydraulic systems, designed to control and manage the pressure within the system by allowing excess pressure to be safely released. When these valves are not functioning correctly, either due to clogging, mechanical failure, or improper adjustment, they fail to relieve pressure, which can make it extremely difficult to connect or disconnect hydraulic couplers. A faulty pressure relief valve can lead to situations where residual pressure remains trapped in the lines, as previously discussed. In addition, an improperly functioning valve can cause pressure spikes during operation, which not only complicates the connection process but also increases the risk of component damage and safety hazards. Regular maintenance and inspection of pressure relief valves are essential to ensure they are working effectively and to prevent such issues.
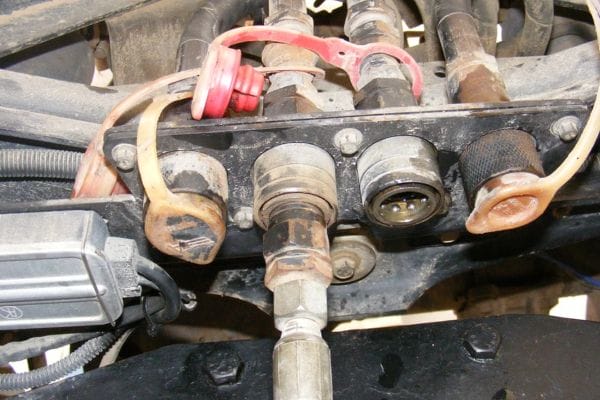
B. Wear and Tear
Degradation of Seals: Hydraulic couplers rely on seals, typically made of rubber or other elastomeric materials, to maintain a tight and leak-proof connection. Over time, these seals can degrade due to factors such as exposure to hydraulic fluid, temperature fluctuations, and mechanical stress. When seals become worn out or damaged, they lose their elasticity and ability to form a proper seal, making it difficult to connect the couplers. Worn seals may also allow air or contaminants to enter the system, further complicating the connection process and leading to potential system inefficiencies. To avoid these issues, it is crucial to inspect seals regularly and replace them at the first signs of wear or damage.
Damage to Coupler Components: The physical components of a hydraulic coupler, such as threads, O-rings, and locking mechanisms, are subject to wear and tear from repeated use. Damage to these components can make connections difficult or impossible. For example, stripped threads can prevent the coupler from securely fastening, while a damaged O-ring might fail to seal properly, leading to leaks. Even minor dents or deformations in the coupler can create alignment issues that hinder the connection process. Routine maintenance checks should include a close examination of all coupler components, and any damaged parts should be repaired or replaced promptly to ensure reliable operation.
C. Contamination
Debris and Dirt: Contamination is a significant issue in hydraulic systems, particularly in environments where dirt, dust, or other debris is prevalent. Particles of dirt can easily find their way into the couplers during connection or disconnection, obstructing the mating surfaces and preventing a proper seal. This not only makes it difficult to connect the couplers but can also lead to leaks and wear over time as the abrasive particles grind against the seals and components. To minimize the risk of contamination, it is important to keep the coupler ends clean and covered when not in use and to inspect them for any debris before making a connection.
Fluid Compatibility Issues: Incompatible hydraulic fluids can also cause problems with coupler connections. Hydraulic systems are designed to work with specific types of fluids, and using the wrong fluid can cause chemical reactions that degrade the seals and internal components of the couplers. For example, a fluid that is too viscous may create excessive resistance during connection, while an incompatible fluid might cause the seals to swell or harden, making it difficult to form a proper connection. Always ensure that the hydraulic fluid being used is compatible with the materials of the coupler and the system as a whole to avoid these issues.
D. Misalignment
Misaligned Hoses or Couplers: Misalignment between hoses or between the male and female parts of a coupler is a common reason for difficult connections. Even slight misalignment can cause the coupler to resist the connection, as the mating surfaces are not properly aligned to engage. This can occur due to improper hose routing, wear on the coupler, or simply due to the angles at which the hoses are being connected. Misalignment can also lead to increased wear and tear on the couplers, exacerbating the problem over time. Ensuring that hoses are properly routed and that the couplers are aligned before attempting to connect can help prevent these issues.
Connector Design Flaws: Certain design flaws in the couplers themselves can contribute to alignment problems. For example, if the coupler is designed with insufficient tolerance for misalignment or if the locking mechanism is overly complex, it may be more difficult to achieve a proper connection. Additionally, some couplers may not be designed to handle the specific pressures or flow rates of the system they are being used in, leading to difficulties in connection. When selecting couplers, it is important to choose designs that are robust and suited to the specific requirements of the application to avoid these potential issues.
E. Incorrect Usage
Over-Tightening or Under-Tightening: The process of tightening hydraulic couplers must be done correctly to ensure a proper connection. Over-tightening can strip threads, crush seals, or even deform the coupler body, making future connections difficult or impossible. Conversely, under-tightening can result in a loose connection that leaks or fails under pressure. Both scenarios not only complicate the connection process but can also lead to premature wear of the coupler and increased maintenance needs. It’s important to follow the manufacturer’s torque specifications and guidelines when tightening couplers to achieve a secure yet not overly tight connection.
Wrong Coupler Type: Using the wrong type of coupler for a specific application is another common issue that can make connections difficult. For instance, a coupler designed for low-pressure systems may not perform well in high-pressure environments, leading to connection issues or even failure. Similarly, using a coupler that is not compatible with the type of hydraulic fluid or the operating environment can result in difficulties during connection. It is essential to choose the correct coupler type based on the application’s requirements, including pressure ratings, fluid compatibility, and environmental conditions, to ensure smooth and reliable connections.
Troubleshooting Connection Problems
A. Step-by-Step Guide
When encountering difficulties with hydraulic coupler connections, following a systematic approach can help identify and resolve the issue efficiently. Here’s a step-by-step troubleshooting guide:
Inspect for Residual Pressure:
Begin by ensuring that the hydraulic system is completely depressurized. Attempt to connect the coupler; if it resists, it may indicate residual pressure in the lines.
If pressure is detected, use the machine’s pressure release function or manually open a pressure relief valve to release any trapped pressure.
Check for Wear and Tear:
Examine the coupler components, including seals, threads, and locking mechanisms, for signs of wear or damage. Look for cracks, flattening, or hardening of seals, and inspect the threads for stripping or deformation.
Replace any worn or damaged components before attempting to reconnect.
Inspect for Contamination:
Clean both the male and female coupler ends to remove any dirt, debris, or other contaminants that could obstruct the connection.
Use a clean cloth or compressed air to clear any particles from the coupler’s mating surfaces.
Ensure Proper Alignment:
Check the alignment of the hoses and couplers. Ensure that both ends are aligned straight and that there is no bending or twisting of the hoses that could cause misalignment.
Adjust the positioning of the hoses if necessary to achieve a proper alignment.
Evaluate Connection Force:
If the coupler still won’t connect, evaluate the amount of force being applied. Hydraulic couplers often require firm pressure, but excessive force can cause damage. If unsure, refer to the manufacturer’s guidelines for the appropriate amount of force to use.
Test the System:
After resolving any identified issues, connect the couplers and test the system under operating conditions. Check for leaks and ensure that the connection remains stable under pressure.
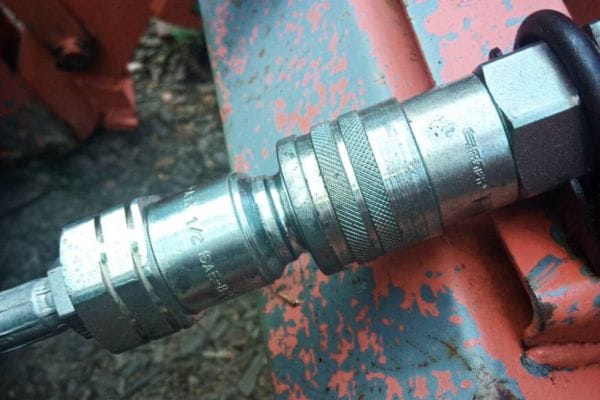
B. Pressure Management Tips
Managing pressure in hydraulic systems is crucial to ensuring smooth and safe connections. Here are some tips to help manage and relieve pressure effectively:
Use Pressure Relief Valves:
Always ensure that the system is equipped with functional pressure relief valves. These valves should be regularly tested to confirm they are operating correctly.
If possible, install additional manual relief valves at strategic points in the system to allow for easier pressure release before making a connection.
Follow Proper Shutdown Procedures:
When shutting down equipment, follow the recommended procedures to ensure that all residual pressure is released from the lines. This often includes cycling the control valves to relieve any remaining pressure.
Check Pressure Gauges:
Regularly monitor pressure gauges to ensure that they reflect accurate pressure levels. Faulty gauges can mislead operators into thinking the system is depressurized when it’s not.
Replace or recalibrate faulty gauges as needed.
Pressure Management During Disconnection:
When disconnecting couplers, release pressure gradually to avoid pressure spikes or fluid blowouts. This can be done by slightly loosening the coupler to allow the pressure to bleed off slowly before fully disconnecting.
C. Maintenance Best Practices
Routine maintenance is key to preventing connection problems caused by wear, contamination, and other issues. Consider these best practices:
Regular Inspection:
Implement a routine inspection schedule to check couplers, seals, and hoses for wear, damage, and contamination. Inspections should be more frequent in harsh operating environments.
Document the findings of each inspection to track wear patterns and predict when replacements will be needed.
Seal Replacement:
Replace seals on a regular basis, even if they don’t show obvious signs of wear. Preventative replacement can prevent unexpected failures and leaks.
Keep spare seals on hand to allow for quick replacements without significant downtime.
Cleanliness Protocols:
Establish cleanliness protocols for handling and storing couplers. This includes wiping down couplers before and after each use and storing them in protective covers when not in use.
Avoid placing couplers directly on the ground or in dirty environments where they can pick up contaminants.
Lubrication:
Periodically lubricate the moving parts of the coupler, such as the locking mechanisms, to ensure smooth operation. Use a lubricant recommended by the manufacturer to avoid compatibility issues with hydraulic fluid.
D. Proper Coupler Handling
Proper handling and storage of hydraulic couplers can significantly extend their lifespan and prevent damage. Here are some best practices:
Use Protective Caps:
Always use protective caps or covers on both ends of the coupler when they are not in use. This prevents debris and moisture from entering the coupler and contaminating the hydraulic fluid.
Avoid Dropping Couplers:
Handle couplers with care, avoiding drops or impacts that could dent or deform the components. Even small deformations can lead to misalignment and connection difficulties.
Store in a Clean, Dry Environment:
Store couplers in a clean, dry location, ideally in a protective case or on a designated rack. Avoid exposure to extreme temperatures, humidity, or direct sunlight, which can degrade seals and other materials over time.
Training and Handling:
Ensure that all personnel who handle hydraulic couplers are properly trained in their use and maintenance. Proper training can prevent many common handling errors that lead to damage and connection issues.
E. Selecting the Right Coupler
Choosing the right coupler for your specific application is critical to avoiding connection issues and ensuring optimal performance. Consider the following factors when selecting a coupler:
Pressure Rating:
Select a coupler with a pressure rating that matches or exceeds the maximum operating pressure of your hydraulic system. Using a coupler with an inadequate pressure rating can lead to failures and safety hazards.
Fluid Compatibility:
Ensure that the coupler materials are compatible with the hydraulic fluid used in your system. Incompatible materials can cause degradation of the coupler components and lead to leaks or failures.
Environmental Considerations:
Consider the operating environment when selecting a coupler. For example, if the system operates in a dirty or corrosive environment, choose a coupler with a robust sealing system and corrosion-resistant materials.
Connection Type:
Choose the connection type that best suits your application. For example, quick-connect couplers are ideal for applications requiring frequent connections and disconnections, while screw-to-connect couplers may be better for high-pressure, high-vibration environments.
Size and Flow Requirements:
Match the size of the coupler to the flow requirements of your hydraulic system. Using a coupler that is too small can restrict flow and reduce system efficiency, while an oversized coupler may be unnecessary and more expensive.
Conclusion
Effectively managing and preventing hydraulic coupler connection issues requires a proactive approach. Regularly inspect your equipment, follow proper procedures for pressure relief, and ensure that you’re using the right type of coupler for your specific application. With attention to detail and consistent maintenance, you can avoid many of the common problems.
FAQ
Why is my hydraulic coupler difficult to connect?
Difficulties in connecting hydraulic couplers can be caused by residual pressure in the lines, wear and tear on the seals or components, contamination, misalignment, or using the wrong type of coupler.
How can I relieve residual pressure in hydraulic lines?
To relieve residual pressure, use the machine’s pressure release function or manually open a pressure relief valve. Ensure the system is completely depressurized before attempting to connect the coupler.
What should I do if my hydraulic coupler is leaking?
A leaking coupler may be due to worn-out seals or damaged components. Inspect the seals replace them if necessary, and check for any damage to the coupler’s threads or O-rings.
How often should I replace the seals in my hydraulic couplers?
Seals should be inspected regularly and replaced at the first signs of wear, cracking, or hardening.
What type of hydraulic coupler should I use for high-pressure applications?
For high-pressure applications, it’s best to use screw-to-connect couplers or other types rated for the specific pressure of your system. These are designed to handle high-pressure conditions securely.
How can I prevent contamination in my hydraulic couplers?
To prevent contamination, always keep the coupler ends clean, use protective caps when they are not in use, and avoid exposing them to dirt and debris during connection and disconnection.