Among the various types of hydraulic hoses, wire-reinforced hydraulic hoses stand out for their enhanced strength and durability. These hoses are constructed with a layer (or multiple layers) of steel wire, embedded between the inner tube and outer cover. This wire reinforcement significantly improves the hose’s ability to withstand high pressures and resist external damage, making them ideal for demanding environments and heavy-duty applications. Whether used in high-pressure hydraulic systems or in conditions where abrasion and extreme temperatures are a concern, wire-reinforced hoses provide the reliability and performance required to keep systems running smoothly and safely.
Construction and Design of Wire-Reinforced Hydraulic Hoses
Materials Used in Construction
Wire reinforced hydraulic hoses are meticulously designed to endure the harsh conditions of high-pressure applications. Their construction involves three primary components: the inner tube, the wire reinforcement layer, and the outer cover. Each of these elements plays a crucial role in the hose’s overall performance and durability.
Inner Tube: The inner tube is typically made from synthetic rubber or thermoplastic materials, chosen for their compatibility with various hydraulic fluids, including oil, water, and synthetic fluids. This layer must be resistant to corrosion and chemical degradation to ensure the longevity and efficiency of the hose.
Wire Reinforcement Layer: This is the defining feature of wire-reinforced hoses. Steel wire, either braided or spirally wound, provides the hose with its strength and pressure resistance. The reinforcement can consist of a single layer, double layer, or even multiple layers of wire, depending on the pressure rating and application needs.
Outer Cover: The outer cover protects the hose from external damage caused by abrasion, weather, and environmental factors. It is usually made of synthetic rubber, polyurethane, or other durable materials that resist wear, UV rays, and harsh environmental conditions.
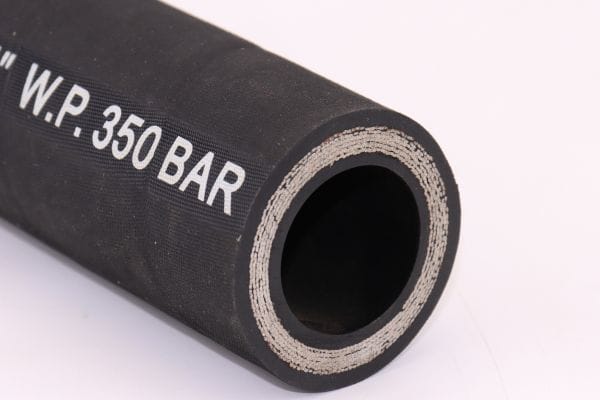
Types of Wire Reinforcement
The wire reinforcement within hydraulic hoses can vary in its configuration, primarily affecting the hose’s flexibility, pressure rating, and durability. The three common types are:
Single-Layer Reinforcement: Single-wire braided hoses are typically used in low to medium pressure applications. They offer flexibility and adequate strength for many standard hydraulic systems, making them suitable for less demanding environments.
Double-Layer Reinforcement: Double-wire braided hoses are designed for medium to high-pressure applications. The additional layer of reinforcement provides increased strength and durability, making these hoses ideal for more demanding industrial and construction equipment.
Multi-Layer Reinforcement: Multi-layer or spiral-wound hoses consist of multiple layers of high-tensile steel wire arranged in a spiral configuration. This type of reinforcement is used for very high-pressure applications where maximum strength and durability are required. They are often found in heavy-duty machinery, such as mining equipment and industrial hydraulic systems.
How Wire Reinforcement Enhances Strength
Wire reinforcement is crucial for enhancing the strength and stability of hydraulic hoses. The steel wire layers act as a structural skeleton, allowing the hose to withstand high internal pressures without collapsing or bursting.
Pressure Resistance: The wire reinforcement prevents the hose from expanding under pressure, enabling it to handle much higher pressures than non-reinforced hoses. This is essential in hydraulic systems where fluid power needs to be efficiently transmitted without compromising the integrity of the hose.
Flexibility: Despite the added strength, wire-reinforced hoses maintain a degree of flexibility, especially those with braided wire reinforcement. This flexibility is vital for applications requiring intricate hose routing without risking kinks or damage.
Braided Wire vs. Spiral Wire Reinforcement:
Braided Wire: Offers better flexibility and is used in applications where bending and movement are common. However, it has a lower pressure capacity compared to spiral reinforcement.
Spiral Wire: Provides superior strength and can withstand much higher pressures, but it is less flexible, making it ideal for stationary or less flexible applications.
Benefits of Wire Reinforced Hydraulic Hoses
Resistance to High Pressure
Wire-reinforced hydraulic hoses are engineered to withstand extreme hydraulic pressures that other types of hoses cannot handle. This capability is primarily due to the hose’s internal structure, which includes one or more layers of high-tensile steel wire reinforcement.
Built for Extreme Pressures: The steel wire reinforcement embedded within the hose’s structure acts as a formidable barrier against pressure surges. This design prevents the hose from expanding or bursting under high pressure, ensuring consistent performance even in the most demanding hydraulic systems. These hoses are suitable for applications with pressure ratings ranging from medium to ultra-high, depending on the number of wire layers and the configuration used.
Durability in Harsh Environments
Wire-reinforced hydraulic hoses are not only strong but also incredibly durable, designed to operate efficiently in harsh and challenging environments. This durability is due to their construction materials and the protective features integrated into their design.
Resistance to Abrasion: The outer cover of wire-reinforced hoses is typically made from materials like synthetic rubber or polyurethane, which offer excellent resistance to abrasion. This means the hose can withstand friction from rough surfaces, sharp edges, and constant movement without significant wear and tear. This is crucial in applications like construction and mining, where hoses are often exposed to abrasive conditions.
Weather and Chemical Resistance: These hoses are also built to resist degradation from environmental factors such as UV rays, ozone, and extreme temperatures. The inner tube material is chosen for its chemical compatibility, ensuring that the hose can transport a wide range of hydraulic fluids without corroding or degrading over time. This makes wire-reinforced hoses suitable for outdoor and industrial environments where exposure to the elements is a concern.
Performance in Heavy-Duty Environments: In industrial and heavy-duty settings, equipment is subjected to rigorous use, and components must endure constant stress. Wire-reinforced hoses can handle these demands due to their robust design. Whether it’s the extreme temperatures of a steel mill or the harsh conditions of an oil rig, these hoses maintain their integrity and performance, reducing the frequency of replacements and maintenance costs.
Flexibility in System Design
Wire-reinforced hoses offer a unique combination of strength and flexibility, making them ideal for complex hydraulic system designs. This flexibility provides significant advantages when routing hoses through machinery or equipment.
Efficient Routing and Installation: Despite their robust construction, wire-reinforced hoses can be bent and routed through tight spaces without compromising their integrity. This flexibility allows for more efficient system design, reducing the number of fittings and connectors needed, which can be potential points of failure. It also simplifies the installation process, saving time and labor costs.
Adaptability to Complex Layouts: In systems with intricate layouts or where space is limited, the ability of wire-reinforced hoses to bend and flex is invaluable. They can be used in applications requiring dynamic movement, such as mobile equipment or robotic arms, without risking kinks or internal damage. This adaptability ensures that the hose performs optimally in both stationary and mobile systems.
Reducing the Need for Multiple Hose Types: Because wire-reinforced hoses can handle a wide range of pressures and environmental conditions, they can often be used in place of multiple specialized hose types. This versatility simplifies inventory management and system maintenance, as fewer hose types need to be stocked and serviced.
Common Applications
Heavy Machinery and Construction
Use in Excavators, Loaders, Cranes, and Other Heavy Machinery
Heavy construction equipment like excavators, loaders, and cranes rely heavily on hydraulic systems to perform tasks such as lifting, digging, and moving heavy loads. These machines operate under high-pressure conditions, and any failure in the hydraulic system could lead to significant safety risks and operational downtime.
Wire-reinforced hoses are ideal for these applications because they can withstand the extreme pressures and constant movement associated with heavy machinery. Their strength and flexibility allow for smooth operation and reduced risk of hose failure, even under the most demanding conditions.
Importance of Wire-Reinforced Hoses in Handling Hydraulic Pressures in Heavy Equipment
Construction machinery often operates in rugged environments where hoses are exposed to abrasion, impact, and extreme temperatures. Wire-reinforced hoses are designed to resist these harsh conditions, maintaining their integrity and performance even under heavy use.
Their ability to handle high pressures ensures that hydraulic systems remain efficient and reliable, crucial for the safe and effective operation of heavy machinery.
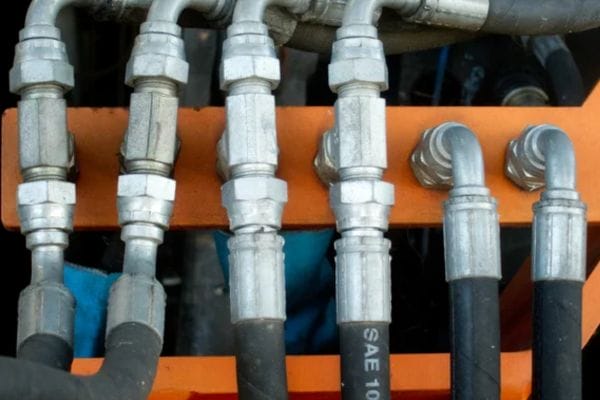
Industrial Manufacturing
Role in Hydraulic Systems within Manufacturing Plants
In manufacturing plants, hydraulic systems are used to power a variety of equipment, including presses, lifts, and conveyor systems. These systems require consistent high pressure to function efficiently, and wire-reinforced hoses are often used to meet these demands.
The strength and durability of these hoses make them suitable for the constant, high-pressure operations typical of manufacturing environments. Their flexibility allows for easy routing through complex machinery setups, reducing the risk of kinks or damage.
High Pressure and Long-Term Use in Industrial Production Lines
Industrial production lines require reliable components that can withstand continuous operation without failure. Wire-reinforced hydraulic hoses are built to endure the long-term high-pressure cycles often found in these environments.
Their resistance to wear, fatigue, and chemical exposure makes them a reliable choice for applications where downtime due to hose failure is not an option. This reliability helps maintain the efficiency and productivity of manufacturing processes.
Agriculture and Forestry Equipment
Application in Tractors, Harvesters, and Other Agricultural Machinery
Agricultural machinery, such as tractors, harvesters, and sprayers, utilize hydraulic systems for various functions, including lifting, steering, and operating attachments. These systems often operate in environments with high levels of dust, dirt, and moisture, which can be detrimental to standard hydraulic hoses.
Wire-reinforced hoses are well-suited for these conditions due to their robust construction and resistance to environmental factors. Their durability ensures that hydraulic systems continue to operate smoothly, even in the harshest agricultural settings.
Importance of Robust Hoses in Dealing with Tough Agricultural Environments
In agriculture, equipment is exposed to frequent movement and vibration, which can cause premature wear in lesser-quality hoses. With their enhanced flexibility and strength, wire-reinforced hoses can absorb these forces without compromising performance.
The ability to withstand extreme conditions, such as exposure to chemicals, fertilizers, and varying temperatures, makes these hoses essential for maintaining the efficiency and reliability of agricultural equipment.
When to Use Wire-Reinforced Hydraulic Hoses
Determining Pressure Requirements
The primary factor in selecting a hydraulic hose is the pressure rating required by the system. Hydraulic systems operate under varying pressure conditions, and hoses must be able to handle these pressures without failure. Wire-reinforced hoses are built to withstand much higher pressures compared to non-reinforced or textile-reinforced hoses.
The pressure capacity of a hose is influenced by the type and number of wire reinforcement layers. For example, a single-wire braided hose can handle medium pressures, while a double-wire braided or multi-spiral hose can endure much higher pressures. It’s essential to match the hose’s pressure rating with the system’s maximum operating pressure to ensure safe and efficient operation.
Operating Environments
Environments with Abrasive Materials, Chemical Exposure, or Extreme Temperatures
Wire-reinforced hydraulic hoses are designed to perform under harsh environmental conditions where other types of hoses may fail. This includes exposure to abrasive materials, chemicals, and extreme temperatures, which can cause premature wear and degradation in standard hoses.
Abrasive Environments: In industries like mining, construction, and quarrying, hoses are often subjected to abrasive conditions. The outer cover of wire-reinforced hoses is made from abrasion-resistant materials, protecting the reinforcement layers from damage and extending the hose’s lifespan.
Chemical Exposure: Many industrial processes involve the transfer of corrosive fluids. The inner tube of wire-reinforced hoses is made from materials compatible with a wide range of chemicals, ensuring that the hose remains intact and functional even under prolonged exposure to aggressive substances.
Extreme Temperatures: Hydraulic systems in extreme temperature environments, such as foundries or cold storage facilities, require hoses that can maintain their integrity and flexibility. Wire-reinforced hoses are built to withstand both high and low temperatures, making them suitable for such demanding conditions.
Why Wire-Reinforced Hoses Are Better Suited for Harsh Conditions
The construction of wire-reinforced hoses provides a higher level of protection against external factors that can compromise hose performance. The multiple layers of wire reinforcement not only increase the hose’s pressure capacity but also add to its structural integrity, making it resistant to external damage.
In environments with frequent movement, impact, or mechanical stress, the durability and strength of wire-reinforced hoses reduce the risk of catastrophic failures. This is particularly important in applications where hose failure could lead to significant safety hazards or operational disruptions.
System Design Complexity
When Flexibility and Easy Routing Are Required in Complex System Designs
Hydraulic systems often need to be routed through confined spaces or around obstacles, requiring hoses that are both strong and flexible. Wire-reinforced hoses, especially those with braided wire reinforcement, offer the necessary flexibility without compromising on strength.
In mobile equipment, robotics, and complex industrial machinery, wire-reinforced hoses can be routed easily around sharp bends and through tight spaces, reducing the need for additional fittings and connections. This not only simplifies system design but also minimizes potential leak points.
Benefits of Using Wire-Reinforced Hoses in Systems with Challenging Layouts
Reduced Installation Time: The flexibility of wire-reinforced hoses allows for easier installation in complex system layouts. This reduces the time and labor costs associated with system setup and maintenance.
Enhanced System Efficiency: Efficient routing of hydraulic hoses minimizes pressure drops and flow restrictions, leading to improved system efficiency. Wire-reinforced hoses enable smooth flow paths, contributing to better overall performance.
Minimized Risk of Damage: The combination of strength and flexibility means that wire-reinforced hoses are less likely to suffer from damage due to improper installation or bending. This is especially important in dynamic applications where the hose is subjected to constant movement.
Maintenance and Inspection Tips
Regular Inspection for Wear and Tear
Common Signs of Damage to Wire-Reinforced Hoses
Abrasion: One of the most common forms of damage in hydraulic hoses is abrasion. This occurs when the hose rubs against other surfaces or components, wearing down the outer cover and potentially exposing the reinforcement layer. Look for scuffed, worn, or frayed areas on the hose’s surface.
Leaks: Leaks are a clear indication of hose damage or connection issues. They can be caused by a puncture, crack, or degradation of the hose material. Signs of leaks include fluid seeping or spraying from the hose, a drop in system pressure, or fluid pooling under the equipment.
Kinks: Kinking can occur if the hose is bent beyond its recommended bend radius, causing internal damage. Kinks restrict fluid flow, increase pressure within the hose, and can lead to rupture or failure. Visual indicators include a flattened or twisted appearance in the hose.
Blisters or Bubbles: These can form on the hose’s outer cover due to delamination or separation between layers, often caused by internal fluid escaping through a damaged inner tube.
Cracks and Cuts: Cracks or cuts in the hose, especially near the fittings, are signs of material fatigue or external damage. These can lead to leaks or complete hose failure if not addressed.
Best Practices for Regularly Inspecting Hoses in High-Pressure Systems
Visual Inspection: Regularly perform a visual inspection of the entire hose assembly, including the fittings. Look for signs of abrasion, leaks, kinks, or any other damage mentioned above.
Feel for Soft Spots: Run your hands along the length of the hose, feeling for any soft or spongy spots, which can indicate internal damage or hose degradation.
Check for Proper Installation: Ensure that hoses are not twisted or kinked and that they are securely attached to the fittings without any visible damage.
Listen for Unusual Noises: If you hear unusual noises like squealing or hissing near the hose, it could be a sign of a pinhole leak or pressure issue.
Pressure Testing: Periodically test the hose’s pressure capacity using a hydraulic test bench to ensure it still meets the required specifications.
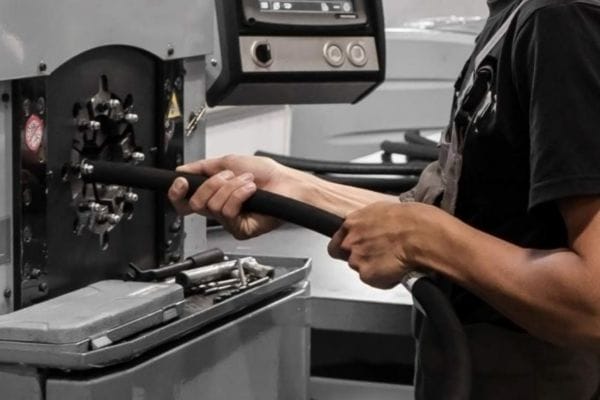
Proper Hose Installation and Routing
Guidelines for Proper Hose Routing to Avoid Premature Wear
Follow the Bend Radius Guidelines: Each hose has a minimum bend radius, which is the tightest curve the hose can handle without damage. Exceeding this limit can lead to kinks, internal damage, and premature failure. Ensure hoses are routed with gentle curves that respect the bend radius.
Avoid Twisting the Hose: Twisting can weaken the hose structure and cause it to fail under pressure. During installation, make sure that the hose is not twisted. Use swivel fittings or adapters if the hose needs to move or rotate.
Secure Hoses with Clamps or Ties: Use appropriate clamps or ties to secure hoses and prevent excessive movement, vibration, or contact with other surfaces. This reduces the risk of abrasion and wear.
Avoid Contact with Sharp Edges: Route hoses away from sharp edges or corners that could cut or abrade the hose cover. Use protective sleeves or guards where contact cannot be avoided.
Consider Environmental Factors: Protect hoses from direct exposure to sunlight, extreme heat, or chemicals that could degrade the hose material. Use covers or shields where necessary.
How Improper Installation Can Reduce Hose Lifespan
Improper installation, such as incorrect bend radius, twisting, or inadequate securing, can lead to a multitude of issues, including premature wear, kinking, and reduced pressure capacity. This not only shortens the hose lifespan but also increases the risk of sudden failure, potentially causing safety hazards and operational downtime.
Replacement Intervals
Heavy-Duty and High-Pressure Applications: For hoses used in high-pressure or heavy-duty environments, a more frequent replacement schedule is recommended. Typically, hoses should be replaced every 1-2 years, depending on usage intensity.
Moderate Use Applications: In less demanding environments, such as light industrial applications, hoses can have a longer lifespan of 3-5 years, provided they are regularly inspected and maintained.
Extreme Environments: In environments with extreme temperatures, chemical exposure, or abrasive conditions, hoses may need to be replaced more frequently, potentially every 6-12 months, depending on the severity of the conditions.
When to Replace a Hose Before Failure Occurs
Replace the hose if you notice any signs of wear and tear, such as significant abrasion, leaks, or kinks, even if they appear minor.
Replace the hose if it fails a pressure test or shows signs of internal damage, such as soft spots or bubbles.
Replace the hose if it has been in service for longer than the manufacturer’s recommended service life, even if no visible damage is present.
Conclusion
To maximize the performance and lifespan of wire-reinforced hoses, it is crucial to select the appropriate hose type based on the specific pressure and environmental requirements of your system. Regular maintenance, including thorough inspections for signs of wear and tear, proper installation, and adherence to recommended replacement intervals, is essential to prevent unexpected failures and ensure continuous system operation. By adopting proactive maintenance strategies and using high-quality wire-reinforced hoses, you can enhance the safety and efficiency of your hydraulic systems, minimize downtime, and ultimately protect your investment.
FAQ
What are wire-reinforced hydraulic hoses used for?
Wire-reinforced hydraulic hoses are used in high-pressure hydraulic systems to transfer fluids safely and efficiently. They are commonly found in industries like construction, agriculture, manufacturing, and oil and gas.
How do I know if I need a wire-reinforced hose?
You need a wire-reinforced hose if your hydraulic system operates under high pressure or in harsh environments where durability and strength are critical.
What is the difference between braided and spiral wire-reinforced hoses?
Braided wire-reinforced hoses offer better flexibility and are suitable for medium pressure applications, while spiral wire-reinforced hoses provide higher pressure capacity and durability, ideal for heavy-duty and high-pressure uses.
How often should I inspect my wire-reinforced hydraulic hoses?
It’s recommended to inspect wire-reinforced hydraulic hoses regularly, ideally before each use in high-pressure applications or at least every three months for less demanding environments.
Can wire-reinforced hoses be used in all temperature conditions?
Wire-reinforced hoses are designed to withstand a wide range of temperatures, but it’s important to check the hose’s specifications to ensure it is suitable for your specific temperature requirements.
What are the signs that my wire-reinforced hose needs to be replaced?
Replace the hose if you notice signs of abrasion, leaks, kinks, blisters, or if it has been in service beyond the recommended lifespan, even if no visible damage is present.