Can You Use Teflon Tape on Brake Line Fittings?
Table of Contents
Introduction
Ensuring the integrity and security of brake line fittings is crucial for vehicle safety, as even minor leaks or failures can lead to catastrophic consequences. This article addresses the common question: can you use Teflon tape on brake line fittings? We will explore the design and purpose of brake line fittings, the properties and uses of Teflon tape, and why it may not be suitable for such critical applications. Additionally, we will provide alternative solutions and best practices to ensure the reliability and safety of your brake system.
Understanding Brake Line Fittings
Brake line fittings are essential components in a hydraulic brake system, responsible for connecting various parts of the braking system and ensuring the secure transfer of brake fluid. These fittings create leak-proof seals that maintain the necessary pressure within the brake lines, allowing the hydraulic fluid to efficiently transfer force from the brake pedal to the brake calipers or wheel cylinders. This process ultimately brings the vehicle to a stop. The critical nature of brake line fittings cannot be overstated, as any failure or leak can lead to brake system malfunctions, putting the vehicle and its occupants at serious risk.
Types of Brake Line Fittings
There are several types of brake line fittings, each designed for specific applications within the brake system:
Inverted Flare Fittings: Commonly used in automotive brake systems, these fittings provide a strong, leak-proof connection by creating a flare at the end of the brake line that fits snugly into the fitting.
Banjo Fittings: Typically used in high-pressure hydraulic systems, banjo fittings feature a hollow bolt and spherical union, allowing fluid to flow through the fitting while providing a secure connection.
AN (Army-Navy) Fittings: Originally designed for military applications, AN fittings are known for their high durability and precision. They use a 37-degree flare to create a tight seal and are often found in performance and racing vehicles.
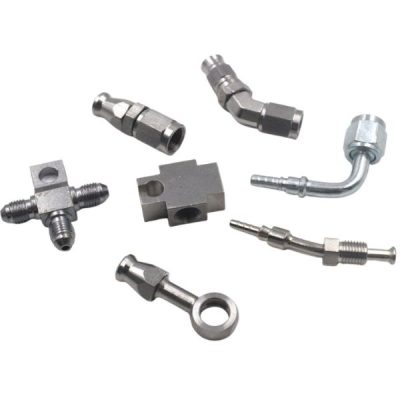
Materials Commonly Used
Brake line fittings are typically made from materials that offer durability and resistance to corrosion, ensuring long-term reliability and performance. The most commonly used materials include:
Steel: Known for its strength and resistance to high pressure, steel fittings are widely used in automotive brake systems.
Brass: Valued for its corrosion resistance and ease of installation, brass fittings are often used in both automotive and industrial applications.
Understanding the different types and materials of brake line fittings is crucial for selecting the right components for your specific needs, ensuring the safety and efficiency of your hydraulic brake system.
What is Teflon Tape?
Composition and Characteristics
Teflon tape, also known as PTFE (Polytetrafluoroethylene) tape, is a thin, white film used to seal pipe threads. It comprises PTFE, a synthetic fluoropolymer of tetrafluoroethylene, known for its non-reactivity, high melting point, and low friction properties. These characteristics make Teflon tape an excellent sealing material, as it can withstand various temperatures and chemical exposures without degrading.
Common Uses
Teflon tape is widely used in various industries, primarily for its sealing capabilities. In plumbing, it is commonly applied to the threads of pipes and fittings to prevent leaks by creating a watertight seal. Additionally, it is used in other applications such as:
Gas Lines: To seal joints in gas piping systems, ensuring no leaks.
Aerospace and Automotive Industries: For sealing hydraulic and pneumatic systems.
Food and Beverage Industry: For applications requiring non-reactive and food-safe sealing materials.
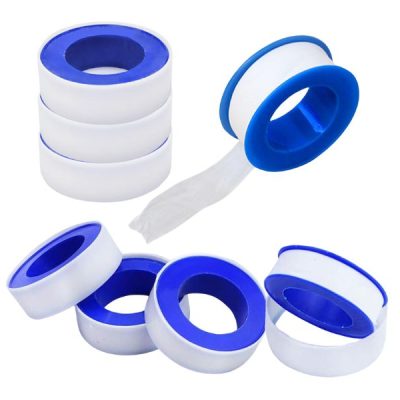
Advantages and Disadvantages
Advantages:
Sealing Threads: Teflon tape effectively fills gaps in threaded connections, preventing leaks.
Ease of Use: It is easy to apply, requiring only a few wraps around the thread to create a seal.
Chemical Resistance: Teflon tape is resistant to most chemicals, making it versatile for various applications.
Temperature Tolerance: It can withstand a broad range of temperatures, from very low to extremely high, without losing its sealing properties.
Disadvantages:
Compatibility Issues: Teflon tape is not suitable for all types of threads and connections. For instance, it is not recommended for use with certain plastics that may react with PTFE.
Over-application Risks: Over-wrapping or using excessive Teflon tape can lead to debris entering the system, potentially causing blockages or contamination.
Not Ideal for High-Pressure Systems: In some high-pressure applications, Teflon tape might not provide a reliable seal, leading to potential leaks or system failures.
The Compatibility of Teflon Tape with Brake Line Fittings
Brake Line Fitting Design
Brake line fittings are meticulously designed to create secure, leak-proof seals without the need for additional sealing materials like Teflon tape. These fittings achieve a tight seal through precision engineering, utilizing the shape and pressure of the fitting itself. Common designs include:
Inverted Flare Fittings: These fittings create a seal by forming a flare at the end of the brake line that fits perfectly into the mating surface of the fitting. The flare compresses to form a tight seal when the fitting is tightened.
AN (Army-Navy) Fittings: These fittings use a 37-degree flare to create a precise seal. The flare angle ensures that the surfaces of the fitting and the brake line form a leak-proof connection when properly torqued.
Banjo Fittings: These fittings use a banjo bolt and a spherical union to create a seal. The design allows fluid to pass through the hollow bolt while maintaining a tight connection.
Brake systems operate under extremely high pressure and require precise engineering to ensure that no leaks occur. The fittings must withstand these pressures without fail, as any breach could result in a loss of braking power and, consequently, vehicle safety.
Potential Issues with Teflon Tape
While Teflon tape is effective in many applications, it is generally not suitable for use with brake line fittings due to several reasons:
Risk of Contamination: Teflon tape can shed small particles during application, which can contaminate the brake fluid. These particles can clog small passages within the brake system, leading to malfunctions.
Improper Sealing: Brake line fittings are designed to create seals through precise metal-to-metal contact. Adding Teflon tape can interfere with this contact, preventing the fitting from sealing correctly. This can result in leaks, as the tape may not hold up under the high pressure of the brake system.
Compatibility Issues: Teflon tape is not designed to handle the high pressures and dynamic forces present in brake systems. Over time, the tape can degrade, leading to a loss of seal integrity.
Examples of Problems:
Leaks: The most immediate issue with using Teflon tape on brake line fittings is the potential for leaks. Even a small leak can lead to a significant loss of brake fluid, reducing braking efficiency or causing total brake failure.
Brake Failure: Contamination from Teflon tape particles can lead to blockages in the brake lines or within the brake calipers and cylinders. This can prevent the proper functioning of the braking system, leading to a dangerous situation where the brakes may fail to engage properly.
Maintenance Issues: Over time, Teflon tape can deteriorate under the high pressures and temperatures within the brake system. This deterioration can lead to the need for frequent maintenance and replacement of brake lines and fittings.
Alternative Solutions for Sealing Brake Line Fittings
Thread Sealants:
When it comes to sealing brake line fittings, suitable alternatives to Teflon tape are specifically designed to withstand the high pressures and conditions of hydraulic systems. One of the most effective alternatives is anaerobic thread sealants.
Anaerobic Thread Sealants: These sealants are designed to cure in the absence of air and in the presence of metal ions, making them ideal for metal-to-metal connections like brake line fittings. They provide a strong, durable seal that can handle the high pressures and temperatures of hydraulic systems without the risk of contamination or improper sealing.
Properties: These sealants remain in a liquid state when exposed to air, but once confined within the threads of the fitting, they harden to form a solid, leak-proof seal.
Advantages: Anaerobic sealants are resistant to most chemicals and fluids found in hydraulic systems, including brake fluid. They also do not degrade over time and maintain their sealing properties under dynamic conditions.
Proper Installation Techniques
Ensuring a secure and leak-free brake line fitting installation involves meticulous attention to detail and adherence to proper techniques. By following a structured approach, you can maintain the integrity and safety of your hydraulic brake system. Here’s a comprehensive step-by-step guide for installing brake line fittings without using Teflon tape:
Preparation
Clean the Threads:
Thorough Cleaning: Begin by ensuring that both the male and female threads of the brake line fittings are meticulously cleaned. Any debris, oil, or remnants of old sealant can compromise the seal. Use a wire brush, brake cleaner, or an appropriate cleaning tool to remove all contaminants. A clean surface is essential for the thread sealant to bond effectively.
Inspect the Fittings:
Detailed Inspection: Carefully inspect the fittings for any signs of damage, wear, or deformation. Even minor imperfections can lead to leaks or a failed connection. Replace any fittings that show signs of damage to ensure a secure and reliable seal. This step is crucial for maintaining the overall safety and functionality of the brake system.
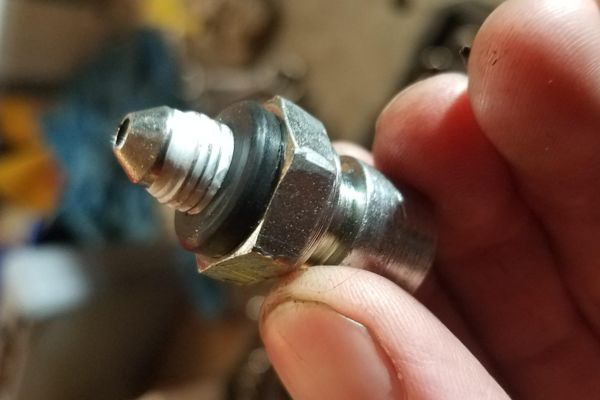
Application of Thread Sealant
Choose the Right Sealant:
Selection Criteria: Select an anaerobic thread sealant specifically designed for hydraulic systems. Anaerobic sealants are ideal as they cure in the absence of air and in the presence of metal, forming a strong, leak-proof bond. Ensure the sealant is compatible with brake fluid and can withstand the high pressures of the brake system.
Apply the Sealant:
Proper Application: Apply a small, even amount of the anaerobic sealant to the male threads of the fitting. Spread it evenly around the threads, taking care to avoid excessive application. Excess sealant can cause contamination inside the brake line, which can lead to blockages or malfunction. Ensure that the sealant does not enter the brake line, as contamination can compromise the system’s effectiveness.
Assembly
Align the Fittings:
Accurate Alignment: Carefully align the male and female threads of the fittings to ensure they thread together smoothly. Proper alignment is critical to prevent cross-threading, which can damage the threads and compromise the seal. Misalignment can lead to a weak connection that may fail under pressure.
Hand Tighten:
Initial Tightening: Begin threading the fittings together by hand. This step helps ensure proper alignment and prevents cross-threading. Hand tightening allows you to feel if the threads are engaging correctly and to adjust as needed before applying full torque.
Torque Specifications
Use a Torque Wrench:
Precision Tightening: Once the fittings are hand-tight, use a torque wrench to tighten them to the manufacturer’s recommended torque specifications. Over-tightening can strip the threads or crack the fitting, while under-tightening can lead to leaks. A torque wrench ensures that the fittings are tightened to the precise torque required for a secure seal.
Check Specifications:
Refer to Guidelines: Always refer to the vehicle’s service manual or the fitting manufacturer’s guidelines for the correct torque values. These specifications are designed to ensure a safe and effective seal under operating conditions.
Final Inspection
Check for Leaks:
Visual Inspection: After tightening the fittings, inspect the connections for any signs of leaks. Wipe the area clean and look for any fluid seepage. Leaks can indicate improper installation or damage to the fittings, requiring immediate attention.
Pressure Test:
Confirm Seal Integrity: If possible, perform a pressure test on the brake system to ensure that the fittings are properly sealed and there are no leaks. A pressure test can reveal hidden issues that may not be visible during a visual inspection.
Regular Maintenance
Periodic Checks:
Routine Inspections: Regularly inspect the brake line fittings as part of routine vehicle maintenance. Look for any signs of wear, corrosion, or leaks, and address any issues promptly. Regular maintenance helps to identify and resolve potential problems before they lead to brake system failure.
By following these proper installation techniques and using suitable thread sealants, you can ensure the reliability and safety of brake line fittings. This meticulous approach helps maintain the integrity of the hydraulic brake system, ensuring optimal performance without the need for Teflon tape. Regular maintenance and adherence to manufacturer guidelines further enhance the longevity and effectiveness of the brake system, providing peace of mind and safety for vehicle operators.
Conclusion
To ensure the safety and reliability of your brake system, always use anaerobic thread sealants specifically designed for hydraulic applications. Follow proper installation techniques, including thorough cleaning of threads, careful alignment, and adherence to torque specifications. Regularly inspect your brake line fittings as part of routine maintenance and address any issues promptly.
FAQ
t is generally not recommended to use Teflon tape on brake line fittings due to the high-pressure requirements and the potential for contamination. Anaerobic thread sealants are a better alternative.
The best sealant for brake line fittings is an anaerobic thread sealant specifically designed for hydraulic systems. These sealants cure in the absence of air and form a strong, durable seal.
Apply a small amount of anaerobic thread sealant evenly around the male threads of the fitting. Ensure that the sealant does not enter the brake line itself to avoid contamination.
Always refer to the vehicle’s service manual or the fitting manufacturer’s guidelines for the correct torque specifications. Using a torque wrench ensures the fittings are tightened to the precise torque required for a secure seal.
After tightening the fittings, inspect the connections for any signs of leaks by wiping the area clean and looking for fluid seepage. If possible, perform a pressure test on the brake system to ensure that the fittings are properly sealed.
Regular maintenance helps to identify and resolve potential problems before they lead to brake system failure. Periodically checking for signs of wear, corrosion, or leaks ensures the longevity and effectiveness of your brake system.