Maintaining clean hose assemblies is critical to ensuring the optimal performance and longevity of hydraulic and other fluid systems. Dirty or contaminated hose assemblies can lead to severe operational inefficiencies, unexpected system failures, and costly downtime. For instance, even small particles of debris can cause significant damage to sensitive components, leading to reduced efficiency and potential safety hazards.
Understanding Hose Assemblies
What Are Hose Assemblies?
Hose assemblies are an integral part of many fluid power systems, including hydraulic, pneumatic, and industrial applications. A hose assembly typically consists of a flexible hose, fittings at either end and, in some cases, protective covers or sleeves. The flexible hose is usually made of rubber, thermoplastic, or other materials that can withstand the pressures and environmental conditions it will be exposed to.
Components of a Hydraulic Hose Assembly:
Hose: The primary flexible conduit that carries fluid.
Fittings: Connectors at both ends of the hose that secure it to other components, such as pumps, valves, or actuators.
Protective Coverings: Additional layers or sleeves that protect the hose from external damage, such as abrasion, chemicals, or extreme temperatures.
Hose assemblies are used in a wide range of industries. In hydraulic systems, they are crucial for transmitting fluid power to different components, enabling the movement and control of machinery. In the automotive industry, hose assemblies are essential for fuel lines, brake systems, and coolant circuits. Other industries, such as agriculture, construction, and manufacturing, also rely heavily on hose assemblies for various fluid transfer applications.
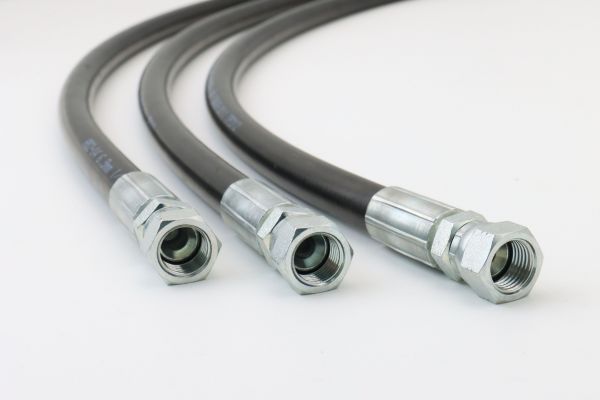
Importance of Clean Hose Assemblies
The cleanliness of hose assemblies directly impacts the performance, efficiency, and longevity of the systems in which they are used. Contaminants such as dirt, debris, moisture, and even microscopic particles can compromise the integrity of the hose assembly, leading to several issues:
Impact on Performance:
Reduced Efficiency: Contaminants can cause blockages or restrict fluid flow, reducing the overall efficiency of the system.
Pressure Loss: Accumulation of debris inside the hose can create turbulence, leading to a drop in pressure and suboptimal performance.
Increased Wear: Dirt and abrasive particles can wear down the internal surfaces of the hose and fittings, leading to premature failure.
Impact on System Longevity:
Corrosion: Moisture and certain chemicals can lead to corrosion of the metal components within the hose assembly, weakening its structural integrity.
Degradation of Hose Material: Exposure to contaminants can degrade the hose material, causing cracks, leaks, or bursts.
Risk of System Failure: In severe cases, a contaminated hose assembly can fail, leading to costly repairs, unplanned downtime, and potential safety hazards.
Common Contaminants Found in Hose Assemblies:
Dirt and Dust: Particles that can enter during installation, maintenance, or through wear and tear.
Debris: Larger particles or fragments from damaged components or external sources.
Moisture: Water or humidity that can cause rust and corrosion.
Chemical Residue: Remnants of fluids or chemicals that can react with hose materials.
The Risks of Not Cleaning Hose Assemblies
System Failures and Downtime
Contaminated hose assemblies are one of the leading causes of system malfunctions and operational inefficiencies. When debris, dirt, or moisture infiltrates a hose assembly, it can significantly disrupt fluid flow and pressure. This disruption often leads to erratic system behavior, such as sudden drops in performance or complete shutdowns.
How Contamination Leads to System Malfunctions:
Blockages and Clogs: Contaminants can accumulate inside the hose, causing blockages that restrict fluid flow. This restriction not only reduces the efficiency of the system but can also lead to an increase in internal pressure, putting additional strain on the hose and other components.
Component Damage: Abrasive particles within the fluid can erode the internal surfaces of the hose and fittings. Over time, this erosion weakens the hose, leading to leaks, bursts, or fitting failures.
Fluid Degradation: Contaminants can react with the fluid being transmitted, altering its properties and effectiveness. This degradation can compromise the system’s overall functionality, leading to unexpected malfunctions.

Increased Wear and Tear
Contaminants in hose assemblies accelerate the degradation of both the hose material and the fittings. The presence of dirt, abrasive particles, and corrosive substances can cause rapid wear, reducing the lifespan of the hose assembly and increasing the frequency of replacements.
Accelerated Degradation Due to Contaminants:
Internal Abrasion: Particles within the hose can continuously abrade the inner surfaces, leading to thinning of the hose walls and eventual failure. This abrasion is particularly problematic in high-pressure systems where fluid velocity is high.
Chemical Corrosion: Certain contaminants, especially moisture and chemicals, can cause corrosion of the metal components within the hose assembly. This corrosion weakens the structural integrity of the hose, making it more susceptible to leaks and bursts.
Material Fatigue: The presence of contaminants can lead to uneven wear on the hose material, resulting in stress concentrations and material fatigue. This fatigue can cause the hose to crack or split under pressure.
Cost Implications of Premature Hose Replacement and System Repairs:
Frequent Replacements: The need for frequent hose replacements due to accelerated wear and tear leads to increased operational costs. Replacing hose assemblies is not only expensive but also time-consuming, especially if the replacement process requires system shutdowns.
System Repairs: Contaminated hose assemblies can cause damage to other system components, such as pumps, valves, and actuators. The cumulative cost of repairing or replacing these components can be substantial, especially if the damage goes unnoticed for an extended period.
Downtime Costs: Every system failure or breakdown due to contaminated hoses results in downtime. For industries reliant on continuous operation, such as manufacturing or agriculture, downtime can lead to significant financial losses and missed production targets.
Safety Hazards
Compromised hose assemblies not only affect system performance but also pose serious safety risks. A hose assembly that is weakened by contamination is more likely to fail under pressure, which can lead to hazardous situations for personnel and equipment.
Potential Safety Risks Posed by Compromised Hose Assemblies:
Bursting Hoses: A hose that fails due to internal contamination can burst, releasing high-pressure fluids that can cause injury to nearby workers. The force of the fluid can also damage surrounding equipment and infrastructure.
Leaking Fluids: Leaks caused by contaminated hose assemblies can lead to slippery surfaces, increasing the risk of falls and injuries. In cases where the fluid is hazardous, leaks can also lead to environmental contamination and health hazards for personnel.
Fire and Explosion Risks: In certain applications, such as fuel lines or hydraulic systems in high-temperature environments, a compromised hose assembly can lead to fires or explosions. Contaminants can cause the hose material to degrade, increasing the likelihood of ignition in the presence of a spark or flame.
Importance of Regular Cleaning in Maintaining Safe Working Conditions:
Preventive Measures: Regular cleaning and maintenance of hose assemblies can significantly reduce the risk of contamination-related failures. By removing contaminants, you ensure that the hose assembly remains in optimal condition, reducing the likelihood of leaks, bursts, or other safety hazards.
Inspection and Monitoring: Routine cleaning provides an opportunity to inspect the hose assembly for signs of wear, damage, or contamination. Early detection of potential issues allows for timely repairs or replacements, preventing catastrophic failures and ensuring a safe working environment.
Step-by-Step Cleaning Process
Preparation
Before starting the cleaning process, it’s crucial to properly prepare the hose assembly to ensure effective cleaning and avoid any damage during the procedure.
Disconnecting from the System:
Begin by safely disconnecting the hose assembly from the system. Ensure that all pressure is relieved from the system to prevent any accidental fluid release during disconnection.
Use appropriate tools to detach the hose from its fittings, being careful not to damage the hose ends or connectors.
Inspection:
Conduct a thorough visual inspection of the hose assembly. Look for signs of wear, damage, or contamination on both the interior and exterior of the hose.
Check for cracks, abrasions, or any deformities that could compromise the hose’s integrity.
Inspect the fittings and connectors for corrosion, rust, or wear that might affect their performance.
Importance of Visual Inspection Before Cleaning:
A visual inspection helps identify any damage that may have occurred during the operation. If significant damage is found, it may be more appropriate to replace the hose rather than clean it.
Inspecting the hose before cleaning allows you to identify areas that require special attention during the cleaning process, such as stubborn contaminants or areas prone to corrosion.
Cleaning the Exterior
Cleaning the exterior of the hose assembly is essential to remove any dirt, grime, or debris that may have accumulated during use. This step not only improves the hose’s appearance but also prevents external contaminants from being introduced into the system during reassembly.
Brushing:
Use a soft-bristled brush to gently scrub the exterior surface of the hose. This technique is effective for removing loose dirt, dust, and debris without damaging the hose material.
Wiping:
For a more thorough clean, use a lint-free cloth or sponge soaked in a mild cleaning solution. Wipe down the entire length of the hose, paying close attention to areas with visible dirt or stains.
Pressure Washing:
In cases where the hose has been exposed to heavy contamination or harsh environments, a low-pressure wash can be used. Ensure that the pressure is low enough to avoid damaging the hose’s outer layer.
Special Considerations for Hoses Exposed to Harsh Environments:
Chemical Exposure: Hoses that have been exposed to chemicals may require specialized cleaning agents that neutralize the contaminants without damaging the hose material.
Abrasive Environments: For hoses that operate in environments with high levels of dust, sand, or other abrasive particles, extra care should be taken to remove all contaminants that could cause external abrasion or wear over time.
Temperature Extremes: Hoses exposed to extreme temperatures may have hardened contaminants on the exterior. In such cases, warming the hose slightly (if the material allows) can help loosen these contaminants before cleaning.
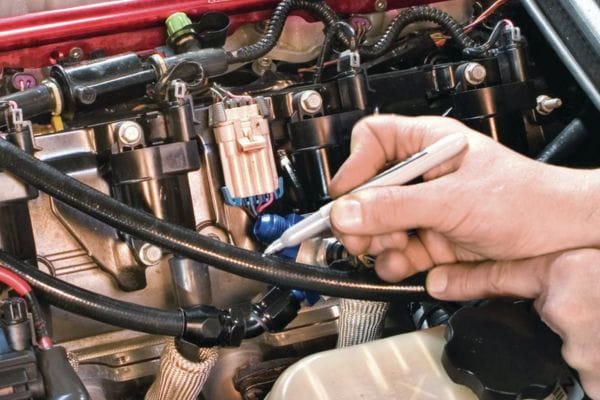
Flushing the Interior
Flushing the interior of the hose is a critical step to ensure that all internal contaminants, such as particles, moisture, and residue, are thoroughly removed. This step helps maintain the cleanliness of the fluid system and prevents contamination-related failures.
Air Blowout:
Connect an air compressor to one end of the hose and securely fasten it. Gradually increase the air pressure to blow out any loose particles, dust, or debris from the interior of the hose.
Continue blowing air through the hose until no more contaminants are expelled. This method is effective for hoses used in dry or low-contaminant environments.
Solvent Flush:
For hoses that have been exposed to oils, chemicals, or other liquids, a solvent flush may be necessary. Choose a solvent compatible with the hose material and the type of contaminant.
Pour the solvent into one end of the hose and allow it to flow through the entire length, ensuring that it reaches all internal surfaces. You may need to repeat this process several times until the solvent runs clear.
Follow up with an air blowout to remove any remaining solvent and dry the interior of the hose.
Choosing the Right Flushing Method Based on Hose Material and Application:
Rubber Hoses: Use a mild solvent or detergent solution that won’t degrade the rubber material. Avoid harsh chemicals that could cause swelling or weakening.
Thermoplastic Hoses: Opt for cleaning agents that are specifically formulated for plastic materials. Ensure the solvent won’t cause cracking or brittleness.
Hydraulic Hoses: For hydraulic applications, it’s crucial to use a solvent that is compatible with the hydraulic fluid used in the system. This ensures that any residual solvent won’t react negatively with the hydraulic fluid.
Drying and Reassembly
After cleaning, it’s important to ensure that the hose assembly is thoroughly dried to prevent moisture from remaining inside the hose, which could lead to corrosion or contamination when the system is reactivated.
Air Drying:
After flushing, use compressed air to blow out any remaining moisture or cleaning agents from the hose interior. Continue until the interior is completely dry.
Natural Drying:
Allow the hose to air dry naturally in a clean, dry environment. This method may take longer but is effective if compressed air is not available.
Heat Drying (If Applicable):
For certain hose materials that can withstand moderate heat, a heat gun or drying chamber may be used to accelerate the drying process. Ensure the temperature is within the hose’s tolerance to avoid damage.
Importance of Reassembly Checks and Torque Specifications for Fittings:
Reassembly Checks:
Before reattaching the hose to the system, inspect the fittings and connectors for any signs of damage or wear. Ensure that all components are in good condition and ready for reassembly.
Check that the hose ends are clean and free of debris. Any particles trapped in the fittings during reassembly can lead to leaks or contamination.
Torque Specifications:
When reassembling the hose, it is essential to tighten the fittings according to the manufacturer’s torque specifications. Over-tightening can damage the fittings or the hose, while under-tightening can lead to leaks.
Use a calibrated torque wrench to ensure that the correct amount of torque is applied. Double-check the connections to ensure a secure and leak-free reassembly.
Troubleshooting Common Cleaning Issues
Stubborn Contaminants
Cleaning stubborn contaminants such as rust, hardened debris, or heavy residues can be challenging. Addressing these issues effectively requires the use of specialized techniques and tools.
Rust:
Rust Remover Solutions: Use rust remover chemicals specifically designed for the type of metal in the hose fittings. Apply the solution as per the manufacturer’s instructions, allowing it to penetrate and dissolve the rust.
Mechanical Scrubbing: For severe rust, use a wire brush or abrasive pad to scrub the affected areas. Ensure that the brush is suitable for the material to avoid causing further damage.
Hardened Debris:
Soaking: Soak the affected areas in a suitable solvent or cleaning agent to soften the hardened debris. This will make it easier to remove using brushes or scrapers.
Ultrasonic Cleaning: For intricate or hard-to-reach areas, ultrasonic cleaning devices can be used. These devices use high-frequency sound waves to remove debris without physically touching the hose.
Use of Specialized Tools and Agents:
Specialized Brushes: Use brushes designed for specific materials or hose types to avoid damage while effectively removing contaminants.
Industrial Cleaners: Employ industrial-grade cleaning agents for tough residues. Ensure that these agents are compatible with the hose material and follow safety guidelines.
High-Pressure Water Jets: For extreme cases, high-pressure water jets may be used. However, this should be done cautiously to prevent damage to the hose or fittings.
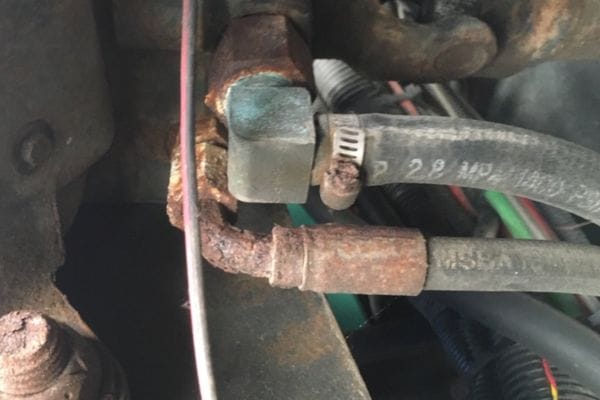
Preventing Damage During Cleaning
Preventing damage to the hose assembly during cleaning is crucial to maintaining its functionality and longevity. Here are some techniques to ensure that the cleaning process does not compromise the hose.
Techniques to Avoid Damaging the Hose Assembly:
Avoid Abrasive Materials: Use non-abrasive cleaning tools and materials to prevent scratching or wearing down the hose surface. Abrasive brushes or pads can cause damage, especially to softer hose materials.
Control Pressure and Temperature: When using pressure washing or steam cleaning, control the pressure and temperature to avoid damaging the hose. Excessive pressure or high temperatures can weaken or distort the hose material.
Use Appropriate Cleaning Agents: Ensure that any cleaning agents used are compatible with the hose material. Harsh chemicals can degrade the hose and fittings, leading to premature failure.
Tips for Maintaining the Integrity of Hose Materials and Fittings:
Regular Inspection: Continuously monitor the condition of the hose and fittings throughout the cleaning process. Address any signs of wear or damage immediately.
Gentle Handling: Handle the hose and fittings gently to avoid bending or stressing them. Avoid dropping or knocking them against hard surfaces.
Proper Drying: Ensure that the hose is completely dried after cleaning to prevent rust or mold formation. Use soft, absorbent towels or air drying methods.
Post-Cleaning Testing
After cleaning, it’s essential to test the hose assembly to confirm that it is free of contaminants and fully functional. This step helps ensure that the assembly will perform reliably in its operational environment.
Importance of Testing Hose Assemblies After Cleaning:
Pressure Testing: This test checks the hose’s ability to withstand operational pressures without leaking or bursting. It helps confirm that the hose can handle the expected pressure once reinstalled.
Leak Testing: Verify that all fittings and connections are secure and leak-free. Use appropriate leak detection methods, such as soap solution or pressure gauges, to identify any potential issues.
Recommended Testing Methods:
Hydrostatic Testing: Apply water or another test fluid at a pressure higher than the normal operating pressure to check for leaks or weaknesses.
Functional Testing: Reconnect the hose to the system and perform operational tests to ensure that it functions correctly under real conditions.
Conclusion
Maintaining clean hose assemblies is essential for ensuring the optimal performance and longevity of fluid systems. Regular cleaning and inspection help prevent system failures, reduce wear and tear, and mitigate safety risks. Contaminants such as dirt, debris, and moisture can severely impact the efficiency and safety of hydraulic and other fluid systems, leading to increased downtime, higher repair costs, and potential hazards. By adhering to the step-by-step cleaning process outlined in this guide, you can effectively manage these risks and ensure your hose assemblies remain in top condition.
FAQ
Why is it important to clean hose assemblies regularly?
Regular cleaning of hose assemblies is crucial to prevent contamination that can cause system malfunctions, reduce efficiency, and increase the risk of system failures and safety hazards.
What tools are needed for cleaning hose assemblies?
Essential tools include brushes, lint-free cloths, solvents or cleaning agents, and personal protective equipment (PPE) such as gloves and goggles. For more stubborn contaminants, you might need specialized tools like ultrasonic cleaners or rust removers.
How do I prepare a hose assembly for cleaning?
Prepare the hose assembly by disconnecting it from the system, relieving any pressure, and conducting a visual inspection for damage. This ensures that you can address any issues before starting the cleaning process.
What is the best method for flushing the interior of a hose?
Flushing the interior of a hose can be done using methods such as air blowout, solvent flush, or high-pressure water jets, depending on the type of hose material and the nature of the contaminants.
How should I dry a hose assembly after cleaning?
After cleaning, dry the hose assembly thoroughly using compressed air or a clean, dry cloth. Ensure that the hose is completely dry before reassembling to prevent moisture-related issues or contamination.
What should I check during reassembly?
During reassembly, ensure that all fittings are properly aligned and tightened to the manufacturer’s torque specifications. Perform a final inspection to confirm that the hose is securely connected and free from any signs of damage or leaks.