Hydraulic hose fittings are integral to ensuring a reliable connection in hydraulic systems, which are typically subject to high-pressure, high-temperature, and harsh working conditions. Over time, however, fittings can become difficult to remove, which can cause operational delays and increased maintenance costs. Whether it’s due to pressure, corrosion, dirt, or improper installation, stuck hydraulic hose fittings are a common issue that can cause headaches for maintenance teams.
Common Reasons Hydraulic Fittings Become Stuck
The Impact of Corrosion and Wear on Hose Fittings
Corrosion is one of the leading culprits behind stuck hydraulic fittings, and it’s no mystery why. Hydraulic systems often operate in challenging environments where exposure to moisture, chemicals, and fluctuating temperatures is the norm. Over time, these elements can degrade the material of the fitting, leading to rust formation. Rust and scale buildup can essentially “weld” the fitting to the hose or its coupling.
Corrosion is especially prevalent when there is material incompatibility between the fitting and the hydraulic fluid or when the system isn’t adequately sealed. For instance, a carbon steel fitting exposed to high-moisture environments without a protective coating is highly susceptible to rust. This corrosion can creep into the threads, making unscrewing a nightmare.
Proper maintenance and the use of corrosion-resistant materials, such as stainless steel or coated fittings, can significantly reduce this risk.
The Role of Pressure and Temperature in Sticking Fittings
Hydraulic systems are synonymous with high-pressure operations. This pressure can lead to fittings binding together, particularly if they were over-tightened during installation. Think of it as the components being pressed into an unyielding embrace due to the immense force they experience daily.
Temperature fluctuations add another layer of complexity. In systems exposed to high-heat environments, metals tend to expand. As the system cools down, the fittings contract but may not return to their original state, causing them to seize. Repeated cycles of this thermal expansion and contraction can create a “lock-in” effect, making disconnection nearly impossible.
To prevent this, use fittings with appropriate temperature and pressure ratings for the application. Proper torque settings during installation also play a crucial role in avoiding this type of sticking.
Signs That Your Hydraulic Hose Fittings Are Stuck
Difficulty in Loosening or Removing the Fitting
One of the most obvious signs that your hydraulic hose fittings are stuck is when they simply refuse to budge. If you’re applying standard loosening force—using wrenches, pipe tools, or even hydraulic tools—but the fitting doesn’t respond, this is a clear indication that something is preventing the threads from moving. Over time, factors like excessive hydraulic pressure, rust, or improper installation can cause the threads to lock into place, making it nearly impossible to disconnect the fitting using typical methods.
Hydraulic fittings subjected to high pressure and extreme temperatures can experience a “locking” effect, where the threads become bound due to thermal expansion or corrosion. This resistance can escalate over time, meaning even the most experienced technicians may find themselves struggling with these fittings. If the fitting has become particularly stuck, you might need to apply specialized tools or methods like penetrating oil or heat to break the seal.
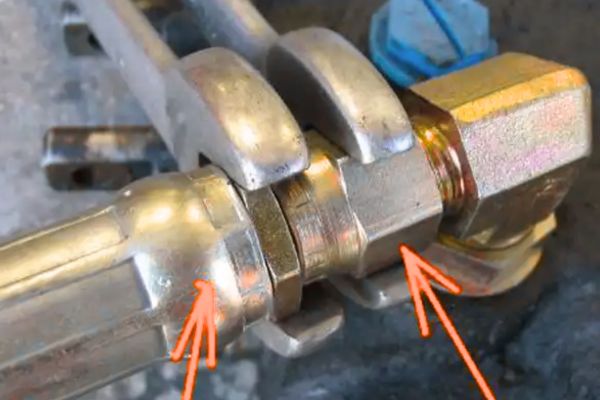
Unusual Leaks Around the Fitting Connection
If you notice fluid leaking from the fitting, it could signal that the fitting is stuck, improperly installed, or has experienced some level of damage. Leaks are often a direct result of either a damaged thread or seal, which might be caused by over-tightening or corrosion.
When a fitting is seized or not properly loosened, the threads can get stripped or the seals can be compromised. This results in hydraulic fluid leaking out, which is not only a safety hazard but also a sign that the fitting may need to be replaced or carefully freed from the system. If the leaks persist despite tightening or trying to reseat the fitting, it’s likely that the underlying issue is a stuck connection, requiring more intensive intervention.
Unresponsive Threads and Seals
Another common sign of stuck hydraulic fittings is unresponsive threads and seals. When you’re working with a hydraulic fitting, you should be able to apply the proper amount of torque to either tighten or loosen the fitting. However, if the threads fail to respond to your wrench or tools, the fitting is likely stuck due to corrosion, pressure buildup, or other environmental factors.
In cases of extreme pressure or corrosion, the threads can become so damaged or locked that no amount of standard tightening or loosening will help. This can prevent the hose from being disconnected properly, and continuing to apply force can risk further damage to the system. In these situations, additional steps like using a penetrating oil or applying heat may be necessary to free the stuck fitting.
Why Do Hydraulic Hose Fittings Get Stuck?
The Effect of Dirt and Debris in the Hydraulic System
One of the lesser-known causes of stuck hydraulic hose fittings is the presence of dirt, dust, and debris within the system. These small particles can infiltrate the hydraulic circuit, entering through vents, leaks, or inadequate filtration systems. Once inside, they can accumulate at the fitting connections, causing additional friction and wear. This accumulation of debris prevents the fitting from sliding or rotating freely, leading to jamming.
As dirt particles settle around the threads or seals, they can bind with the metal surfaces, creating a gritty layer that can make it nearly impossible to disconnect or remove the fitting without additional force. Over time, this debris can cause permanent damage to the threads or seals, resulting in a stuck fitting that might need to be replaced entirely.
Regular cleaning and proper filtration are critical in preventing this buildup. Ensuring the hydraulic system is properly sealed and maintaining a clean environment can significantly reduce the chances of dirt and debris causing stuck fittings.
Corrosion from Fluid Leaks and External Exposure
Fluid leaks and external exposure are among the leading causes of corrosion in hydraulic systems, and they often play a significant role in making hydraulic hose fittings get stuck. If the hydraulic system is exposed to moisture—either through weather conditions or fluid leaks—rust can begin to form on the fittings. This rust essentially binds the fitting and hose together, making it incredibly difficult to remove or disconnect.
Additionally, hydraulic fluid itself can sometimes contain corrosive elements, especially if it has been in use for extended periods or hasn’t been properly filtered. Some hydraulic fluids may contain acids, salts, or other compounds that can eat away at metal parts, accelerating the corrosion process. This corrosion can lock the fitting in place, preventing proper disconnection and even damaging the fitting to the point where it must be replaced.
To prevent corrosion, regular inspection of fittings and timely maintenance, such as replacing worn seals or treating fluid leaks, are essential. Using corrosion-resistant materials and applying anti-corrosive coatings can also help protect fittings from rust and wear over time.
The Consequences of Over-Tightening Hydraulic Fittings
Over-tightening hydraulic fittings during installation is one of the most common causes of fittings becoming stuck. It may seem counterintuitive, but applying too much torque to a fitting can lead to it binding with the hose or coupling, creating an immovable connection.
When a fitting is over-tightened, the metal components may deform, causing the threads to become misaligned or the seals to compress too much. This unnecessary pressure puts additional stress on the connection and makes it harder to loosen or remove the fitting in the future. The excessive tightening also increases the likelihood of corrosion due to the increased friction, especially in high-pressure environments.
To prevent this, always use the correct torque settings as specified by the manufacturer. Using a torque wrench during installation can ensure the right amount of force is applied, which helps avoid over-tightening and keeps fittings functioning smoothly over time.
The Role of Pressure Build-Up in Stuck Fittings
Hydraulic systems operate under very high pressure, and this pressure can often cause fittings to become stuck over time. When a fitting is constantly subjected to pressure, the internal components of the fitting can expand and contract. If the system pressure is too high or fluctuates too much, this repeated expansion and contraction can cause the fitting to “lock” into place.
Additionally, excessive pressure can cause the threads or seals to distort, further increasing the difficulty in loosening or removing the fitting. In extreme cases, the pressure can cause the fitting to become permanently fused with the hose or coupling, making any disconnection attempts almost impossible without special tools or techniques.
Regular maintenance and pressure regulation are key to preventing pressure build-up issues. Monitoring the pressure levels within the hydraulic system and addressing any abnormalities can help prevent fittings from becoming stuck due to internal stress. Additionally, pressure relief valves should be used to safely manage system pressure and ensure fittings remain in optimal condition.
Step-by-Step Guide to Removing Stuck Hydraulic Hose Fittings
Step 1: Assess the Situation and Prepare Your Work Area
Before attempting to remove a stuck hydraulic hose fitting, it’s important to first assess the situation. Check the surrounding area for any potential hazards, such as external damage to the fittings or system. Ensure that the work area is clean and free of flammable materials, especially when working with hydraulic fluids, which can be flammable.
Disconnect any power sources to the hydraulic system to prevent any accidental operation of the system while you’re working on it. Always wear appropriate personal protective equipment (PPE) such as gloves, goggles, and protective clothing to safeguard yourself from flying debris, hot surfaces, or accidental fluid sprays.
Step 2: Relieve System Pressure and Drain Fluid if Necessary
Before you begin working on any hydraulic system, it is crucial to relieve all pressure to ensure safety. The first action should be to open the system’s pressure release valve. This will allow the hydraulic pressure to dissipate and prevent any accidental pressure bursts that could lead to injury or further damage to the system.
Once the pressure has been relieved, drain any residual hydraulic fluid from the hoses. This step is especially important as hydraulic fluids can remain under pressure even after the system is turned off. Draining the fluid helps to prevent leaks or sudden bursts of fluid when you attempt to remove the fitting.
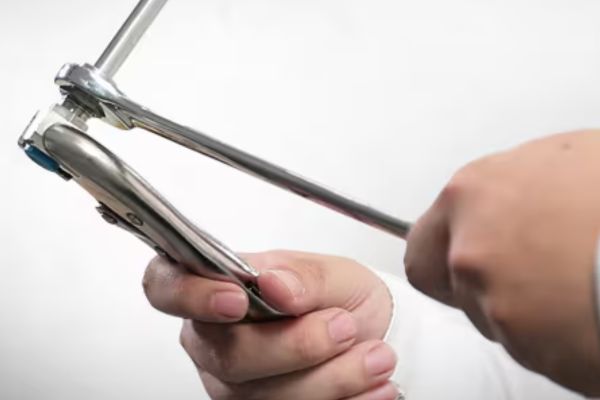
Step 3: Inspect for Visible Corrosion or Debris
Once you’ve prepared the area and relieved pressure, visually inspect the fitting and surrounding parts for any signs of corrosion, rust, or accumulated debris. This step will give you an idea of the extent of the issue and whether additional cleaning or lubrication is needed.
If you spot significant corrosion or debris, it may be necessary to clean the area before attempting further removal. Corrosion can cause the fitting to become fused with the hose, and debris can obstruct the fitting’s movement, making it harder to loosen. A wire brush, cleaning solvent, or mild abrasive can help clear the area before proceeding.
Step 4: Loosen the Fitting with Correct Torque Application
Once the fitting is free of visible corrosion and debris, the next step is to try loosening it using the proper torque. Select a proper-sized wrench or spanner that fits the fitting securely. It’s critical to apply the correct amount of torque as specified by the manufacturer to avoid damaging the fitting or hose.
Apply steady, controlled force to the fitting. Avoid jerking or sudden movements, as this can cause stripping of threads, damaging seals, or even breaking the fitting. If the fitting resists, stop and reconsider your approach before applying more force, as over-tightening may make it even harder to loosen.
Step 5: Use Penetrating Oil to Break the Bond
If the fitting still won’t loosen, applying penetrating oil is a key step in the process. This type of oil is designed to break down rust, corrosion, and other debris that may be causing the fitting to stick. Apply a generous amount of penetrating oil to the threads of the stuck fitting, ensuring the oil fully coats the area around the connection.
Allow the oil to sit for several minutes, or longer if necessary, to give it time to penetrate the rust or debris. For particularly stubborn fittings, you may need to apply the oil multiple times. The oil works by reducing friction and breaking down the corrosion, making it easier to loosen the fitting.
Step 6: Carefully Use Leverage for Stubborn Fittings
If the fitting still remains stuck after using penetrating oil, you can try using additional leverage to break the bond. A pipe wrench or breaker bar can provide extra force to loosen a fitting that won’t budge. Attach the tool securely and apply gradual, consistent pressure.
However, when using leverage, caution is essential. Avoid applying excessive force, as it can cause damage to the fitting, the hose, or even the entire hydraulic system. Be mindful of the force you’re applying to ensure that the fitting is not over-tightened in the process, which could cause further issues down the line.
If the fitting still won’t come off, it may be time to consult a professional or use more advanced methods, such as heat or impact tools, to free the stuck connection.
Troubleshooting Stuck Hydraulic Hose Fittings
What to Do When the Fitting Won’t Budge
If you’ve tried all standard methods—such as applying the correct torque, using penetrating oil, or leveraging tools like a pipe wrench—and the fitting still refuses to budge, it’s time to take more advanced steps. One effective method is to apply heat to the fitting. Heat can help expand the metal, breaking the bond between the fitting and the hose or coupling, particularly if rust or corrosion is the issue. However, be cautious when applying heat; overheating could damage seals, O-rings, or other parts of the hydraulic system.
Another tool you can use is vibration. Impact wrenches or vibration tools can help break loose stuck fittings by loosening the rust or debris around the connection. The vibration disrupts the bond, making it easier to loosen the fitting without using excessive force.
In extreme cases, if the fitting is severely corroded or damaged beyond repair, you may need to cut off the fitting. Using a pipe cutter or saw, carefully cut through the fitting, but make sure to protect the surrounding components to avoid unnecessary damage. This should be a last resort, as cutting the fitting could require replacing parts of the hydraulic system.
How to Avoid Damaging Hydraulic Hoses and Fittings During Removal
When dealing with stuck hydraulic fittings, it’s crucial to prevent further damage to the hose or fitting. The first step in avoiding damage is to use the correct tools. Never try to force a fitting off with improper tools, as this can damage the threads, seals, or the hose itself. Always choose the right-sized wrenches, pipe tools, or torque wrenches to ensure you’re applying force in the most efficient and controlled way possible.
Additionally, it’s important to apply gradual, consistent force when attempting to loosen a fitting. Jerking or using excessive force can lead to damaged threads or cracked fittings, and in some cases, it may even cause the fitting to break entirely. Instead, work slowly and carefully, ensuring you’re not applying too much torque all at once.
If the fitting still doesn’t budge, don’t rush the process—give the penetrating oil time to work, or use a heat gun to gradually warm up the fitting. Patience is key to avoid costly repairs and prevent damaging the system during removal.
Dealing with Fittings That Seem Permanently Stuck
In certain cases, particularly when the fitting seems permanently stuck, professional assistance may be necessary. If the fitting is severely corroded, rusted, or has been overtightened beyond the point of reasonable removal, attempting to remove it yourself can lead to even more serious damage. For example, forcing a stuck fitting can damage the hose, the fitting itself, or even other parts of the hydraulic system like the couplings or valves.
When this happens, it’s time to consult a hydraulic technician or a professional mechanic who has experience dealing with stuck hydraulic fittings. Professionals may have access to specialized tools, such as cutting torches, high-powered impact tools, or hydraulic pullers that can remove even the most stubborn fittings without damaging the system. They can also evaluate the rest of the hydraulic system to ensure that removing the stuck fitting doesn’t lead to further complications.
Conclusion
To prevent hydraulic hose fittings from becoming stuck in the first place, regular inspection and maintenance are key. Monitoring the system for signs of corrosion, pressure fluctuations, or improper tightening can help catch issues before they become significant problems. Additionally, using proper installation techniques, anti-seize lubricants, and ensuring a clean environment can greatly extend the life of your hydraulic fittings.
FAQ
What should I do if a hydraulic hose fitting is stuck?
Start by assessing the situation. Ensure the system is powered off and the pressure is relieved. Inspect for corrosion or debris, apply penetrating oil, and then attempt to loosen the fitting with the proper tools.
How can I prevent hydraulic hose fittings from getting stuck?
Inspect fittings for corrosion, dirt, or debris, and clean them periodically. Use the correct torque when tightening fittings, and apply anti-seize lubricants during installation to prevent them from seizing in the future.
Can I use any oil to loosen a stuck hydraulic fitting?
No, use penetrating oil specifically designed for breaking rust and corrosion. Regular oils or lubricants may not have the same properties needed to dissolve rust or reduce friction, making the process less effective.
What tools do I need to remove a stuck hydraulic fitting?
Essential tools include a proper-sized wrench or spanner, penetrating oil, and if needed, a pipe wrench or breaker bar for additional leverage. Always ensure that the tools are compatible with the size and type of fitting you’re working on.
Is it safe to use heat on a stuck hydraulic fitting?
Yes, heat can help loosen a stuck fitting by expanding the metal and breaking the bond formed by corrosion. However, be cautious not to overheat, as it can damage the seals, O-rings, or other parts of the hydraulic system.
When should I call a professional for stuck hydraulic fittings?
If you’ve tried all removal methods, including the use of penetrating oil, heat, and proper leverage, and the fitting remains stuck, it’s time to consult a professional. Forcing the fitting can cause expensive damage to the system.