Hydraulic hose standards play a critical role in ensuring the safe and efficient operation of hydraulic systems across various industries. These standards define the requirements for hose construction, performance, pressure ratings, and safety, ensuring that systems operate reliably under demanding conditions. The adoption and adherence to these standards help to mitigate risks, such as hose failure or leaks, which could lead to downtime, equipment damage, or even safety hazards.
Importance of Hydraulic Hose Standards
Hydraulic hose standards are essential for ensuring both safety and performance across industries that rely heavily on hydraulic systems. These standards set specific criteria for hose construction, pressure capacity, temperature tolerance, and material integrity, which are crucial in maintaining the safety and efficiency of hydraulic systems. Adhering to these standards helps prevent catastrophic failures such as leaks, bursts, and malfunctions that can cause extensive downtime, costly repairs, and even pose significant safety hazards to personnel and equipment.
Ensuring Safety and Performance
Hydraulic hose standards serve as a protective measure, mitigating risks by ensuring that hoses are designed and manufactured to withstand the pressures and demands of specific applications. For example, standards like SAE J517 and ISO 18752 dictate the pressure ratings, temperature ranges, and flexibility required for different hose types, reducing the chances of failure due to overloading or extreme conditions. By following these guidelines, manufacturers and users can ensure that their hoses perform consistently, reducing the likelihood of leaks, bursts, or other malfunctions that could result in injuries or system downtime.
Compliance with Industry Regulations
Hydraulic hose standards also play a critical role in regulatory compliance across various industries such as construction, manufacturing, agriculture, and transportation. These industries often have stringent safety and operational regulations that must be followed to avoid penalties, legal issues, and reputational damage. For instance, the construction industry must comply with safety regulations that ensure hydraulic equipment can operate under high-stress conditions without failure. Meeting recognized standards like ISO, SAE, or EN ensures that companies remain compliant with regulatory requirements and that their hydraulic systems are fit for purpose.
Globalization of Standards
In an increasingly globalized market, the need for standardized hydraulic hoses is paramount. Manufacturers and suppliers that operate across borders face the challenge of ensuring their products meet the various national and international standards applicable in different regions. This standardization allows for smoother operations in global markets, enabling compatibility and consistency in hydraulic systems regardless of the geographical location. Whether manufacturing in Europe or supplying to North America, adherence to globally recognized standards like ISO and SAE ensures that hoses can be used universally, reducing complexity and the potential for compatibility issues.
Overview of Major Hydraulic Hose Standards
Hydraulic hose standards play a crucial role in ensuring that hoses meet the requirements for performance, safety, and durability across various industries. Different regions and organizations have developed specific standards to guide the manufacturing and application of hydraulic hoses.
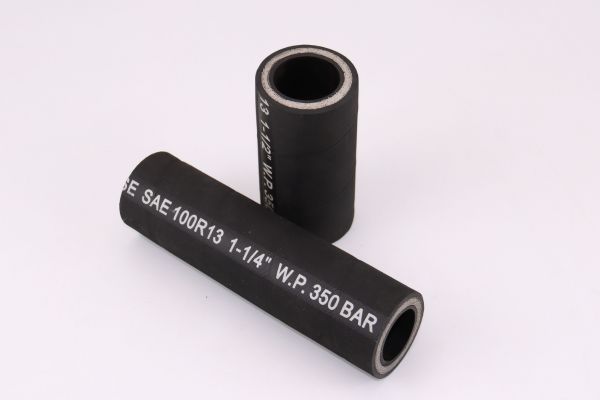
SAE Standards
Description:
The Society of Automotive Engineers (SAE) is a globally recognized organization that sets standards for hydraulic hoses used across multiple industries. The most widely adopted set of standards within the hydraulic hose industry is SAE J517, which specifies the requirements for hydraulic hose construction, performance, and pressure ratings. SAE standards are crucial for ensuring that hydraulic systems operate safely and efficiently.
Key Aspects:
Classification by Pressure Rating:
SAE J517 classifies hoses into different pressure ratings, which include low, medium, high, and very high pressures. Each class is designed to meet specific needs depending on the operating environment and system requirements.
Specific Hose Types and Construction:
SAE standards cover a range of hose types, including SAE 100R1, 100R2, and others:
SAE 100R1: A single-wire braid hose designed for medium pressure hydraulic systems.
SAE 100R2: A double-wire braid hose designed for higher pressure applications.
These hoses are constructed with layers of rubber and steel braiding, ensuring strength and flexibility while adhering to strict performance specifications.
Durability and Testing:
SAE standards also define the testing protocols to ensure that hoses can withstand rigorous use, including impulse, burst, and temperature testing. The guidelines ensure that the hoses meet the required specifications for different operational conditions.
ISO Standards
Description:
The International Organization for Standardization (ISO) develops global standards that apply across industries and geographical boundaries. One of the most significant standards for hydraulic hoses is ISO 18752, which focuses on performance-based criteria, particularly pressure classes and durability.
Key Aspects:
Explanation of ISO 18752:
ISO 18752 categorizes hydraulic hoses into different pressure classes rather than focusing solely on construction types. These classes range from Class A to Class D, with each class representing different pressure capacities and impulse life requirements. This classification allows users to select hoses based on their service conditions, such as the pressure rating and environmental exposure.
Differences Between ISO and SAE Standards:
While SAE standards are predominantly construction-based, ISO standards are performance-based, with a stronger focus on pressure and durability in service conditions. ISO 18752 is often preferred in applications where pressure stability and impulse life are critical, whereas SAE standards may be more commonly used for region-specific construction specifications. The global reach of ISO standards makes them ideal for international applications, providing a unified system for hose selection across different countries and industries.
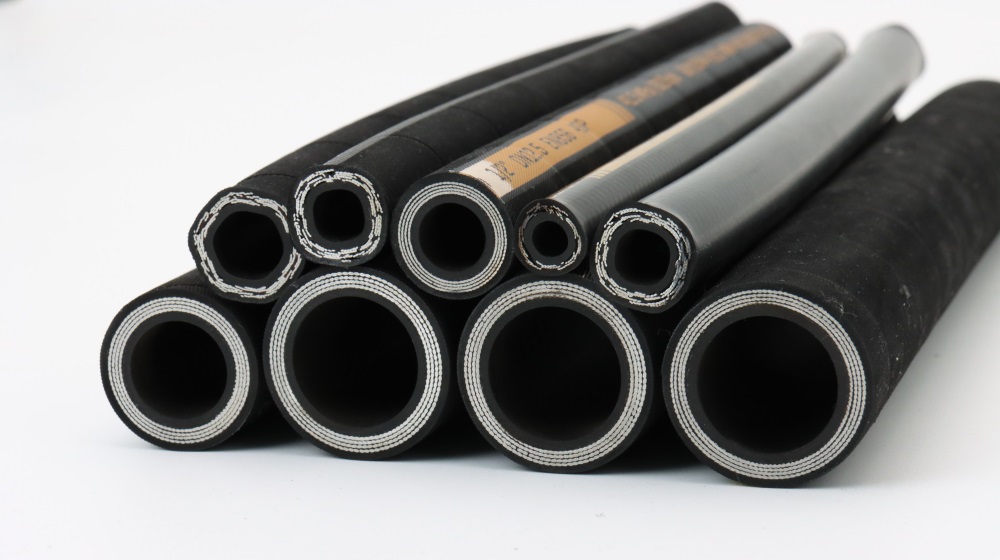
EN Standards
Description:
European Standards (EN) provide the foundation for hydraulic hose specifications across Europe. These standards cover a broad range of hose types, each designed to meet the stringent requirements of European industries.
Key Aspects:
EN standards encompass several important hose specifications, including EN 853, EN 856, and EN 857.
EN 853: This standard covers medium-pressure hoses with single or double wire braid reinforcement. These hoses are suitable for general hydraulic applications in industries like manufacturing and construction.
EN 856: This standard addresses high-pressure hoses, such as 4SH and 4SP, which are designed for very high-pressure environments. These hoses are used in heavy-duty applications where the hydraulic system operates under extreme pressures and conditions.
EN 857: This standard is for compact wire braid reinforced hoses, which are more flexible than traditional hoses. These hoses are often used in applications where space is limited but high-pressure performance is still required.
EN standards are widely accepted in the European Union and provide a strong regulatory framework that ensures high quality and safety.
DIN Standards
Description:
The German Institute for Standardization (DIN) develops hydraulic hose standards primarily used in Germany and other parts of Europe. DIN standards are known for their precision and high-quality requirements, making them a benchmark in the hydraulic hose industry.
Key Aspects:
Popular DIN Specifications:
DIN 20022: This standard specifies hoses with single or double wire braids, similar to SAE 100R1 and 100R2 hoses, and is commonly used for medium-pressure applications. These hoses are often chosen for their flexibility and ease of installation.
DIN 20023: This standard covers very high-pressure hoses with multiple layers of steel wire reinforcement. These hoses are typically used in demanding environments such as heavy machinery and construction equipment, where high-pressure stability is crucial.
DIN 20024: This standard addresses ultra-high-pressure hoses, often used in specialized applications such as oil drilling or hydraulic presses. These hoses are constructed with extra reinforcement to handle extreme pressures and conditions.
DIN standards are widely respected for their attention to detail and focus on ensuring that hoses meet specific performance criteria, particularly in high-pressure and high-stress environments.
Comparison of Hydraulic Hose Standards
Understanding the differences and similarities between hydraulic hose standards is crucial for selecting the appropriate hoses for various applications. In this section, we will compare SAE vs. ISO standards and EN vs. DIN standards, highlighting key differences in pressure ratings, temperature tolerances, hose construction, and testing criteria.
SAE vs. ISO Standards
Pressure Ratings:
SAE Standards: SAE hydraulic hose standards, such as SAE J517, classify hoses based on their pressure ratings, including low, medium, high, and very high pressures. For example, SAE 100R1 hoses are designed for lower pressures, while SAE 100R2 and 100R12 are constructed for higher-pressure applications. The focus is on the construction of the hose, primarily on how reinforcement layers affect pressure-handling capabilities.
ISO Standards: ISO standards, particularly ISO 18752, categorize hoses into pressure classes (A-D) rather than focusing on construction types. This classification is performance-based, where Class A handles lower pressures, and Class D is designed for very high-pressure environments. The emphasis is on the hose’s ability to maintain performance under specific pressure and impulse life conditions.
Temperature Tolerances:
SAE Standards: SAE standards define temperature ranges for each hose type, specifying operational temperatures in both cold and hot environments. However, the focus tends to be on the construction material (e.g., rubber, thermoplastic) that dictates the allowable temperature ranges.
ISO Standards: ISO standards take a more performance-oriented approach to temperature tolerances, considering the hose’s ability to withstand extreme temperatures while maintaining its pressure rating and flexibility. ISO 18752 is designed to account for temperature variations across different environmental conditions and operating cycles.
Hose Construction:
SAE Standards: The construction of SAE hoses is primarily based on the number and type of reinforcement layers. Hoses like SAE 100R1 are single-wire braid hoses, while others like SAE 100R12 use multiple spiral layers for higher pressure capabilities.
ISO Standards: ISO standards, on the other hand, focus less on the exact construction (e.g., number of layers) and more on the overall performance of the hose in terms of pressure, impulse, and environmental resistance. While construction is important, the performance classification (A-D) serves as the primary reference for selection.
EN vs. DIN Standards
Scope and Applications:
EN Standards: EN standards cover a wide range of hose types with a focus on European markets and industries. Standards like EN 853, EN 856, and EN 857 define hoses for medium, high, and compact applications. EN standards are more focused on the application scope, detailing which industries and equipment types each hose is suited for, such as general hydraulic systems, construction machinery, or compact spaces.
DIN Standards: DIN standards, particularly DIN 20022, 20023, and 20024, are known for their precision and strict requirements. DIN standards are often applied to high-pressure systems and are widely used in German industries and beyond. They are known for defining extremely specific performance criteria, such as resistance to oil, chemicals, and environmental factors, making them ideal for high-performance applications like heavy machinery.
Testing Criteria:
EN Standards: EN standards emphasize durability and flexibility under European operating conditions. Testing criteria focus on the hose’s ability to handle specific pressure ranges, impulse life, and environmental resistance, with allowances for regional variations. These standards are often aligned with broader European safety regulations.
DIN Standards: DIN standards are more stringent when it comes to testing, with a focus on high pressure and demanding operating conditions. Hoses under DIN standards undergo rigorous testing for factors like resistance to abrasion, oil, and extreme temperatures. DIN standards are known for their high level of detail, ensuring hoses meet precise requirements in challenging environments.
How to Select the Right Hydraulic Hose Based on Standards
Selecting the appropriate hydraulic hose for your application is crucial to ensuring the efficiency, safety, and longevity of your hydraulic system. With the abundance of standards from SAE, ISO, EN, and DIN, understanding how to choose the right hose can seem overwhelming.
Step-by-Step Selection Process
Understanding Application Requirements:
Pressure: The first step is determining the operating pressure of your hydraulic system. This is vital because the hose you select must be able to handle the system’s pressure without failure. Check the system’s maximum operating pressure and ensure the hose has a pressure rating that meets or exceeds this requirement.
Temperature: Consider the temperature range of the environment where the hose will operate. Hydraulic hoses must be able to withstand both the ambient temperature and the temperature of the fluid passing through them. Ensure the hose meets the required temperature tolerances as specified by the relevant standard.
Fluid Type: The type of fluid used in the system (e.g., oil, water, chemicals) can affect the hose material’s durability and compatibility. Hydraulic hoses are typically made from materials such as synthetic rubber or thermoplastic, and selecting the right material depends on the fluid type to avoid corrosion or degradation over time.
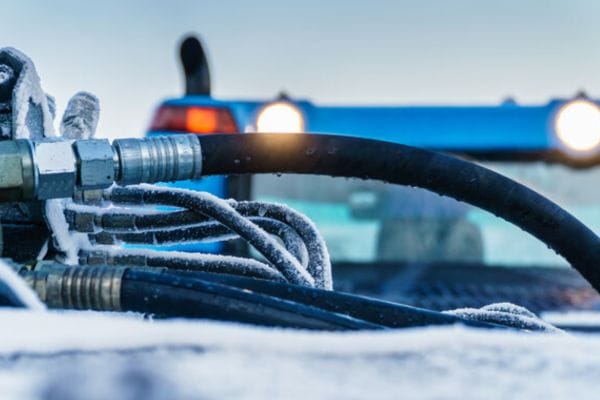
Selecting a Hose That Meets or Exceeds the Required Standard:
Once the application requirements are clear, the next step is to select a hose that meets or exceeds the standards for that specific application. For example, if your system operates under high pressure, choose a hose that complies with high-pressure standards like SAE 100R2 or ISO Class D. Always ensure the hose is rated for the maximum operating pressure, temperature, and fluid type your system will encounter.
Performance Standards: Choose a hose based on the relevant standard (SAE, ISO, EN, DIN) that is commonly used in your industry or region. For example, if you’re operating in Europe, you might select a hose compliant with EN standards, while North American applications might favor SAE standards.
Performance Ratings
Pressure Ratings:
Performance ratings, as dictated by SAE, ISO, EN, and DIN standards, indicate a hose’s ability to withstand specific pressures. Always check the hose’s pressure rating in the standard and ensure it aligns with your system’s maximum operating pressure. For example, SAE standards classify hoses by low, medium, and high pressure, while ISO focuses on performance classes (A-D) to determine pressure capabilities.
Temperature Tolerances:
Each standard will specify a range of temperatures that the hose can withstand while maintaining its integrity. It is important to ensure that the hose you select can handle both the fluid and ambient temperatures in your system without deteriorating.
Impulse Life: Standards like ISO 18752 also include an impulse life rating, which measures how many pressure cycles a hose can withstand before failure. This is particularly important in high-stress applications where the hose is subjected to frequent pressure changes.
Interpreting the Standards:
Standards provide detailed performance ratings for hoses, including burst pressure, working pressure, and temperature limits. These ratings are essential for ensuring that the hose can handle the system’s demands without failure. Make sure to cross-reference these ratings with your system’s requirements to ensure a suitable match.
Hose Construction and Materials
The Role of Materials:
The material of the hose plays a crucial role in meeting specific standards. For instance, hoses made of synthetic rubber are commonly used in hydraulic applications because of their flexibility and resistance to various fluids. However, thermoplastic hoses may be preferred in applications where high chemical resistance or low weight is required.
Selecting the right material also depends on the fluid type. For example, hoses in contact with aggressive chemicals require specific material compositions that prevent degradation. Ensure the material meets the fluid compatibility requirements outlined in the relevant standard.

Reinforcement Layers:
The reinforcement of a hydraulic hose typically consists of braided or spiral wire layers that provide strength and pressure resistance. SAE standards, for example, categorize hoses by the number of reinforcement layers (e.g., single or double wire braid for SAE 100R1 and SAE 100R2, respectively).
Impact on Performance: The reinforcement layer also affects the hose’s flexibility, weight, and ability to withstand high pressures. Heavier-duty applications require hoses with more robust reinforcement layers, such as multi-spiral wire designs, to prevent bursts under high-pressure conditions.
Meeting Different Standards:
Hoses must be constructed to meet the performance criteria established by the applicable standard, whether SAE, ISO, EN, or DIN. The construction requirements are often specific, including the type of material, the number of reinforcement layers, and the method of hose assembly.
Durability and Longevity: The right construction will ensure that the hose remains durable over time, even in harsh environments. A hose with proper materials and reinforcement will also meet or exceed the expected service life as outlined in the standard.
Conclusion
As technology and industrial needs evolve, hydraulic hose standards will continue to change and adapt. Therefore, it’s essential to stay informed and updated on the latest developments in hose specifications. By doing so, you can ensure that your systems remain compliant with current regulations and continue to perform optimally, keeping your operations running efficiently and safely for the long term.
FAQ
What are hydraulic hose standards?
Hydraulic hose standards are guidelines set by organizations like SAE, ISO, EN, and DIN that define the performance, construction, and safety requirements for hydraulic hoses used in various industries.
Why are hydraulic hose standards important?
These standards ensure that hydraulic hoses meet specific safety, performance, and compatibility requirements, reducing the risk of system failures, leaks, or bursts.
What is the difference between SAE and ISO standards?
SAE standards are typically construction-based, focusing on hose materials and layers, while ISO standards are performance-based, categorizing hoses by pressure classes and durability in different environments.
How do I select the right hydraulic hose for my system?
To select the right hose, consider your system’s pressure, temperature, and fluid requirements, and choose a hose that meets or exceeds the standards relevant to your application.
What happens if I use a hose that doesn’t meet the standard?
Using a hose that doesn’t meet the required standard could lead to system failures, such as leaks or bursts, resulting in safety hazards and costly downtime.
How often do hydraulic hose standards change?
Hydraulic hose standards are updated periodically to accommodate advancements in materials, technology, and industry needs. Staying informed on changes ensures compliance and optimal system performance.