Thermoplastic hydraulic hoses represent a significant advancement in hose technology, offering unique benefits over traditional rubber hoses. These hoses are constructed from thermoplastic materials, which are polymers that become pliable when heated and hardened upon cooling. Unlike rubber, which can degrade over time due to exposure to environmental factors, thermoplastic hoses are engineered to resist chemical corrosion, UV radiation, and extreme temperatures. The design and material properties of thermoplastic hoses make them particularly suited for applications where conventional rubber hoses might fail.
Understanding Thermoplastic Materials
A. What Are Thermoplastic Materials?
Thermoplastic materials are a unique class of polymers characterized by their ability to soften when heated and harden upon cooling. This process is entirely reversible, allowing these materials to be reshaped multiple times without significant degradation in their properties. This versatility makes thermoplastics ideal for a variety of manufacturing processes, particularly in the production of hydraulic hoses.
Common thermoplastic polymers used in hydraulic hoses include polyurethane (PU), nylon (PA), and polyester (PET). These materials are selected for their distinct advantages, such as excellent flexibility, high tensile strength, and robust resistance to environmental stressors like abrasion, chemicals, and ultraviolet (UV) radiation. For instance, polyurethane is known for its superior abrasion resistance, making it ideal for applications where the hose may be exposed to harsh physical environments. Nylon, on the other hand, offers excellent thermal stability and chemical resistance, which is critical in hydraulic systems exposed to various fluids and temperature fluctuations.
These materials also contribute to the lightweight nature of thermoplastic hoses, which is a significant advantage in applications requiring ease of handling and installation. The durability of thermoplastics, coupled with their ability to maintain performance in extreme conditions, underscores their growing popularity in demanding industrial applications.
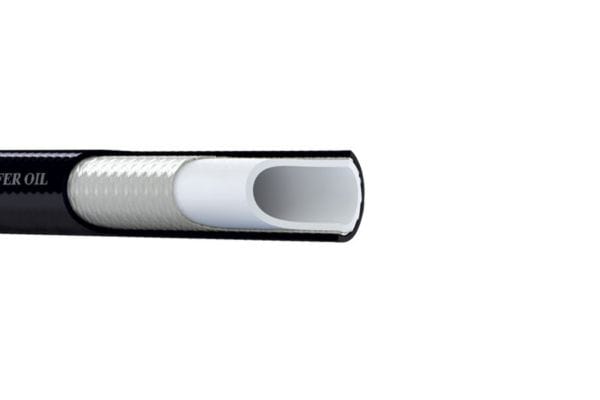
B. Manufacturing Process of Thermoplastic Hoses
The manufacturing process of thermoplastic hoses is a sophisticated procedure that ensures the production of high-performance hoses tailored to specific industrial needs. The process typically involves the following key steps:
Extrusion: The manufacturing begins with the extrusion of the thermoplastic material. In this step, the selected polymer is heated until it becomes pliable and is then forced through a specially designed-die to form the initial shape of the hose. The extrusion process allows for precise control over the hose’s dimensions and wall thickness, ensuring consistency and quality across the production batch.
Reinforcement Layer Addition: To enhance the hose’s mechanical properties, such as tensile strength and pressure resistance, reinforcement layers are added. These layers can consist of synthetic fibers like polyester or aramid, or in some cases, steel wire. The reinforcement is applied in a braided or spiral pattern around the extruded core, providing the hose with the necessary strength to withstand high internal pressures typical of hydraulic systems.
Outer Layer Extrusion: After the reinforcement is applied, a second extrusion process encases the reinforced structure in an outer layer of thermoplastic material. This outer layer acts as a protective barrier, shielding the hose from external factors such as abrasion, chemicals, and environmental conditions like moisture or UV exposure. This final layer is critical for ensuring the longevity and durability of the hose in challenging operating environments.
Cooling and Cutting: Once the hose has been fully formed, it is rapidly cooled to solidify its structure. After cooling, the hose is cut to the desired lengths and subjected to rigorous quality control tests to ensure it meets the required specifications for performance and safety.
C. Comparison with Rubber and Other Hose Materials
When comparing thermoplastic hoses with traditional rubber hoses, several critical differences emerge that influence the choice of material for specific applications.
Weight and Flexibility: Thermoplastic hoses are generally lighter and more flexible than their rubber counterparts. This difference is particularly advantageous in applications where ease of handling, installation, and routing through complex systems are crucial. The flexibility of thermoplastics also reduces the risk of kinking and allows for tighter bend radii, which is beneficial in confined spaces.
Chemical and UV Resistance: Thermoplastic materials excel in environments with high chemical exposure or UV radiation. Unlike rubber, which can degrade or harden over time when exposed to certain chemicals or sunlight, thermoplastics maintain their integrity, offering a longer service life. This makes thermoplastic hoses ideal for outdoor applications or environments where hoses are exposed to aggressive fluids.
Temperature Tolerance: While thermoplastics offer good thermal resistance, rubber hoses typically outperform them in extremely high-temperature applications. Rubber hoses, especially those made from materials like EPDM or nitrile, can withstand higher continuous operating temperatures, making them suitable for specific industrial processes or equipment that generates significant heat.
Permeability and Contamination Risk: Thermoplastic hoses generally have lower permeability compared to rubber, which reduces the risk of fluid leakage and contamination. This property is essential in applications where maintaining fluid purity is critical, such as in the food and pharmaceutical industries.
Environmental Impact: Thermoplastics are often more environmentally friendly due to their recyclability. Rubber, particularly vulcanized rubber, is more challenging to recycle due to its cross-linked molecular structure. The recyclability of thermoplastics not only contributes to sustainability efforts but also aligns with the increasing regulatory and industry focus on reducing environmental footprints.
Key Advantages of Thermoplastic Hoses
A. Superior Flexibility and Lightweight Design
One of the most significant advantages of thermoplastic hoses is their exceptional flexibility and lightweight construction. Compared to traditional rubber hoses, thermoplastic hoses are easier to handle, install, and maneuver, especially in applications where space is limited or where hoses need to be routed through complex systems. The reduced weight also decreases the overall load on the hydraulic system, which can lead to improved fuel efficiency in mobile equipment and ease of installation in stationary systems. The inherent flexibility of thermoplastic materials allows these hoses to bend without kinking, which is critical in ensuring uninterrupted fluid flow and avoiding potential hose damage.
B. Enhanced Chemical and UV Resistance
Thermoplastic hoses offer superior resistance to a wide range of chemicals and environmental factors, including UV radiation. This makes them particularly well-suited for use in harsh environments where rubber hoses might degrade over time. For example, in chemical processing plants or outdoor applications, thermoplastic hoses maintain their structural integrity and performance, even when exposed to aggressive substances or prolonged sunlight. This resistance is due to the molecular structure of the polymers used in these hoses, which are specifically engineered to withstand such conditions. As a result, thermoplastic hoses often outlast rubber hoses in environments with significant chemical exposure or UV radiation, leading to lower maintenance costs and reduced downtime.
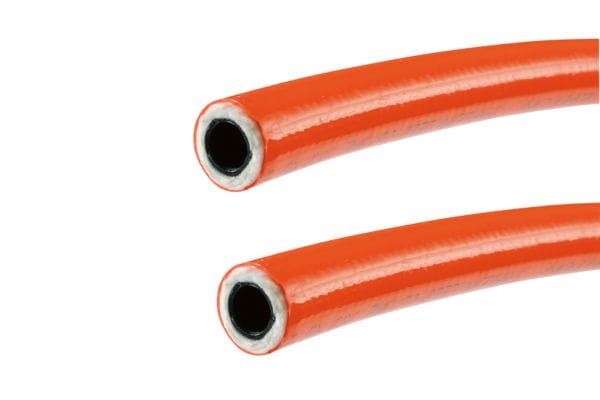
C. High Pressure and Temperature Tolerance
Thermoplastic hoses are designed to operate under high pressure and temperature conditions, making them suitable for demanding industrial applications. While rubber hoses also offer good pressure resistance, thermoplastics provide a more consistent performance over a broader temperature range. This is particularly important in hydraulic systems that experience frequent temperature fluctuations or that are exposed to extreme temperatures. The reinforcement layers within thermoplastic hoses, often made from synthetic fibers or steel, enhance their ability to withstand high internal pressures without compromising flexibility. This combination of pressure tolerance and thermal stability ensures reliable performance in high-stress environments, such as in heavy machinery, automotive systems, and aerospace applications.
D. Reduced Risk of Contamination
The non-permeable nature of thermoplastic materials significantly reduces the risk of contamination in hydraulic systems. Unlike some rubber hoses, which can allow small amounts of fluid or gas to permeate through the hose wall over time, thermoplastic hoses maintain a secure barrier against such leakage. This property is especially critical in industries where contamination control is paramount, such as food processing, pharmaceuticals, and medical device manufacturing. The non-permeable design helps ensure that the hydraulic fluid remains pure, preventing any potential impact on the quality of the end product or the performance of the hydraulic system. Additionally, this characteristic minimizes the environmental impact by preventing leaks that could contaminate the surrounding area.
How to Choose the Right Thermoplastic Hydraulic Hose
A. Assessing Your Application Needs
Selecting the appropriate thermoplastic hydraulic hose begins with a detailed assessment of the specific requirements of your application. This process involves evaluating several critical factors:
Operating Pressure: Determine the maximum operating pressure of your hydraulic system. Thermoplastic hoses are available in various pressure ratings, and selecting a hose that can comfortably handle the system’s peak pressure is crucial to prevent failures and ensure safety. It’s also essential to account for potential pressure surges that could exceed normal operating conditions.
Temperature Range: Consider both the minimum and maximum temperatures to which the hose will be exposed. Thermoplastic hoses are designed to operate efficiently across a range of temperatures, but certain polymers are better suited for extreme heat or cold. For instance, nylon-based hoses offer excellent high-temperature resistance, while polyurethane hoses may perform better in colder environments.
Chemical Exposure: Evaluate the types of fluids that will pass through the hose and any chemicals it may encounter externally. Thermoplastic hoses are generally more resistant to chemicals than rubber hoses, but different polymers offer varying degrees of resistance. Ensuring that the selected hose material is compatible with the hydraulic fluids and potential chemical exposures in your application will prevent premature degradation and extend hose life.
Environmental Conditions: Consider the external environment where the hose will be used. Factors such as UV exposure, humidity, and physical wear (abrasion) should influence your choice. For outdoor applications, hoses with enhanced UV resistance and robust outer layers are recommended to withstand environmental stressors.
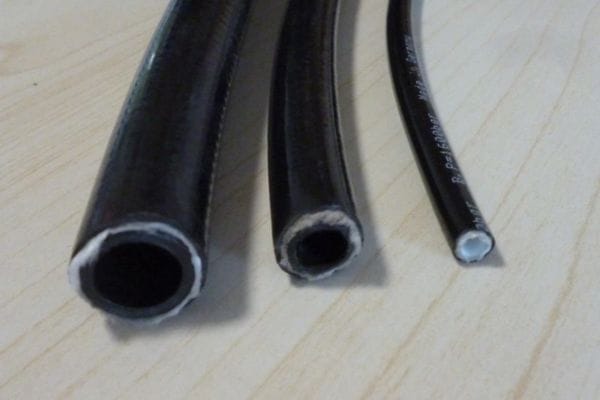
B. Consulting with Suppliers and Manufacturers
Engaging with experienced suppliers and manufacturers is a critical step in the selection process. These professionals can provide valuable insights into the most suitable hose options for your application based on their technical specifications and field performance data. When consulting with suppliers, consider the following:
Pressure and Temperature Ratings: Request detailed information about the hose’s pressure and temperature capabilities. This includes understanding the burst pressure, which is typically several times higher than the operating pressure, and the working temperature range to ensure compatibility with your system’s demands.
Compatibility with System Components: Discuss the compatibility of the hose with existing fittings, connectors, and other system components. Ensuring that the hose integrates seamlessly with your current system is essential to avoid leaks, inefficiencies, or potential failures. Suppliers can also advise on any necessary adapters or modifications.
Customization Options: If your application has unique requirements, inquire about the possibility of custom solutions. Many manufacturers offer customized hose configurations, including specific reinforcement types, outer coatings, or hose lengths tailored to your needs. Customization can optimize hose performance for specialized applications, ensuring a better fit and longer service life.
Supplier Reputation and Support: Consider the reputation of the supplier and the level of technical support they offer. A reliable supplier should provide comprehensive product information, technical assistance, and support services, such as hose assembly and testing. Long-term relationships with reputable suppliers can also facilitate easier procurement and consistent quality.
C. Testing and Validation
Before implementing thermoplastic hoses on a large scale, conducting thorough testing and validation is essential to ensure their performance in real-world conditions. This process should involve several key steps:
Lab Testing: Begin by testing the hose under controlled conditions to verify that it meets the specified performance criteria. This includes pressure tests, temperature exposure tests, and chemical compatibility assessments. Ensure that the hose conforms to relevant industry standards, such as ISO or SAE, which provide benchmarks for safety and performance.
Field Testing: After lab validation, perform field tests by installing the hose in a limited portion of your hydraulic system. Monitor its performance over a designated period, paying attention to any signs of wear, leakage, or failure. Field testing under actual operating conditions is crucial for identifying potential issues that may not be evident in laboratory settings.
Monitoring and Feedback: During the testing phase, continuously monitor the hose’s performance and gather feedback from operators or maintenance personnel. This feedback is invaluable for assessing the hose’s ease of installation, durability, and overall effectiveness in your specific application.
Adjustments and Final Selection: Based on the results of testing and feedback, make any necessary adjustments to the hose selection. This might involve choosing a different material, modifying the reinforcement type, or opting for a different hose size. Once the ideal hose is identified, proceed with full-scale implementation, confident in its ability to meet your application’s demands.
Conclusion
Thermoplastic hoses offer numerous advantages over traditional materials, including superior flexibility, chemical resistance, and recyclability. These benefits make them an excellent choice for a wide range of applications, from industrial machinery to specialized equipment. Given the critical role that hydraulic hoses play in system performance, the importance of material selection cannot be overstated. Thermoplastic hoses represent a significant advancement in hose technology, offering enhanced performance and sustainability.
FAQ
What are thermoplastic hoses made of?
Thermoplastic hoses are made from durable polymers such as polyurethane, nylon, and polyester, which offer flexibility, chemical resistance, and UV protection.
How do thermoplastic hoses compare to rubber hoses?
Thermoplastic hoses are generally lighter, more flexible, and more resistant to chemicals and UV radiation than rubber hoses, making them ideal for demanding environments.
Can thermoplastic hoses handle high pressure?
Yes, thermoplastic hoses are designed to handle high pressure, often with ratings comparable to or exceeding those of traditional rubber hoses, depending on the specific application.
Are thermoplastic hoses suitable for outdoor use?
Yes, thermoplastic hoses are highly resistant to UV radiation and harsh environmental conditions, making them well-suited for outdoor applications.
How do I choose the right thermoplastic hose for my application?
Consider factors such as operating pressure, temperature range, chemical exposure, and environmental conditions. Consulting with suppliers and conducting testing are also key steps in the selection process.
Are thermoplastic hoses recyclable?
Yes, thermoplastic hoses are generally recyclable, which makes them a more environmentally friendly option compared to traditional rubber hoses.