Did you know that a significant percentage of hydraulic system failures can be traced back to improper reassembly of fittings? Studies suggest that up to 30% of hydraulic leaks are due to issues related to reassembling fittings, leading to costly downtime and potential safety hazards. This statistic underscores a critical question: How many times can you safely reassemble a hydraulic fitting before it becomes a liability?
Understanding Hydraulic Fittings
Types of Hydraulic Fittings
JIC Fittings:
JIC fittings are widely used due to their reliable, high-pressure capabilities. They feature a 37-degree flare seating surface that forms a strong seal when the fitting is tightened. JIC fittings are versatile, and commonly found in fluid power systems across many industries, including agriculture, automotive, and industrial machinery.
BSP Fittings:
BSP fittings are prevalent in Europe and the UK, offering a threaded connection that can be either tapered (BSPT) or parallel (BSPP). These fittings are known for their robust sealing properties, especially when paired with an O-ring or bonded seal, making them ideal for applications where pressure integrity is critical.
ORFS Fittings:
ORFS fittings provide a reliable, leak-free connection by utilizing an O-ring embedded in the face of the fitting. These are particularly useful in applications where vibration or thermal cycling might otherwise cause fittings to loosen, such as in heavy equipment or hydraulic power units.
Face Seal Fittings:
Face seal fittings, such as SAE Straight Thread O-Ring Boss (ORB), offer a leak-proof connection ideal for high-pressure applications. They rely on an O-ring seated in a groove to create a tight seal, minimizing the risk of fluid leaks even under extreme conditions.
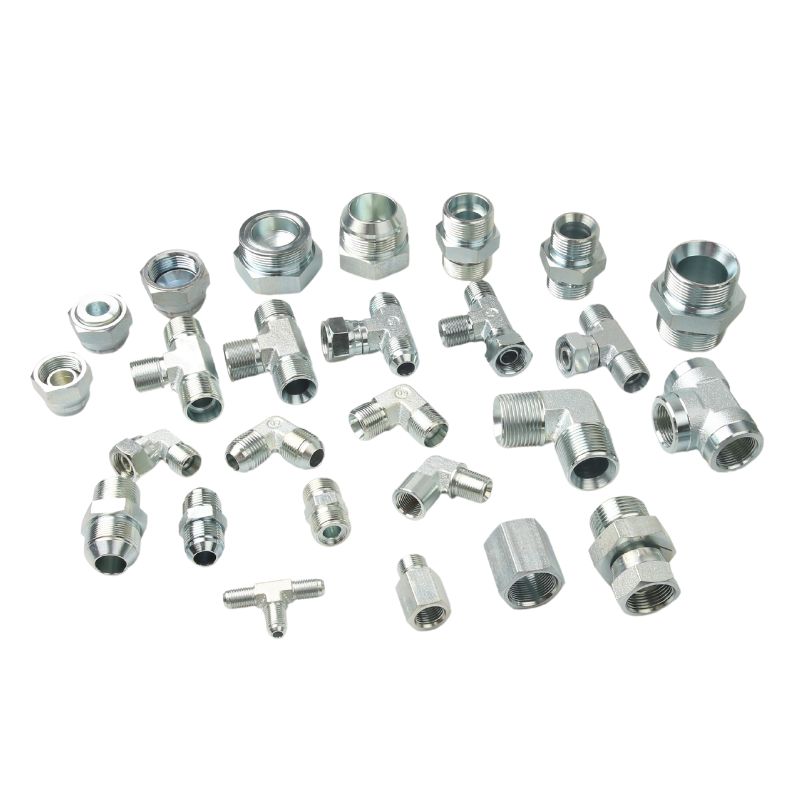
Materials Used in Manufacturing Fittings
The material composition of hydraulic fittings plays a crucial role in their performance, durability, and suitability for specific applications. Common materials include:
Steel:
Steel fittings are strong, durable, and capable of withstanding high pressures. They are commonly used in industrial and heavy machinery applications. However, they can be susceptible to corrosion, which is why they are often coated with zinc or other protective finishes.
Stainless Steel:
Stainless steel fittings offer superior corrosion resistance, making them ideal for applications in harsh environments, such as marine, chemical processing, or food and beverage industries. While more expensive than regular steel, their longevity and performance in corrosive environments justify the cost.
Brass:
Brass fittings are commonly used in lower-pressure applications, particularly in industries like plumbing, where their resistance to corrosion from water is advantageous. They are also easier to machine, which makes them a cost-effective option for certain applications.
Aluminum:
Aluminum fittings are lightweight and corrosion-resistant, often used in aerospace and automotive applications where weight reduction is crucial. However, they are not as strong as steel or stainless steel, limiting their use in high-pressure systems.
Function and Role in Hydraulic Systems
How Fittings Contribute to System Integrity:
Hydraulic fittings are the connectors that link hoses, pipes, and tubes within a hydraulic system. They play a critical role in maintaining the system’s integrity by ensuring a leak-free, secure connection that can withstand the pressures and temperatures generated by the hydraulic fluid. The effectiveness of a hydraulic system depends on the reliability of these fittings, as even a minor leak can lead to significant system inefficiencies, contamination, or failure.
The design of hydraulic fittings, including their threading, sealing surfaces, and materials, is tailored to specific pressure ranges and fluid types. This specificity helps prevent issues such as fluid loss, pressure drops, or fitting blowouts, which can have catastrophic consequences in high-stakes environments like manufacturing plants or aircraft systems.
Importance of Proper Installation and Assembly:
The installation and assembly of hydraulic fittings are just as critical as their selection. Proper installation ensures that the fitting is seated correctly, with appropriate torque applied to create a secure, leak-free connection. Misalignment, over-tightening, or under-tightening during assembly can lead to compromised seals, resulting in leaks or fitting failure under pressure.
Additionally, the use of appropriate tools and adherence to manufacturer guidelines during installation cannot be overstated. For instance, using a torque wrench ensures that the fitting is neither too loose, risking leaks, nor too tight, which could damage the fitting or the connected component.
The Reassembly Process Explained
What is Reassembly?
Reassembly of hydraulic fittings refers to the process of disassembling and then reassembling the components of a hydraulic fitting to restore or maintain the integrity of the hydraulic system. Reassembly is often required during routine maintenance, repairs, or when modifications to the hydraulic system are necessary. Common scenarios include replacing worn-out seals, adjusting hose lengths, or reconfiguring connections to accommodate system changes.
Reassembly is crucial in ensuring that the hydraulic system continues to operate efficiently and without leaks. However, the process requires careful attention to detail, as improper reassembly can lead to compromised fitting integrity, resulting in leaks, reduced performance, or even system failure.
Steps Involved in Reassembling Hydraulic Fittings
Preparation:
Gather Tools and Equipment: Before beginning, ensure you have the appropriate tools for disassembly and reassembly, such as wrenches, torque tools, and lubricant if required.
Depressurize the System: Always start by depressurizing the hydraulic system to prevent fluid spray or injury. Disconnect the system from its power source and ensure all pressure has been safely released.
Disassembly:
Loosen the Fitting: Using the appropriate wrench, carefully loosen the fitting by turning it counterclockwise. Avoid applying excessive force that could damage the threads.
Remove the Fitting Components: Once loosened, gently separate the fitting components, including the body, nut, and any seals or O-rings.
Inspect the Components: Examine each component for signs of wear, damage, or corrosion. Replace any parts that show signs of deterioration.
Preparation for Reassembly:
Clean the Components: Thoroughly clean all fitting components to remove any dirt, debris, or old lubricant. This ensures a proper seal and prevents contamination of the hydraulic fluid.
Lubricate Threads and Seals: Apply a small amount of hydraulic fitting lubricant to the threads and seals, if recommended by the manufacturer. This helps achieve the correct torque during reassembly and reduces the risk of galling (thread damage).
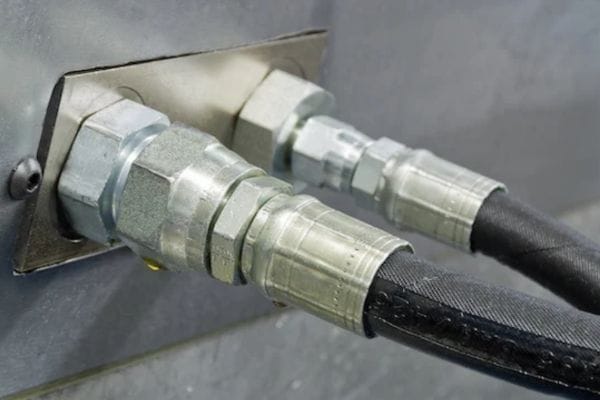
Reassembly:
Reposition the Components: Carefully place the fitting components back in their original positions. Ensure that any seals or O-rings are seated correctly and that the threads are aligned.
Tighten the Fitting: Using a wrench, tighten the fitting by turning it clockwise. Follow the manufacturer’s recommended torque specifications to avoid overtightening or under-tightening. If using a torque wrench, ensure it is calibrated correctly.
Testing:
Check for Leaks: Once reassembly is complete, gradually reintroduce pressure to the system while monitoring the fitting for any signs of leakage.
Final Adjustments: If necessary, make minor adjustments to the fitting to achieve a leak-free connection. Recheck the torque if adjustments are made.
Common Mistakes During Reassembly
Overtightening:
Overapplying torque to a hydraulic fitting can damage the threads, crush seals, and distort the fitting body. This not only compromises the seal but can also lead to premature failure of the fitting.
Improper Alignment:
Misalignment of the fitting components during reassembly is a common mistake that can lead to cross-threading. Cross-threading damages both the fitting and the connected component, making it difficult to achieve a secure seal and increasing the risk of leaks.
Reuse of Damaged Seals:
Reusing seals or O-rings that are worn, cracked, or deformed is a frequent error. Even minor imperfections in these components can prevent a proper seal, leading to fluid leaks and potential system failure.
Inadequate Cleaning:
Failing to thoroughly clean the fitting components before reassembly can introduce contaminants into the hydraulic system. Dirt, debris, or old lubricant can prevent a proper seal and cause wear on the system over time.
Incorrect Torque Application:
Using incorrect torque during reassembly—whether too little or too much—can lead to leaks or damage. It’s essential to follow the manufacturer’s guidelines precisely to ensure a secure and durable connection.
Factors Influencing Reassembly Limits
Material Wear and Tear
Steel:
Steel fittings are known for their strength and durability, making them capable of withstanding multiple reassemblies without significant wear. However, repeated reassembly can still cause minor thread deformation or galling, especially if proper lubrication is not used. Over time, these issues can compromise the seal, leading to leaks.
Stainless Steel:
Stainless steel is highly resistant to corrosion and wear, which can extend the number of times it can be reassembled. However, stainless steel is also prone to galling—a form of adhesive wear that occurs when metal surfaces slide against each other under pressure. To mitigate this, it’s essential to use proper lubricants and avoid overtightening during reassembly.
Brass:
Brass fittings are softer than steel or stainless steel, which makes them more susceptible to wear and deformation after multiple reassemblies. While brass is corrosion-resistant and easier to machine, repeated reassembly can quickly wear down the threads and sealing surfaces, reducing the fitting’s effectiveness over time.
Aluminum:
Aluminum fittings are lightweight and corrosion-resistant but also softer and more prone to wear than steel or stainless steel. After several reassemblies, aluminum fittings may show significant thread wear, making it difficult to achieve a reliable seal. Due to this, aluminum fittings generally have a lower reassembly tolerance and may need to be replaced more frequently.
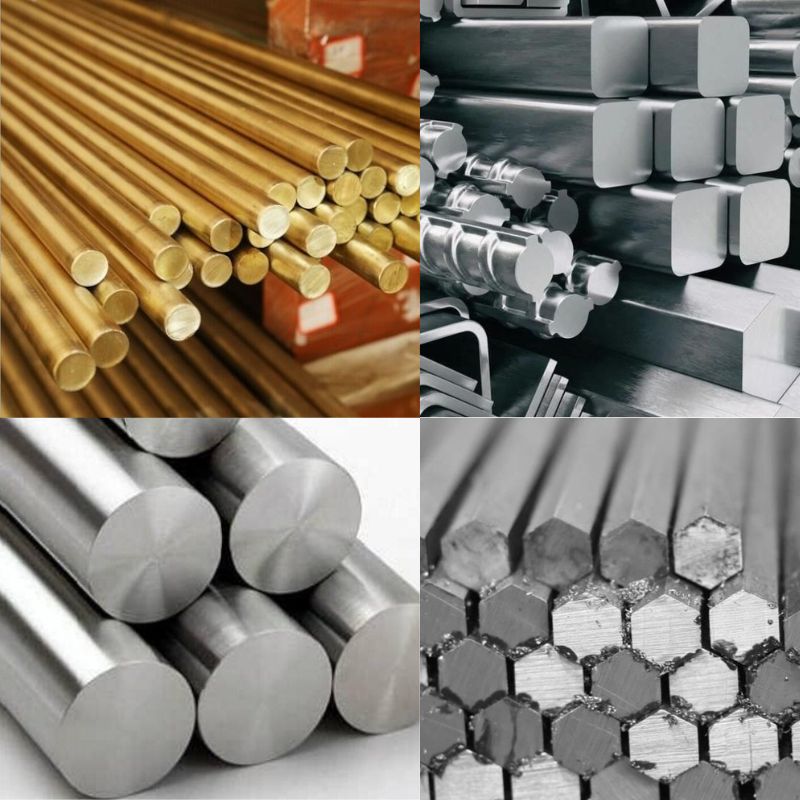
Signs of Wear That Indicate a Fitting Should Not Be Reused
Recognizing the signs of wear on a hydraulic fitting is crucial for determining whether it’s safe to reassemble or if it should be replaced. Common indicators that a fitting should not be reused include:
Thread Damage:
Visible thread wear, such as rounding, flattening, or galling, suggests that the fitting may no longer create a secure seal. Damaged threads can also lead to cross-threading during reassembly, further compromising the fitting.
Deformed Seals or O-Rings:
Seals and O-rings that appear cracked, flattened, or hardened are no longer effective at preventing leaks. These components should be replaced rather than reused.
Corrosion:
Any signs of corrosion on the fitting, especially near the sealing surfaces or threads, indicate that the fitting’s integrity has been compromised. Corroded fittings are more likely to leak and should be replaced immediately.
Surface Cracks or Deformation:
Inspect the fitting body for any visible cracks or deformities. Even minor cracks can expand under pressure, leading to sudden fitting failure.
Type of Fitting
Compression Fittings:
Compression fittings rely on a compression ring or ferrule to create a seal. Repeated reassembly can cause the ferrule to deform, reducing its ability to seal effectively. Therefore, compression fittings generally have a lower reassembly tolerance, and the ferrule often needs to be replaced after a few reassemblies.
Flare Fittings:
Flare fittings use a cone-shaped end that flares out to fit against a corresponding surface. These fittings can generally withstand more reassemblies than compression fittings, as long as the flared surface remains undamaged. However, excessive reassembly can lead to metal fatigue in the flare, making it less effective at sealing.
O-Ring Face Seal (ORFS) Fittings:
ORFS fittings are designed for high-pressure applications and use an O-ring to create a leak-proof seal. While these fittings can typically be reassembled multiple times, the O-ring is a worn component that may need to be replaced with each reassembly to maintain a reliable seal.
Pipe Thread Fittings:
Pipe thread fittings rely on the threads themselves to create a seal, often with the addition of thread sealant or tape. Repeated reassembly can cause the threads to wear down, particularly in softer materials like brass or aluminum. The use of sealant can also make reassembly challenging, as residual sealant can cause improper seating of the threads.
Pressure and Temperature Conditions
How the Operational Environment Affects the Reusability of Fittings:
The operational conditions—particularly the pressure and temperature—under which a hydraulic fitting is used significantly impact its reusability. High-pressure environments place additional stress on fittings, particularly on the sealing surfaces and threads. Over time, this stress can lead to deformation, making the fitting less effective at sealing after multiple reassemblies.
High-Pressure Environments:
In systems operating under high pressure, the forces acting on the fittings are much greater, increasing the risk of thread wear and seal degradation during reassembly. Fittings in these environments may have a lower reassembly tolerance and require more frequent inspection and replacement.
Temperature Extremes:
Extreme temperatures—both high and low—can affect the materials used in hydraulic fittings. High temperatures can cause metal expansion and O-ring degradation, while low temperatures can make materials brittle. These effects can reduce the number of times a fitting can be safely reassembled, particularly if the fitting is repeatedly exposed to these conditions.
Vibration and Shock:
Fittings in environments with high vibration or shock loads are subject to additional wear during reassembly. Vibration can loosen connections over time, and repeated tightening can lead to over-torquing, which damages the fitting.
Application-Specific Considerations
Construction Industry:
In construction, hydraulic systems are often exposed to harsh environments, including dirt, dust, and extreme weather conditions. Fittings in these systems may require more frequent reassembly due to maintenance needs, but the harsh conditions also increase wear, limiting the number of safe reassemblies.
Manufacturing Industry:
In manufacturing, hydraulic systems are typically operated in controlled environments. Fittings may not need to be reassembled as frequently, and when they are, the controlled conditions help extend the reassembly limit. However, the precision required in manufacturing systems means that even slight wear can necessitate replacement rather than reassembly.
Aerospace Industry:
The aerospace industry has extremely stringent requirements for hydraulic fittings, with a focus on reliability and safety. Fittings in aerospace applications may have very low reassembly limits, as the risk associated with failure is too high. In many cases, fittings are replaced rather than reassembled to ensure maximum reliability.
Agricultural Industry:
Agricultural machinery often operates in environments with high levels of dirt, debris, and moisture. Fittings in these systems may be subject to frequent disassembly for cleaning and maintenance, which can limit their reassembly lifespan. The combination of harsh environmental conditions and frequent maintenance cycles means that fittings in agriculture may require more regular replacement.
Risks Associated with Repeated Reassembly
Potential for Leaks
How Reassembly Can Affect the Seal and Lead to Leaks:
One of the most significant risks associated with repeated reassembly of hydraulic fittings is the potential for leaks. Each time a fitting is reassembled, there is a chance that the seal will be compromised, especially if the fitting is not handled with care or if the components have started to wear.
During reassembly, the threads, seals, and seating surfaces are subjected to mechanical stress. Over time, this stress can cause subtle deformations in the threads or flattening of the O-rings and seals, leading to an imperfect fit. Even a minor imperfection can result in fluid leaks, which are particularly problematic in high-pressure hydraulic systems where even small leaks can lead to significant fluid loss and pressure drops.
Moreover, the use of improper torque during reassembly—either too much or too little—can exacerbate this issue. Overtightening can crush seals and damage threads, while under-tightening may not provide a sufficient seal, both leading to potential leaks.
Reduced Fitting Reliability
The Impact on Performance and Safety:
Repeated reassembly does not just increase the risk of leaks; it can also reduce the overall reliability of the hydraulic fitting. Hydraulic fittings are designed to create a secure and leak-proof connection under specific conditions. Each reassembly weakens the fitting’s ability to maintain this connection, particularly if the fitting has already experienced wear and tear.
Reduced reliability manifests in several ways:
Loss of Structural Integrity: The threads and seals may not engage as tightly as they did during the initial assembly, leading to a less secure connection that is more susceptible to loosening under pressure or vibration.
Inconsistent Performance: A fitting that has been reassembled multiple times may no longer maintain consistent pressure levels within the system, leading to fluctuations in system performance and efficiency.
Safety Hazards: In critical applications, such as in aerospace or industrial machinery, reduced fitting reliability can pose significant safety risks. A sudden fitting failure can lead to system shutdowns, fluid spills, or even catastrophic accidents, especially if the system is operating under high pressure.
Conclusion
To maintain the integrity and reliability of your hydraulic systems, make it a routine to inspect your fittings regularly and follow best practices for reassembly. Don’t wait for a failure to occur—be proactive in replacing worn or damaged fittings. By doing so, you can prevent leaks, avoid costly downtime, and ensure the safety of your operations. Remember, the key to a long-lasting hydraulic system lies in attention to detail and a commitment to quality maintenance practices.
FAQ
How many times can I reassemble a hydraulic fitting?
The number of times a hydraulic fitting can be safely reassembled depends on the material, type of fitting, and the conditions under which it operates. Regular inspections are crucial to determine if a fitting is still suitable for reuse.
What are the signs that a hydraulic fitting should not be reused?
Signs include visible thread damage, deformed or cracked seals, corrosion, and any surface cracks or deformations in the fitting body.
Can I reuse the same O-ring when reassembling a fitting?
It’s generally recommended to replace the O-ring each time a fitting is reassembled to ensure a reliable seal and prevent leaks.
What happens if I overtighten a hydraulic fitting during reassembly?
Overtightening can damage the threads, crush seals, and lead to leaks or fitting failure. Always use the recommended torque specifications.
Is it safe to reassemble hydraulic fittings in high-pressure systems?
Reassembly in high-pressure systems should be done with caution. Fittings in these environments are under greater stress, and repeated reassembly can increase the risk of failure. Inspect carefully and replace fittings as needed.
How can I prevent leaks when reassembling hydraulic fittings?
Ensure that all components are clean, and properly aligned and that the correct torque is applied. Replace any worn or damaged parts, including seals, to maintain a secure, leak-free connection.