This guide offers a detailed comparison between nylon and stainless steel braided hose, focusing on their composition, characteristics, advantages, and limitations. It aims to help professionals like engineers and technicians make informed decisions by exploring key factors such as durability, flexibility, and cost-effectiveness. By the end, you will have a clear understanding of which hose type is best suited for their specific industrial applications, along with practical tips for installation and maintenance.
Understanding Nylon Braided Hoses
A. Composition and Structure
Nylon Braided Hoses are a type of flexible hose that features a reinforced outer layer made from braided nylon fibers. The core of these hoses is typically made from a thermoplastic elastomer or rubber material, which provides the necessary flexibility and durability. The nylon braiding is tightly woven around the inner core, serving as a protective layer that enhances the hose’s strength and resistance to pressure. This braided structure not only prevents the hose from expanding under pressure but also provides additional abrasion resistance, making it suitable for various demanding environments. The inner core and outer braiding work together to create a hose that is both flexible and robust, ideal for dynamic applications.
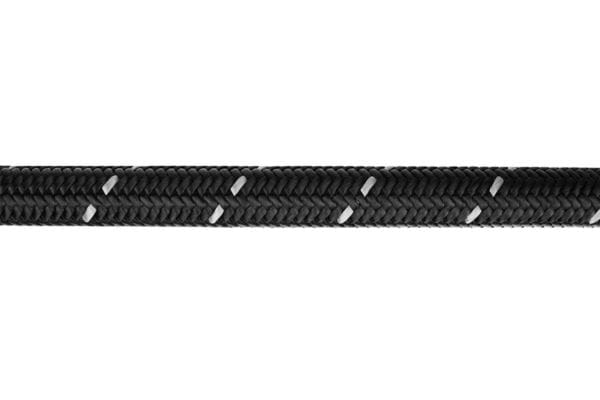
B. Key Characteristics
Nylon Braided Hoses are known for their unique combination of flexibility, lightweight, and durability. These hoses are highly flexible, which makes them easy to install and route through complex systems. The lightweight nature of nylon also contributes to ease of handling and reduces the overall load on the system.
In terms of temperature resistance, Nylon Braided Hoses can typically withstand moderate temperature ranges, making them suitable for applications where extreme heat or cold is not a factor. Additionally, these hoses offer good chemical compatibility, resisting many oils, fuels, and solvents, though they may not be suitable for highly corrosive substances.
There are variations in Nylon Braided Hoses based on the grade of nylon used. Higher grades may offer enhanced strength, abrasion resistance, and longevity. For instance, some hoses may use Nylon 6 or Nylon 6/6, which are known for their superior mechanical properties and better resistance to wear and tear.
C. Common Applications
Nylon Braided Hoses are widely used in industries that require flexible and durable fluid transfer solutions. In the automotive industry, they are often employed in fuel lines, brake systems, and power steering systems due to their resistance to fuel and oil. These hoses are also common in hydraulic systems where moderate pressure and flexibility are required, making them ideal for machinery and equipment that operate under dynamic conditions.
In the industrial sector, Nylon Braided Hoses are used for pneumatic lines, cooling systems, and general fluid transfer applications. Their flexibility and resistance to chemicals make them suitable for environments where hoses need to be routed through tight spaces or exposed to various chemicals.
D. Advantages
One of the primary advantages of Nylon Braided Hoses is their cost-effectiveness. Compared to other types of braided hoses, nylon offers a balance between performance and price, making it an economical choice for many applications. The flexibility of these hoses is another significant benefit, allowing them to be easily installed in complex systems without the risk of kinking or breaking.
Their lightweight nature further adds to their appeal, reducing the overall weight of the system they are installed in and making them easier to handle during installation and maintenance. Additionally, the abrasion resistance provided by the nylon braiding ensures a longer service life, especially in environments where the hose might be exposed to mechanical wear.
E. Disadvantages
Despite their many advantages, Nylon Braided Hoses also have some limitations. One of the main drawbacks is their lower temperature tolerance compared to hoses made from more heat-resistant materials like stainless steel. This makes them less suitable for applications involving extreme temperatures, such as in high-performance engines or industrial settings with high thermal loads.
Another potential issue is the wear and tear over time, especially in environments where the hose is exposed to harsh chemicals or continuous mechanical stress. While nylon braiding offers some protection, it may not be sufficient in highly abrasive or corrosive environments, leading to premature failure.
Additionally, Nylon Braided Hoses may not be the best choice for high-pressure applications, as they are generally designed for moderate pressure ranges. In situations where high pressure is a constant factor, stainless braided hoses or other more robust materials may be necessary to ensure safety and reliability.
Understanding Stainless Braided Hoses
A. Composition and Structure
Stainless Braided Hoses are composed of an inner core made from flexible materials such as rubber, PTFE (Polytetrafluoroethylene), or other thermoplastics, surrounded by an outer layer of stainless steel braiding. The inner core is responsible for containing the fluid and maintaining flexibility, while the stainless steel braiding provides reinforcement, significantly enhancing the hose’s strength and durability. The braiding is usually made from high-grade stainless steel, which offers excellent resistance to corrosion and wear. The layered structure, with the inner core providing fluid transport and the outer steel braid offering protection and strength, results in a hose that can withstand high pressures and extreme conditions.
B. Key Characteristics
Stainless Braided Hoses are known for their exceptional strength and durability. The stainless steel braiding reinforces the hose, allowing it to handle high pressure without expanding or bursting. This makes these hoses ideal for applications where safety and reliability are paramount.
The temperature resistance of Stainless Braided Hoses is another critical characteristic. These hoses can withstand a wide range of temperatures, from very low to extremely high, making them suitable for use in environments where thermal stability is crucial. The stainless steel braiding also provides excellent resistance to abrasion, cutting, and other mechanical stresses, ensuring a long service life even in demanding conditions.
In addition, Stainless Braided Hoses are highly resistant to corrosion, especially when exposed to harsh chemicals or environmental factors like saltwater. This corrosion resistance is particularly important in industries like marine and chemical processing, where exposure to corrosive elements is common.
Variations in Stainless Braided Hoses arise from the different grades of stainless steel used. For example, hoses made with 304 stainless steel offer good corrosion resistance and strength, while those made with 316 stainless steel provide even greater corrosion resistance, especially in chloride-rich environments. These variations allow for customization based on the specific needs of the application.
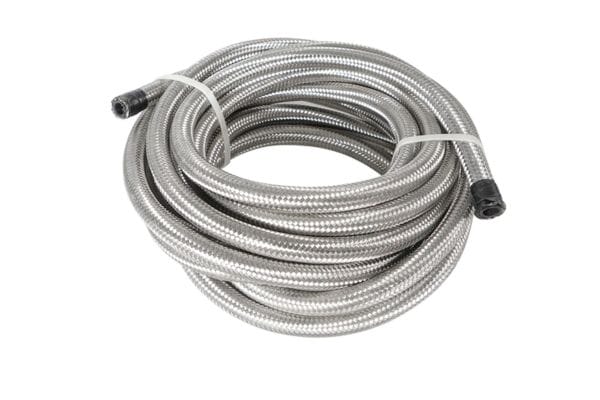
C. Common Applications
Stainless Braided Hoses are widely used in industries that demand high performance under extreme conditions. In the aerospace industry, these hoses are used for hydraulic lines, fuel systems, and other critical applications where both high pressure and temperature resistance are required.
In high-performance automotive systems, Stainless Braided Hoses are employed in brake lines, fuel lines, and turbocharger systems. Their ability to withstand high pressure and extreme temperatures makes them ideal for these demanding applications, where failure is not an option.
Other common applications include industrial machinery, where Stainless Braided Hoses are used to transport high-pressure fluids and gases, and in chemical processing plants, where their resistance to corrosive chemicals ensures long-term reliability.
D. Advantages
The primary advantage of Stainless Braided Hoses is their superior strength and durability. The stainless steel braiding provides excellent reinforcement, allowing the hose to withstand high pressures without the risk of bursting or failure. This makes them particularly suitable for safety-critical applications in industries like aerospace and automotive.
Another significant benefit is their high-pressure tolerance. Stainless Braided Hoses can handle much higher pressures than many other types of hoses, making them ideal for applications where pressure is a critical factor. Their long lifespan also contributes to their cost-effectiveness, as they require less frequent replacement compared to other hose types.
Stainless Braided Hoses are also highly resistant to both corrosion and abrasion, ensuring that they can be used in harsh environments without degrading over time. This makes them a reliable choice for industries where exposure to corrosive chemicals or mechanical wear is common.
E. Disadvantages
Despite their many advantages, Stainless Braided Hoses do have some limitations. One of the most significant drawbacks is their higher cost compared to other hose types, such as Nylon Braided Hoses. The use of high-grade stainless steel and the manufacturing process involved in creating these hoses contribute to their higher price point.
Another limitation is their reduced flexibility. While stainless steel braiding provides excellent strength and protection, it also makes the hose less flexible than other types, such as Nylon Braided Hoses. This can make installation more challenging, especially in tight or complex spaces where greater flexibility is needed.
Nylon vs Stainless Steel Braided Hoses
A. Flexibility and Ease of Installation
Nylon Braided Hoses: Nylon Braided Hoses are highly regarded for their flexibility. The nylon outer layer provides a degree of pliability that makes these hoses easy to handle and install, even in tight or complex spaces. The flexibility is particularly beneficial in applications where the hose needs to be routed around obstacles or fitted into compact areas. The bend radius of Nylon Braided Hoses is typically smaller, meaning they can bend more tightly without kinking, which is a significant advantage during installation.
In addition, the lightweight nature of nylon makes these hoses easier to work with. Installers can maneuver and position the hose with minimal effort, reducing the time and labor required for installation. This ease of handling is especially advantageous in applications where multiple hoses need to be installed, or where frequent maintenance and replacements are necessary.
Stainless Braided Hoses: In contrast, Stainless Braided Hoses are less flexible due to the rigidity of the stainless steel braiding. While this braiding offers superior strength and protection, it also reduces the hose’s ability to bend and flex. The bend radius for Stainless Braided Hoses is larger, meaning they require more space to achieve a bend without kinking. This can make installation more challenging, especially in confined spaces or systems with complex routing.
The weight of Stainless Braided Hoses further complicates installation. The added heft from the stainless steel makes these hoses harder to handle, requiring more effort and potentially more time to install correctly. Installers may need additional tools or support to position the hoses properly, particularly in more extensive systems.
B. Temperature and Pressure Tolerance
Nylon Braided Hoses: Nylon Braided Hoses are designed to operate effectively within moderate temperature and pressure ranges. Typically, these hoses can handle temperatures from -40°C to 100°C, making them suitable for most standard industrial applications. However, they may not perform as well in extreme temperature environments, such as those involving intense heat or freezing conditions. The nylon material, while durable, can become brittle at very low temperatures and may soften or degrade under high heat.
In terms of pressure tolerance, Nylon Braided Hoses are generally rated for moderate pressure applications. They can handle pressures ranging from 500 to 3000 psi, depending on the specific design and construction. While sufficient for many applications, they may not be the best choice for systems that experience high-pressure spikes or sustained high-pressure conditions.
Stainless Braided Hoses: Stainless Braided Hoses, on the other hand, excel in both temperature and pressure tolerance. These hoses are capable of withstanding extreme temperatures, typically ranging from -73°C to 260°C or higher, depending on the materials used in the inner core. This makes them ideal for applications in harsh environments, such as those found in aerospace or high-performance automotive systems where temperatures can vary widely and rapidly.
In terms of pressure, Stainless Braided Hoses can handle significantly higher pressures compared to their nylon counterparts. They are often rated for pressures exceeding 3000 psi and can go much higher depending on the specific design. This makes them suitable for high-pressure systems where safety and reliability are paramount.
C. Chemical and Environmental Resistance
Nylon Braided Hoses: Nylon Braided Hoses offer good resistance to a wide range of chemicals, including many oils, fuels, and solvents. This makes them suitable for use in environments where they may be exposed to such substances. However, nylon can be susceptible to certain chemicals, particularly strong acids and bases, which can cause degradation over time. Additionally, nylon is somewhat hygroscopic, meaning it can absorb moisture from the environment, which can affect its mechanical properties and lead to swelling or other issues over time.
In terms of environmental resistance, Nylon Braided Hoses provide decent protection against UV radiation, though prolonged exposure to sunlight can cause the material to degrade, leading to brittleness and cracking. Nylon hoses are also resistant to abrasion, though not to the same extent as stainless steel, and they offer limited protection against mechanical damage.
Stainless Braided Hoses: Stainless Braided Hoses are highly resistant to a broad range of chemicals, including many corrosive substances that would quickly degrade other materials. The stainless steel braiding provides a robust barrier against chemical attack, ensuring the hose’s integrity even in aggressive environments. This makes them ideal for use in chemical processing plants, marine environments, and other settings where exposure to harsh chemicals is common.
Environmental resistance is another strong point for Stainless Braided Hoses. They are impervious to UV radiation, making them suitable for outdoor use in direct sunlight without the risk of degradation. The stainless steel braiding also provides exceptional resistance to abrasion, cutting, and other forms of mechanical damage, ensuring a long lifespan even in harsh conditions.
Choosing the Right Hose for Your Needs
A. Assessing Application Requirements
Application Type:
Identify the primary function of the hose within your system. Is it for fluid transfer, gas conveyance, or another purpose? Different applications may require hoses with specific characteristics, such as high flexibility or resistance to certain chemicals.
Environmental Conditions:
Consider the environmental conditions in which the hose will operate. Will it be exposed to extreme temperatures, direct sunlight, or abrasive materials? Understanding the environmental demands will help determine whether a Nylon or Stainless Braided Hose is more suitable.
Pressure and Temperature Requirements:
Evaluate the pressure and temperature conditions that the hose will need to withstand. If the application involves high-pressure fluids or extreme temperatures, the hose’s tolerance levels must match these demands to ensure safety and reliability.
Chemical Compatibility:
Determine the types of fluids or gases that the hose will carry. Some chemicals can degrade certain materials over time, so it’s crucial to choose a hose with the appropriate chemical resistance.
Flexibility and Installation:
Assess the installation environment to determine the importance of hose flexibility. If the hose needs to be routed through tight or complex spaces, a more flexible hose like a Nylon Braided Hose might be necessary.
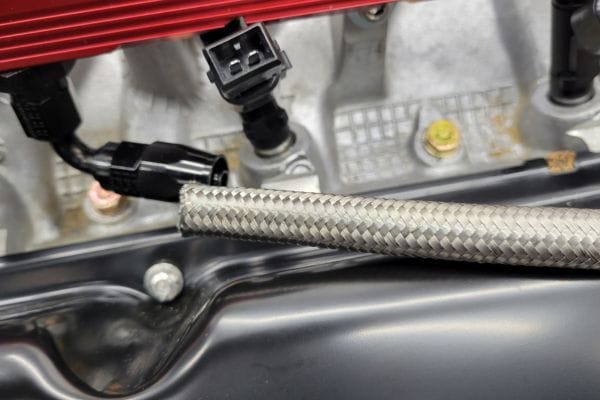
B. Decision-Making Criteria
Strength and Durability:
Stainless Braided Hoses: Choose this option if your application requires maximum strength and durability, especially in environments where the hose will be exposed to high pressure, abrasion, or mechanical stress.
Nylon Braided Hoses: Opt for this if the application does not demand extreme durability, and where flexibility and ease of handling are more critical.
Temperature and Pressure Tolerance:
Stainless Braided Hoses: Ideal for applications involving high temperatures and pressures. Their superior temperature and pressure tolerance make them suitable for use in extreme conditions.
Nylon Braided Hoses: Better suited for moderate temperature and pressure environments where extreme conditions are not a concern.
Chemical and Environmental Resistance:
Stainless Braided Hoses: Select this hose type for applications where exposure to harsh chemicals, corrosive environments, or UV radiation is expected. Their robust resistance to environmental factors ensures a longer lifespan in such conditions.
Nylon Braided Hoses: Consider these for applications with less exposure to aggressive chemicals and environmental factors. They are effective for many industrial uses but may not be as resilient in harsher environments.
Flexibility and Ease of Installation:
Nylon Braided Hoses: Choose these if flexibility and ease of installation are top priorities. Their lightweight and pliable nature make them ideal for complex routing in tight spaces.
Stainless Braided Hoses: Consider these when flexibility is less important than strength and durability. While they are more challenging to install, they offer unmatched protection and performance in demanding applications.
Conclusion
As you evaluate your hose requirements, take the time to thoroughly assess your application’s unique demands. Don’t hesitate to consult with a professional or supplier who can provide expert advice tailored to your specific needs. Ensuring that you choose the right hose type will not only optimize your system’s performance but also enhance safety and reduce maintenance costs in the long run. For further guidance or to discuss your options, reach out to our team of experts who are ready to assist you in finding the perfect solution for your application.
FAQ
What are the main differences between Nylon and Stainless Braided Hoses?
Nylon Braided Hoses are more flexible and lightweight, while Stainless Braided Hoses offer superior strength, durability, and higher resistance to extreme temperatures and pressures.
Which hose type is better for high-pressure applications?
Stainless Braided Hoses are better suited for high-pressure applications due to their reinforced stainless steel braiding.
Are Nylon Braided Hoses suitable for outdoor use?
Nylon Braided Hoses can be used outdoors but may degrade over time with prolonged exposure to UV radiation.
Can Stainless Braided Hoses resist chemical corrosion?
Yes, Stainless Braided Hoses have excellent chemical resistance, making them ideal for environments with harsh chemicals.
Which hose is easier to install in tight spaces?
Nylon Braided Hoses are easier to install in tight spaces due to their flexibility and smaller bend radius.
What factors should I consider when choosing between Nylon and Stainless Braided Hoses?
Consider factors such as pressure and temperature requirements, chemical exposure, flexibility needs, and budget when choosing between the two hose types.