Hydraulic quick couplers are specialized connectors designed to facilitate the rapid and secure joining and disjoining of hydraulic lines without the need for manual intervention or the use of tools. These couplers are integral components in hydraulic systems, allowing operators to swiftly switch between different tools or machinery parts, thereby minimizing downtime and enhancing operational efficiency. Typically consisting of a male and female connector, quick hydraulic couplers incorporate seals and locking mechanisms to ensure leak-proof connections and maintain consistent flow rates. Their design not only streamlines workflow but also enhances the overall safety and reliability of hydraulic operations by reducing the risk of accidental disconnections and fluid leaks.
Understanding Hydraulic Flow Rate
A. Definition of Flow Rate
In the realm of hydraulic systems, flow rate refers to the volume of hydraulic fluid that moves through the system within a specific period, typically measured in liters per minute (L/min) or gallons per minute (GPM). It represents the speed at which the fluid circulates through the hydraulic circuit, driving various actuators such as cylinders and motors that perform mechanical work. Flow rate is a critical parameter because it directly influences the system’s ability to generate force, perform tasks efficiently, and respond to operational demands. A precise understanding of flow rate is essential for designing hydraulic systems that meet the required performance specifications, ensuring that machinery operates smoothly and effectively under varying load conditions.
B. Importance of Flow Rate Efficiency
Flow rate efficiency is paramount in determining the overall performance and productivity of hydraulic machinery. Efficient flow rates ensure that hydraulic components receive the necessary fluid volume to operate optimally, leading to several key benefits:
Enhanced Performance: Adequate flow rates allow actuators to move swiftly and with sufficient force, enabling machinery to perform tasks faster and more accurately. For instance, in construction equipment like excavators, optimal flow rates ensure precise digging and lifting operations.
Energy Efficiency: Efficient flow management reduces energy consumption by minimizing the work the hydraulic pump must perform. When flow rates are optimized, the system operates closer to its ideal efficiency, lowering fuel or power usage and reducing operational costs.
Reduced Wear and Tear: Maintaining appropriate flow rates prevents excessive pressure drops and turbulence within the system, which can lead to increased wear on components such as seals, hoses, and valves. This results in longer equipment lifespans and fewer maintenance requirements.
Improved Responsiveness: High flow rate efficiency enhances the system’s responsiveness to control inputs, allowing for smoother and more precise movements. This is particularly important in applications requiring fine control, such as in manufacturing automation or agricultural machinery.
Minimized Downtime: Efficient flow rates contribute to the reliability of hydraulic systems, reducing the likelihood of unexpected failures and downtime. Consistent performance ensures that operations run smoothly, maintaining productivity levels and meeting project deadlines.
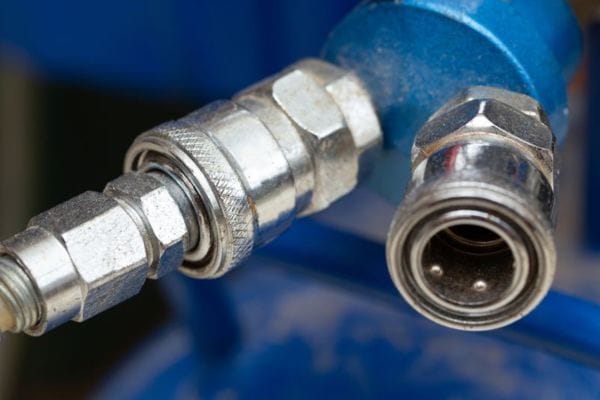
C. Factors Affecting Flow Rate
Several factors influence the flow rate within hydraulic systems, each playing a pivotal role in determining how effectively the system performs. Understanding these factors is essential for optimizing flow rate efficiency and ensuring the reliable operation of hydraulic machinery.
The viscosity of the Hydraulic Fluid
Definition: Viscosity refers to the thickness or resistance to flow of the hydraulic fluid. It is influenced by the fluid’s temperature and composition.
Impact on Flow Rate: Higher viscosity fluids are thicker and flow more slowly, which can reduce the overall flow rate within the system. Conversely, lower viscosity fluids flow more easily, potentially increasing the flow rate. However, too low a viscosity can lead to insufficient lubrication and increased wear on system components.
Optimization: Selecting a hydraulic fluid with the appropriate viscosity for the operating temperature and pressure conditions is crucial. Ensuring the fluid maintains consistent viscosity helps in maintaining stable flow rates and system performance.
Pipe Diameter and Length
Pipe Diameter:
Definition: The internal diameter of hydraulic hoses and pipes affects the volume of fluid that can pass through them.
Impact on Flow Rate: Larger diameters allow more fluid to flow through with less resistance, increasing the flow rate. However, excessively large diameters can lead to increased material costs and potential issues with fluid velocity.
Pipe Length:
Definition: The total length of the hydraulic circuit from the pump to the actuators.
Impact on Flow Rate: Longer pipes introduce more friction and resistance, which can decrease the flow rate. Each additional length adds to the cumulative pressure drop, hindering the fluid’s ability to move efficiently through the system.
Optimization: Balancing pipe diameter and length is essential. Using appropriately sized hoses and minimizing unnecessary lengths can enhance flow rates while maintaining system integrity and cost-effectiveness.
Pressure Levels
Definition: Hydraulic pressure is the force exerted by the fluid within the system, typically measured in pounds per square inch (PSI) or bar.
Impact on Flow Rate: Higher pressure levels can increase the flow rate by forcing more fluid through the system. However, excessively high pressures can cause damage to components, increase energy consumption, and pose safety risks.
Optimization: Maintaining optimal pressure levels that match the system’s design specifications ensures efficient flow rates without overburdening the hydraulic components. Pressure regulation devices, such as relief valves and pressure compensators, are used to control and stabilize system pressure.
Temperature Variations
Definition: The operating temperature of the hydraulic fluid and the surrounding environment can significantly affect system performance.
Impact on Flow Rate: Temperature changes influence fluid viscosity; as temperature increases, viscosity decreases, allowing for higher flow rates, and vice versa. Extreme temperatures can also affect the elasticity of hoses and seals, potentially leading to leaks or reduced efficiency.
Optimization: Implementing proper thermal management, such as cooling systems and temperature monitoring, helps maintain fluid viscosity within optimal ranges. Selecting fluids with stable viscosity profiles across expected temperature ranges and using materials that can withstand temperature variations are also important strategies.
System Design and Component Quality
Design Layout: The configuration of the hydraulic circuit, including the arrangement of valves, filters, and actuators, can impact the flow rate. Complex or inefficient designs may create unnecessary restrictions and reduce flow efficiency.
Component Quality: High-quality components with precise manufacturing tolerances ensure minimal internal resistance and leakage, facilitating smoother fluid flow. Poorly designed or low-quality components can introduce bottlenecks and inefficiencies.
Optimization: Designing streamlined hydraulic circuits with minimal restrictions and selecting high-quality components contribute to maintaining optimal flow rates and overall system performance.
Presence of Blockages or Contaminants:
Definition: Foreign particles, debris, or buildup within the hydraulic fluid can obstruct flow pathways.
Impact on Flow Rate: Blockages caused by contaminants can significantly reduce flow rates by restricting fluid movement and increasing resistance within the system.
Optimization: Regular maintenance, including filtering and fluid purification, helps prevent contamination and ensures unobstructed flow paths. Using effective filtration systems and adhering to proper fluid handling practices are essential for maintaining flow rate efficiency.
What Are Hydraulic Quick Couplers?
A. Definition and Function
Hydraulic quick couplers are specialized connectors designed to facilitate the rapid and secure attachment and detachment of hydraulic hoses and tools without the need for manual intervention or the use of additional tools. These couplers play a crucial role in hydraulic systems by enabling operators to switch between different hydraulic tools or machinery components swiftly and efficiently, thereby minimizing downtime and enhancing overall operational productivity.
The primary function of hydraulic quick couplers is to provide a reliable and leak-proof connection that maintains consistent flow rates and pressure levels within the hydraulic circuit. They achieve this through a combination of precise engineering and robust sealing mechanisms that prevent fluid leaks and ensure the integrity of the hydraulic system during connection and disconnection processes. By allowing for seamless transitions between various hydraulic attachments, quick couplers contribute to the versatility and flexibility of hydraulic machinery, making them indispensable in industries such as construction, manufacturing, agriculture, and more.
B. Components of Quick Couplers
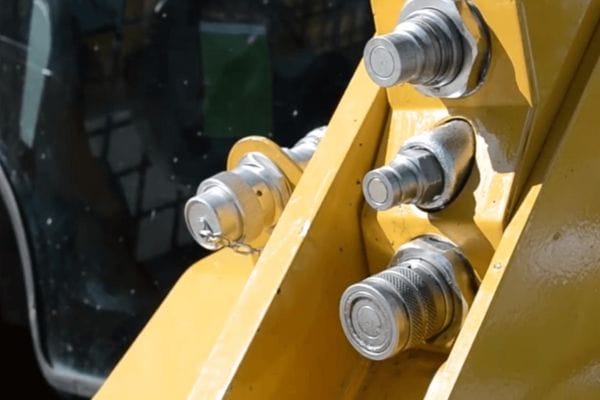
Hydraulic quick couplers are composed of several key components, each of which plays a vital role in ensuring the functionality, reliability, and efficiency of the connection. Understanding these components is essential for selecting the right coupler for specific applications and for maintaining the overall health of hydraulic systems.
Male and Female Connectors:
Male Connector: Often referred to as the “plug,” the male connector is typically attached to the hydraulic tool or device. It is designed to insert into the female connector seamlessly.
Female Connector: Known as the “socket” or “receiver,” the female connector is usually mounted on the hydraulic hose or the main hydraulic system. It receives the male connector to form a secure connection.
Seals and O-Rings:
Seals: These are critical for preventing hydraulic fluid leaks at the connection points. Seals are usually made from materials like rubber or synthetic polymers that can withstand high pressures and resist wear.
O-rings: A type of seal, O-rings are circular gaskets that provide a tight seal between the male and female connectors, ensuring that fluid does not escape during operation.
Locking Mechanisms:
Automatic Locking: Many quick couplers feature automatic locking systems that engage as soon as the male and female connectors are joined. This ensures a secure connection without the need for manual intervention.
Manual Locking: Some couplers require manual locking, where the operator must engage a latch or lever to secure the connection fully. This type provides an additional layer of security, especially in high-vibration environments.
Spring-Loaded Valves:
Function: These valves control the flow of hydraulic fluid during the connection and disconnection processes. They automatically open to allow fluid flow when connected and close to prevent leaks when disconnected.
Benefits: Spring-loaded valves enhance the efficiency of quick couplers by ensuring that the system maintains its pressure and flow rate integrity during transitions.
Protective Covers and Shields:
Purpose: To protect the internal components of the coupler from environmental contaminants such as dirt, dust, and moisture, which can compromise the seals and overall functionality.
Design: These covers are typically made from durable materials like stainless steel or reinforced plastics and are designed to withstand harsh operating conditions.
Alignment Aids:
Guide Pins and Bushings: These features help align the male and female connectors accurately during the connection process, reducing the risk of damage and ensuring a proper seal.
Visual Indicators: Some couplers include color-coded or marked indicators to assist operators in correctly aligning and connecting the couplers.
Enhancing Flow Rate Efficiency with Quick Couplers
Enhancing flow rate efficiency in hydraulic systems is essential for maximizing performance, reducing energy consumption, and prolonging equipment lifespan. Hydraulic quick couplers play a pivotal role in achieving these efficiencies by incorporating specific design features, utilizing high-quality materials, and integrating advanced technologies.
A. Design Features That Improve Flow Rate
The design of hydraulic quick couplers significantly impacts the flow rate efficiency within a hydraulic system. Several design features are specifically engineered to optimize fluid movement, reduce resistance, and maintain consistent pressure levels.
1. Streamlined Pathways to Reduce Turbulence
Streamlined Internal Pathways: Hydraulic quick couplers are designed with smooth, streamlined internal pathways that guide the hydraulic fluid seamlessly from one connector to another. This minimizes turbulence, which can cause energy losses and reduce overall flow efficiency.
Turbulence Reduction Techniques:
Rounded Corners and Transitions: Sharp angles and abrupt transitions can disrupt fluid flow, creating eddies and vortices. By incorporating rounded corners and gradual transitions, couplers facilitate a more laminar flow, reducing turbulence.
Optimized Flow Channels: The internal channels are meticulously engineered to align with the natural flow patterns of the hydraulic fluid, ensuring minimal resistance and disruption.
Benefits:
Increased Flow Efficiency: Reduced turbulence allows for smoother fluid movement, enhancing the overall flow rate.
Energy Savings: Minimizing turbulence decreases the energy required to pump the fluid, leading to lower operational costs.
Enhanced System Performance: Consistent flow contributes to more predictable and reliable hydraulic system behavior.
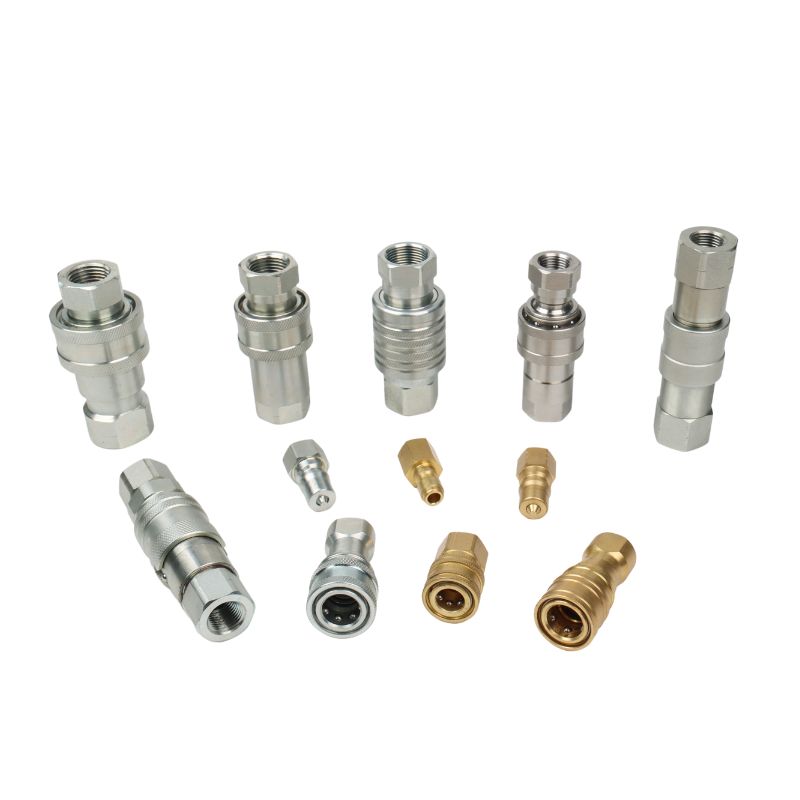
2. Larger Internal Diameters
Maximizing Fluid Volume: Hydraulic quick couplers with larger internal diameters can accommodate greater volumes of fluid passing through them. This is crucial for systems that demand high flow rates to perform heavy-duty tasks efficiently.
Design Considerations:
Balanced Sizing: While larger diameters increase flow capacity, they must be balanced with the overall system design to prevent issues such as increased fluid velocity or higher material costs.
Compatibility: Ensuring that the coupler’s internal diameter aligns with the system’s hydraulic hoses and components is essential for maintaining flow integrity.
Benefits:
Higher Flow Rates: Larger diameters facilitate the movement of more fluid per unit of time, directly increasing the flow rate.
Reduced Pressure Drops: Increased cross-sectional area decreases resistance, resulting in lower pressure drops across the coupler.
Enhanced Performance in Demanding Applications: High-flow couplers are better suited for applications requiring rapid actuation and high-speed operations.
3. Minimization of Pressure Drops
Efficient Pressure Management: Pressure drops occur when there is a loss of pressure as fluid flows through a system, often due to friction and turbulence. Designing quick couplers to minimize these drops is critical for maintaining system efficiency.
Design Strategies:
Short Flow Paths: Reducing the length of the flow path within the coupler minimizes the distance the fluid must travel, thereby decreasing frictional losses.
Smooth Internal Surfaces: Finishing the internal surfaces to a high degree of smoothness reduces friction between the fluid and the coupler walls, further minimizing pressure drops.
Optimal Flow Alignment: Ensuring that the flow direction aligns with the natural movement of the fluid reduces resistance and prevents unnecessary energy loss.
Benefits:
Maintained System Pressure: Minimizing pressure drops ensures that the hydraulic system operates at the desired pressure levels, maintaining performance standards.
Energy Efficiency: Lower pressure drops mean that less energy is required to achieve the same flow rate, contributing to overall energy savings.
Improved Component Longevity: Consistent pressure levels reduce stress on hydraulic components, enhancing their durability and lifespan.
B. Material Selection and Its Impact
The materials used in the construction of hydraulic quick couplers play a crucial role in maintaining flow integrity and ensuring long-term performance. High-quality materials contribute to efficient fluid flow, resistance to wear and corrosion, and overall system reliability.
1. Importance of Using High-Quality Materials to Maintain Flow Integrity
Material Properties:
Durability: Materials must withstand the high pressures and mechanical stresses inherent in hydraulic systems without deforming or failing.
Corrosion Resistance: Hydraulic fluids can be corrosive, and materials must resist degradation to prevent leaks and maintain fluid purity.
Smoothness: The internal surfaces should be made from materials that can maintain a smooth finish over time, preventing roughness that could disrupt fluid flow.
Common High-Quality Materials:
Stainless Steel: Offers excellent strength, corrosion resistance, and smooth surface finishes, making it ideal for high-performance couplers.
Aluminum Alloys: Lightweight yet strong, aluminum alloys are used in applications where weight savings are essential without compromising durability.
High-Grade Plastics and Composites: These materials provide corrosion resistance and flexibility, suitable for specific applications requiring non-metallic components.
Benefits:
Flow Integrity Maintenance: High-quality materials ensure that the internal pathways remain smooth and unobstructed, preserving efficient fluid flow.
Leak Prevention: Durable and corrosion-resistant materials minimize the risk of leaks, maintaining system pressure and reducing maintenance needs.
Extended Service Life: Robust materials contribute to longer-lasting couplers, reducing the frequency of replacements and associated costs.
C. Advanced Technologies in Quick Couplers
The integration of advanced technologies into hydraulic quick couplers has revolutionized their functionality and efficiency. Innovations such as smart couplers with sensors and couplers with integrated filtration systems enhance flow rate management and overall system performance.
1. Smart Couplers with Sensors
Functionality: Smart couplers are equipped with embedded sensors that monitor various parameters of the hydraulic system in real time. These sensors can track flow rates, pressure levels, and temperature, and even detect leaks or connection issues.
Key Features:
Real-Time Monitoring: Continuous tracking of critical system metrics allows for immediate detection of anomalies.
Data Integration: Smart couplers can communicate with centralized control systems or IoT platforms, providing valuable data for analysis and optimization.
Predictive Maintenance: By analyzing sensor data, potential failures can be predicted and addressed before they lead to system downtime.
Benefits:
Enhanced Flow Management: Real-time data enables precise control over flow rates, ensuring optimal performance under varying operational conditions.
Increased System Reliability: Early detection of issues reduces the likelihood of unexpected failures and minimizes downtime.
Operational Efficiency: Automated adjustments based on sensor data can optimize system performance without manual intervention.
Example Application: In a manufacturing setting, smart couplers can adjust flow rates dynamically based on the production line’s demands, ensuring consistent product quality and maximizing throughput.
2. Quick Couplers with Integrated Filtration
Functionality: Integrated filtration systems within quick couplers help maintain the cleanliness of the hydraulic fluid by removing contaminants as the fluid passes through the coupler. This dual functionality ensures that the fluid remains free of debris, which can impede flow and damage components.
Key Features:
Built-In Filters: These couplers incorporate filters that capture particulates and impurities, preventing them from circulating through the hydraulic system.
Self-Cleaning Mechanisms: Some advanced couplers feature self-cleaning filters that automatically remove trapped contaminants, reducing maintenance efforts.
Flow-Through Design: Ensures that the filtration process does not significantly impede fluid flow, maintaining high flow rate efficiency.
Benefits:
Improved Fluid Quality: Continuous filtration ensures that the hydraulic fluid remains clean, enhancing flow rate consistency and reducing wear on system components.
Extended Component Lifespan: By removing contaminants, integrated filters protect actuators, valves, and other critical components from damage and premature failure.
Reduced Maintenance: Integrated filtration simplifies the maintenance process, eliminating the need for separate filtration units and reducing the frequency of maintenance tasks.
Conclusion
In summary, hydraulic quick couplers play a vital role in enhancing flow rate efficiency within hydraulic systems, directly contributing to improved performance, reduced energy consumption, and extended equipment lifespan. Choosing the right quick coupler is paramount, as it can significantly impact the overall system performance, ensuring that hydraulic operations are both efficient and cost-effective. We encourage readers to thoroughly evaluate their current hydraulic setups and consider upgrading their quick couplers to achieve greater efficiency and productivity.
FAQ
What is a hydraulic quick coupler?
A hydraulic quick coupler is a specialized connector that allows for the rapid and secure attachment and detachment of hydraulic hoses and tools without the need for manual intervention or additional tools.
How do hydraulic quick couplers enhance flow rate efficiency?
Hydraulic quick couplers enhance flow rate efficiency by incorporating streamlined internal pathways, larger internal diameters, and minimizing pressure drops.
What are the main types of hydraulic quick couplers available?
The main types of hydraulic quick couplers include standard vs. high-flow couplers and magnetic vs. mechanical couplers. Additionally, there are specialized types such as push-button, poppet, swivel, fittingless, and cam lock couplers, each designed to meet specific application requirements.
What factors should I consider when selecting a hydraulic quick coupler?
When selecting a hydraulic quick coupler, consider factors such as the required flow rate and pressure levels, compatibility with existing hydraulic components, environmental conditions, and the quality and durability of materials used.
Can hydraulic quick couplers prevent leaks and improve system safety?
Yes, hydraulic quick couplers are designed with robust sealing mechanisms, such as seals and O-rings, which prevent fluid leaks during connections and disconnections.
How often should hydraulic quick couplers be maintained or replaced?
Maintenance frequency for hydraulic quick couplers depends on usage and operating conditions. Regular inspections should be conducted to check for signs of wear, leaks, or damage. Seals and O-rings should be cleaned and replaced as needed.