The safety and efficiency of hydraulic systems heavily depend on the reliability of their hoses. Hydraulic hose testing is designed to verify a hose’s ability to handle high-pressure environments without bursting, leaking, or wearing out prematurely. By regularly testing hoses, businesses can prevent costly malfunctions, protect workers from potential harm, and extend the life of hydraulic equipment. Moreover, adherence to industry standards during testing further guarantees that hoses meet strict safety and performance criteria.
The Basics of Hydraulic Hoses Testing
What is Hydraulic Hose Testing?
Hydraulic hose testing refers to the process of evaluating the durability, strength, and performance of hydraulic hoses to ensure they meet specific safety and operational standards. This testing is a crucial part of hydraulic system maintenance, helping to verify that hoses can handle the high pressures, temperature fluctuations, and extreme environments they are exposed to in various applications.
Hydraulic hoses are integral components of hydraulic systems, used to transfer hydraulic fluids between different parts of machinery. Failure to properly test these hoses can result in equipment breakdowns, costly repairs, and even safety hazards in industries such as construction, agriculture, manufacturing, and mining. By conducting thorough testing, companies can ensure the reliability and longevity of their hydraulic systems.
There are two primary types of hydraulic hose testing:
Pressure Testing: This involves subjecting the hose to controlled pressure levels, typically higher than its standard operating pressure, to ensure that it can safely handle the maximum expected pressures during regular use.
Functional Testing: This test examines the overall performance of the hose in real-world conditions, including its flexibility, endurance, and ability to maintain pressure without leaks or malfunctions during normal operations.
Why Conduct Hydraulic Hose Testing?
The importance of hydraulic hose testing cannot be overstated, particularly in industries that rely on heavy machinery and equipment, such as construction, aerospace, oil and gas, and agriculture. Here are the key reasons why regular testing is essential:
Preventing Failures in Critical Applications: Hydraulic systems are often the backbone of heavy machinery, and any failure in the hydraulic hoses can lead to significant downtime, costly repairs, and even dangerous accidents. Testing helps identify potential issues such as leaks, pressure drops, or material fatigue before they escalate into full-blown failures.
Improving Safety: High-pressure hydraulic systems pose a considerable safety risk if a hose fails unexpectedly. Workers can be exposed to high-pressure fluid sprays, which can lead to serious injuries. Regular testing ensures that hoses are in good condition, reducing the likelihood of accidents in the workplace.
Ensuring Compliance with Standards: Regulatory bodies like the Society of Automotive Engineers (SAE) and the International Organization for Standardization (ISO) have established stringent standards for hydraulic hoses. These standards, such as SAE J343 or ISO 18752, specify the pressure ratings, burst pressure requirements, and other safety benchmarks that hydraulic hoses must meet. Conducting tests ensures that your hoses comply with these standards, maintaining both the performance and safety of your systems.
Types of Hydraulic Hose Tests
Burst Pressure Testing
Definition & Purpose: Burst pressure testing is designed to push a hydraulic hose to its breaking point by subjecting it to extreme pressure levels that exceed its normal operating conditions. The goal is to ensure the hose can withstand pressures far beyond what it would typically experience in daily use, thus verifying its strength and safety margins. This test helps to identify the maximum pressure the hose can endure before it fails.
Procedure:
Preparation: Secure the hose in a hydraulic test bench or similar equipment, ensuring all connections are tightened and safety precautions are in place.
Pressurization: Gradually increase the internal pressure within the hose using a hydraulic pump until the hose bursts.
Observation: Record the pressure level at which the hose bursts and inspect the point of failure for signs of material weakness or poor assembly.
Evaluation: Compare the burst pressure to industry standards and the manufacturer’s specifications to determine whether the hose meets safety requirements.
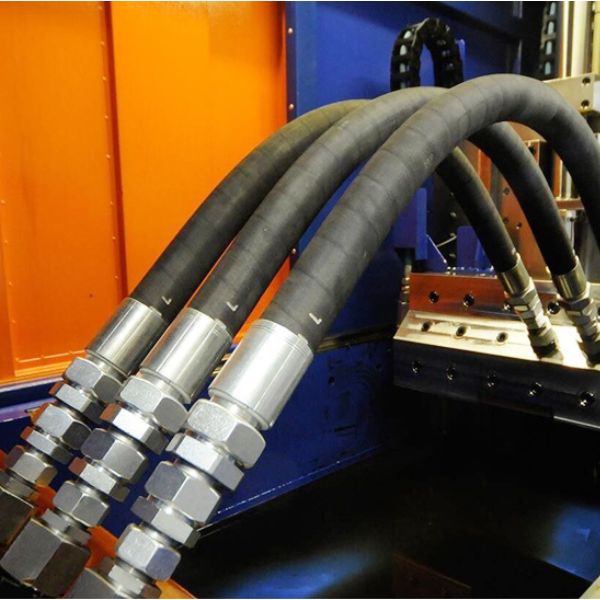
Proof Pressure Testing
Definition & Purpose: Proof pressure testing is a method of verifying that a hydraulic hose can safely operate under its designated working pressure. Unlike burst testing, which pushes the hose beyond its limits, proof pressure testing subjects the hose to a controlled pressure that is typically 1.5 to 2 times the working pressure to confirm its integrity and reliability.
How it Differs from Burst Testing:
Burst Testing: A destructive test where the hose is pushed to failure to determine its maximum pressure capacity.
Proof Pressure Testing: A non-destructive test that verifies the hose can handle the rated working pressure without any leaks or defects, ensuring safety in regular operations.
Impulse Testing
What is Impulse Testing? Impulse testing simulates the repetitive pressure cycles that hydraulic hoses experience in real-world operations. This test subjects the hose to repeated pressure spikes at various frequencies to mimic the pulsating stress found in hydraulic systems, particularly in applications where hoses undergo rapid changes in pressure, such as heavy equipment or industrial machinery.
Importance: Impulse testing is essential for predicting the long-term performance and durability of hydraulic hoses. Since many hydraulic systems experience frequent pressure surges, impulse testing ensures that the hose can handle these cycles over an extended period without cracking, leaking, or failing prematurely. This is crucial for applications with heavy-duty or high-frequency operations, such as construction or mining.
Leakage Testing
What it Entails: Leakage testing is a process used to identify small leaks in hydraulic hoses that could eventually lead to larger, more catastrophic failures. It involves pressurizing the hose to its operating pressure and inspecting for any visible or microscopic leaks. Special detection tools, such as pressure gauges or dye penetration tests, are often used to spot leaks that may not be immediately apparent.
Procedure:
Pressurize the hose to the appropriate working pressure.
Inspect all joints, connections, and the length of the hose for any signs of fluid leakage.
Use leak detection equipment (e.g., ultrasonic sensors or dye tests) to identify hard-to-see leaks.
Evaluate the results and take corrective action if any leaks are detected.
Leakage testing is a critical step in ensuring the hose’s reliability in high-pressure applications, preventing costly downtime and damage.

Non-Destructive Testing (NDT)
Hydrostatic Pressure Testing:
Hydrostatic testing is a type of non-destructive testing (NDT) that assesses the strength and integrity of a hydraulic hose by filling it with liquid (usually water or oil) and applying pressure. The goal is to detect any weaknesses or potential failures in the hose without causing permanent damage.
Procedure:
Fill the Hose: The hose is filled with liquid to eliminate air pockets.
Apply Pressure: Pressure is gradually increased to the desired level (usually higher than the working pressure but lower than the burst pressure).
Inspect for Leaks: The hose is visually inspected for leaks, bulges, or deformations during the test.
Release Pressure: Once the test is complete, pressure is carefully released, and the hose is re-evaluated.
Why it Matters: Hydrostatic testing helps verify the structural integrity of a hose under pressure without permanently damaging it, making it ideal for ongoing quality control.
Step-by-Step Guide to Conducting Hydraulic Hose Testing
Preparation
Tools & Equipment:
To effectively conduct hydraulic hose testing, the following essential tools and equipment are required:
Hydraulic Test Bench: Used to secure the hose and apply pressure during the test.
Test Fluids: Typically, water or oil is used to fill the hose for testing purposes.
Pressure Gauges: Accurate pressure gauges are crucial to measure the levels of pressure applied to the hose.
Hydraulic Pump: To generate the required pressure for burst, proof, or impulse testing.
Leak Detection Equipment: Ultrasonic sensors, dye tests, or pressure gauges can detect leaks during the test.
Safety Enclosure: A secure enclosure is necessary to contain any potential failures and prevent injury.
Safety Precautions:
Safety is paramount during hydraulic hose testing due to the high pressures involved. The following precautions should be followed:
Proper Fitting Checks: Ensure that all fittings and connections are tight and properly assembled to prevent leaks or blow-offs during testing.
Clearing Air from Lines: Air pockets in the system can lead to inaccurate results or even dangerous pressure surges. Bleed the system to ensure no air remains in the hose before starting the test.
Wear Personal Protective Equipment (PPE): Always wear PPE such as safety goggles, gloves, and protective clothing to shield against potential fluid sprays or hose failures.
Keep a Safe Distance: During testing, stand clear of the hose and maintain a safe distance to avoid injury if the hose bursts or leaks under pressure.
Performing the Test
The procedures for conducting different types of hydraulic hose tests require specific steps:
Burst Pressure Testing:
Step 1: Secure the hose to the hydraulic test bench and attach it to the pressure pump. Make sure all connections are properly tightened.
Step 2: Gradually increase the pressure using the hydraulic pump. Continue raising the pressure until the hose bursts.
Step 3: Record the pressure at which the hose bursts and visually inspect the failure point for signs of wear or material fatigue.
Best Practice: Increase pressure gradually to avoid overshooting and ensure that the test bench and safety enclosure can contain the burst.
Proof Pressure Testing:
Step 1: Mount the hose securely in the test rig, making sure all fittings are tight.
Step 2: Slowly raise the pressure to 1.5 to 2 times the hose’s working pressure.
Step 3: Hold the pressure for a specified duration, typically around 30-60 seconds, while monitoring the pressure gauge for drops or leaks.
Best Practice: Ensure that the test duration and pressure are consistent with the manufacturer’s specifications for proof testing. Any pressure drop during the test should trigger further investigation.
Impulse Testing:
Step 1: Connect the hose to an impulse tester, which cycles pressure through the hose repeatedly.
Step 2: Set the tester to simulate the pressure cycles the hose will experience in its actual application (e.g., rapid pressure surges).
Step 3: Run the test for the specified number of cycles, which could range from thousands to millions, depending on the application.
Best Practice: Monitor the test closely to detect early signs of wear, bulging, or material fatigue, which could indicate that the hose will not withstand long-term use.
Post-Test Analysis
Evaluating Results:
Once the tests are completed, it’s critical to properly analyze the results:
Burst Test Results: Compare the burst pressure to the manufacturer’s rated burst pressure and ensure it exceeds industry standards such as SAE J343 or ISO 18752. If the hose bursts below the required level, it has failed the test.
Proof Test Results: Check for any pressure drops during the proof pressure test. A stable pressure reading without leaks indicates a successful test.
Impulse Test Results: After impulse testing, inspect the hose for any visible wear, cracks, or bulging. The hose should withstand the required number of pressure cycles without deterioration.
When to Reject a Hose:
There are specific criteria that determine when a hose should be deemed unfit for further use:
Failure to Meet Burst Pressure: If the hose bursts below the manufacturer’s specified pressure rating or industry standards, it should be rejected.
Leaks Detected During Testing: Even small leaks identified through leakage testing indicate that the hose is not safe for use.
Visible Wear After Testing: Cracks, bulging, or any signs of material fatigue discovered after impulse testing suggest that the hose may not withstand operational conditions and should be replaced.
Inconsistent Test Results: If the pressure drops during proof testing or fluctuates unexpectedly, it indicates a problem with the hose’s integrity, and it should be removed from service.
Common Failures Detected During Testing
Hose Burst
Causes of Hose Bursting:
Hydraulic hoses can burst for a variety of reasons, most commonly due to excessive pressure, incorrect installation, material defects, or wear and tear over time. When a hose is subjected to pressures that exceed its rated capacity, or when it is not properly maintained, the walls of the hose can weaken, leading to a burst. External damage, such as abrasions or cuts, can also compromise the structural integrity of the hose, making it more susceptible to failure.
How Testing Helps Detect Weaknesses:
Burst pressure testing plays a crucial role in identifying hoses that are at risk of bursting. By subjecting the hose to pressures well beyond its normal operating range, testing can reveal weak points or potential failure zones that may not be apparent during regular operation. This ensures that only hoses that meet the highest safety standards are put into use, reducing the likelihood of catastrophic failure in the field.
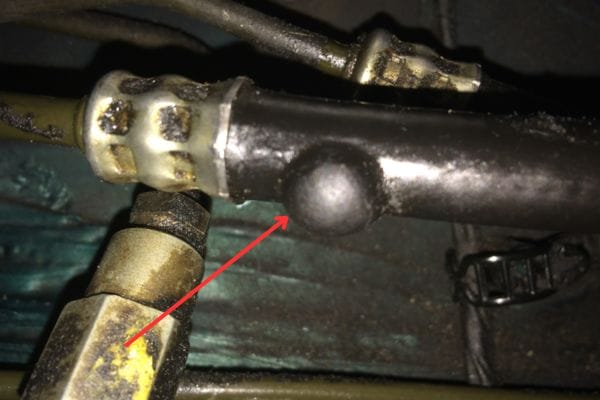
Fitting Leaks
Causes of Fitting Leaks:
Improper assembly practices, such as using the wrong size fittings or not tightening them correctly, are common causes of leaks at the connection points between the hose and its fittings. Misaligned fittings, cross-threading, or poor-quality sealing materials can also contribute to leakage. These issues often occur during installation but may not be immediately apparent until the hose is under pressure.
How Testing Helps Detect Leaks:
Hydraulic hose testing, particularly leakage tests and proof pressure tests, can detect these small leaks before they escalate into larger problems. During testing, the hose is pressurized, and all fittings and connections are carefully inspected for fluid leakage. This allows technicians to identify and fix any issues with the fittings before the hose is put into service, preventing unexpected fluid loss and reducing maintenance costs.
Wear and Tear in High-Pressure Applications
Wear Patterns in High-Pressure Environments:
In high-pressure applications, hydraulic hoses are subjected to extreme forces that can cause abrasions, internal wall degradation, and surface cracks. These wear patterns often occur in areas where the hose rubs against machinery, is exposed to environmental factors like heat or chemicals, or undergoes constant bending and flexing.
How Testing Reveals Wear Patterns:
Impulse testing is particularly effective at revealing wear and tear. This test simulates the repeated pressure surges and fluctuations that hoses experience in real-world high-pressure environments. Over time, impulse testing can highlight early signs of wear, such as small cracks or thinning of the hose walls. Identifying these issues during testing allows operators to replace worn hoses before they fail in the field, ensuring continuous, safe operation.
Material Fatigue and Failure
What is Material Fatigue?
Material fatigue occurs when the hose’s material structure weakens over time due to repetitive stress, leading to the formation of small cracks or fractures. This is particularly common in hoses that are exposed to repeated pressure cycling, vibration, or temperature fluctuations. Over time, the constant expansion and contraction of the hose material under stress can cause it to fail, even if the hose is not subjected to extreme pressures.
How Material Fatigue is Detected:
Fatigue tests, such as impulse testing or pressure cycling tests, are designed to simulate long-term use and stress. During these tests, the hose is exposed to multiple cycles of pressure changes to evaluate its ability to withstand repeated use. Early detection of material fatigue through testing is critical because once fatigue cracks begin to form, the hose’s integrity is compromised, and it is more likely to fail under pressure. By identifying hoses that show signs of fatigue early, technicians can replace them before they pose a safety risk.
Conclusion
In conclusion, hydraulic hose testing is essential for ensuring the safety, performance, and reliability of hydraulic systems across various industries. By conducting regular tests such as burst, proof, and impulse testing, businesses can prevent costly failures, enhance operational efficiency, and maintain compliance with industry standards like SAE and ISO. Companies should prioritize routine testing and adhere to best practices to avoid unexpected downtime and equipment failures.
FAQ
What is hydraulic hose testing?
Hydraulic hose testing evaluates the strength, durability, and safety of hoses to ensure they meet performance standards.
Why is hydraulic hose testing important?
It prevents failures, improves safety, and ensures compliance with industry standards like SAE and ISO.
What are the main types of hydraulic hose tests?
Common tests include burst pressure testing, proof pressure testing, impulse testing, leakage testing, and hydrostatic pressure testing.
How often should hydraulic hoses be tested?
Testing frequency depends on the application, but routine inspections and tests are recommended as part of regular maintenance.
What causes hydraulic hoses to burst?
Hoses can burst due to excessive pressure, improper installation, material fatigue, or external damage.
How can I detect leaks in hydraulic hoses?
Leaks can be identified through pressure testing, visual inspections, and using leak detection tools like ultrasonic sensors or dye tests.