Properly installed hose clamps help manage the stresses that hoses face during operation, including vibration and thermal expansion. This, in turn, reduces the risk of hose failure, which can lead to costly downtime and potentially hazardous situations.
Understanding Hose Clamps
A. Definition and Function of Hose Clamps
Hose clamps are fastening devices designed to secure hoses onto fittings or other components in hydraulic systems, preventing fluid leakage and ensuring the integrity of the connection. Their primary function is to create a tight seal around the hose, accommodating any movement or pressure variations that may occur during operation. Properly installed hose clamps help maintain consistent fluid flow, reduce the risk of hose failure, and contribute to the overall safety and efficiency of hydraulic systems.
B. Types of Hose Clamps
Worm Gear Clamps
Worm gear clamps are among the most commonly used types of hose clamps. They consist of a metal band with a threaded screw that allows for precise tightening. When the screw is turned, it pulls the band tighter around the hose, creating a secure seal. These clamps are highly versatile and can accommodate a range of hose sizes, making them suitable for various applications in hydraulic systems.
Band Clamps
Band clamps are designed with a continuous band of material that encircles the hose. They typically feature a simple design that provides even pressure distribution around the hose. Band clamps are ideal for applications where a uniform seal is essential, such as in high-pressure hydraulic systems. They can be installed quickly and are available in both adjustable and non-adjustable options.
Spring Clamps
Spring clamps utilize a spring mechanism to maintain constant pressure on the hose. They automatically adjust to changes in the hose diameter due to temperature fluctuations or pressure changes. While easy to install and remove, spring clamps are generally better suited for lower-pressure applications where the risk of leaks is less critical. Their design allows for quick assembly and disassembly, making them a popular choice in automotive and plumbing applications.
Specialty Clamps (e.g., T-bolt, Quick-release)
Specialty clamps, such as T-bolt and quick-release clamps, serve specific purposes in hydraulic applications. T-bolt clamps provide enhanced strength and torque distribution, making them ideal for high-performance applications where pressure and vibration are significant concerns. Quick-release clamps allow for rapid disconnection and reconnection of hoses, making them valuable in scenarios requiring frequent maintenance or adjustment. These clamps are designed for convenience without compromising reliability.

C. Materials Used in Hose Clamps
Stainless Steel
Stainless steel is the most common material used for hose clamps due to its excellent corrosion resistance, strength, and durability. These clamps can withstand harsh environmental conditions, making them suitable for both indoor and outdoor applications. Stainless steel clamps are particularly beneficial in hydraulic systems where exposure to moisture and chemicals is prevalent.
Carbon Steel
Carbon steel clamps are often more economical than stainless steel options. However, they are less resistant to corrosion and are generally recommended for use in less demanding environments. When coated or treated, carbon steel clamps can provide adequate performance in mild conditions but may require replacement more frequently in harsher environments.
Plastic and Composite Materials
Plastic and composite material clamps are lightweight and resistant to corrosion. While they may not provide the same strength as metal clamps, they are suitable for low-pressure applications and environments where metal components could lead to corrosion or chemical reactions. These clamps are often used in specialized applications where weight savings are critical or where electrical conductivity must be minimized.
Common Causes of Hydraulic Hose Failure
A. Vibration and Movement in Hydraulic Systems
One of the most significant contributors to hydraulic hose failure is vibration. Hydraulic systems are often subject to dynamic forces due to the movement of machinery, the operation of pumps, and the flow of hydraulic fluid. This constant vibration can lead to fatigue in the hoses, causing them to become loose at the fittings. If hose clamps are not adequately secured or if they wear down over time, the vibration can cause a loss of clamping force, leading to leaks or disconnections. Additionally, excessive movement can create stress points on hoses, making them more susceptible to damage.
B. Improper Installation and Torque Settings
Improper installation of hose clamps is another critical factor leading to hose failure. When clamps are not installed correctly, they may not provide adequate pressure around the hose, leading to leaks. A common mistake is over-tightening or under-tightening the clamps. Over-tightening can crush the hose material, while under-tightening can allow fluid to escape. Both scenarios can result in catastrophic failures. Ensuring that the correct torque settings are applied during installation is essential to maintain the integrity of the connection. Regular checks to confirm that the clamps remain secure after initial installation can help prevent issues arising from improper installation.
C. Environmental Factors (Temperature, Chemicals, UV Exposure)
Hydraulic hoses are often exposed to a range of environmental conditions that can accelerate wear and lead to failure. Temperature fluctuations can cause the hose material to expand and contract, impacting the effectiveness of hose clamps. Extreme heat can degrade the rubber or plastic used in hoses, while cold temperatures can make the materials brittle.
Chemical exposure is another significant concern. Hydraulic fluids, oils, and other chemicals can erode the hose material over time. If a hose is not designed to withstand specific chemicals, it may deteriorate faster than expected, leading to leaks. UV exposure can also weaken hoses, especially if they are used outdoors without adequate protection. Hoses that are not resistant to UV rays can become cracked and brittle, leading to premature failure.
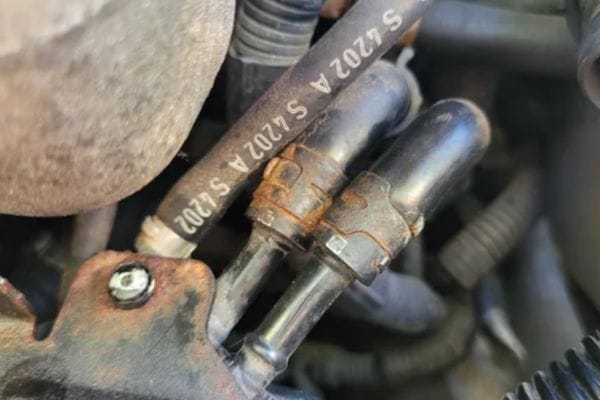
D. Wear and Tear Over Time
Wear and tear is an inevitable part of any hydraulic system’s life cycle. Hoses experience continual pressure, flexing, and exposure to environmental factors, which can lead to degradation. Over time, the materials used in hoses may break down, leading to cracks, bulges, or other forms of damage. Additionally, hose clamps themselves can become worn or corroded, losing their effectiveness in maintaining a secure connection.
Regular maintenance and inspections are crucial to identifying signs of wear before they result in failures. Operators should look for any visible signs of damage, such as fraying, discoloration, or unusual swelling in hoses. By establishing a routine for checking the condition of hoses and clamps, potential issues can be addressed before they escalate into significant failures that could halt operations or pose safety risks.
Best Practices for Hose Clamp Use
A. Selecting the Right Clamp for Your Application
Choosing the appropriate hose clamp is crucial for ensuring the longevity and effectiveness of hydraulic hoses. Several factors should be considered when selecting a clamp:
Type of Hose: Different hoses have varying thicknesses and materials. Ensure that the clamp you select is compatible with the specific type of hose you are using, whether it’s rubber, plastic, or reinforced fabric.
Pressure Rating: Each hose and clamp has a specific pressure rating. Choose a clamp that can handle the maximum pressure your hydraulic system will encounter to prevent failure under stress.
Environmental Conditions: Consider the environment in which the hose will be operating. For outdoor applications, stainless steel clamps may be preferable due to their corrosion resistance. For chemical exposure, select clamps made from materials that can withstand the specific chemicals involved.
Size and Adjustability: Make sure the clamp is appropriately sized for the hose. Adjustable clamps can provide flexibility for varying hose sizes, while non-adjustable options may be better for fixed applications.
Special Features: Some applications may require specialty clamps, such as quick-release clamps for easy access or T-bolt clamps for high-pressure scenarios. Assess your specific needs to determine if additional features are necessary.
B. Proper Installation Techniques
Aligning Clamps Correctly: Proper alignment of hose clamps is critical for ensuring a secure fit. The clamp should be positioned evenly around the hose and the fitting, without overlapping or misaligning. Misalignment can cause uneven pressure distribution, leading to leaks or hose damage.
Ensuring Appropriate Torque Settings: Each type of hose clamp comes with recommended torque settings. Over-tightening can crush the hose material, while under-tightening can lead to slippage and leaks. Utilize a torque wrench to achieve the manufacturer’s specifications for optimal performance. It’s advisable to recheck the torque after installation, as hoses can settle and compress after being placed under pressure.
Using Proper Tools: Always use the right tools for installation. For worm gear clamps, a screwdriver or ratchet may be required, while band clamps might need specific installation tools. Using the correct tools helps prevent damage to both the clamp and the hose.
C. Regular Inspection and Maintenance
Routine inspection and maintenance of hose clamps and hoses are essential for preventing failures. Here are some key practices:
Visual Inspections: Regularly examine hoses and clamps for signs of wear, such as cracks, discoloration, or deformation. Pay close attention to areas near the clamps, where leaks are most likely to occur.
Checking Torque Settings: Periodically verify that hose clamps remain at the appropriate torque settings, especially after the initial installation or following significant operational changes. This helps maintain the integrity of the connection over time.
Monitoring for Vibration and Movement: In systems prone to vibration, assess whether hose clamps are loosening due to dynamic forces. Consider adding additional supports or guides to minimize movement if necessary.
Environmental Assessments: If the operating environment changes, reassess the suitability of the existing clamps. For instance, if new chemicals are introduced or if there’s a change in temperature extremes, it may be necessary to upgrade to more resistant clamps.
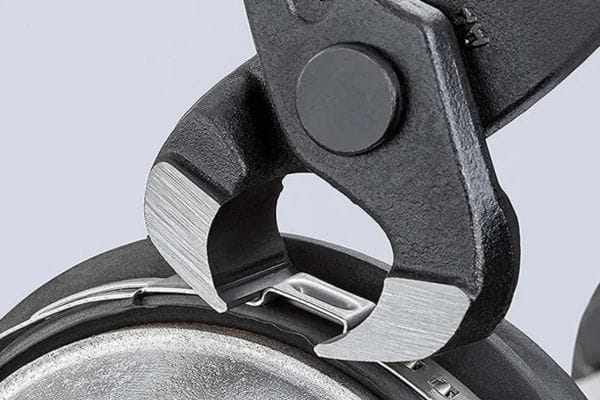
D. Guidelines for Replacing Clamps and Hoses
Timing for Replacement: Clamps and hoses should be replaced at the first sign of wear or damage. Waiting too long can lead to catastrophic failures. Develop a timeline for replacements based on the operating conditions and expected wear rates.
Removal Process: When removing old clamps, take care not to damage the hose or fittings. Use appropriate tools and techniques to avoid causing additional wear that could lead to leaks upon reinstallation.
Hose Replacement Protocols: When replacing hoses, ensure that the new hose matches the specifications of the original. Use the same size, pressure rating, and material type. After installation, follow proper clamping techniques to secure the new hose.
Documentation and Record Keeping: Maintain records of inspections, installations, and replacements. Documentation helps track the condition of hoses and clamps over time, allowing for better planning of maintenance activities and replacements.
Innovations in Hose Clamping Technology
A. Overview of New Materials and Designs
Recent advancements in materials science have led to the development of innovative hose clamps that offer enhanced performance and durability. New composite materials are being used to produce clamps that are lighter yet stronger, providing superior resistance to corrosion and temperature fluctuations. Additionally, designs incorporating flexible materials allow for better conformability to various hose shapes, ensuring a tighter seal without damaging the hose. The introduction of quick-release mechanisms and self-adjusting clamps also reflects a trend toward user-friendly solutions, reducing installation time and improving accessibility.
B. Advances in Automated Clamping Solutions
Automation is revolutionizing the way hose clamps are utilized in hydraulic systems. Automated clamping solutions, such as robotic arm installations, enable precise and consistent application of clamps across large production lines. These systems can adjust clamping pressure in real time, ensuring optimal tightness without the risk of over-tightening. Additionally, automated sensors can monitor clamp integrity and notify operators of any issues, further enhancing system reliability. This technology not only improves efficiency but also minimizes human error, leading to safer and more reliable hydraulic operations.
C. Future Trends in Hose Clamp Technology
Looking ahead, several trends are poised to shape the future of hose clamp technology. The integration of smart technology into clamps is expected to become more prevalent, with the potential for real-time monitoring of hose conditions, pressure levels, and even temperature changes. This data can be used to predict maintenance needs and prevent failures before they occur.
Sustainability is another significant focus, with manufacturers exploring biodegradable and recyclable materials for clamps to reduce environmental impact. Additionally, the ongoing demand for lightweight and compact designs in hydraulic systems will likely drive innovation in clamp materials and configurations, pushing the boundaries of current engineering practices.
Conclusion
Ensuring that clamps are selected and installed correctly is vital for preventing leaks and maintaining system pressure, which directly impacts the overall performance of the hydraulic system. By minimizing the risk of hose failure, operators can enhance both safety and operational efficiency, reducing downtime and maintenance costs.
FAQ
What is the primary function of a hose clamp?
A hose clamp secures hoses onto fittings to prevent leaks and maintain pressure within hydraulic systems.
What are the common types of hose clamps?
Common types include worm gear clamps, band clamps, spring clamps, and specialty clamps like T-bolt and quick-release clamps.
How do I know which hose clamp to choose?
Select a clamp based on the hose type, pressure rating, environmental conditions, and specific application needs.
What are the signs that a hose clamp needs to be replaced?
Look for visible signs of wear, such as corrosion, deformation, or cracks in the clamp, as well as any leaks around the hose connection.
How often should I inspect hose clamps?
Regular inspections are recommended, ideally every few months or after significant operational changes, to ensure clamps are secure and in good condition.
Can I reuse hose clamps?
It is generally advisable to replace hose clamps if they show signs of wear or damage, as reusing them can lead to compromised performance and safety risks.