Ball valves are a type of quarter-turn valve that uses a hollow, perforated, and pivoting ball to control the flow of fluids and gases through a pipe or system. They are known for their simple yet effective design, which allows for quick and reliable opening and closing of fluid pathways. Ball valves are widely used across a variety of industries due to their durability, ease of operation, and ability to provide a tight shutoff when fully closed.
Common Signs of a Failing Ball Valve
Difficulty in Valve Operation
One of the first signs that a ball valve may be failing is difficulty in turning or operating the valve. When a valve becomes unresponsive or harder to operate than usual, it can indicate several potential issues.
Symptoms to Watch For:
Tightness: The valve feels unusually tight or stiff when turning the handle or actuator.
Grinding Noise: When you attempt to open or close the valve, you hear a grinding, scraping, or friction-like sound.
Resistance: Increased resistance while turning the valve handle or actuator.
Impact on System Performance: When a valve is difficult to operate, it can cause delays in the flow control process, making it harder to regulate or shut off the fluid as needed. In severe cases, it can lead to damage to other system components, as excessive force may be required to turn the valve. The inability to control the valve smoothly can also result in inconsistent flow or pressure, disrupting the operation of the entire fluid control system.
Possible Causes:
Debris, corrosion, or dirt buildup inside the valve.
Damage to the internal ball or valve seat.
Improper lubrication or lack of maintenance.
Leaks Around the Valve Stem or Body
Leakage is one of the most common and visible signs of a failing ball valve. A leaking valve can be a major issue in fluid control systems, especially when dealing with hazardous, corrosive, or pressurized fluids.
Visual Signs of Leaks:
Wet Spots: The area around the valve stem or body becomes wet.
Dripping or Pooling Liquid: Liquid begins to accumulate around the valve, indicating a possible leak.
Visible Fluid Leakage: Liquid may escape from the valve body, stem, or at the seal points.
Causes of Leaks:
Seal Degradation: Over time, the seals around the valve stem or body can degrade due to pressure, temperature, or chemical exposure.
Cracked Valve Body: Cracks in the valve body caused by corrosion or over-pressurization can lead to leakage.
Worn-out Gaskets: Gaskets can wear out, causing poor sealing and leading to leaks around the valve.
Impact on System Performance: Leaks can lead to fluid loss, reduced system efficiency, and potential environmental hazards. Even small leaks can result in significant issues, including pressure drops, increased operational costs, and potential system failure if left unaddressed.
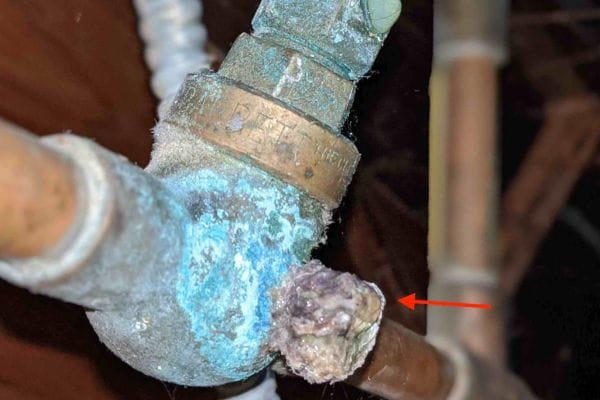
Inconsistent Flow or Pressure
Another key indicator of a failing valve is inconsistent flow or fluctuating pressure. A healthy ball valve should maintain a steady, controlled flow, and any irregularities can indicate underlying issues with the valve.
Symptoms to Watch For:
Reduced Flow Rate: The fluid flow through the valve is noticeably slower than usual, even though the system pressure remains the same.
Fluctuating Pressure: Pressure gauges indicate erratic or fluctuating pressure despite a steady flow input.
Unsteady Fluid Control: Difficulty maintaining a stable, consistent flow rate, leading to poor system performance.
Correlation with Ball Valve Failure: Ball valves are designed to provide a tight seal when closed and a smooth passage for fluid when open. If the valve is malfunctioning, it may not fully open or close as intended, leading to inconsistent flow and pressure. This may occur due to:
Worn-out or damaged valve components like the ball or seats.
Blockage or debris buildup inside the valve.
Seal failure allowing partial flow even when the valve is meant to be closed.
Impact on System Performance: Inconsistent flow or pressure can cause inefficiencies in the system, affect the quality of the processed fluid, and lead to overall instability in the fluid control system. This can cause operational disruptions and even damage to downstream equipment.
Excessive Wear on Moving Parts
Ball valves contain several moving components that can wear down over time, leading to performance issues. The primary moving parts include the ball, valve seats, and the actuator mechanism.
Symptoms of Wear:
Worn-out Balls: The ball inside the valve can become worn or deformed, affecting its ability to create a tight seal or control flow.
Damaged Valve Seats: The valve seats, which help seal the valve shut, can degrade over time due to pressure, heat, or chemical exposure.
Actuator Wear: In automated systems, the actuator (whether pneumatic, electric, or manual) may show signs of wear, affecting valve responsiveness.
Importance of Monitoring Moving Parts: The ball, valve seat, and actuator are critical to the proper functioning of a ball valve. Regular monitoring and maintenance of these moving parts can prevent issues like leakage, difficulty in valve operation, and irregular flow.
Impact on System Performance: Excessive wear on moving parts reduces the valve’s ability to control flow effectively, leading to inconsistent operation, increased risk of failure, and potential system inefficiencies. If wear is not addressed, it could lead to valve failure, resulting in downtime and costly repairs.
Unusual Sounds or Noises
Strange noises during valve operation are often an early indicator that something is wrong inside the valve. These sounds can be a result of internal damage or friction between moving parts.
Symptoms of Unusual Noises:
Squeaking or Rattling: A squeaking or rattling noise may indicate friction between internal components such as the ball and valve seat, or dirt buildup.
Grinding: A grinding noise often signals that parts inside the valve are rubbing against each other due to wear or corrosion.
Whistling: Whistling noises can occur when there is turbulence in the fluid caused by improper valve operation.
Connection to Internal Damage: Unusual sounds typically arise from:
Friction between the ball and valve seat due to insufficient lubrication or worn-out parts.
Corrosion or debris buildup causes restricted movement within the valve.
Damaged actuators or other components create abnormal sounds.
Impact on System Performance: Noise is not just an annoying side effect; it often signifies internal damage that can impair the valve’s function. Ignoring unusual sounds can lead to further damage, including complete valve failure, which can disrupt the entire fluid control system.
Diagnosing a Failing Ball Valve
Visual Inspection Techniques
The first step in diagnosing ball valve is a thorough visual inspection. Regular inspections can help detect any obvious signs of wear or damage that could indicate potential valve failure.
Step-by-Step Process:
Inspect the Valve Body: Examine the valve body for any visible cracks, corrosion, or discoloration. Cracks can form due to excessive pressure or exposure to extreme temperatures, leading to leaks or complete valve failure.
Check for Rust or Corrosion: Look for rust or other signs of corrosion around the valve, especially in environments where the valve is exposed to moisture or harsh chemicals. Corrosion can weaken the valve structure and lead to premature failure.
Examine the Stem and Seals: Check for any visible leakage around the valve stem or seals. Worn-out seals are a common cause of leaks. If the valve stem is not aligned or is loose, it may indicate internal damage or that the valve is stuck in a particular position.
Look for Discoloration: Discoloration around the valve, particularly on the ball or valve body, could indicate overheating, corrosion, or chemical damage. This can affect the performance and longevity of the valve.
What to Look For:
Cracks or fractures in the valve body.
Rust or visible corrosion on the valve or its components.
Leaking fluid around the stem or seals.
Discoloration of parts, suggesting excessive wear, overheating, or chemical exposure.
Testing Valve Function
Testing the valve’s operation is essential to ensure it is working as intended. A functioning ball valve should open and close smoothly with minimal resistance.
How to Test Valve Operation:
Manual Testing: If the valve is a manual type, try turning the valve handle to assess its responsiveness. A valve that’s difficult to turn, requires excessive force, or feels stiff can be an indicator of internal damage, dirt buildup, or a worn-out actuator.
Automated Testing: For actuated ball valves (pneumatic, electric), test the actuator’s response. Ensure that the valve moves smoothly and completely when the actuator is engaged. The valve should open fully when in the “open” position and close tightly when in the “closed” position.
Look for Resistance or Sticking: If the valve does not move easily, it may be stuck due to internal corrosion, dirt, or wear. This could also indicate problems with the actuator mechanism.
Identifying Issues:
Difficulty in Turning: If the valve handle is hard to turn, there may be internal buildup or mechanical failure.
Inability to Fully Open or Close: If the valve does not fully open or close, the ball inside the valve may be damaged, misaligned, or obstructed.
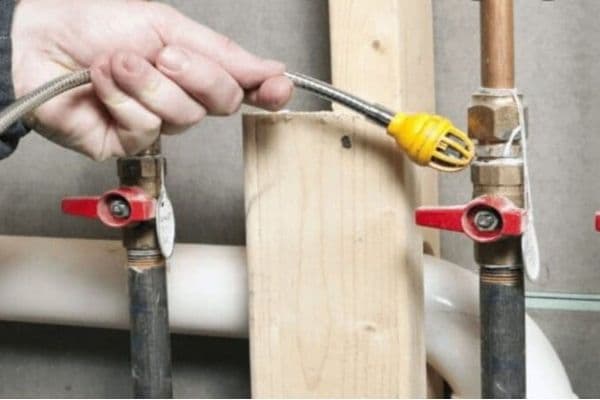
Pressure and Flow Tests
Pressure and flow tests are among the most effective ways to diagnose issues like leaks or inconsistent flow, which can be indicative of a failing ball valve.
How to Perform Basic Pressure Tests:
Pressure Relief Valves: Use pressure relief valves or pressure gauges installed in the system to monitor the pressure before and after the ball valve. This will help you assess if the valve is creating an abnormal pressure drop or is failing to maintain the required pressure in the system.
Leak Test: Conduct a pressure test by pressurizing the system and observing the valve for any signs of leakage. If there is a noticeable pressure drop, this can indicate a leak or a faulty seal inside the ball valve.
Interpreting Flow Rates and Pressure Readings:
Reduced Flow Rate: If the flow rate is lower than expected despite the valve being fully open, it could suggest a blockage or a damaged valve ball or seat.
Fluctuating Pressure: Inconsistent pressure readings indicate that the valve is not sealing properly, which could be due to damaged seals or a worn-out ball.
Steady Flow but Low Pressure: If the flow appears constant but the pressure is too low, the issue may lie in valve degradation that causes a loss of sealing effectiveness.
Sound-Based Diagnosis
Listening to the sounds produced by a ball valve during operation can provide valuable insight into the internal condition of the valve. Unusual sounds may indicate friction, wear, or other damage that requires attention.
Techniques for Identifying Unusual Noises:
Squeaking or Rattling: Squeaking or rattling sounds can indicate friction between the ball and valve seat. This may be caused by insufficient lubrication or dirt buildup inside the valve.
Grinding Noise: Grinding sounds are typically a sign of internal damage or wear, such as the ball rubbing against the valve seat, which can be caused by corrosion or physical damage to internal components.
Whistling: A whistling sound may suggest turbulence in the flow path, often due to a partial obstruction or misalignment within the valve.
When to Take Action:
If you hear any of the above noises, it’s important to shut down the system and inspect the valve for damage.
Prolonged exposure to friction can lead to further deterioration, resulting in valve failure if left untreated.
Checking Temperature and Pressure Readings
Monitoring the temperature and pressure of the fluid flowing through the valve can provide an early warning of a failing valve, especially when abnormal readings are detected.
How Abnormal Readings Can Signal Issues:
High Temperature: If the temperature of the valve or the surrounding area is higher than the manufacturer’s recommended limits, it can indicate overheating, which could cause seal degradation or distortion of valve components.
Low or Fluctuating Pressure: Unstable pressure readings might point to an internal leak or valve failure that’s not fully closing, allowing fluid to pass even when the valve is supposed to be shut off.
Using Sensors and Gauges:
Install temperature sensors and pressure gauges before and after the valve to continuously monitor the system’s performance. Comparing the readings will help identify discrepancies caused by the valve’s malfunction.
If you observe that the temperature is unusually high or pressure is dropping without a valid explanation, the valve may be failing, and corrective action should be taken immediately.
Preventive Maintenance to Avoid Valve Failure
Regular Inspection and Monitoring
Importance of Periodic Valve Inspections:
Identifying Early Issues: Regular inspection is essential for identifying issues such as leaks, corrosion, or wear before they result in significant damage. Catching problems early allows for proactive repair, avoiding costly shutdowns or system failures.
Visual Inspection: The valve body, seals, and moving parts should be checked for visible signs of degradation such as cracks, rust, or discoloration. Inspect the valve stem and actuator for any misalignment or leaks around the seals. The valve’s operation should be tested by turning the handle or checking actuator movement.
Leak Detection: Leaks around the valve stem or body may indicate worn-out seals or gaskets. Monitoring for leakage ensures early identification of failures and can help reduce the risk of contamination or fluid loss.
Monitoring System Parameters:
Temperature and Pressure: Continuous monitoring of system parameters, such as temperature and pressure, is crucial. Excessive heat or pressure can cause significant damage to ball valves. Ensure that the system is operating within the recommended temperature and pressure ranges to prevent overheating or overpressure conditions, which can compromise valve integrity.
Flow Control: Monitoring flow rates can also reveal potential issues with valve performance. A drop in flow rate or fluctuating pressure may indicate that the valve is failing to function properly.
Best Practices:
Schedule inspections regularly—monthly or quarterly, depending on the operating conditions.
Look for signs of leaks, wear, or corrosion during each inspection.
Keep an eye on pressure and temperature gauges and maintain accurate records.
Proper Lubrication and Seal Maintenance
Lubrication to Extend Valve Life:
Reducing Friction: Proper lubrication of valve components, especially the moving parts like the ball and stem, reduces friction and minimizes wear. Friction between the ball and valve seat can cause degradation, while proper lubrication ensures smooth valve operation and prevents damage to internal components.
Seal Maintenance: Regularly inspect and replace seals, gaskets, and O-rings. Seals play a crucial role in maintaining pressure integrity and preventing leaks. Over time, seals can become brittle, cracked, or worn, leading to leaks or pressure loss. Regular seal replacement ensures the valve’s sealing capabilities are maintained.
Recommended Practices for Lubrication:
Use high-quality lubricants that are compatible with the materials used in the valve and the fluid it controls.
Apply lubrication to the ball, stem, and actuator components during each inspection or service.
Check seals for signs of wear or degradation and replace them as needed.
Ensuring Proper Installation
The Importance of Proper Installation: Proper installation is crucial to prevent early valve failure. Incorrect installation can lead to immediate or long-term issues such as valve misalignment, leakage, or improper sealing. Common installation issues can include using the wrong materials, improper torque on bolts, or failure to align the valve properly within the system.
Key Installation Factors to Consider:
Torque: Proper torque ensures that bolts and valve components are tightened to the correct specifications. Over-tightening can lead to seal damage, while under-tightening can cause leaks. Always refer to the manufacturer’s specifications for the correct torque values.
Alignment: Ensuring that the valve is correctly aligned with the pipeline prevents undue stress on the valve’s internal parts. Misalignment can cause issues with valve operation, such as difficulty in turning or sticking, and may result in damage over time.
Material Compatibility: Choose materials that are compatible with the operating environment and the fluid being controlled. Mismatched materials can lead to chemical corrosion, accelerated wear, and reduced performance.
Best Practices:
Follow the manufacturer’s installation guidelines carefully.
Double-check alignment before securing the valve in place.
Use the correct gaskets, seals, and torque values to ensure optimal sealing and valve function.
Upgrading to Corrosion-Resistant Materials
Corrosion Resistance for Durability: Corrosion is one of the leading causes of valve failure, especially in harsh industrial environments where chemicals or extreme temperatures are involved. Ball valves made from corrosion-resistant materials such as stainless steel or specialized alloys offer enhanced durability and longevity.
Role of Corrosion-Resistant Alloys:
Stainless Steel: Stainless steel is one of the most common materials used for ball valves due to its resistance to corrosion, oxidation, and rust. It is ideal for use in industries such as oil and gas, chemical processing, and water treatment.
Alloy Options: In environments with highly corrosive fluids, higher-grade alloys (e.g., Hastelloy, Monel, or Inconel) may be required. These alloys provide even greater resistance to chemical attack and can withstand higher temperatures and pressures.
Choosing the Right Materials:
Always choose a valve made of materials that are resistant to the type of chemicals, fluids, and temperatures in your system.
For applications involving seawater or highly acidic substances, consider materials with higher resistance to corrosion.
Best Practices:
When replacing or upgrading ball valves, opt for corrosion-resistant materials to extend the valve’s lifespan.
Regularly check the condition of the valve body and internal components for early signs of corrosion.
Flow and Pressure Management
Implementing Flow Regulators: Ball valves control the flow of fluids, but if the flow rate is too high, it can put undue stress on the valve, leading to premature wear or failure. Installing flow regulators before the valve helps to manage the flow and ensures the valve operates within its rated capacity.
Pressure Relief Valves: Pressure relief valves are critical in preventing excessive pressure from building up in the system, which can damage the ball valve and other components. These valves automatically open when the pressure exceeds a preset limit, allowing excess fluid to escape and reducing stress on the valve.
Managing Excessive Pressure:
System Design: Ensure that the ball valve is selected for the correct pressure and temperature range based on the system’s specifications.
Pressure Relief Systems: In high-pressure applications, consider adding pressure relief systems to avoid overloading the ball valve and causing damage.
Best Practices:
Use flow regulators to maintain the desired flow rate and prevent excessive force on the valve.
Implement pressure relief systems or pressure regulators where necessary to prevent overpressure conditions.
Conclusion
We encourage readers to implement regular valve checks and proactive maintenance schedules to catch issues early. If you suspect a failing valve or are unsure about its condition, consider consulting with a professional valve maintenance service or supplier who can assess and provide the necessary repairs or replacements.
FAQ
What are the most common signs of ball valve failure?
Common signs include leaks, difficulty in valve operation (tightness or stiffness), unusual noises (grinding or rattling), and inconsistent flow or pressure.
Why is my ball valve leaking?
Leaks can occur due to worn-out seals, degraded gaskets, cracked valve bodies, or improper installation. Regular inspections can help identify and fix these issues before they worsen.
How can I prevent my ball valve from failing?
Preventive measures include regular inspections, proper lubrication, seal maintenance, and ensuring the valve is installed correctly. Monitoring pressure, flow, and temperature levels can also help prevent damage.
When should I replace a ball valve?
Replace a ball valve when it shows signs of extreme wear, or irreparable damage, or when repairs become cost-prohibitive. If the valve’s performance is unreliable even after repairs, replacement is recommended.
How do I diagnose ball valve fail?
Perform visual inspections for cracks, discoloration, or rust. Test the valve’s functionality by checking if it opens and closes smoothly. Pressure and flow tests can help identify leaks or inconsistencies in performance.
What are the consequences of neglecting a fail ball valve?
Neglecting a fail ball valve can lead to leaks, system inefficiency, or even catastrophic failure. This could result in costly repairs, downtime, or safety hazards in fluid control systems. Regular maintenance helps avoid such risks.