Vulcanization is a chemical process that involves treating rubber or synthetic materials with heat and a curing agent to improve their properties. In the context of hydraulic hoses, vulcanization transforms raw rubber or rubber compounds into a durable, elastic, and heat-resistant material that can withstand the stresses and challenges of high-pressure environments. During this process, the rubber’s molecular structure is cross-linked, which gives the hose its strength, flexibility, and resilience.
The Science Behind Hydraulic Hose Vulcanization
Hydraulic hose vulcanization is a complex chemical process that transforms raw rubber into a strong, durable, and flexible material, capable of withstanding the extreme conditions found in hydraulic systems. To understand why vulcanization is so crucial for hydraulic hoses, it’s important to dive into the science behind the process—starting with the chemistry, the role of heat, and the molecular transformation that occurs during vulcanization.
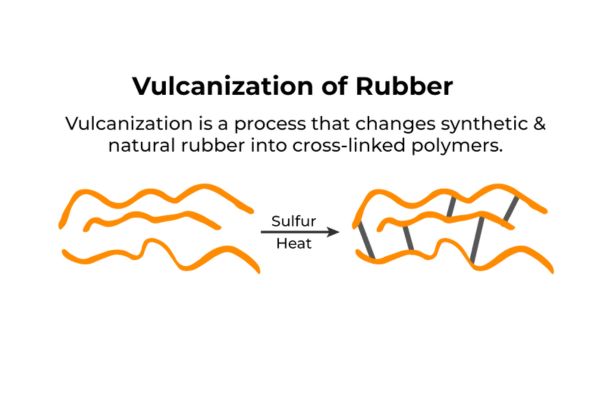
Rubber Vulcanization Chemistry: A Quick Overview
At its core, rubber vulcanization is a chemical reaction that involves the treatment of rubber with sulfur or other curing agents, heat, and pressure. This process changes the rubber’s molecular structure, making it stronger, more flexible, and less prone to degradation over time. Here’s a basic breakdown:
Raw Rubber: Natural rubber or synthetic rubber (like neoprene, nitrile, or EPDM) starts as a polymer—a long chain of molecules that slide past each other easily. While it has some elasticity, it’s not durable enough for high-pressure, high-temperature environments.
Curing Agents: To kick off the vulcanization process, sulfur is typically used as the curing agent. Other agents like peroxides may also be used, depending on the rubber type. Sulfur molecules form bonds between the polymer chains, creating a stronger and more rigid network.
Chemical Reaction: When the rubber is heated, sulfur atoms link up with the polymer chains through sulfur bridges, or cross-links. These bonds drastically change the way the rubber behaves, enhancing its elasticity, toughness, and overall performance.
End Result: The rubber is no longer a loose, slippery chain of molecules. Instead, it’s a tough, flexible network of interconnected chains that can withstand pressure, temperature fluctuations, and other stresses.
The Role of Heat in the Vulcanization Process
Heat is a critical factor in the vulcanization process because it activates the curing agents and speeds up the chemical reaction that creates cross-links between the polymer chains. Here’s how heat plays its part:
Condition | Result |
Too Low(<140) | Incomplete vulcanization; weak, unstable rubber |
Optimal(140-180) | Maximum bonding and performance |
Too High(>180℃) | Incomplete vulcanization; weak, unstable rubber |
Activating the Curing Agents: For sulfur to effectively bond with the polymer chains, it needs heat to become reactive. The right temperature—usually between 140°C to 180°C (284°F to 356°F)—is necessary to break the sulfur molecules into smaller components that can form cross-links with the rubber molecules.
Optimizing Reaction Time: The temperature needs to be maintained over a specific period to allow the chemical reaction to reach its full potential. If the temperature is too low, the vulcanization process will be incomplete, leaving the rubber weaker and more prone to failure. If the temperature is too high, it can cause the rubber to over-cure, making it brittle and prone to cracking.
Improved Rubber Properties: As heat drives the cross-linking process, the rubber becomes more durable, flexible, and resistant to wear and tear. Additionally, the heat helps drive off excess moisture or volatile compounds in the rubber, ensuring the final product is stable and ready for use in demanding environments.
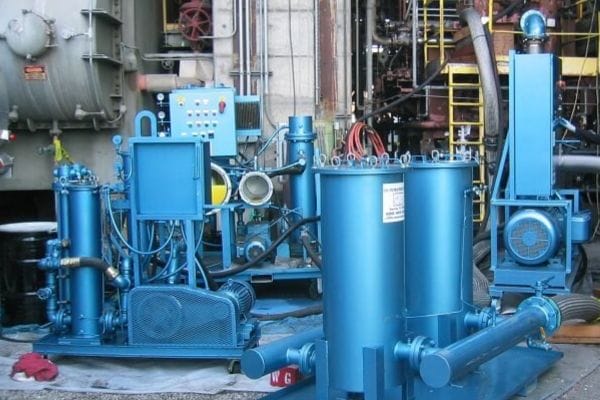
How Cross-Linking Strengthens Rubber at the Molecular Level
Cross-linking is the heart of the vulcanization process and the key to rubber’s newfound strength. But how does it actually work at the molecular level?
Polymer Chains and Elasticity: In its raw state, rubber is made up of long chains of polymer molecules. These chains can move around freely, allowing the material to stretch and return to its original shape. While this gives rubber its elasticity, it also makes it weak and prone to deformation under stress.
The Cross-Linking Process: During vulcanization, the curing agents (like sulfur) create bonds between the polymer chains. These bonds act like bridges, linking individual polymer chains into a more rigid structure. This network of interconnected chains prevents the molecules from sliding past one another too easily, significantly increasing the material’s strength and resistance to wear.
Enhanced Rubber Properties:
Stronger: The interconnected network makes the material far less likely to tear or deform under pressure.
More Elastic: The rubber retains its ability to stretch and return to its original shape, but it does so more efficiently without losing its structural integrity.
Heat and Pressure Resistant: The cross-linked structure prevents the rubber from softening or breaking down at high temperatures and pressures, which is essential for hydraulic systems.
More Durable: The material becomes resistant to environmental factors like UV light, ozone, and abrasion, extending the life of hydraulic hoses.
The Bottom Line: Cross-linking is what turns simple rubber into something far more resilient and capable of handling the demands of hydraulic systems. Without this crucial step in the vulcanization process, the hose would quickly degrade, leading to leaks, failure, and costly repairs.
The Hydraulic Hose Manufacturing Process: From Start to Finish
The manufacturing of hydraulic hoses is a detailed and precise process, requiring careful attention to material selection, construction, and quality control. Each stage of the process plays a vital role in ensuring that the final product is durable, reliable, and capable of withstanding the harsh conditions encountered in hydraulic systems.
Materials Used in Hydraulic Hose Production
The materials used in hydraulic hose manufacturing are carefully chosen to meet the demanding performance requirements of hydraulic systems. These materials provide the strength, flexibility, and resistance necessary for hoses to operate effectively under high pressure, extreme temperatures, and varying environmental conditions.
Rubber: Rubber is the most common material used in hydraulic hose construction. It provides excellent flexibility, durability, and resistance to heat, pressure, and abrasion. Various types of rubber, such as synthetic rubber and natural rubber, are selected based on the hose’s intended use and environmental factors.
Reinforcement Materials: To prevent the hose from bursting or collapsing under pressure, reinforcement layers are added to provide additional strength. Common reinforcement materials include:
Steel Wire: Steel wire braids or spirals are often used to reinforce hoses for high-pressure applications.
Textile Fabrics: Polyester, nylon, or other synthetic fibers are used for moderate-pressure hoses and add flexibility without compromising strength.
Kevlar® or Aramid: High-performance synthetic fibers like Kevlar® can be used for applications requiring exceptional strength and resistance to wear.
Inner Lining: The inner layer of the hydraulic hose is typically made from oil-resistant rubber or synthetic compounds, such as nitrile rubber. This lining prevents degradation caused by the hydraulic fluid passing through the hose.
Outer Cover: The outer layer is designed to provide protection against external elements, such as abrasions, UV rays, ozone, chemicals, and extreme temperatures. The cover is made from materials like PVC, neoprene, or EPDM rubber, depending on the intended environment and durability requirements.
The Key Stages of Hydraulic Hose Fabrication
The hydraulic hose manufacturing process involves several key stages that ensure the hose is built to withstand the demanding conditions of hydraulic systems. Each stage plays a crucial role in determining the performance and durability of the final product.
Preparation of Materials: The first step in manufacturing hydraulic hoses is gathering all the necessary materials: rubber compounds, reinforcement materials, inner linings, and outer covers. These materials are carefully tested to ensure they meet the specifications required for the intended use of the hose.
Extrusion of Rubber: In this stage, the rubber compounds are melted and forced through an extrusion machine to form the inner and outer layers of the hose. The rubber is shaped into tubes, which will later be reinforced with layers of steel wire or fabric. The extrusion process ensures uniform thickness and consistency throughout the hose.
Reinforcement Layer Application: After the rubber tube has been formed, reinforcement layers are added. These can include braiding or spiraling steel wire, or laying down synthetic textile fibers. This reinforcement strengthens the hose and helps it withstand the internal pressures it will be subjected to. The reinforcement is applied through a process called braiding (for steel wire) or spiraling (for textile fibers) over the rubber core.
Covering the Hose: Once the hose has been reinforced, the next step is to apply the outer cover. This cover provides protection against abrasions, chemicals, UV rays, and other environmental factors. The outer cover is typically extruded over the reinforcement layers and cured to ensure a durable finish.
Cutting and Fitting: After the hose is formed, it is cut into specific lengths based on the customer’s requirements. Fittings and connectors are then attached to the hose ends. These fittings are typically made of brass, carbon steel, or stainless steel, depending on the intended application and the type of hydraulic fluid being used.
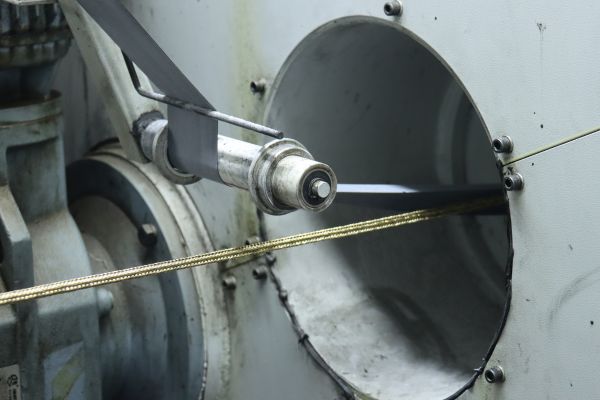
Testing and Inspection
Once the hose is fully assembled, it undergoes rigorous testing to ensure it meets the required standards. Common tests include:
Pressure testing: Ensures the hose can withstand internal pressure without bursting.
Flexibility testing: Assesses the hose’s ability to bend without cracking or breaking.
Leak testing: Ensures the hose is free from leaks at the connection points and along the length.
How Vulcanization Fits Into the Hose Production Cycle
Vulcanization is a critical step in the hydraulic hose production process. It is during this stage that the rubber components of the hose undergo the chemical transformation that makes them durable, flexible, and heat-resistant. Here’s how vulcanization fits into the overall production cycle:
Pre-Vulcanization (Before Reinforcement): Some hoses undergo initial vulcanization before the reinforcement layers are added. This process ensures that the rubber core has the desired properties of strength and flexibility. After this stage, the core is ready to be reinforced with steel wire or fabric.
Vulcanization of the Completed Hose Assembly: Once the rubber core is reinforced and the outer cover is applied, the entire hose assembly is placed in a vulcanizing press. The hose is heated to the required temperature for a specified period, which allows the sulfur and curing agents to cross-link the rubber molecules, giving the hose its final characteristics. The process typically takes place in a steam autoclave or molding press.
Curing and Finalization: After vulcanization, the hose is allowed to cool and set. The heat treatment strengthens the rubber, making it resistant to internal pressure, temperature extremes, and external wear. This process is also crucial for ensuring the hose’s flexibility remains intact, allowing it to bend and stretch without cracking under pressure.
Post-Vulcanization Inspection: Once vulcanization is complete, the hose undergoes final quality inspections. The curing process ensures that the rubber has the necessary elasticity, strength, and durability to perform under the demanding conditions of hydraulic systems. If the hose passes all tests, it’s ready for shipment.
The Hose Curing Process: How Vulcanization Works
The curing process, also known as vulcanization, is a critical step in the manufacturing of hydraulic hoses. It is during this phase that rubber undergoes a chemical transformation, enhancing its strength, elasticity, heat resistance, and overall durability.
What is the Curing Process for Hydraulic Hoses?
The curing process for hydraulic hoses involves heating the rubber (or rubber compounds) and adding specific curing agents, like sulfur, to initiate a chemical reaction. This reaction causes rubber molecules to bond together through cross-linking, which strengthens the material and makes it more resistant to wear and environmental damage.
Here’s how it works:
Raw Rubber Preparation: Before curing, the raw rubber is mixed with various chemicals (such as sulfur, accelerators, stabilizers, and plasticizers) to improve its performance. These ingredients are designed to enhance properties like heat resistance, chemical stability, and flexibility.
Heat Application: The rubber is then subjected to heat—typically between 140°C and 180°C (284°F and 356°F)—for a specific period of time. The temperature causes the sulfur molecules to break down and form sulfur bridges (cross-links) between the polymer chains in the rubber.
Cross-Linking: The sulfur bridges created by the heat cause the polymer chains to link together in a network. This cross-linking process turns the rubber from a soft, flexible material into a more rigid and durable one, significantly enhancing its ability to withstand pressure, temperature fluctuations, and physical wear.
Final Product: After the curing time has been completed, the rubber is no longer in its original form. It is now a durable, heat-resistant, and flexible material that can handle the harsh conditions in which hydraulic hoses operate. The vulcanization process is essential for giving the hose its final strength and performance characteristics.
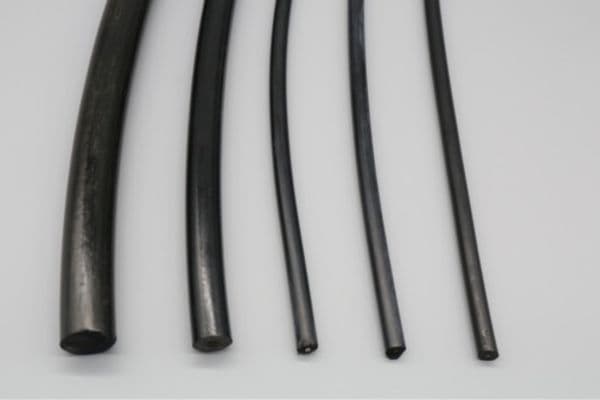
Key Factors Affecting the Curing Time and Temperature
The curing time and temperature are critical factors in determining the final quality and performance of the hydraulic hose. If these factors are not carefully controlled, the rubber may either be over-cured (making it brittle) or under-cured (making it weak and prone to failure). Below are the key factors that influence curing time and temperature:
Temperature Control: The heat applied during the curing process is essential for activating the curing agents and promoting cross-linking. However, too much heat can cause the rubber to degrade or become brittle, while too little heat can result in incomplete curing. The ideal temperature range typically lies between 140°C and 180°C, but it varies depending on the type of rubber and the curing agents used.
Curing Time: The amount of time the rubber is exposed to heat directly affects the degree of cross-linking. Curing time typically ranges from 10 minutes to several hours, depending on factors like the thickness of the hose, the type of rubber, and the specific application. Longer curing times can lead to a stronger, more durable hose, but excessive curing can cause the rubber to become too rigid and lose flexibility.
Rubber Thickness: The thickness of the hose material impacts both curing time and temperature. Thicker hoses require more time to cure effectively because the heat needs to penetrate deeper into the material. If not fully cured, the inner layers of the hose may remain soft and susceptible to failure, while the outer layers may become too hardened.
Type of Rubber and Curing Agents: Different types of rubber require different curing agents and conditions. For instance, synthetic rubbers like nitrile or EPDM may require different temperatures or curing times compared to natural rubber. The choice of curing agent, such as sulfur or peroxides, also impacts the curing process, with sulfur-based curing agents typically used for greater durability and heat resistance.
Pressure During Curing: Some curing processes apply pressure during vulcanization to ensure that the rubber remains properly shaped and free from air bubbles or voids. Pressure is particularly important for hoses designed to handle high-pressure hydraulic fluids, as it ensures the hose’s integrity during the curing phase.
Conclusion
As technology has evolved, so has the vulcanization process, enabling the production of hoses that can cope with more extreme conditions. If you still have questions about the vulcanization process for your hose products, feel free to contact Topa and we can help you with your questions.
FAQ
What is hydraulic hose vulcanization?
Hydraulic hose vulcanization is a process where rubber compounds are heated and treated with curing agents like sulfur to improve the material’s strength, elasticity, heat resistance, and overall durability. This makes the hose suitable for high-pressure hydraulic systems.
Why is vulcanization important for hydraulic hoses?
Vulcanization strengthens the rubber, making hydraulic hoses more durable, flexible, and resistant to extreme temperatures and pressures. This ensures that hoses can perform reliably over long periods, even in harsh conditions.
How does vulcanization improve hose performance?
Vulcanization creates cross-links between the polymer chains in the rubber, which improves the hose’s resistance to wear, heat, pressure, and aging. This process enhances the hose’s strength, flexibility, and longevity.
What factors affect the vulcanization process?
The key factors include curing temperature, curing time, the type of rubber and curing agents used, and the thickness of the hose. Proper control of these variables ensures consistent quality and performance.
How long does the vulcanization process take?
The vulcanization process typically lasts anywhere from 10 minutes to several hours, depending on the hose thickness, material, and temperature. The goal is to ensure the rubber is fully cured to achieve the desired strength and flexibility.
Can vulcanized hydraulic hoses be customized?
Yes, hydraulic hoses can be customized in terms of size, material, reinforcement type, and even color. Vulcanization ensures that the final hose meets specific performance requirements for different industrial applications.