Ball valve sealing is far more than just a mechanical function; it’s what keeps the valve’s operation smooth and leak-free. Seals are the unsung heroes in ball valve design, maintaining pressure, ensuring flow control, and preventing potentially hazardous leaks. Without proper sealing, a ball valve can fail prematurely, leading to operational inefficiencies, costly repairs, and even safety hazards in some environments.
What is Ball Valve Sealing?
Ball valve sealing is the process by which a ball valve prevents leaks and ensures smooth operation by creating a tight seal between its internal components. This sealing is crucial for the valve’s ability to control fluid flow effectively, whether it’s in a high-pressure gas pipeline or a water distribution system. Without proper sealing, a ball valve could fail to function properly, leading to unwanted leaks, pressure loss, or even complete system shutdowns.
Understanding the Basic Function of Ball Valve Sealing
At its core, a ball valve works by rotating a spherical ball with a hole or port through which fluid flows. When the valve is in the “closed” position, the hole in the ball aligns with the valve body, and the fluid flow is stopped. Sealing in a ball valve happens primarily around the ball and the valve seat. The tight contact between these two components ensures that no fluid can escape around the ball, preventing leaks. The strength and durability of the seal directly impact the valve’s performance, ensuring that it operates reliably over time, even in demanding environments.
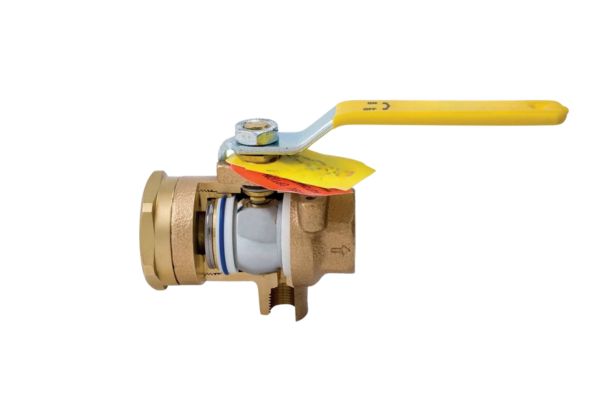
Components Involved in the Sealing Mechanism
The sealing mechanism in a ball valve involves several key components that work together to ensure the valve operates efficiently:
- Ball – The central moving part of the valve, typically made of stainless steel or other durable materials. The ball has a hole (port) that controls the flow of fluid. The surface of the ball must be smooth and free from defects to maintain an effective seal.
- Valve Seat – This is the stationary part of the valve that directly interfaces with the ball. The seat is often made from soft, resilient materials like PTFE (polytetrafluoroethylene) or elastomers. It forms the primary seal when the ball presses against it, stopping the flow of fluid.
- Seals or O-Rings – These are placed around the ball or the valve seat to provide an extra layer of sealing. The O-rings help maintain pressure and prevent any leakage around the ball or between the ball and the seat.
- Spring Mechanisms – In many designs, springs are used to ensure constant pressure against the ball or seat. They help maintain the seal even when there are changes in pressure or temperature within the system.
- Stem and Packing – The stem connects the actuator (manual lever or motor) to the ball. The packing around the stem ensures that there are no leaks along this critical point, preventing fluid from escaping.
The Mechanics of a Ball Valve: How Does Sealing Work?
A ball valve is a reliable and effective mechanism used to control the flow of fluids in pipelines and systems across various industries. Understanding the mechanics of how a ball valve operates and how sealing works is essential for maintaining the performance and longevity of the valve.
The Interaction Between the Ball, Seat, and Seals
The key to proper sealing lies in the interaction between the ball, the valve seat, and the seals:
- Ball and Seat Interaction – The ball is designed to create a precise fit against the valve seat when the valve is closed. The smooth surface of the ball is essential for creating a tight, effective seal. The seat, usually made from softer materials, is compressed against the ball to prevent leakage. Over time, the material properties of the seat ensure that it conforms to the ball, maintaining a secure seal.
- Seals and O-Rings – In addition to the ball and seat, seals and O-rings around the ball or the valve body further prevent fluid from escaping. These components help to seal the gaps between moving parts, such as where the stem enters the valve body. The seals maintain pressure and prevent leakage, especially in high-pressure applications where even the smallest gap could result in a significant failure.
- Spring Pressure – In some ball valves, springs are used to maintain constant pressure against the ball or seat. This is particularly important when the pressure changes within the system. Springs ensure that the seat remains tightly compressed against the ball, preventing any leakage even when there is a fluctuation in pressure.
How Pressure and Fluid Impact Sealing Performance
Pressure and fluid characteristics play a significant role in the sealing performance of ball valves. Here’s how these factors influence the sealing mechanism:
- Internal Pressure – The pressure of the fluid in the pipeline pushes against the ball and seat. When the pressure increases, the ball is forced tighter against the seat, ensuring a better seal. However, excessive pressure can also lead to damage or wear of the sealing components if not properly managed.
- Fluid Type – The nature of the fluid—whether it’s gas, liquid, or slurry—can impact the sealing materials. Liquids with low viscosity, such as water, tend to flow easily and require a well-formed seal. On the other hand, gases or highly viscous fluids exert different forces on the seal, which may require specific seat materials and sealing technologies to handle them effectively.
- Temperature Effects – Fluid temperature affects both the material properties of the ball and the seat. Higher temperatures can cause certain materials to soften, potentially compromising the seal. Conversely, extremely low temperatures can make some seals brittle, leading to failures. Proper material selection and temperature management are crucial to maintaining effective sealing performance.
- Vibration and Movement – In systems with high vibration or where the valve experiences frequent opening and closing cycles, the seal must be durable enough to handle the repeated stress. Over time, the ball and seat may wear down due to the constant interaction, potentially weakening the seal and leading to leakage.
The Double Piston Effect: A Game-Changer in Sealing Technology
The Double Piston Effect (DPE) is a revolutionary design principle used in ball valve technology to enhance sealing performance, especially in high-pressure and high-demand applications. This innovative technology has drastically improved the reliability and efficiency of ball valves, ensuring leak-proof operation even in the most challenging environments.
What is the Double Piston Effect (DPE)?
The Double Piston Effect (DPE) is a unique valve seat design that uses two distinct sealing forces to improve the sealing performance of ball valves. Unlike traditional single-seal designs, DPE incorporates a system where the valve seat is pressed against the ball from two different directions—both from the pipeline pressure (downstream) and the valve chamber pressure (upstream).
In essence, DPE is designed to ensure that both the upstream and downstream pressures work together to keep the ball tightly sealed against the valve seat. This dual-action sealing mechanism provides superior sealing efficiency and ensures that the valve maintains its leak-proof integrity, even when subjected to fluctuating or high-pressure conditions.
The core of the DPE system lies in its two piston-like actions, which are created by the pressure differences inside the valve. The downstream pressure exerts force on the valve seat, while the upstream pressure acts as a secondary force, pushing the seat towards the ball, creating a strong, leak-resistant seal. This self-pressurizing feature eliminates the need for external springs or additional mechanisms to maintain the seal.
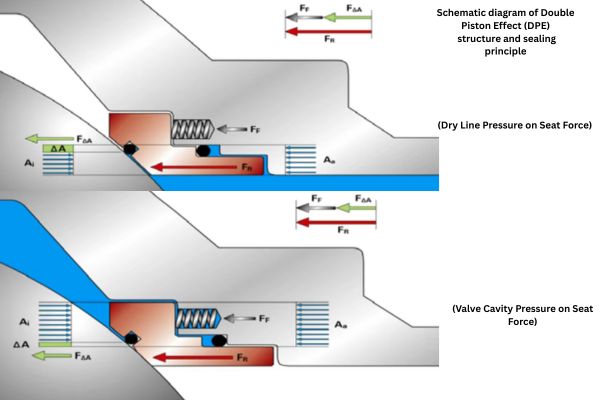
How DPE Enhances Ball Valve Sealing
The Double Piston Effect offers a host of advantages that enhance the overall sealing of ball valves:
- Enhanced Sealing Force – By utilizing both upstream and downstream pressures, DPE generates a more consistent and powerful sealing force than single-seal designs. This dual-force mechanism ensures that the ball is firmly pressed against the seat, creating a tighter seal that is less likely to fail under pressure.
- Leak-Proof Operation – The primary benefit of DPE is its ability to prevent leakage, especially in high-pressure systems. The combined force from both directions ensures that no fluid can escape around the ball, making the valve far more reliable and efficient than traditional designs.
- Self-Adjusting Seal – DPE is self-adjusting to pressure changes. As the pressure in the system fluctuates, the force exerted on the ball valve seat changes as well, ensuring that the seal remains tight regardless of pressure fluctuations. This makes DPE ideal for applications where pressure levels are not constant.
- Reduced Wear and Tear – Traditional sealing mechanisms may require frequent adjustments or replacements due to wear over time. The DPE system, by contrast, provides a longer-lasting seal, reducing the frequency of maintenance and extending the overall service life of the valve.
- Improved Performance in Harsh Environments – DPE significantly improves sealing performance in extreme conditions, including high temperatures, aggressive chemicals, and high-pressure systems. Its design reduces the risk of failure, making it perfect for industries like oil and gas, chemical processing, and power generation.
Ball Valve Sticking Failure Diagnosis and Resolution
Ball valves are widely used in industrial pipeline systems due to their reliable sealing and durability, making them suitable for high-pressure, high-temperature, and harsh conditions. However, over time, ball valves may experience “sticking” failures, where the valve cannot open or close properly, affecting fluid control and system efficiency. This article will provide a detailed guide on how to diagnose ball valve sticking failures and offer effective methods for resolution, helping users quickly restore equipment to normal operation.
Symptoms of Ball Valve Sticking Failure
Ball valve sticking failures typically manifest when the valve cannot be rotated manually or automatically, causing the valve to be in a “stuck” state. Specific symptoms include:
- Excessive Operating Torque: When attempting to open or close the ball valve, an unusually large force is required to rotate the valve.
- Inability to Open or Close: Regardless of whether it is manually or automatically operated, the ball valve cannot be smoothly rotated, and may become jammed or stagnant.
- Leaks: Leaks may occur on the valve surface, even when the valve is in the closed position, which could be due to a jammed or damaged sealing seat preventing a proper seal.
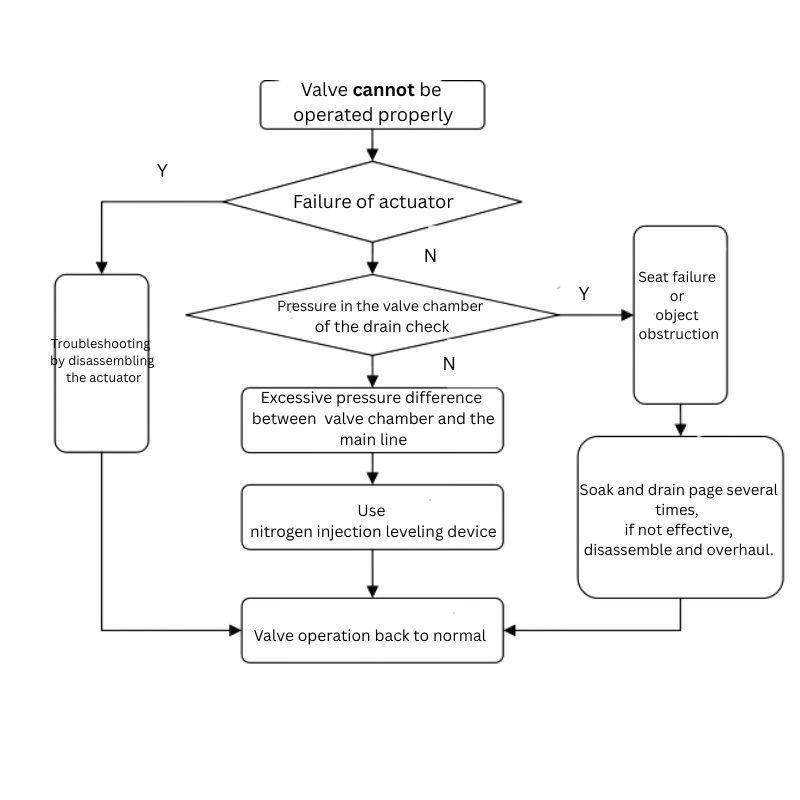
Methods for Diagnosing Ball Valve Sticking Failures
Diagnosing whether a ball valve has a sticking failure is critical and involves a series of checks and troubleshooting steps to identify the specific cause. Below are common diagnostic methods:
Step 1: Check the Actuation Gearbox
The drive mechanism of the ball valve is often powered by an actuation gearbox. If the gearbox experiences severe corrosion, bearing damage, or foreign object blockages, it may cause the valve to fail to operate. The following checks should be performed:
- Open the gearbox and inspect the gears and bearings for wear or damage.
- Check if debris or contaminants have blocked the gears or bearings, preventing smooth rotation.
- If problems are found, clean out foreign objects, inspect the lubrication, and replace any damaged components.
Step 2: Inspect the Valve Chamber for Pressure or Contaminants
If the gearbox is not the issue, the next step is to check the valve chamber for pressure or contaminants. The specific steps include:
- Check for Gas Pressure: If there is gas pressure in the valve chamber, this can help diagnose the sticking issue as being caused by a jammed sealing seat. Normally, the sealing seat should have 0.003 inches of lateral movement. Hardened sealing grease, foreign particles in the seat gaps, or a malfunctioning spring could cause a jam.
- Perform a Purging Operation: Purge the valve to remove debris, contaminants, or hardened sealing grease from the valve chamber.
Step 3: Check the Pressure Difference Between the Valve Chamber and Pipeline
If there is no gas pressure in the chamber, the sticking failure could be due to excessive pressure difference between the valve chamber and the pipeline. In this case, the sealing seat may be under excessive pressure, preventing normal operation. To resolve this, perform the following checks:
- Pressure Difference Analysis: Check if the pressure difference between the valve chamber and the pipeline is too large. A large pressure difference can cause the sealing seat to press too tightly against the ball, requiring excessive operating torque and resulting in a stuck valve.
- Purge and Adjust: Inject gas or cleaning fluid through the purge port to balance the pressure difference between the valve chamber and pipeline, resolving the sticking failure caused by the excessive pressure difference.
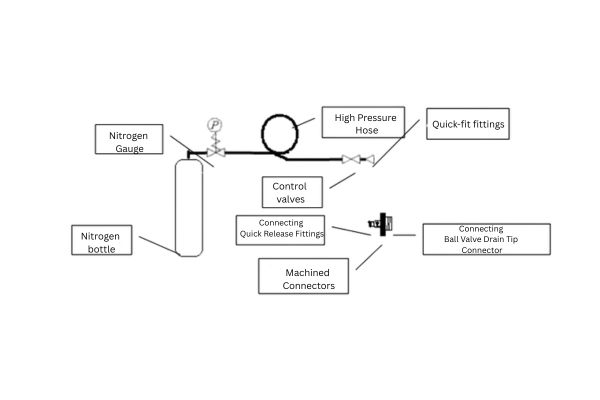
Methods for Resolving Ball Valve Sticking Failures
Once the cause of the sticking failure has been confirmed, the next step is to implement effective measures to restore normal valve operation.
Resolving Actuation Gearbox Failures
If the sticking failure is caused by a problem with the actuation gearbox, preventative maintenance is key. Common resolution methods include:
- Regular Inspections: Open the gearbox annually to inspect the lubrication, rust prevention, and integrity of gears and bearings. Clean out any water or foreign particles inside the gearbox and replace the lubrication with fresh grease.
- Replace Damaged Components: If any components such as bearings are found to be damaged, replace them promptly to ensure smooth valve operation.
Resolving Sealing Seat Jamming Failures
Sealing seat jams are a common cause of ball valve sticking, often due to hardened sealing grease or contaminants. The resolution methods include:
- Cleaning the Sealing Seat: Inject cleaning fluid and soak the sealing seat to remove hardened sealing grease and contaminants. Purge the valve further to clean any remaining debris from the valve chamber.
- Check the Sealing Spring: If the valve still cannot operate after cleaning, the sealing seat spring may be defective or deformed. In this case, the valve should be disassembled for inspection, and the spring or any other damaged sealing components should be replaced.
Resolving Excessive Pressure Difference Failures
To resolve sticking failures caused by excessive pressure differences, perform the following:
- Gas Injection Device: Install a purge gas injection device as shown in the diagram, allowing gas to be injected to balance the pressure difference between the valve chamber and pipeline, eliminating the sticking failure caused by excessive pressure differences.
- Install Two-Valve Purge Design: For systems requiring pressure balancing during purge operations, it is recommended to use a two-valve purge design to improve maintenance convenience and safety.
Hazards of Using Forceful Methods
When ball valves experience sticking failures, some operators may resort to forceful methods (such as using a force tool or multiple people working together). However, this can lead to significant hazards:
Gearbox Damage: Forceful operation can subject the gearbox to excessive stress, potentially leading to the housing breaking or gears being damaged.
Sealing Damage: Forcing the valve open can cause scratches on the ball surface, which can damage the seal, resulting in serious internal leakage.
Operator Injury: Using a force tool or multiple operators simultaneously increases the risk of operator injury.
Therefore, when a ball valve is not operating normally, avoid using improper methods to force it. Instead, thoroughly analyze the cause of the failure and take appropriate steps to resolve it.
The Dangers of Forceful Operations
In industrial equipment, especially when ball valves encounter failures, many operators may resort to improper, forceful methods (such as using force tools, multiple people operating together, etc.) due to impatience or a lack of understanding of the equipment. These “forceful operations” may seem like they solve the problem in the short term, but they can lead to severe consequences and even greater damage. Below are some common hazards associated with forceful operations:
Gearbox Damage
The drive mechanism of a ball valve is typically powered by a gearbox, which contains precision components like gears and bearings that are responsible for opening and closing the valve. If forceful operations are used when the valve fails to operate, such as applying excessive force or using inappropriate tools, the gearbox may be subjected to excessive load, resulting in the following issues:
- Gear Damage or Deformation: Over-application of force can subject the gears to uneven stress, potentially leading to gear breakage or deformation, which could cause the valve to completely fail.
- Bearing Damage: Forceful operation may damage the bearings, affecting the smooth operation of the transmission system. In severe cases, it may cause the bearings to seize, rendering the valve inoperable.
These issues not only render the ball valve useless but can also lead to costly repairs and the replacement of damaged parts.
Seal Damage
The sealing capability of a ball valve is crucial for its proper function. The contact between the sealing seat and the ball requires precise and uniform pressure. If forceful operations are applied while the valve is stuck, it may cause severe scratches or indentations on the ball’s surface, thereby damaging the seal. Below are the potential consequences:
- Seal Surface Scratching: Forceful operation can cause uneven contact between the seat and the ball, leading to scratches or abrasions. This significantly reduces the sealing effect, even potentially causing leakage.
- Damaged Sealing O-rings: Excessive pressure or improper operation can cause the sealing O-rings to crack or permanently deform, losing their sealing function, which results in valve leakage and jeopardizes system safety.
- Internal Leaks: Damaged seals can cause internal leakage, affecting system pressure and fluid control, and potentially leading to hazardous leaks, such as chemical spills or fire risks.
These issues not only impair the efficiency of the equipment but also pose safety hazards, increasing maintenance costs.
Operator Injuries
During forceful operations, operators are also exposed to significant safety risks. Since these operations often require a lot of force, they can lead to injuries. Common injuries include:
- Mechanical Crushing: When excessive force is applied, parts of the body, such as hands or legs, may get caught by the valve or force tools, causing severe crushing injuries.
- Slipping or Loss of Control of Tools: When using inappropriate tools, they may slip or lose control, and flying debris or parts can injure operators.
- Overexertion: When multiple people operate the valve together with force, it may lead to uncoordinated efforts, increasing the likelihood of accidental injuries.
Therefore, ensuring operator safety is extremely important, and forceful operations should be avoided when dealing with a stuck valve.
Further Equipment and System Damage
Excessive, forceful operations may not only damage the ball valve itself but could also affect the entire system. Since the ball valve is a crucial component of the fluid system, any failures resulting from forceful operations can impact the system’s overall performance, leading to:
- Pipeline Pressure Instability: Damage to the ball valve may affect the pressure balance in the pipeline, causing extreme pressure fluctuations and even leading to pipe rupture.
- System-wide Failures: Damage to the valve may affect other components within the system, causing a chain reaction that leads to a complete system failure, increasing repair difficulty and cost.
- Operational Shutdown: If the ball valve cannot open or close properly, the system may require a shutdown for repairs, causing production delays, time waste, and production losses.
Increased Repair Costs and Downtime
The damage caused by forceful operations is often irreversible. Repairing these issues may require replacing damaged components or undertaking major repairs. Compared to regular maintenance, fixing damage caused by forceful operations is not only expensive but also usually requires extended downtime. This is a significant cost burden for any production system that relies on this equipment.
Key Measures to Avoid Forceful Operations
To avoid the aforementioned issues, operators should take a scientific and rational approach to dealing with ball valve failures:
- Calmly Diagnose the Fault: Start by inspecting, purging, and adjusting the pressure to accurately diagnose the cause of the failure, avoiding blind operation.
- Use Proper Tools: When a valve is stuck, specialized tools should be used, not force tools.
- Regular Maintenance: Regularly inspect the ball valve’s drive components, sealing seats, and O-rings, and clean off any buildup or contaminants to ensure the valve is in good working condition.
- Train Operators: Operators should undergo professional training to master the correct operating techniques and avoid equipment damage and personal injury due to improper operation.
Conclusion
To maximize the performance of your ball valves and prevent costly failures, start by adopting best practices for valve sealing. Ensure that your ball valve selection aligns with your operational needs, and commit to a regular maintenance schedule. Additionally, consider advanced sealing technologies like DPE for high-pressure applications to enhance sealing reliability and longevity. If you haven’t yet, now is the perfect time to review your existing ball valves, perform necessary upgrades, and integrate effective sealing solutions.
FAQ
What is ball valve sealing?
Ball valve sealing refers to the mechanism that ensures a tight seal between the ball and the valve seat, preventing fluid leakage when the valve is closed.
What causes a ball valve to leak?
Leaks in a ball valve can be caused by worn or damaged seals, misalignment between the ball and seat, improper installation, or buildup of debris affecting the seal.
How do I maintain ball valve seals?
Regular maintenance includes inspecting the seals, lubricating moving parts, cleaning debris, and replacing damaged components to ensure long-lasting performance.
What is the Double Piston Effect (DPE) in ball valves?
DPE is a sealing design where the pressure from both the upstream and downstream sides pushes the valve seat tightly against the ball, improving sealing efficiency, especially in high-pressure systems.
Can ball valve seals handle high-pressure applications?
Yes, ball valve seals are designed to handle high-pressure conditions, especially with technologies like DPE, which enhances the sealing force under high pressure.
How often should I inspect ball valve seals?
Ball valve seals should be inspected regularly as part of routine maintenance, particularly in high-pressure or critical systems. Depending on usage, inspections may be required annually or more frequently.