Heavy-duty trucks operate under demanding conditions that place significant stress on hydraulic cylinder systems. These critical components must deliver consistent performance while maintaining durability across extended service intervals. So, where do you optimize? Keep reading for detailed optimization details!
Understanding Hydraulic Cylinder Systems in Heavy-duty Trucks
Core Components and Functionality
To effectively optimize hydraulic cylinder systems, it’s essential to understand the key components and their functions:
Cylinder Barrel: The main body housing internal components and containing pressurized hydraulic fluid.
For optimization, focus on:
- Regular inspection for internal scoring or damage
- Verification of proper wall thickness for operating pressures
- Monitoring for signs of internal corrosion or contamination
Piston and Piston Rod: The piston moves within the cylinder barrel, while the connected rod transfers force to external mechanisms.
Optimization recommendations:
- Inspect for straightness and surface damage during maintenance
- Verify proper chrome plating thickness and condition
- Check for signs of bending or misalignment under load
Cylinder Head and Cap: These components seal the ends of the cylinder and provide mounting points.
Key optimization points:
- Ensure proper torque on all fasteners
- Verify alignment during installation and maintenance
- Check for signs of leakage or stress cracking
Seals and Bearings: Critical for preventing fluid leakage and maintaining proper alignment.
Optimization focus:
- Implement appropriate seal selection for specific operating conditions
- Establish regular replacement intervals before failure occurs
- Ensure proper installation techniques to prevent damage
Hydraulic Fluid: Serves as the medium for transferring energy while lubricating moving parts and dissipating heat.
Optimization strategies:
- Select fluid viscosity appropriate for operating temperature range
- Implement regular fluid analysis program
- Maintain proper fluid levels and change intervals
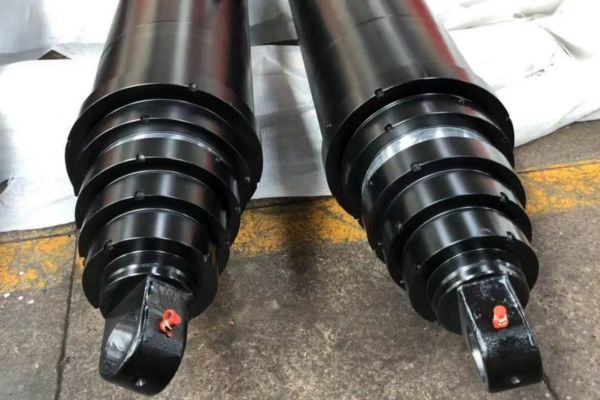
Performance Requirements in Heavy-duty Applications
Understanding the specific performance demands helps prioritize optimization efforts:
High Load Capacity: Recommendations for optimizing load handling:
- Calculate actual operating loads and maintain 25% safety margin
- Implement pressure relief protection to prevent overloading
- Monitor for signs of stress during peak loading conditions
Operational Precision: Strategies to maintain precise movement control:
- Eliminate air from the system through proper bleeding procedures
- Adjust flow control valves for smooth operation
- Implement proper counterbalance valves for suspended loads
Rapid Response: Techniques to optimize response characteristics:
- Minimize line lengths between valves and cylinders
- Properly size hydraulic lines to reduce flow restrictions
- Eliminate unnecessary fittings and direction changes in hydraulic circuits
Thermal Stability: Methods to maintain consistent performance across temperature ranges:
- Install temperature monitoring on critical cylinders
- Implement appropriate cooling systems for continuous operation
- Select seals rated for the full temperature range experienced
Contamination Resistance: Practical approaches to minimize contamination impact:
- Install high-quality filtration systems rated for operating conditions
- Implement proper cylinder rod protection during operation
- Establish clean maintenance protocols to prevent introducing contaminants
Energy Efficiency: Techniques to optimize energy consumption:
- Right-size cylinders for the application to avoid wasted energy
- Implement regenerative circuits where appropriate
- Consider load-sensing hydraulic systems for variable demand applications
Design Optimization Strategies
Material Selection and Surface Treatments
Practical recommendations for material selection to balance performance and lifespan:
- Cylinder Barrel Materials:
- For standard applications, specify SAE 1045 or 4140 alloy steel with proper heat treatment
- For corrosive environments, consider chrome-plated or nickel-plated internal surfaces
- Specify proper honing finish (typically 10-20 microinch) for optimal seal performance
- Piston Rod Materials:
- Specify induction-hardened carbon steel with chrome plating (minimum 0.001″ thickness)
- For corrosive environments, consider stainless steel or nickel-chrome plated rods
- Verify surface hardness (minimum 55 HRC) and finish (maximum 8 microinch) specifications
- Surface Treatments:
- Implement hard chrome plating with post-plate grinding and polishing
- Consider HVOF (High Velocity Oxygen Fuel) coatings for extreme wear applications
- Specify proper surface finish requirements in all component specifications
- Seal Materials:
- For standard applications, specify polyurethane or NBR (Nitrile) compounds
- For high-temperature applications, select Viton or other fluoroelastomer compounds
- For extreme pressure applications, implement PTFE-based seal systems with proper backup rings
Geometric Design Considerations
Practical geometric optimization recommendations:
- Cylinder Bore-to-Rod Ratio:
- For push-dominant applications, maintain ratio between 1.5:1 and 2:1
- For pull-dominant applications, consider larger rod diameters (ratio closer to 1.3:1)
- Verify ratio calculations based on actual operating pressures and required forces
- Stroke Length Optimization:
- Limit stroke length to 10x rod diameter to prevent deflection issues
- For longer strokes, increase rod diameter or implement intermediate rod supports
- Calculate critical buckling load for push applications with long strokes
- Wall Thickness Calculations:
- Calculate minimum wall thickness based on maximum system pressure plus 25% safety factor
- Increase thickness in high-stress mounting areas
- Verify calculations using appropriate pressure vessel formulas for specific materials
- Cushioning Mechanisms:
- Implement adjustable cushioning for cylinders operating at high speeds
- Set cushioning to decelerate over the last 10-15% of stroke
- Regularly verify cushioning adjustment during maintenance intervals
- Port Design and Placement:
- Size ports based on maximum flow requirements (typically 15-25 ft/sec velocity)
- Position ports to minimize cross-flow and turbulence
- Consider SAE straight thread O-ring ports for reliable sealing
- Mounting Configuration:
- Select mounting style based on load direction and alignment requirements
- For pivoting applications, implement self-aligning mounts with proper bearings
- Ensure mounting structures are sufficiently rigid to prevent deflection under load
Enhancing Durability and Lifespan
Seal System Optimization
Practical seal system recommendations for maximum lifespan:
- Multi-Stage Sealing Systems:
- Implement primary and secondary sealing elements for critical applications
- Use wiper seals appropriate for the operating environment
- Consider buffer seals for applications with pressure spikes
- Seal Profile Engineering:
- Select step-cut profiles for reduced friction in high-cycle applications
- Implement pressure-activated designs for high-pressure systems
- Consider composite seals combining multiple materials for optimal performance
- Seal Material Combinations:
- Use PTFE-based compounds for high-temperature or high-speed applications
- Select polyurethane for general-purpose applications with good wear resistance
- Implement specialized elastomers only when operating conditions require them
- Seal Housing Design:
- Verify proper groove dimensions according to seal manufacturer specifications
- Implement proper chamfers to prevent seal damage during installation
- Specify appropriate surface finish in seal contact areas
- Lubrication Management:
- Ensure hydraulic fluid maintains proper lubrication properties
- Consider pre-lubrication of seals during installation
- Implement proper break-in procedures for new or rebuilt cylinders
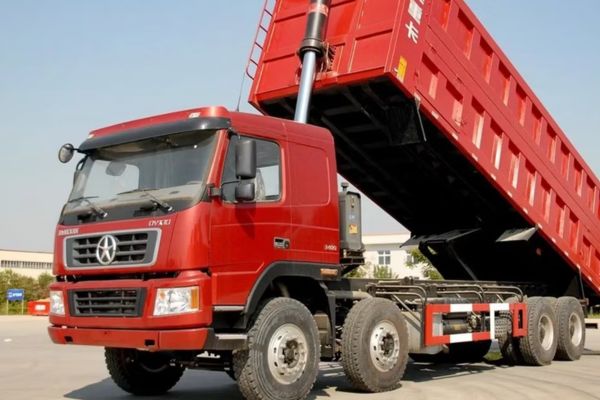
Corrosion and Contamination Protection
Practical recommendations for protecting against environmental factors:
- External Corrosion Protection:
- Apply appropriate paint systems to external surfaces (minimum two-coat system)
- Implement regular inspection for paint damage or corrosion
- Apply corrosion-inhibiting compounds to exposed areas during maintenance
- Internal Corrosion Prevention:
- Maintain proper fluid condition through regular analysis and replacement
- Implement water-removing filters in systems operating in humid environments
- Consider internal surface treatments for cylinders in corrosive applications
- Contamination Control Strategies:
- Install filtration meeting or exceeding ISO 4406 cleanliness standards
- Implement rod boots or bellows for extremely dirty environments
- Establish clean maintenance protocols including proper port plugging during service
- Material Compatibility Considerations:
- Verify compatibility between seal materials and hydraulic fluids
- Consider galvanic corrosion potential in mounting hardware selection
- Implement appropriate isolation when dissimilar metals must be used
Performance Optimization Techniques
Hydraulic System Integration
Recommendations for optimizing the entire hydraulic system:
- Pressure Management:
- Set system pressure no higher than required for the application (typically 500-3000 psi)
- Implement properly sized relief valves to prevent pressure spikes
- Consider accumulators to absorb shock and reduce pump cycling
- Flow Control Optimization:
- Size flow controls based on desired cylinder speeds
- Implement meter-out flow control for suspended loads
- Consider proportional valves for applications requiring precise control
- Thermal Management:
- Monitor system temperature during operation (optimal range typically 100-140°F)
- Implement appropriate cooling for continuous duty applications
- Size reservoirs appropriately (minimum 2-3 times pump flow per minute)
- Circuit Design Considerations:
- Implement regenerative circuits for applications requiring rapid extension
- Use counterbalance valves for load-holding applications
- Consider synchronized circuits for multiple-cylinder applications
Advanced Control Systems
Practical control system recommendations:
- Electronic Control Integration:
- Implement pressure sensors to monitor system performance
- Consider position feedback for critical positioning applications
- Establish alarm parameters for abnormal operating conditions
- Position Sensing Technologies:
- Select appropriate position sensing based on accuracy requirements
- Protect external sensors from physical damage
- Implement redundant sensing for safety-critical applications
- Pressure and Temperature Monitoring:
- Install pressure gauges at key points in the system
- Implement temperature monitoring for continuous duty applications
- Consider data logging for troubleshooting intermittent issues
- Automated Maintenance Systems:
- Implement automatic lubrication where appropriate
- Consider centralized fluid monitoring systems
- Establish maintenance alerts based on operating hours or conditions
Maintenance Strategies for Optimized Lifespan
Preventive Maintenance Protocols
Practical maintenance recommendations:
- Inspection Schedules:
- Implement daily visual inspections for leaks or damage
- Conduct monthly performance checks measuring drift and cycle times
- Perform quarterly comprehensive inspections including mounting and alignment
- Fluid Management:
- Analyze fluid samples every 500 operating hours or quarterly
- Replace filters according to manufacturer recommendations or pressure indicators
- Maintain proper fluid levels and change intervals based on operating conditions
- Seal Maintenance:
- Replace seals proactively based on operating hours (typically 2000-4000 hours)
- Maintain inventory of correct seal kits for each cylinder type
- Train maintenance personnel in proper seal installation techniques
- Alignment Verification:
- Check mounting hardware torque quarterly
- Verify cylinder alignment during installation and after repairs
- Monitor for signs of side-loading such as uneven rod wear or binding
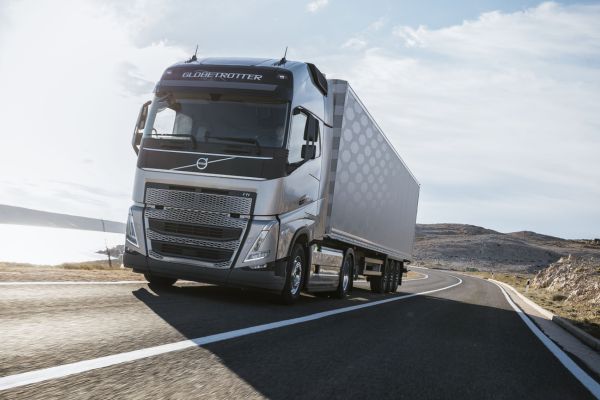
Rebuilding and Reconditioning Considerations
Practical rebuilding recommendations:
- Rebuild Timing Optimization:
- Establish rebuild criteria based on performance metrics rather than failure
- Consider scheduled rebuilds during planned downtime periods
- Maintain proper documentation of rebuild history and component replacement
- Reconditioning Techniques:
- Hone cylinder barrels to restore proper surface finish
- Replace rods showing signs of wear, scoring, or bending
- Verify all dimensions and tolerances during reassembly
- Upgrade Opportunities During Rebuilds:
- Consider implementing improved seal designs during rebuilds
- Upgrade to better surface treatments when available
- Implement design improvements addressing any recurring issues
- Quality Assurance Processes:
- Pressure test all rebuilt cylinders before installation
- Verify proper operation through full stroke under controlled conditions
- Document all rebuild procedures and component replacements
Conclusion
Optimizing hydraulic cylinder systems in heavy-duty trucks requires a balanced approach focusing on both performance and longevity. By implementing the practical recommendations outlined in this article—from material selection and geometric design to seal system optimization and maintenance protocols—fleet managers and maintenance professionals can significantly improve reliability while reducing total operating costs. Remember that optimization is an ongoing process requiring regular assessment and adjustment based on operating conditions and performance requirements.
If you need a more specialized custom hydraulic cylinder, contact Topa and we can customize the most appropriate product for your needs!
FAQ
What is the role of hydraulic cylinders in heavy-duty trucks?
Hydraulic cylinders are used in heavy-duty trucks for various functions, such as lifting, tilting, and controlling truck beds, cranes, and other components.
How do hydraulic cylinders affect the performance of a heavy-duty truck?
Hydraulic cylinders enable smooth and efficient movement of heavy components, ensuring that trucks can handle heavy loads with precision and power.
What factors should be considered when optimizing hydraulic cylinders in heavy-duty trucks?
Key factors include the truck’s weight capacity, the environment it operates in, the hydraulic fluid used, and the required speed and force of the hydraulic movements.
How can I extend the lifespan of hydraulic cylinders in trucks?
Regular maintenance, proper fluid levels, using high-quality seals, and ensuring correct installation and alignment can all help extend the lifespan of hydraulic cylinders.
What are the common signs that a hydraulic cylinder in a truck needs maintenance?
Common signs include oil leaks, erratic movement, increased noise during operation, or decreased lifting capacity.
How do operating conditions affect the performance of hydraulic cylinders in trucks?
Extreme temperatures, excessive pressure, and exposure to contaminants can impact the performance of hydraulic cylinders, causing wear and tear or even failure.