Hydraulic oil is a specially formulated fluid used in hydraulic systems to transmit power. These systems rely on pressurized fluid to move parts or machinery, and hydraulic oil serves as the medium for transferring that power.
The Hydraulic Oil Basics: How It Works
Hydraulic systems are powerful and efficient tools used in a wide range of industries, from construction to manufacturing. At the heart of these systems lies hydraulic oil, a special fluid that transmits force and energy to perform various tasks. In this section, we’ll delve deeper into the science behind how hydraulic fluid works, the role of fluid dynamics, and why oil pressure and lubrication are critical to system efficiency.
Fluid Dynamics: How Hydraulic Oil Powers Machinery
Fluid dynamics is the study of how fluids—like hydraulic oil—move and interact with their environment. In a hydraulic system, fluid dynamics governs how the oil moves through pipes, pumps, valves, and actuators to transmit power.
Hydraulic systems operate by creating pressure in a confined space. When hydraulic oil is pumped into the system, it is forced through tubes and valves, moving at a high speed and creating pressure. The pressure generated in the oil allows the hydraulic system to perform various functions such as lifting, rotating, or pushing machinery components.
The key to understanding how hydraulic oil powers machinery lies in the Pascal’s Law, which states that when pressure is applied to a confined fluid, the pressure is transmitted equally in all directions. This principle allows hydraulic systems to generate significant force from a small amount of fluid. As the hydraulic oil moves through the system, it transmits this pressure to hydraulic cylinders, pistons, and other actuators, making heavy machinery capable of performing tasks that would otherwise require much more effort or power.
For example, when you press a button to raise a crane’s arm or push a lever to lift a load, the hydraulic oil’s ability to transmit pressure effectively powers the machinery. Hydraulic fluid is ideal for this because it can carry force over long distances without losing energy, even under high pressure.
Understanding Oil Pressure and its Role in System Efficiency
Oil pressure is at the core of how hydraulic systems function. It is the force exerted by the hydraulic oil on the system’s components, such as pistons, valves, and cylinders. The pressure created in the hydraulic system allows oil to flow through the system, generating the power necessary to perform a variety of tasks.
The pressure within a hydraulic system must be carefully regulated for the system to function efficiently. Too much pressure can lead to system failure or damage to components, while too little pressure can cause sluggish performance, insufficient power output, or even the inability to complete tasks.
Several factors determine the pressure within a hydraulic system:
Pump Output: The hydraulic pump generates the pressure needed to move the oil through the system. The pump’s capacity, combined with the system’s resistance, determines the maximum pressure that can be achieved.
System Design: The layout of the hydraulic system, including the size of pipes, valves, and actuators, plays a role in the pressure buildup. Narrow pipes or restrictive valves can create resistance that affects pressure, while larger components or more efficient designs can help maintain steady pressure levels.
Oil Viscosity: The viscosity of the hydraulic oil (how thick or thin it is) plays a key role in maintaining oil pressure. Oils with a higher viscosity create more resistance to flow, which can affect pressure. However, oils that are too thin may not create enough resistance, leading to insufficient pressure.
Temperature: Temperature fluctuations affect hydraulic oil viscosity. At higher temperatures, oil tends to become less viscous (thinner), which may reduce the pressure in the system. In colder temperatures, oil thickens and creates more resistance to flow, potentially increasing pressure. Maintaining the correct oil temperature is crucial for optimal performance.
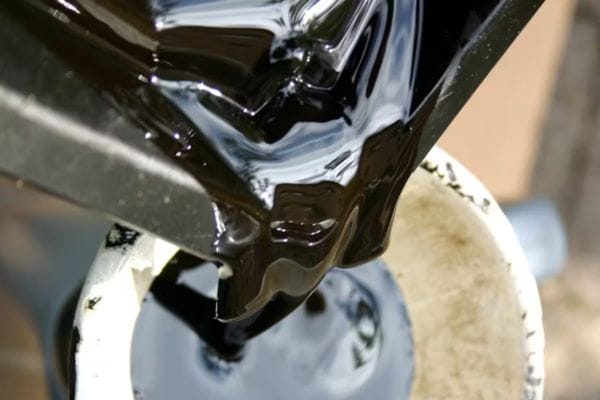
Pressure Lubrication: Keeping Your Equipment Running Smoothly
Pressure lubrication refers to the use of hydraulic oil to lubricate moving components within a hydraulic system under pressure. The primary function of lubrication in any machine is to reduce friction between moving parts, preventing wear and tear, and ensuring smooth operation. Hydraulic oil’s role in pressure lubrication is particularly critical because it not only lubricates but also carries the pressure needed to perform heavy-duty tasks.
When hydraulic oil flows through the system, it not only powers the machinery but also coats the moving parts, such as pistons, cylinders, and gears. This creates a thin film of oil between the surfaces of these parts, reducing friction and minimizing metal-on-metal contact.
Here’s why pressure lubrication is essential for system longevity and efficiency:
Reduces Wear and Tear: Constant movement and pressure can wear down metal parts in hydraulic systems. The oil film created by hydraulic fluid prevents direct contact between these parts, which significantly reduces friction and wear. This means components last longer and require fewer repairs.
Prevents Overheating: Lubrication helps dissipate heat generated by friction. As hydraulic oil flows through the system, it absorbs heat from moving components and carries it away, helping to prevent overheating. Overheating is a major cause of hydraulic oil degradation and system failure.
Maintains System Efficiency: By reducing friction and preventing damage, pressure lubrication ensures that the system runs at peak efficiency. Less friction means less energy is lost in the form of heat, and the system can perform tasks more quickly and with less power. This not only saves energy but also ensures that machinery operates smoothly without unnecessary stress on its components.
Contaminant Control: Hydraulic oil also helps to carry away contaminants like dirt, metal particles, and debris that may enter the system. By trapping these particles in the oil and filtering them out, the oil prevents contaminants from damaging sensitive components and maintains system integrity.
Different Types of Hydraulic Oil: Which One Do You Need?
Hydraulic oil is not a one-size-fits-all product. Depending on the nature of your hydraulic system, the operating environment, and your specific requirements, different types of hydraulic oils will be more suitable for your machinery.
Mineral Oil vs. Synthetic Hydraulic Oil: What’s the Difference?
When it comes to choosing hydraulic oil, one of the most fundamental decisions is whether to go with mineral oil or synthetic hydraulic oil. Each has its own set of advantages and applications, and understanding the differences between them is key to selecting the right oil for your system.
Mineral Oil Hydraulic Oil
Mineral oil is derived from crude oil through a refining process. It has been the standard choice for hydraulic systems for many years, and it is often favored due to its availability and cost-effectiveness. Mineral oils are typically used in less demanding hydraulic applications, such as standard construction equipment, low-pressure systems, and machinery that doesn’t operate in extreme temperatures.
Advantages of Mineral Oil:
Cost-effective and widely available.
Provides good lubrication for most common systems.
Available in a wide range of viscosities for different operational needs.
Suitable for systems operating in moderate temperature ranges.
Disadvantages of Mineral Oil:
Lower thermal and oxidative stability compared to synthetic oils.
More prone to contamination and degradation over time.
Not as effective in extreme temperatures or high-pressure systems.
Synthetic Hydraulic Oil
Synthetic hydraulic oils, on the other hand, are engineered fluids made from specially synthesized chemical compounds. They are designed to offer superior performance, especially in high-performance systems or extreme conditions. These oils are more resistant to temperature variations, oxidation, and contamination, making them ideal for high-pressure, high-temperature environments such as aerospace, military, and heavy industrial applications.
Advantages of Synthetic Oil:
Better thermal stability and resistance to oxidation.
Performs well in extreme temperatures (both high and low).
Longer service life due to reduced degradation.
Superior anti-wear properties and less evaporation loss.
Improved fluid efficiency and reduced friction.
Disadvantages of Synthetic Oil:
Higher initial cost compared to mineral oils.
May not be necessary for lower-pressure, less-demanding systems.
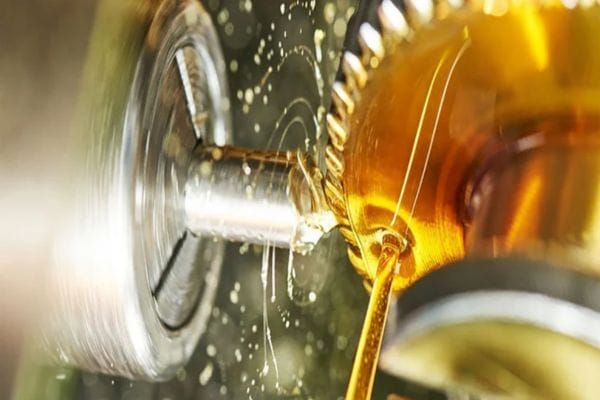
Understanding Biodegradable Hydraulic Oil and Its Environmental Benefits
As environmental concerns continue to grow, there has been an increasing demand for biodegradable hydraulic oils. These oils are designed to break down naturally when exposed to the environment, minimizing their impact on ecosystems if spillage occurs. Biodegradable oils are made from renewable resources like vegetable oils or esters, and they are often used in environmentally sensitive areas, such as forestry, agriculture, and offshore operations.
Key Benefits of Biodegradable Hydraulic Oils:
Environmentally Friendly: They break down much faster than traditional mineral oils, reducing the risk of long-term contamination of soil, water, and wildlife.
Renewable and Sustainable: Many biodegradable oils are made from renewable sources like plant-based oils, making them more sustainable compared to mineral oils.
Reduced Toxicity: In case of leakage or spill, biodegradable oils are less toxic to aquatic life and wildlife, minimizing the environmental damage.
Common Applications for Biodegradable Hydraulic Oils:
Forestry equipment, where oils are often exposed to the environment.
Marine vessels and offshore platforms where oil spills can be devastating to marine ecosystems.
Agricultural machinery operating in sensitive areas, like near water bodies.
Drawbacks of Biodegradable Hydraulic Oils:
Higher Cost: Biodegradable oils tend to be more expensive due to the sourcing of raw materials and the manufacturing process.
Shorter Shelf Life: They may have a shorter shelf life compared to mineral oils and require more frequent changes.
Overview of Common Hydraulic Oil Types: AW, HM, HLP
Hydraulic oils come in a variety of formulations, each designed to meet specific needs depending on the operating environment and the machinery involved. Below are some of the most common types of hydraulic oil you’ll encounter.
AW (Anti-Wear) Hydraulic Oil AW oils are specifically formulated with additives that protect hydraulic components from wear. These oils are used in systems where wear prevention is crucial, especially in pumps, motors, and other moving parts. AW oils help extend the lifespan of hydraulic components by providing extra protection against friction and wear.
Key Features of AW Oils:
Excellent anti-wear properties to protect against mechanical wear.
Commonly used in general industrial applications, such as manufacturing machinery and construction equipment.
Protects against corrosion and rust, extending component life.
Best For: Mid-range hydraulic applications with moderate pressure and standard operating conditions.
HM (Hydraulic Mineral) Oil HM oils are mineral-based oils that offer good anti-wear properties and are commonly used in general-purpose hydraulic systems. These oils are suitable for medium to high-pressure systems where wear prevention and high lubrication are important. HM oils are also formulated to resist oxidation and contamination, extending their service life.
Key Features of HM Oils:
Good anti-wear additives to protect system components.
Suitable for moderate to high-pressure systems.
Resists oxidation and degradation for longer operational life.
Available in a variety of viscosities to suit different system needs.
Best For: Hydraulic systems with moderate to high pressure, like manufacturing equipment, cranes, and hydraulic presses.
HLP (High-Pressure Lubricant) Oil HLP oils are formulated for high-pressure systems where extreme conditions demand superior protection. These oils are designed to withstand the high shear forces generated in high-pressure hydraulic systems. HLP oils provide excellent lubrication, reduce wear, and enhance the overall performance of pumps and motors under stress.
Key Features of HLP Oils:
Specifically formulated for high-pressure applications.
Excellent oxidative stability to withstand high temperatures.
Ideal for systems with high load and pressure conditions, such as injection molding machines or heavy-duty industrial presses.
Includes additives to improve rust protection, anti-foam properties, and wear resistance.
Best For: High-pressure, high-load systems that need robust performance, like construction machinery, mining equipment, and oil rigs.
Choosing the Right Hydraulic Oil for Your System
Selecting the correct hydraulic oil is essential to ensuring the optimal performance and longevity of your hydraulic system. Choosing the wrong oil can lead to poor system performance, excessive wear, overheating, and increased maintenance costs. In this section, we will cover the key factors you need to consider when choosing hydraulic oil, the role of viscosity, and how to match hydraulic oil to your hydraulic pump and machinery for peak efficiency.
Hydraulic Oil Selection
When selecting hydraulic oil, it’s important to take into account the specific requirements of your hydraulic system. Different systems have different needs based on factors like pressure, temperature, load, and speed. Here are the most important factors to consider when choosing hydraulic oil:
Operating Pressure and Load The operating pressure of your hydraulic system determines the level of stress the oil will be under. Systems operating at high pressure require oils with higher viscosity and anti-wear additives to protect the system components. If your system operates at lower pressure, you can often use oils with lower viscosity for improved flow and efficiency.
Operating Temperature The temperature at which your hydraulic system operates plays a significant role in determining which oil is best suited for your needs. Hydraulic oils must maintain their viscosity under varying temperature conditions. High temperatures can cause the oil to thin out, which may reduce lubrication effectiveness, while low temperatures can make oil too thick, increasing system resistance. Be sure to choose an oil with a viscosity that suits the operating temperature range.
System Speed If your system involves high-speed components such as motors or pumps, you’ll need oil that is designed to handle the increased shear forces. High-speed systems benefit from oils that maintain a stable viscosity and perform well under heat stress. Lower-speed systems, on the other hand, may do well with oils that are thinner or have better flow characteristics.
Environmental Conditions Consider whether your hydraulic system is operating in harsh or environmentally sensitive conditions. If you’re using hydraulic equipment in an area where oil leaks can have significant environmental impacts, biodegradable hydraulic oils may be the right choice. Additionally, environmental factors like humidity, dust, or exposure to chemicals can affect oil performance and may require oils with specific additives or enhanced protection.
Viscosity and Its Impact on Hydraulic System Performance
Viscosity is one of the most important factors in hydraulic oil selection because it directly impacts the performance, efficiency, and reliability of your hydraulic system. Viscosity is a measure of the oil’s thickness or resistance to flow. It determines how easily the oil can flow through the system and how well it can maintain pressure.
High Viscosity Oils with higher viscosity are thicker and flow more slowly, making them ideal for systems that operate under high pressure or high load. These oils provide better lubrication under intense conditions and can help protect components from wear and tear. However, high-viscosity oils are not ideal for systems that require high flow rates or are exposed to low temperatures.
Best for: High-pressure systems, slow-moving hydraulic machinery, and environments with high temperatures.
Low Viscosity Low-viscosity oils are thinner and flow more easily, which makes them suitable for systems with high-speed components or lower operating pressures. These oils help to reduce energy loss and improve system efficiency. However, they may not offer the same level of protection in high-pressure or heavy-load applications.
Best for: Low-pressure systems, high-speed machinery, and environments with cold temperatures.
Viscosity Index (VI) The viscosity index is a measure of how the viscosity of an oil changes with temperature. Hydraulic oils with a high VI remain relatively stable in viscosity over a wide range of temperatures, ensuring consistent performance under varying operating conditions. Oils with a low VI, on the other hand, may become too thick in cold conditions or too thin at high temperatures.
Choosing the Right Viscosity: Always refer to the manufacturer’s recommendations for the specific viscosity grade required for your hydraulic system. The most common viscosity grades are ISO VG 32, ISO VG 46, and ISO VG 68, but the best choice depends on factors like temperature range, system load, and operating speed.
Shear Stability Some hydraulic oils, particularly those with synthetic components, are designed for better shear stability. Shear stability refers to the oil’s ability to retain its viscosity under high mechanical stress and high-speed operation. Choosing a shear-stable oil ensures that the oil’s viscosity doesn’t break down, maintaining effective lubrication over time.
How to Match Hydraulic Oil to Your Hydraulic Pump and Machinery
The choice of hydraulic oil should also be aligned with the specific components of your hydraulic system, including your hydraulic pump, motors, valves, and cylinders. Here’s how to match hydraulic oil to your equipment:
Hydraulic Pumps
The hydraulic pump is responsible for pressurizing the oil and driving the system, so it requires oil that has both sufficient viscosity and lubricating properties to protect its internal components. Pumps generally work better with oils that have anti-wear additives, especially in high-pressure applications where friction and heat can cause significant wear. Be sure to use oil with the correct viscosity to avoid cavitation (air bubbles in the oil) and to maintain optimal pump performance.
Hydraulic Motors
Hydraulic motors rely on the oil to transmit torque and rotational energy. They require an oil that can handle high speeds, pressure, and mechanical forces. Oils with high shear stability and good lubricating properties are crucial here to prevent premature wear.
Hydraulic Cylinders
Hydraulic cylinders rely on the oil to exert force and produce movement. Cylinders typically experience both high pressure and significant wear due to the constant movement of their internal seals and rods. Oils with high anti-wear protection and appropriate viscosity are essential to ensure smooth, long-lasting operation.
Valves and Filters
Hydraulic valves control the flow of oil within the system, while filters help keep contaminants out. Both require oils that are clean and free from excessive contaminants. It’s essential to use oil that doesn’t degrade quickly or generate harmful particles that could clog valves or filters.
Hydraulic Oil Contamination: Prevention and Management
Hydraulic oil contamination is one of the leading causes of hydraulic system failure. Contaminants like dirt, water, and metal particles can cause increased wear, system inefficiency, and even catastrophic breakdowns if not properly managed. Understanding how contamination affects performance and adopting strategies to prevent and manage contamination is essential for the longevity and reliability of hydraulic systems.
What is Fluid Contamination and How Does It Affect Performance?
Fluid contamination refers to the presence of unwanted particles, liquids, or gases in hydraulic oil that can degrade its quality and performance. These contaminants typically enter the hydraulic system through leaks, maintenance procedures, or environmental factors, and they can significantly impact the efficiency and longevity of the system.
The most common types of contaminants found in hydraulic oil include:
Solid Particles: Dirt, dust, metal shavings, rust, and wear debris from system components.
Water: Water can enter the system through condensation or leaks, often causing emulsification of the oil.
Air: Entrained air can lead to cavitation (formation of bubbles) in pumps, causing damage and reduced performance.
Gases: Nitrogen or other gases can dissolve in the oil and affect its lubricating ability.
Contamination can cause several issues, including:
Increased Wear: Solid particles and metal shavings can scratch and wear down critical components like pumps, valves, and cylinders, leading to premature failure.
Reduced Lubrication: Water and air contamination can degrade the oil’s lubricating properties, leading to friction, overheating, and more wear on system parts.
Blockages and Clogging: Solid particles can clog filters, valves, and small passages in the system, impairing fluid flow and reducing system efficiency.
Corrosion: Water contamination can cause rusting and corrosion of metal parts, leading to the degradation of seals, pumps, and valves.
Overheating: Contaminated oil may not effectively dissipate heat, leading to overheating, which can further degrade the oil and damage components.
System Downtime: Ultimately, contamination can lead to increased downtime for repairs and maintenance, affecting production schedules and operational costs.
Signs of Hydraulic Oil Contamination and How to Spot Them
Detecting contamination early is crucial for preventing severe damage and reducing downtime. Here are some common signs that your hydraulic oil may be contaminated and how to spot them:
Sudden Drop in System Pressure
What It Means: If your system suddenly starts showing a drop in pressure or is underperforming, it could be due to clogging caused by solid contaminants, or degraded oil caused by water or air contamination.
How to Spot It: Monitor your pressure gauges for inconsistencies, especially during load changes. If the pressure drops unexpectedly, contamination might be causing flow restriction or damage to system components.
Excessive Heat or Overheating
What It Means: Contaminated oil, particularly with water or air, has reduced heat transfer capabilities. As a result, your hydraulic system may overheat, potentially leading to further oil degradation and system failure.
How to Spot It: Monitor the temperature of your hydraulic oil using temperature sensors or gauges. If the oil temperature rises above the recommended operating range without a clear reason, contamination could be the culprit.
Increased Wear on Components
What It Means: Contaminants such as dirt, metal particles, and debris can cause excessive wear on key components like hydraulic pumps, valves, and cylinders. This leads to lower system efficiency and premature failure.
How to Spot It: Listen for unusual sounds such as grinding or excessive noise in the pump or motor. Also, check for signs of wear or damage on moving parts, such as scoring or rough surfaces.
Oil Discoloration or Change in Appearance
What It Means: Contaminants such as water or particles can cause noticeable changes in the appearance of hydraulic oil. Oil discoloration, cloudiness, or emulsification can signal contamination.
How to Spot It: Visually inspect the hydraulic oil. Healthy oil typically has a clear, clean appearance, but if the oil looks cloudy, milky, or darkened, it may contain water or particulate contamination.
Poor Hydraulic Response or Sluggish Operation
What It Means: If your system components are moving slower or less smoothly than usual, it could indicate that contaminants have reduced the oil’s flow properties or lubricating ability.
How to Spot It: Notice any delay or sluggishness in the response time of cylinders, valves, or motors. This can indicate internal friction, clogging, or changes in the oil’s viscosity due to contamination.
Increased Filter or Strainer Blockages
What It Means: Contaminants like dirt, wear particles, and sludge can quickly clog filters or strainers, making the system less efficient and leading to higher maintenance requirements.
How to Spot It: Keep track of your oil filter’s performance and change intervals. If you notice that filters are getting clogged much quicker than usual, it may indicate contamination in the hydraulic oil.
Best Practices for Preventing Hydraulic Oil Contamination
Preventing hydraulic oil contamination is critical to maintaining system performance and avoiding costly repairs. Here are some best practices for keeping your hydraulic oil clean and your system running smoothly:
Implement a Regular Maintenance Schedule
Conduct regular maintenance checks to monitor the condition of your hydraulic oil and system components. Schedule oil changes, filter replacements, and system inspections at regular intervals.
Use High-Quality Filters and Change Them Regularly
Filters are your first line of defense against contaminants. Use high-quality filters that are designed to trap both large and small particles.
Ensure Proper Sealing and Tight Fitting
Leaks allow contaminants such as dirt and moisture to enter the system. Check seals, fittings, and gaskets for wear or damage and replace them when necessary.
Control Moisture and Humidity
Moisture is one of the most damaging contaminants to hydraulic oil, leading to rust, corrosion, and oil emulsification. Store hydraulic oil in a dry environment, and ensure your system is sealed against water ingress.
Cleanliness During Oil Changes
During oil changes or when topping up oil, make sure the oil is kept clean and free from contaminants. Always use clean, properly stored oil to avoid introducing debris or dirt into the system.
Conclusion
By understanding the importance of proper oil selection, contamination prevention, and maintenance, you can avoid costly repairs, reduce downtime, and improve system efficiency. Keep an eye on emerging trends in hydraulic oil technology, and implement a maintenance strategy that ensures your equipment continues to run at peak performance for years to come.
FAQ
How do I know my hydraulic fluid needs to be changed?
Hydraulic fluid replacement intervals depend on a variety of factors, such as the system’s operating load, the cleanliness of the fluid, and environmental conditions. In general, if the hydraulic fluid becomes discolored, foul smelling, or shows visible contamination, it may mean that the oil has degraded and replacement should be considered.
Can I mix different types of hydraulic fluids?
Mixing different types of hydraulic fluids is not recommended, especially mineral vs. synthetic or different brands of hydraulic fluids. Mixing fluids may result in degradation of the fluid’s performance, affect lubrication, and may even cause damage to the system. When changing fluids, it is best to use the same type of oil as the original fluid and clean the system to avoid mixing.
What are some common contaminants in hydraulic fluids?
Common contaminants in hydraulic fluids include solid particles (e.g., dirt, metal shavings), moisture, air, and gas. Solid particles can increase friction and lead to component wear; moisture can cause fluid emulsification or corrosion of metal parts; and air can affect fluid flow and lead to cavitation problems.
How does hydraulic fluid viscosity affect system performance?
The viscosity of the hydraulic fluid determines its flow and lubrication. A fluid with too high a viscosity will increase system resistance and result in power loss, while a fluid with too low a viscosity may not provide adequate lubrication and increase component wear.
How can hydraulic systems prevent fluid contamination?
The key to preventing fluid contamination is to keep the system clean. First, fluid filters should be inspected and replaced regularly, and a highly efficient filtration system should be used to remove particulate contaminants. Second, ensure that the seals of the hydraulic system are intact to avoid moisture, dust, etc. from entering the system. Finally, check the quality of the fluid regularly to detect contamination problems in time and take appropriate cleaning or replacement measures.
What are the environmental options for hydraulic fluids?
As environmental regulations continue to get stricter, more and more environmentally friendly hydraulic fluids are being developed. One of the more common environmentally friendly options is biodegradable hydraulic fluids, which use renewable materials.