UNF threads are characterized by their fine pitch, making them suitable for applications requiring precise connections. In contrast, JIC fittings feature a 37-degree flare design, providing a metal-to-metal seal that enhances performance under high pressures. Both thread types have unique advantages and are selected based on specific application requirements.
What is UNF Thread?
Definition and Origin of UNF (Unified National Fine)
UNF, or Unified National Fine, refers to a standardized thread system integral to the Unified Thread Standard (UTS) established in the United States. This standard was developed to promote uniformity in fasteners, enabling compatibility across various applications and industries. The “fine” designation signifies that UNF threads have a smaller pitch than their Unified National Coarse (UNC) threads. This finer pitch allows for tighter, more secure connections, which are essential in applications where reliability and strength are paramount.
Technical Specifications
UNF threads are available in a wide range of diameters and pitches. Common diameters span from 0.25 inches to 2 inches, accommodating different sizes of fasteners and applications. The pitch of UNF threads typically varies from 32 threads per inch (TPI) to 4 TPI, providing options for various connection strengths. The precise technical specifications of UNF ensure compatibility with other UNF components, allowing for robust connections that can withstand stress and vibration. Additionally, the standardized design of UNF threads simplifies the manufacturing process, promoting easy interchangeability among different manufacturers and reducing the potential for errors.
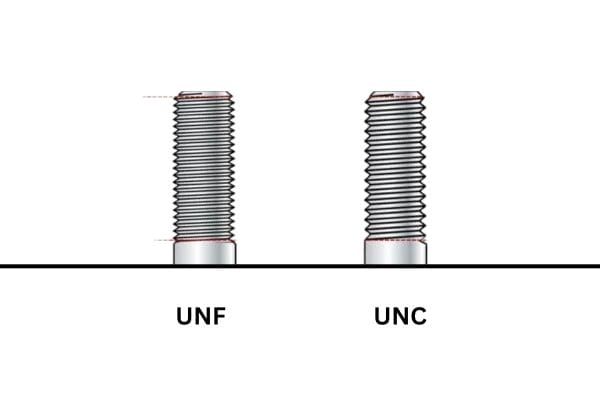
Common Applications and Industries Using UNF
UNF threads are widely utilized across several industries that demand strong and reliable fasteners. Key sectors include automotive, aerospace, machinery, and hydraulic systems. In the automotive industry, UNF threads are often used for connecting components in engines and transmission systems, where precise fittings are crucial. In aerospace, these threads provide secure connections in high-stress environments, ensuring safety and reliability. Hydraulic systems frequently use UNF threads for connecting hydraulic cylinders and hoses, making them vital in machinery that requires fluid power for operation. The versatility and strength of UNF threads make them a preferred choice in applications where precision and durability are essential.
Advantages of Using UNF Threads
The advantages of UNF threads are numerous, contributing to their widespread adoption in various industries. One of the primary benefits is their ability to provide strong connections with a reduced risk of stripping, thanks to the finer pitch of the threads. This characteristic is particularly important in high-stress applications where a secure connection is critical. Furthermore, UNF threads facilitate easier assembly and disassembly, making maintenance processes more efficient and less time-consuming. This ease of use can lead to lower labor costs and minimized downtime in production settings.
Another significant advantage is the standardization of UNF threads, which ensures compatibility across a broad range of products. This standardization simplifies inventory management for manufacturers, as they can rely on a consistent system of fittings and fasteners. By reducing confusion regarding thread types and specifications, UNF threads enhance operational efficiency and contribute to the overall reliability of hydraulic and mechanical systems. Overall, the unique characteristics and benefits of UNF threads make them an essential component in modern engineering and manufacturing practices.
What is JIC Fitting?
Definition and Standards (SAE J514/ISO 8434-2)
JIC, or Joint Industry Council, fittings represent a specialized category of hydraulic fittings that adhere to the SAE J514 standard, which is internationally recognized as ISO 8434-2. This standard ensures that JIC fittings maintain a high level of consistency and reliability in their design and manufacturing processes. Specifically engineered for high-pressure applications, JIC fittings incorporate a unique metal-to-metal sealing mechanism. This design not only enhances the performance of the fittings but also significantly minimizes the risk of leaks, making them a preferred choice in demanding environments.
Technical Specifications
JIC fittings are distinctly characterized by their 37-degree flare design, which provides a precise sealing surface. This feature is essential for ensuring a tight connection that can withstand high pressure. Additionally, JIC fittings utilize straight threads—specifically UNF threads—that complement the 37-degree flare design. Common sizes for JIC fittings typically range from 1/8 inch to 2 inches, and thread sizes are defined by both diameter and threads per inch (TPI). This robust design allows JIC fittings to handle pressures of up to 10,000 psi in various applications, making them suitable for the most demanding hydraulic systems.
Typical Applications and Industries Using JIC
JIC fittings find extensive use in several industries that require durable and robust hydraulic connections. Key sectors include aerospace, automotive, construction, and manufacturing. In aerospace, JIC fittings are employed in hydraulic systems where reliability is critical due to the high-stress environments involved. The automotive industry frequently utilizes JIC fittings in fuel delivery systems and hydraulic machinery. In construction and manufacturing, these fittings are essential for connecting hydraulic hoses to pumps and cylinders, providing fluid power to equipment that demands consistent performance under high pressure. The versatility of JIC fittings makes them a vital component in mobile machinery and equipment, where dependable connections are crucial.
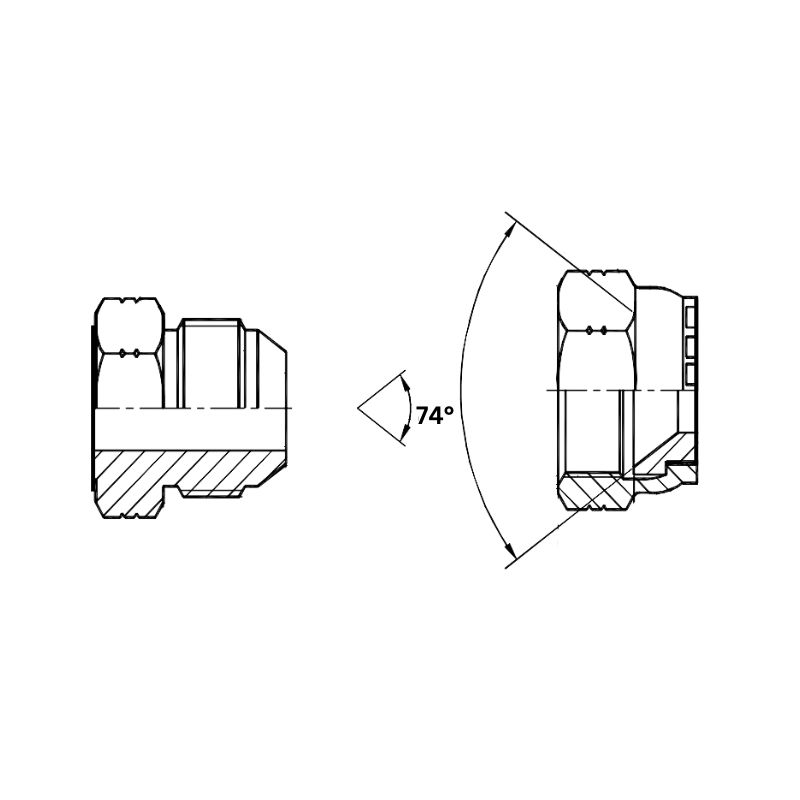
Advantages of JIC Fittings
The primary advantages of JIC fittings lie in their exceptional pressure-handling capabilities and the secure, leak-free connections they provide. The metal-to-metal sealing mechanism minimizes the risk of leaks, even in extreme pressure conditions, ensuring the integrity of hydraulic systems. JIC fittings are also notably versatile and compatible with a wide array of hydraulic components, which allows for easy integration into existing systems. Their design facilitates straightforward assembly and disassembly, simplifying maintenance and repair processes.
Moreover, the standardized nature of JIC fittings streamlines inventory management, reducing the likelihood of compatibility issues across different manufacturers. The ability to withstand harsh environmental conditions, coupled with resistance to wear and tear, further enhances the reliability and longevity of JIC fittings, making them a favored choice in various applications where performance and durability are paramount.
Key Differences Between UNF and JIC
Thread Design and Sealing Surfaces
The primary difference between UNF and JIC fittings lies in their thread design and sealing mechanisms. UNF threads feature a fine pitch that provides a secure fit, making them ideal for applications where precision is essential. The sealing approach of UNF is straightforward, relying primarily on the engagement of the threads to maintain tightness. This simplicity can be advantageous in environments where precision is critical but may not provide the robust sealing required in high-pressure scenarios.
In contrast, JIC fittings incorporate a unique 37-degree flare design, which creates a metal-to-metal sealing surface. This configuration significantly enhances leak prevention by ensuring that the flared surfaces make direct contact under pressure, providing a secure and reliable connection. The combination of UNF threads and the flared design results in a highly effective sealing system that can accommodate high-pressure applications with ease. This fundamental difference makes JIC fittings particularly suitable for fluid power systems subjected to significant pressure, where a reliable seal is paramount.
Pressure Ratings and Performance
When it comes to pressure ratings, JIC fittings generally outperform UNF threads due to their robust construction. JIC fittings can withstand pressures of up to 10,000 psi, making them ideal for high-pressure hydraulic systems commonly found in industries such as aerospace, manufacturing, and heavy machinery. This high-pressure capability is critical, as it reduces the risk of failures that could have serious safety implications in these demanding environments.
Conversely, UNF threads are suitable for applications where the pressure demands are more moderate. They typically handle pressures ranging from a few hundred to several thousand psi, depending on the specific configuration and materials used. While UNF threads are reliable for many applications, their lower pressure ratings mean they are not always appropriate for high-stress situations. The differences in pressure handling capabilities are a crucial consideration when selecting fittings for specific applications, particularly in scenarios that involve elevated pressures.
Compatibility and Standardization
Another significant difference between UNF and JIC fittings lies in their compatibility and standardization. UNF threads are part of the Unified Thread Standard (UTS), which promotes interchangeability among different manufacturers and components. This standardization simplifies the selection process for engineers and technicians, ensuring that UNF fittings can be easily sourced and integrated into existing systems without compatibility concerns. This is particularly beneficial for manufacturers and repair services, as it reduces inventory complexity and enhances the availability of parts.
On the other hand, JIC fittings also adhere to standardized dimensions and specifications but are specifically designed for high-pressure applications. While they share some compatibility with UNF threads, mixing and matching can lead to issues if not done carefully. It’s crucial to ensure that the correct fitting type is used in conjunction with compatible components to avoid leaks and system failures. The distinct standards for UNF and JIC emphasize the importance of proper selection in maintaining the integrity and safety of hydraulic systems.
Maintenance and Installation Considerations
Maintenance and installation practices can also differ significantly between UNF and JIC fittings. UNF fittings, with their simple thread engagement design, may be easier to install in certain applications. However, they require careful attention to torque specifications to prevent stripping or damaging the threads during assembly.
In contrast, JIC fittings, due to their metal-to-metal sealing mechanism, require precise installation to ensure proper contact between the flared surfaces. This might necessitate more thorough alignment during installation, but once secured, JIC fittings often require less frequent maintenance due to their reliable sealing capabilities. Regular inspections are still important, but the inherent design of JIC fittings minimizes the risk of leaks, making them a favored choice for high-stress applications.
Choosing the Right Fitting
Factors to Consider When Selecting Between UNF vs JIC
When determining whether to use UNF or JIC fittings, several key factors should be evaluated:
Application Requirements: The specific demands of your application are paramount. For high-pressure hydraulic systems, JIC fittings are generally preferred due to their superior pressure ratings and metal-to-metal sealing design. These features make them ideal for critical applications where reliability is essential. Conversely, if the application involves moderate pressure and less critical sealing requirements, UNF threads may suffice, offering a reliable connection without the need for the enhanced capabilities of JIC fittings.
Environmental Conditions: Consider the operating environment of the fittings. If they are exposed to harsh conditions—such as extreme temperatures, corrosive chemicals, or significant vibrations—JIC fittings might provide better durability and reliability. Their design often allows for enhanced performance in challenging environments, reducing the risk of failure and ensuring longevity.
Compatibility: Assess the existing systems and components with which you will be working. UNF fittings are standardized, promoting easier integration with other UNF components and simplifying sourcing. However, if your system already utilizes JIC fittings, it’s prudent to stick with them to minimize compatibility issues and streamline maintenance processes.
Maintenance Needs: The ease of maintenance is another crucial factor to consider. JIC fittings are generally easier to assemble and disassemble, facilitating quicker maintenance and repairs. If frequent maintenance is anticipated, the design of JIC fittings can significantly influence your choice, as they allow for reduced downtime.
Cost Considerations: While both types of fittings are widely available, pricing may vary based on the specific application and required components. It’s important to factor in both the initial costs and potential long-term savings from reduced maintenance or failure rates. Sometimes, investing in higher-quality JIC fittings may lead to greater savings in the long run due to their durability and reliability.
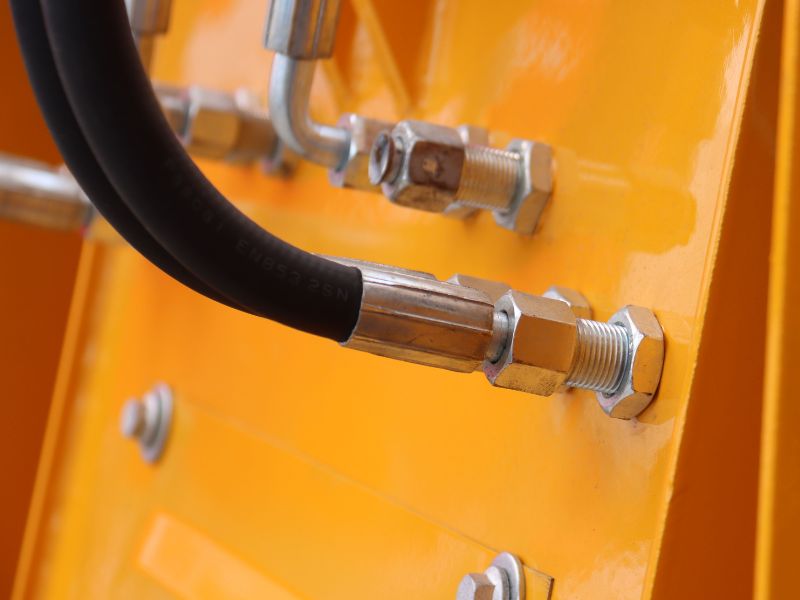
Common Misconceptions About Thread Types
There are several misconceptions surrounding UNF and JIC fittings that can lead to confusion:
All Thread Types Are Interchangeable: A common misconception is that all hydraulic fittings can be easily interchanged. However, due to the differences in thread design, sealing surfaces, and pressure capabilities, mixing UNF and JIC fittings can lead to leaks and system failures. Understanding the distinctions is vital for ensuring the integrity of hydraulic systems.
JIC Fittings Are Always Superior: While JIC fittings offer high-pressure capabilities and are excellent for critical applications, they are not necessarily the best choice for every situation. UNF fittings can be more suitable for low-pressure applications or environments where the risk of pressure-induced failure is minimal. Choosing the right fitting requires a comprehensive understanding of the specific application rather than a blanket assumption about superiority.
Fittings Do Not Require Regular Inspection: Another misconception is that once installed, fittings do not require regular maintenance or inspection. In reality, all hydraulic fittings, whether UNF or JIC, should be regularly inspected for signs of wear, damage, or leaks. This proactive approach helps ensure the safety and efficiency of hydraulic systems.
Expert Recommendations and Tips for Best Practices
To make informed decisions when selecting fittings, consider the following expert recommendations:
Consult with Experts: Engaging with hydraulic system specialists or engineers can provide valuable insights into which fitting type best meets your needs. Their experience can help navigate complex applications and ensure optimal choices.
Follow Manufacturer Guidelines: Always adhere to the specifications and recommendations provided by manufacturers. These guidelines can offer crucial information about pressure ratings, compatibility, and installation best practices.
Regular Training and Updates: Ensure that personnel responsible for installation and maintenance are regularly trained on the latest technologies and best practices related to hydraulic fittings. This knowledge can improve safety and efficiency.
Conduct Periodic Inspections: Implement a routine inspection schedule for all hydraulic fittings to identify potential issues before they escalate. Regular maintenance can prevent leaks and prolong the life of the system.
Conclusion
Selecting the appropriate fitting not only enhances system efficiency but also minimizes the risk of failures, which can lead to costly downtime and safety hazards. For those looking to deepen their understanding or needing assistance in selecting the right fittings for their specific needs, we encourage you to reach out for further inquiries or consultations.
FAQ
What is the main difference between UNF and JIC fittings?
UNF fittings have a fine thread design, while JIC fittings feature a 37-degree flare for metal-to-metal sealing, making JIC better for high-pressure applications.
Can I use UNF fittings in high-pressure systems?
UNF fittings are suitable for moderate pressure applications but may not handle the high pressures that JIC fittings can withstand.
Are UNF and JIC fittings interchangeable?
No, they are not interchangeable due to differences in thread design and sealing mechanisms, which can lead to compatibility issues.
What industries commonly use JIC fittings?
JIC fittings are widely used in aerospace, automotive, construction, and manufacturing industries where reliable high-pressure connections are needed.
How do I choose between UNF and JIC fittings?
Consider factors like application requirements, environmental conditions, compatibility with existing systems, maintenance needs, and cost.
What maintenance is required for these fittings?
Regular inspection for wear, ensuring proper torque during installation, and checking for leaks are essential for both UNF and JIC fittings.