Properly fabricated hoses are essential for maintaining the integrity of fluid transfer, ensuring optimal performance, and minimizing downtime. When done right, they enhance system reliability and extend the lifespan of components, ultimately saving time and costs. Conversely, improper fabrication or installation can lead to significant issues, including leaks, system failures, and even safety hazards.
Understanding Hose Fabrication
A. Definition and Importance of Hose Fabrication
Hose fabrication is the process of creating hoses tailored for specific applications, ensuring they meet the demands of various industries. This involves selecting the appropriate materials, designing the hose structure, and assembling it with fittings and connectors. The importance of proper hose fabrication cannot be overstated; it directly influences the performance and safety of hydraulic and pneumatic systems. A well-fabricated hose minimizes the risk of leaks, enhances efficiency, and prolongs the life of the equipment, which is vital for maintaining operational integrity.
B. Types of Hoses and Their Applications
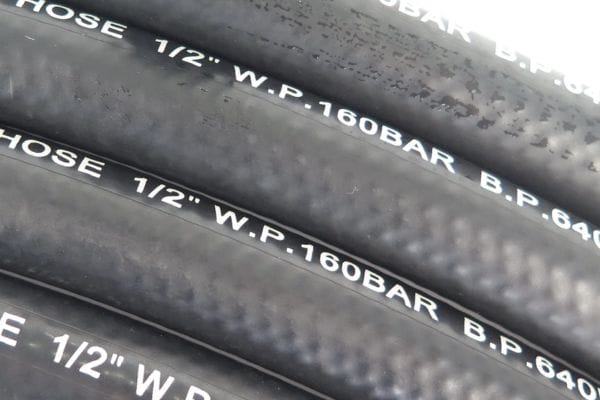
Hydraulic Hoses
Hydraulic hoses are designed to carry high-pressure fluids in hydraulic systems. These hoses are typically used in machinery, construction equipment, and automotive applications. Their ability to withstand extreme pressure and temperature makes them essential for effective fluid power transmission.
Industrial Hoses
Industrial hoses serve a broad range of applications, from transferring water and chemicals to conveying air and gas. Commonly found in manufacturing plants, construction sites, and agricultural settings, these hoses are versatile and can be customized to meet specific needs. Industrial hoses may vary in diameter, length, and material composition, depending on their intended use.
Specialty Hoses
Specialty hoses are designed for unique applications that require specific properties, such as resistance to chemicals, abrasion, or extreme temperatures. These hoses can include food-grade hoses for the food and beverage industry, fire hoses for firefighting, and hoses used in medical applications. Their specialized design ensures they perform optimally in challenging environments.
C. Materials Used in Hose Fabrication
Rubber vs Thermoplastic
Rubber hoses are known for their flexibility, durability, and resistance to environmental factors. They are often used in hydraulic and industrial applications where flexibility is crucial. Conversely, thermoplastic hoses are lighter and more resistant to chemical degradation, making them suitable for applications requiring enhanced chemical compatibility and lower weight.
Reinforcement Materials
The reinforcement of hoses is critical for enhancing their strength and pressure tolerance. Common reinforcement materials include textile braids, steel wire, and spiral wire. The choice of reinforcement depends on the hose’s application, pressure requirements, and environmental conditions. Proper reinforcement helps prevent hose collapse or rupture under high pressure, ensuring reliable performance.
D. Key Considerations During the Fabrication Process
Pressure Ratings
Understanding the pressure rating of a hose is vital for ensuring it can handle the intended application. The pressure rating indicates the maximum pressure the hose can withstand without failing. Selecting hoses with appropriate ratings is essential to avoid catastrophic failures that can lead to leaks or equipment damage.
Temperature Ranges
Hoses must also be fabricated to endure specific temperature ranges. Extreme temperatures can affect the material properties, leading to hose degradation. It is crucial to select materials that maintain their integrity within the operational temperature limits to ensure longevity and performance.
Fluid Compatibility
Different fluids can react differently with hose materials, leading to deterioration or failure. Therefore, it is essential to assess the compatibility of the hose material with the fluids it will transport. Ensuring fluid compatibility helps prevent chemical reactions that could compromise the hose’s performance and safety.
Common Mistakes in Hose Fabrication
A. Inadequate Material Selection
One of the most critical mistakes in hose fabrication is selecting the wrong materials. Each application requires specific characteristics, such as chemical resistance, flexibility, and durability. For instance, using a rubber hose in an environment where chemical exposure is common can lead to rapid degradation, resulting in leaks and potential system failures. Conversely, thermoplastic hoses, while lightweight and flexible, may not withstand high-pressure applications if improperly chosen. The consequences of incorrect material selection can include increased maintenance costs, reduced efficiency, and safety hazards, making it essential to thoroughly understand the requirements of each application before fabrication begins.
B. Miscalculating Hose Lengths
Accurate hose length calculations are crucial for optimal system performance. Miscalculating the length can lead to several issues, such as excessive bending, kinking, or tension, which can compromise the integrity of the hose. A hose that is too short may lead to system strain, while an overly long hose can create unnecessary slack, increasing the risk of abrasion and wear. Both scenarios can result in inefficient fluid flow and potential system failures. To avoid these pitfalls, it’s important to carefully measure the required lengths and account for any bends or fittings that may alter the final length during installation.
C. Neglecting Pressure Ratings
Pressure ratings are a fundamental aspect of hose fabrication that must never be overlooked. Each hose is designed to handle a specific maximum pressure, and exceeding this limit can lead to catastrophic failures, including ruptures or leaks. Neglecting pressure ratings can occur when operators underestimate the system’s demands or fail to consider pressure surges. This mistake not only jeopardizes equipment but also poses significant safety risks to personnel. It’s essential to consult manufacturer specifications and ensure that the selected hose is rated for the intended application, including any potential pressure spikes.
D. Poor Joint and Fitting Choices
The choice of joints and fittings is another area where common mistakes can occur. Using incompatible fittings can lead to leaks and system inefficiencies. There are various fitting types, such as threaded, flanged, and quick-connect, each suited for specific applications. Selecting the wrong fitting can result in improper sealing or weak connections, leading to failures. For example, using a non-matching fitting for a hydraulic hose can cause a pressure drop or even catastrophic failure under load. Understanding the specific requirements of each application and selecting the appropriate fittings is crucial for maintaining system integrity and reliability.
Best Practices for Hose Installation
A. Pre-installation Preparation
Before installation, thorough preparation is crucial to ensure a successful outcome. First, inspecting all components, including hoses, fittings, and connectors, helps identify any defects or damages that could compromise performance. Look for signs of wear, corrosion, or contamination that could affect the integrity of the system. Additionally, ensuring cleanliness is vital. Contaminants such as dirt, dust, and debris can enter the system during installation, leading to blockages or premature wear. A clean workspace and the use of proper handling techniques will help maintain the integrity of the components throughout the installation process.
B. Proper Installation Techniques
Utilizing correct installation techniques is essential for maximizing the longevity and performance of hoses. Proper hose routing is one of the key aspects; hoses should follow the shortest and most direct path, avoiding unnecessary twists and turns. This minimizes stress on the hose and promotes efficient fluid flow. It’s also important to avoid kinks and bends, as these can restrict flow and create weak points that may fail under pressure. Always refer to the manufacturer’s guidelines for recommended routing paths and installation angles to ensure optimal performance.
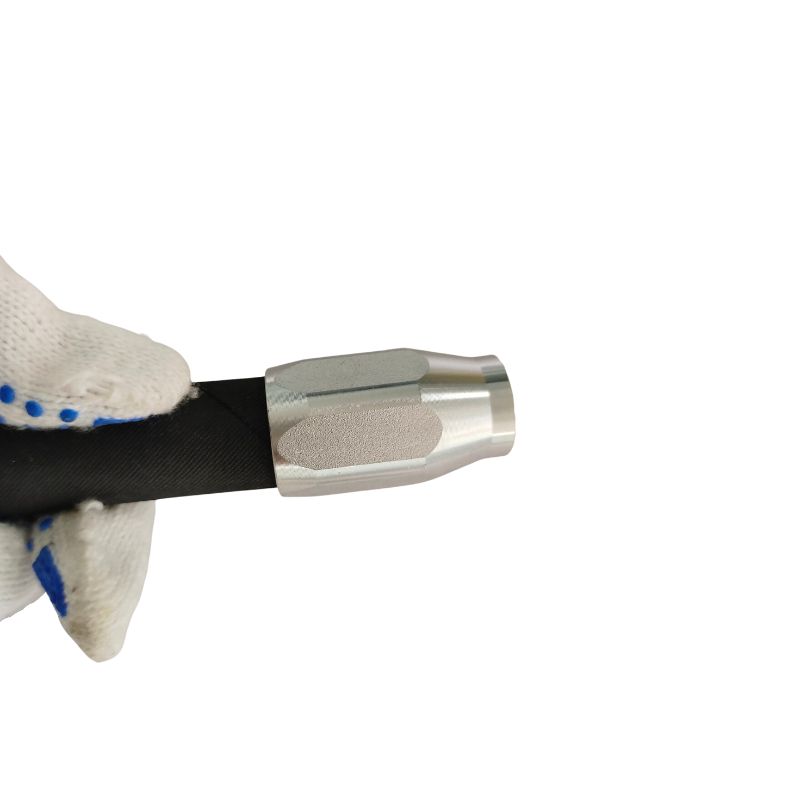
C. Securing Hoses and Fittings
Once installed, securing hoses and fittings is necessary to prevent movement and stress during operation. The use of clamps and supports is essential in achieving this. Properly placed clamps keep hoses in position and reduce the risk of abrasion against other surfaces. When selecting clamps, ensure they are appropriate for the hose diameter and material, as poorly chosen clamps can cause damage. Additionally, using supports, such as brackets or hangers, can further stabilize the hose assembly, allowing it to function efficiently without risk of disconnection or wear.
D. Importance of Torque Specifications for Fittings
Finally, adhering to torque specifications for fittings is critical in hose installation. Over-tightening can damage components, leading to leaks, while under-tightening can result in loose connections that may fail during operation. Each fitting has specific torque requirements outlined by the manufacturer, and it’s essential to use a calibrated torque wrench to ensure accuracy. Following these specifications guarantees a secure connection, enhancing the overall reliability of the hose assembly. By prioritizing these best practices, you can significantly reduce the likelihood of common mistakes and ensure a successful installation.
Common Mistakes in Hose Installation
A. Skipping the Preparation Phase
One of the most critical mistakes during hose installation is skipping the preparation phase. This phase involves inspecting all components, ensuring cleanliness, and planning the installation process. Neglecting this step can lead to using damaged or contaminated parts, resulting in leaks or system failures. Proper preparation sets the foundation for a successful installation, making it essential to take the time to conduct thorough checks and maintain a clean workspace.
B. Improper Routing and Securing of Hoses
Improper routing and securing of hoses can severely impact system performance. Hoses should be routed to minimize bends and kinks, which can restrict fluid flow and increase the likelihood of wear. Additionally, failing to secure hoses properly can lead to movement during operation, causing abrasion against other components or even disconnection. Ensuring that hoses are routed correctly and secured with appropriate clamps and supports is vital for maintaining system integrity.
C. Ignoring Alignment of Fittings
Ignoring the alignment of fittings during installation is a common oversight that can lead to significant issues. Misaligned fittings can create stress points, resulting in leaks or premature wear. Ensuring that all fittings are aligned correctly not only promotes better fluid flow but also enhances the longevity of the hose assembly. Operators should take the time to check alignment before finalizing connections, as this small step can prevent larger problems down the line.
D. Failing to Test the System Post-installation
After installation, failing to test the system is a critical error. System testing is essential to verify that the hoses are functioning correctly and that there are no leaks or pressure issues. Skipping this step can result in undetected problems that could lead to catastrophic failures during operation. Conducting a thorough pressure test and visual inspection ensures that the installation is sound and that the system operates as intended.
E. Neglecting Maintenance Checks
Even after a successful installation, neglecting regular maintenance checks can lead to long-term issues. Hoses should be regularly inspected for signs of wear, leaks, or other damage that could compromise performance. Establishing a routine maintenance schedule helps identify potential problems early, allowing for timely repairs or replacements. Maintaining awareness of the condition of hoses and fittings ensures system reliability and safety over time, reducing the risk of unexpected failures.
Troubleshooting Common Issues
A. Identifying Leaks and Their Causes
Leaks in hydraulic and industrial systems can lead to decreased efficiency, environmental hazards, and safety risks. Identifying the source of a leak is the first step in troubleshooting. Common causes of leaks include improper fittings, worn-out hoses, and inadequate installation practices.
Visual Inspection: Regular visual inspections can help spot leaks early. Look for signs of fluid accumulation, dampness around fittings, and any unusual wear on hoses.
Pressure Testing: Conducting pressure tests can help pinpoint leaks. By gradually increasing pressure in the system and monitoring for drops, you can identify potential leak points.
Fluid Analysis: Analyzing the type of fluid leaking can also provide clues. For example, hydraulic fluid leaks typically have a different texture and viscosity compared to water or other liquids.
B. Diagnosing Hose Failures
Hose failures can occur due to various reasons, and diagnosing the cause is crucial for effective repairs. Common indicators of hose failure include reduced fluid flow, abnormal noises, or visible damage.
Visual Checks: Examine the hose for cracks, abrasions, or bulges. These signs often indicate wear that could lead to failure.
Pressure Monitoring: Fluctuations in pressure readings can suggest a blockage or a failure in the hose. Keeping an eye on pressure gauges can help detect these issues early.
Temperature Monitoring: Excessive heat can weaken hoses, especially those not rated for high temperatures. Monitoring the operating temperature helps ensure that hoses are functioning within safe limits.
C. Solutions for Common Installation Problems
Several installation-related issues can arise, but many have straightforward solutions:
Misalignment of Fittings: If fittings are misaligned, they can often be adjusted without removing the entire assembly. Ensure fittings are aligned before tightening to avoid stress points.
Kinks and Bends: If kinks occur after installation, rerouting the hose or adding support can help alleviate stress. Always follow recommended routing guidelines to prevent this issue from arising.
Leakage at Fittings: Tightening fittings to the specified torque can usually solve minor leaks. If leaks persist, consider replacing the fittings or using sealants designed for hydraulic applications.
Hose Wear: Regular maintenance checks can help identify wear before it leads to failure. Replacing hoses showing signs of wear can prevent future issues and ensure system reliability.
Conclusion
In summary, the importance of proper hose fabrication and installation cannot be overstated. These processes are fundamental to ensuring the safety, efficiency, and longevity of hydraulic and industrial systems. When done correctly, they minimize the risk of leaks, equipment failures, and costly downtime. Understanding common mistakes and best practices empowers professionals to make informed decisions that enhance system reliability and performance.
FAQ
What is hose fabrication?
Hose fabrication is the process of designing and assembling hoses to meet specific application requirements, including selecting materials and fittings.
What are common types of hoses?
The most common types are hydraulic hoses, industrial hoses, and specialty hoses, each serving different purposes across various industries.
Why is proper hose installation important?
Proper installation ensures optimal performance, minimizes the risk of leaks and failures, and prolongs the lifespan of the hose assembly.
What materials are typically used for hoses?
Common materials include rubber and thermoplastic, with reinforcements such as steel wire or fabric for added strength.
What should I do if I detect a leak?
Inspect the hose and fittings for damage, conduct pressure tests to locate the source, and replace any faulty components immediately.
How can I ensure my hose system lasts longer?
Regular maintenance checks, proper installation techniques, and using quality materials can significantly extend the lifespan of your hose system.