Surface treatments are designed to improve key characteristics such as hardness, corrosion resistance, wear resistance, and overall durability. For instance, a well-applied coating can reduce friction, leading to smoother valve operation and lower chances of valve malfunction. Furthermore, certain treatments protect the valve from harsh chemicals and extreme temperatures, making them ideal for demanding environments.
Understanding Ball Valve Surface Treatment
What is Ball Valve Surface Treatment?
Ball valve surface treatment refers to a variety of processes applied to the external and internal surfaces of a valve to improve its resistance to wear, corrosion, and other forms of damage. These treatments typically involve applying coatings, plating, or other methods to alter the surface properties of the ball valve material. The primary goal is to enhance the valve’s ability to perform in harsh operating conditions, extending its lifespan and ensuring reliable performance. Surface treatments can also improve the valve’s sealing capabilities, reduce friction, and prevent material degradation over time.
The Role of Surface Treatment in Valve Durability and Longevity
Surface treatment plays a crucial role in extending the durability and lifespan of ball valves. Without these protective measures, valves are more susceptible to wear, corrosion, and other forms of deterioration that can shorten their service life. By applying surface treatments like hard chrome plating or PTFE coatings, the valve’s surface becomes more resistant to abrasion, chemicals, and extreme temperatures. This not only helps the valve last longer but also ensures that it operates efficiently, reducing the frequency of repairs or replacements. In addition, surface treatments can improve the valve’s sealing properties, leading to fewer leaks and better overall performance, especially in high-pressure systems.
Common Challenges Faced Without Proper Surface Treatment
Without proper surface treatment, ball valves are prone to a variety of issues that can compromise their performance and reliability. Some common challenges include:
Corrosion: Ball valves exposed to harsh chemicals, water, or extreme environments are vulnerable to rust and corrosion, which can cause leakage and failure.
Wear and Tear: Constant motion and friction between valve components can lead to premature wear, affecting the valve’s ability to seal properly and control flow effectively.
Erosion: In high-velocity fluid systems, particles can cause erosion on valve surfaces, resulting in damage to the valve body and internal components.
Reduced Efficiency: The lack of surface treatments can lead to increased friction, reducing the valve’s operational efficiency and making it harder to open or close.
Shortened Lifespan: Without protective coatings, the valve is more likely to suffer from early degradation, requiring more frequent maintenance or replacement, which adds operational costs.
Types of Ball Valve Surface Treatments
Hard Chrome Plating
Benefits of Hard Chrome Plating for Ball Valves Hard chrome plating is one of the most widely used surface treatments for ball valves, offering superior protection against wear and corrosion. The process involves electroplating a layer of chrome onto the valve surface, which creates a hard, durable finish that significantly enhances the valve’s performance. The key benefits include increased hardness, reduced friction, and a smoother surface, all of which contribute to longer valve life and better operational efficiency.
How Hard Chrome Enhances Corrosion Resistance and Wear Resistance Hard chrome plating provides exceptional protection against wear caused by friction and erosion, making it ideal for valves subjected to harsh operational environments. The plating’s dense, smooth structure helps prevent the formation of rust and corrosion, even in water or chemically aggressive environments. Additionally, the increased hardness of the chrome-plated surface improves wear resistance, ensuring that ball valves maintain their functionality over time, even under high-stress conditions.
When to Choose Hard Chrome Plating for Your Valves Hard chrome plating is best suited for applications where valves are exposed to frequent wear, high friction, or aggressive fluids. Industries such as oil and gas, chemical processing, and water treatment commonly use hard chrome-plated ball valves to ensure reliability and reduce maintenance costs. If your valves operate in conditions where durability and resistance to wear and corrosion are essential, hard chrome plating is an excellent choice.
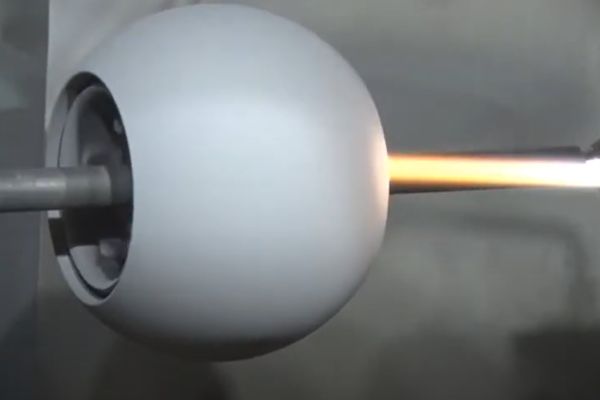
Ceramic Coating
Advantages of Ceramic Coatings for Ball Valve Surfaces Ceramic coatings are a cutting-edge surface treatment that enhances a valve’s ability to withstand extreme wear and erosion. These coatings are typically applied as a thin layer of ceramic material, providing a high level of hardness and resistance to abrasive forces. Ceramic coatings can also withstand high temperatures and aggressive fluids, making them ideal for challenging applications. The key benefits include improved valve longevity, increased surface hardness, and the ability to protect against abrasive particles.
How Ceramic Coatings Improve Valve Performance Ceramic coatings improve valve performance by creating a tough, impermeable surface that prevents wear and tear. This is particularly beneficial in valves exposed to high-velocity fluid or slurry systems, where erosion can degrade the valve’s function over time. Ceramic coatings also offer excellent thermal stability, allowing valves to maintain their performance in high-temperature environments. Furthermore, they can reduce friction, making valve operation smoother and more efficient.
Best Applications for Ceramic Coatings in Industrial Settings Ceramic coatings are ideal for applications where valves are exposed to abrasive materials, extreme temperatures, or high-velocity flows. Industries like mining, petrochemical, and power generation frequently use ceramic-coated ball valves to ensure operational efficiency and minimize downtime. They are especially valuable in systems handling slurries, chemicals, or steam, where standard coatings may not provide sufficient protection.
PTFE Coating
What is PTFE Coating and Why is it Important? PTFE (Polytetrafluoroethylene) is a synthetic polymer known for its excellent chemical resistance and non-stick properties. When applied as a coating to ball valves, PTFE creates a protective barrier that prevents the valve surfaces from being damaged by aggressive chemicals, solvents, or acids. PTFE coatings are particularly beneficial in environments where valves are exposed to corrosive substances that could otherwise degrade the valve material.
How PTFE Protects Against Chemical Damage PTFE coatings provide an impermeable layer that prevents corrosive substances from coming into contact with the underlying metal, effectively shielding the valve from chemical damage. This coating ensures that the valve remains functional even when exposed to harsh chemicals, acids, or solvents. Additionally, PTFE’s non-stick properties reduce the accumulation of deposits or scale, ensuring that the valve’s performance remains unaffected by chemical buildup.
The Use of PTFE Coatings in High-Temperature Environments While PTFE is best known for its chemical resistance, it also performs well in high-temperature environments. The coating can withstand temperatures up to 260°C (500°F), making it ideal for applications in industries like food processing, pharmaceuticals, and chemical manufacturing, where both high temperatures and corrosive chemicals are present. PTFE coatings ensure the valve operates smoothly, even in challenging conditions.
Electroless Nickel Plating
Key Benefits of Electroless Nickel Plating for Valves Electroless nickel plating is a highly effective, cost-efficient surface treatment that offers excellent protection against corrosion and wear. Unlike electroplating, which requires an external current, electroless nickel plating relies on a chemical reaction to deposit a uniform nickel layer over the valve surface. This plating offers a consistent thickness, even on complex geometries, and provides improved corrosion resistance, reduced friction, and enhanced wear resistance.
How Electroless Nickel Enhances Corrosion and Wear Resistance Electroless nickel plating enhances corrosion resistance by forming a dense, non-porous layer that protects the valve from water, chemicals, and other corrosive agents. It also improves wear resistance, as the nickel layer is harder and more durable than many base materials. This makes electroless nickel plating a popular choice for valves used in water treatment, petrochemical, and industrial fluid systems.
The Versatility of Electroless Nickel Plating in Various Industries Electroless nickel plating is widely used in diverse industries due to its versatility and cost-effectiveness. It is ideal for valves in food processing, water treatment, and chemical industries, where durability and resistance to corrosion are critical. This surface treatment is also used in applications where uniform coating is essential, such as in valves with intricate shapes or tight tolerances.
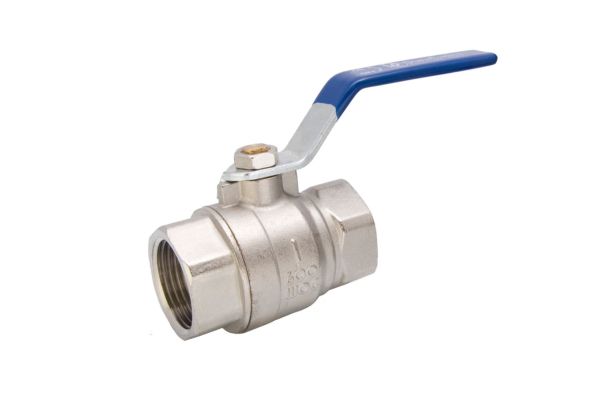
PVD Coating
What is PVD (Physical Vapor Deposition) Coating? PVD coating is a modern surface treatment process in which thin layers of material are deposited onto the valve surface using a vacuum process. The material, often a metal or ceramic, is vaporized and then condensed onto the valve, creating a highly durable and wear-resistant coating. PVD coatings are known for their high surface hardness, wear resistance, and aesthetic finish, making them an excellent choice for high-performance valves.
How PVD Improves Surface Hardness and Wear Resistance PVD coating improves the surface hardness of ball valves by creating a thin, yet highly durable, protective layer. This increases the valve’s resistance to scratching, abrasion, and erosion, even in high-pressure or high-velocity fluid systems. PVD coatings are also resistant to corrosion and reduce friction, helping the valve to operate smoothly while maintaining its integrity over time.
Popular Applications of PVD Coatings in the Valve Industry PVD coatings are commonly used in industries requiring high-performance valves, such as aerospace, automotive, and high-tech manufacturing. In these industries, valves are exposed to extreme pressures, temperatures, and abrasive materials. PVD coatings offer a reliable solution, providing enhanced durability and ensuring that the valve can withstand demanding operational conditions while maintaining peak performance.
The Science Behind Surface Hardening: How It Increases Valve Longevity
What is Surface Hardening, and How Does It Work?
Surface hardening is a metallurgical process designed to increase the hardness of the outer layer of a material, typically metal, without affecting the material’s core properties. In ball valves, this means that the external surface is treated to resist wear, abrasion, and corrosion, while the interior retains its ductility and strength. The hardening process works by altering the structure of the material’s surface atoms, making them more resistant to the forces they will face in operation.
The process typically involves the diffusion of carbon or other hardening elements into the surface layer of the valve. The result is a hardened outer surface that can withstand friction and harsh conditions while maintaining the core material’s toughness and flexibility. This makes the ball valve more durable, with the added benefit of preserving its internal strength for optimal performance over time.
Different Surface Hardening Methods for Ball Valves
There are several methods for surface hardening ball valves, each offering unique advantages depending on the application and material. The most common methods include:
Carburizing Carburizing involves heating the valve to a high temperature in a carbon-rich environment, allowing carbon to diffuse into the surface layer. This process creates a hardened outer layer while maintaining a softer, tougher core. It’s particularly useful for valves that need to withstand high wear while still maintaining flexibility.
Nitriding Nitriding is a heat treatment process that introduces nitrogen into the surface of the material, creating a hard, wear-resistant surface. This method improves the surface hardness without the need for additional coatings or treatments, making it ideal for high-performance ball valves in aggressive environments.
Induction Hardening Induction hardening uses electromagnetic induction to heat the surface of the valve quickly and uniformly, followed by rapid cooling (quenching). This process creates a hardened outer layer with minimal distortion or damage to the valve’s internal structure. It is commonly used for valves that need localized surface hardening and fast processing times.
Flame Hardening In flame hardening, a high-temperature flame is used to heat the valve’s surface, followed by immediate cooling in water or oil. This process is suitable for large ball valves that require selective hardening in specific areas, especially when dealing with wear-prone zones.
Laser Hardening Laser hardening uses a high-powered laser beam to heat the surface of the valve material, followed by rapid cooling. This method is highly precise, allowing for targeted hardening and minimal distortion. It is often used for high-precision applications where a controlled surface layer is crucial.
How Surface Hardening Improves Valve Lifespan and Performance
Surface hardening significantly extends the lifespan and enhances the performance of ball valves. Here’s how:
Enhanced Wear Resistance A harder surface is less susceptible to wear and tear, especially when the valve operates in high-friction environments. By making the outer layer of the valve harder, surface hardening reduces the effects of abrasion and minimizes the degradation of the valve’s moving parts, leading to a longer service life.
Reduced Risk of Deformation In high-pressure or high-velocity systems, valves can be subject to significant stresses. Surface hardening increases the ability of the valve to resist deformation under these conditions, maintaining its shape and functionality over time. This helps prevent issues like warping, which can compromise valve performance and lead to leaks.
Increased Corrosion Resistance Surface hardening processes like nitriding or carburizing often create a layer that enhances the valve’s resistance to corrosion. The hardened layer acts as a protective barrier against rust, acids, and other corrosive substances, helping to prevent the valve from failing prematurely in harsh chemical environments.
Improved Sealing Performance Harder surfaces often have smoother finishes, which can improve the valve’s sealing ability. In ball valves, where the sealing surfaces need to make a perfect contact, surface hardening can reduce the chance of leaks by improving the fit and reducing wear that might affect the seal integrity.
Better Overall Valve Performance By making the ball valve’s surface more resistant to external factors such as friction, erosion, and corrosion, surface hardening ensures that the valve operates more efficiently. This leads to fewer maintenance requirements, reduced downtime, and better overall system performance.
Maintenance Best Practices for Surface-Treated Ball Valves
Tips for Maintaining Surface-Treated Valves for Maximum Longevity
Regular Inspection and Cleaning Regularly inspect the ball valve for signs of wear, corrosion, or damage to the surface coating. Ensure that the valve’s exterior is clean and free from debris, dirt, or chemical buildup that could affect performance. Use non-abrasive cleaning solutions to avoid damaging the surface treatment.
Lubrication of Moving Parts For valves with moving components, proper lubrication is essential. Lubricate the stem and actuator regularly to ensure smooth operation and to reduce friction that could wear down the surface treatment. Use lubricants that are compatible with the valve’s material and the surface coating.
Monitor Operating Conditions Keep track of the operating conditions such as pressure, temperature, and flow rate to ensure that the valve is not subjected to extremes beyond its design specifications. Excessive pressure or temperature could damage the surface treatment or lead to premature failure.
Protect Against Contaminants Ensure that the valve is shielded from external contaminants that may compromise the coating, such as abrasives, chemicals, or moisture. This is especially important in environments with high dust levels or where the valve is exposed to aggressive chemicals.
Periodic Re-Coating or Touch-Up Depending on the type of surface treatment, you may need to re-coat or touch up certain areas of the valve after a set period. For instance, hard chrome plating may require periodic maintenance to prevent the coating from thinning in areas of high wear.
Temperature Management Ensure that the valve operates within its temperature range. Exposing surface-treated valves to temperatures that exceed their tolerance could degrade the coating and negatively affect valve performance. Implement temperature control systems if necessary.
Common Issues with Surface-Treated Valves and How to Resolve Them
Chipping or Cracking of Coatings
Cause: Impact or stress from operational forces may cause the surface coating to crack or chip, especially on hard chrome or ceramic coatings.
Solution: Inspect regularly for any signs of cracking or chipping. If detected, stop operation immediately and replace or repair the damaged components. Some treatments, like electroless nickel plating, can be repaired by re-plating.
Corrosion Under the Coating
Cause: Inadequate surface preparation before applying the coating, or poor coating adhesion, can result in corrosion forming underneath the coating.
Solution: Ensure proper surface preparation during the initial installation. If corrosion is detected under the coating, consider re-coating the valve with a more suitable treatment and inspect the substrate material for damage.
Surface Wear and Erosion
Cause: Extended exposure to abrasive fluids or chemicals can wear down even the toughest surface treatments, such as ceramic or PVD coatings.
Solution: If excessive wear is observed, check if the valve has been exposed to higher-than-recommended operational stress. Regularly inspect for early signs of wear and replace components before failure occurs.
Improper Valve Sealing
Cause: If the surface treatment wears down or becomes damaged, it could lead to poor sealing, causing leaks and inefficiencies.
Solution: Regularly monitor the valve’s sealing ability. If leaks occur, inspect the sealing surfaces and clean them to remove any buildup. For surface-treated valves, reapply the coating if necessary.
Temperature-Related Degradation
Cause: Surface treatments like PTFE or ceramic coatings may degrade or lose effectiveness if exposed to temperatures beyond their specified limits.
Solution: Ensure that the ball valve operates within the designated temperature range. In extreme cases, upgrade to a higher-temperature-resistant coating, such as PVD or hard chrome plating.
Conclusion
Remember, the right surface treatment not only extends the lifespan of your ball valves but also reduces downtime, lowers maintenance costs, and improves overall system efficiency. Regular maintenance and proper monitoring will ensure that your surface-treated valves continue to perform at their best for years to come.
FAQ
What is a ball valve surface treatment?
A ball valve surface treatment involves applying coatings or plating to the valve’s surface to enhance its resistance to wear, corrosion, and other forms of damage, ensuring longer lifespan and better performance.
Why do ball valves need surface treatment?
Surface treatments improve the valve’s durability, reduce friction, prevent corrosion, and enhance wear resistance, which helps the valve perform reliably in demanding environments.
What are the most common types of ball valve surface treatments?
The most common types include hard chrome plating, ceramic coatings, PTFE coatings, electroless nickel plating, and PVD coatings, each offering different benefits depending on the application.
How do I choose the right surface treatment for my valve?
Consider factors such as the operating environment, the level of wear resistance required, and your budget. For example, ceramic coatings are ideal for high abrasion, while PTFE coatings are best for chemical resistance.
How long do surface-treated ball valves last?
Properly maintained surface-treated ball valves can last significantly longer than untreated valves. The treatment protects the valve from wear and corrosion, but regular inspections and upkeep are essential to maximize its lifespan.
Can I reapply or touch up the surface treatment on my valve?
Yes, in many cases, surface treatments like electroless nickel plating or hard chrome plating can be re-applied or touched up if they begin to degrade, ensuring continued protection and performance.