Ball valves are designed to last a long time, but like any mechanical component, they wear out over time. Without regular attention, small problems can pile up and become larger, more expensive problems that can lead to system downtime, leaks, or even catastrophic failures.
Common Causes of Ball Valve Failure
Valve Wear and Tear: Identifying the Culprits
Over time, ball valves experience natural wear and tear due to continuous operation, exposure to high pressures, and frequent cycling. This gradual deterioration can lead to reduced performance and failure if not addressed promptly. Some of the key components affected by wear and tear include the valve stem, seals, and the ball itself. The constant movement and friction between these parts can cause abrasion, leading to rough surfaces that impair the valve’s ability to seal properly.
Signs of Wear and Tear: Difficulty in operation, noticeable leaks, or an inability to achieve full closure are all indicators that wear has taken its toll on critical components.
How to Prevent: Regular inspection, proper lubrication, and replacing worn-out parts are key to preventing extensive damage from wear.
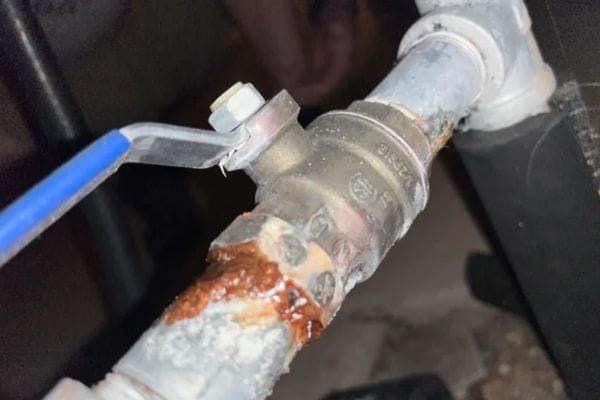
Valve Seat Damage: What It Means for Your Valve’s Function
The valve seat is one of the most critical components in a ball valve, responsible for ensuring a tight seal when the valve is closed. Valve seat damage, which can occur due to repeated opening and closing cycles, high-pressure surges, or exposure to extreme temperatures, can result in leakage or complete valve failure.
Signs of Valve Seat Damage: Leaks around the valve body, reduced sealing capability, and irregular valve operation are all signs that the valve seat may be damaged.
Why It Matters: If the valve seat is damaged, even the best-quality valve can no longer function as intended. A compromised seal can lead to fluid loss, system inefficiency, and safety risks.
Solution: Replacing the damaged seat or regrinding it to restore a proper seal is essential for keeping the ball valve in working condition.
The Role of Valve Packing in Valve Failure
Valve packing provides the sealing mechanism around the valve stem, preventing leaks along the stem and around the valve. Over time, the packing material can degrade due to exposure to high temperatures, pressure fluctuations, and chemical exposure, leading to leaks and valve malfunction. Improper installation or inadequate maintenance can also contribute to packing failure.
Signs of Valve Packing Failure: Leakage around the valve stem, excessive stem movement, or difficulty in turning the valve are all indications that the packing needs attention.
Why It Matters: Without functional valve packing, fluid or gas can escape through the stem, causing pressure loss and potential contamination of the surrounding environment.
Solution: Regular inspection and replacement of valve packing are necessary to prevent this issue. Tightening the packing or replacing it with a more durable material can solve the problem.
How Corrosion Impacts Ball Valve Performance
Corrosion is a major cause of failure in ball valves, especially in industries where valves are exposed to harsh environments, chemicals, or seawater. Corrosion can occur internally or externally and can severely affect the valve’s sealing ability, structural integrity, and overall function. Common types of corrosion affecting ball valves include galvanic corrosion, pitting corrosion, and stress corrosion cracking.
Signs of Corrosion: Rust or discoloration on the valve body, cracks or pitting on the ball or stem, and noticeable leakage are all signs that corrosion is affecting the valve.
Why It Matters: Corrosion weakens the valve material, reducing its ability to withstand pressure, temperature fluctuations, and chemical exposure. Over time, this leads to valve failure.
Solution: Corrosion-resistant materials like stainless steel, regular cleaning, and proper maintenance can help prevent corrosion. In cases where corrosion has already set in, the damaged components must be replaced to restore the valve’s functionality.
Diagnosing Ball Valve Issues
Ball Valve Leakage: Common Signs and Causes
Identifying Ball Valve Leakage
Ball valve leakage is one of the most common and troublesome issues that arise during the life of a valve. Leakage occurs when the sealing mechanism within the valve fails, causing fluid or gas to escape through the valve body, stem, or between the ball and seat. Understanding the signs and causes of leakage can help you quickly diagnose and fix the problem.
Signs of Leakage: The most obvious sign is visible leakage around the valve body, particularly at the stem or valve seat. You may also notice a decrease in system pressure, an unusual drop in flow, or audible sounds like hissing or gurgling when fluid is escaping.
Common Causes of Leakage: Leakage can be caused by a number of factors, including:
Worn-out valve seats: Over time, the valve seats can wear down, causing an imperfect seal when the valve is closed.
Damaged O-rings or seals: If these components degrade or crack, they can no longer provide the proper sealing effect.
Corrosion or erosion: Corrosion on the valve body, stem, or seals can create small cracks or holes that allow leakage.
Improper valve installation or misalignment: If the valve is not installed correctly, it may not achieve a tight seal, leading to leaks.
How to Fix Valve Leakage
Once you’ve identified leakage, it’s important to determine the source. In many cases, replacing the damaged seals, gaskets, or valve seats can stop the leakage. If the problem is more severe, such as internal corrosion, you may need to replace the entire valve or affected components.
Troubleshooting Valve Pressure Issues
Identifying Pressure Loss in a Ball Valve
A pressure drop is a serious issue that can compromise the performance of the entire system. Pressure issues in ball valves typically arise when there’s an obstruction, a seal failure, or a problem with the valve’s internal components. If you notice a significant decrease in flow rate or pressure, it could be a sign that the ball valve isn’t functioning properly.
Signs of Pressure Issues: The most common sign of a pressure problem is a noticeable dip in pressure readings from your pressure gauges. You may also experience inconsistent flow or difficulty in achieving the required flow rate.
Common Causes of Pressure Issues:
Partial closure of the valve: Sometimes, the ball doesn’t fully rotate, which may lead to a constriction in the flow and cause a drop in pressure.
Valve seat damage: If the valve seat is worn or damaged, it can create a leak path, allowing pressure to escape.
Blockage or debris: Any foreign particles lodged in the valve can obstruct the flow, leading to pressure fluctuations.
How to Resolve Pressure Problems
To troubleshoot pressure issues, first ensure that the valve is fully open and operating correctly. Inspect the valve seat and seals for any damage, and clean the valve to remove debris. If the issue persists, consider replacing the faulty components or recalibrating your pressure settings to ensure the system runs smoothly.
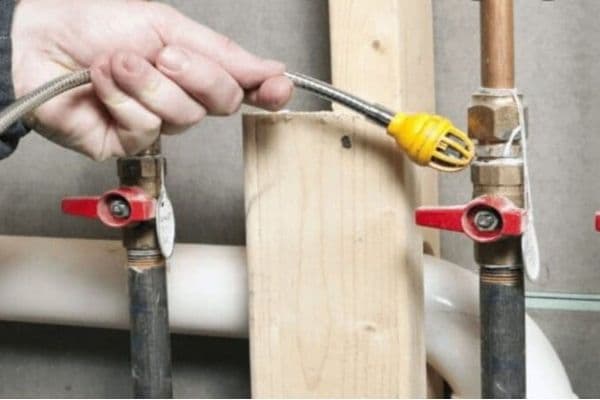
How to Identify Valve Stem Seal Failures
Understanding Valve Stem Seal Functions
The valve stem seal is a crucial component in maintaining the integrity of the valve’s operation. It ensures that no leakage occurs along the stem, where the ball is rotated to control fluid flow. Stem seal failure can result in leaks, system pressure loss, and even valve malfunction.
Signs of Valve Stem Seal Failure:
Visible leaks around the valve stem: Fluid may leak from the valve stem or around the packing area.
Increased friction or resistance during valve operation: If the valve becomes harder to turn, it could be due to a damaged stem seal that’s causing excessive friction.
Loss of fluid: A stem seal failure often results in a loss of pressure, causing fluid to escape from the valve and leading to system inefficiencies.
Common Causes of Stem Seal Failure
Improper installation: Incorrect installation of the stem seals can lead to early wear or misalignment, causing leaks.
Worn packing materials: Over time, the packing material around the stem can wear out, crack, or shrink, leading to leaks.
Exposure to extreme temperatures or chemicals: Excessive heat or harsh chemical exposure can degrade the material of the stem seal, compromising its integrity.
Fixing Valve Stem Seal Failures
To fix a stem seal failure, you may need to replace the packing or seal material. Depending on the valve design, this may involve disassembling the valve, cleaning the stem and packing area, and installing new seals or packing. Lubricating the stem with a suitable valve lubricant can also help reduce friction and improve sealing.
Recognizing Sealing Problems in Ball Valves
Common Types of Sealing Problems
Sealing issues in ball valves can occur at various points, including the valve seat, the stem, and the ball itself. These problems usually stem from improper maintenance, wear, or external damage. Sealing issues can lead to leaks, loss of pressure, and system inefficiency.
Signs of Sealing Problems:
Leakage from the valve body, especially around the ball or stem.
Inability to fully shut the valve: The ball valve may not close completely, which leads to improper sealing.
Irregular flow or pressure fluctuations: A valve with sealing problems may allow fluid or gas to bypass, affecting the pressure and flow rate.
Causes of Sealing Issues
Worn or damaged valve seats: Valve seats are critical for ensuring a proper seal when the valve is closed. Over time, they can degrade, leading to leaks.
Ball misalignment: If the ball inside the valve is not correctly aligned or damaged, it may not provide a complete seal when the valve is closed.
Aging seals and gaskets: Seals and gaskets around the valve can degrade due to age, exposure to chemicals, and high temperatures, resulting in ineffective sealing.
Solving Sealing Problems
To address sealing problems, first inspect the seats, seals, and ball for damage. Replace any worn-out components such as seals, gaskets, or valve seats. If the ball is damaged, it may need to be replaced as well. Ensuring proper valve maintenance and lubrication can help prevent sealing problems in the future.
Step-by-Step Guide to Ball Valve Repair
Preparing for Ball Valve Disassembly
Before diving into any ball valve repair, ensuring safety should be your first priority. Disassembling a ball valve can expose you to high-pressure systems, hazardous materials, and potential valve failure risks, so taking the right precautions is critical.
Isolate the Valve
Shut off the system: Ensure that the fluid or gas supply to the valve is completely isolated. Close the upstream and downstream valves and depressurize the system before proceeding with any disassembly.
Drain residual fluid: Drain any remaining liquid or gas in the valve and associated piping to avoid spills and pressure hazards.
Use Personal Protective Equipment (PPE)
Wear gloves: Protect your hands from sharp edges, hot surfaces, or harmful substances.
Safety goggles: Always wear goggles to prevent any debris or fluid from entering your eyes.
Face shield: If working with hazardous materials or under high pressure, use a face shield for additional protection.
Prepare the Work Area
Clear workspace: Make sure your workspace is clean and free of obstructions. Use a flat, stable surface, such as a workbench or repair station, for better control during disassembly.
Gather tools: Ensure you have all necessary tools on hand, such as wrenches, screwdrivers, valve repair kits, and any replacement parts you’ll need.
Verify Valve Type and Specifications
Consult manufacturer’s manual: Understanding the type of ball valve and its unique specifications will help in disassembly, repair, and reassembly. Different valve types may require special tools or procedures.
How to Fix a Leaking Ball Valve
Valve leakage is one of the most common issues in ball valve maintenance. Here’s how to fix it efficiently:
Identify the Source of the Leak
Check the valve seat: Leaks around the valve body may indicate worn or damaged valve seats.
Examine the stem: Leaks near the valve stem may be caused by a failing stem seal or packing.
Inspect the gaskets: Gasket leaks are common, especially in older valves or valves that have been over-tightened.
Tighten the Valve Packing
For minor leaks around the stem, you can often solve the problem by tightening the valve packing. Turn the packing nut clockwise to compress the packing material and stop the leak.
Important tip: Avoid overtightening, as this can cause excessive friction, making the valve harder to operate.
Replace the Valve Seat
If the valve seat is worn or damaged, it must be replaced. Use a seat removal tool to carefully extract the old seat and replace it with a new one.
Seat grinding: If the seat isn’t heavily damaged, you may be able to grind it back into shape to restore its sealing ability.
Replace the Gasket or Seals
If leaks are present around the valve body, replacing the gasket or seals may solve the issue. Use a high-quality replacement seal that matches the valve type and size to ensure a proper fit.
Reassemble and Test
Once the necessary repairs are made, carefully reassemble the valve. Test for leaks by pressurizing the system slowly and checking all repair points. Ensure the valve operates smoothly and closes tightly without leakage.
Repairing Valve Seats
Here’s how to do it properly:
Remove the Valve Seat
Disassemble the valve: After isolating and depressurizing the valve, remove the valve body to access the seats.
Use a seat removal tool: Gently remove the damaged seat using an appropriate seat extraction tool to avoid damaging the valve body.
Inspect the Valve Seat for Damage
Check for pitting or erosion: If the seat is cracked, pitted, or heavily eroded, it may need to be replaced entirely.
Assess the surface: If the damage is minimal, the seat may be restored by grinding or polishing it.
Grind the Valve Seat
Use a grinding tool: For minor damage, use a valve seat grinder to restore a smooth, even surface. This process will help the valve seal tightly when closed.
Polish the surface: After grinding, use a polishing tool to smooth the seat and remove any imperfections that could affect the seal.
Install the New or Restored Valve Seat
Carefully place the new or reconditioned valve seat into the valve body. Ensure it sits evenly and is securely in place to achieve the best seal.
Reassemble and Test the Valve
Reassemble the valve body and check for proper operation. Run a pressure test to ensure that the seat is properly sealed and there are no leaks.
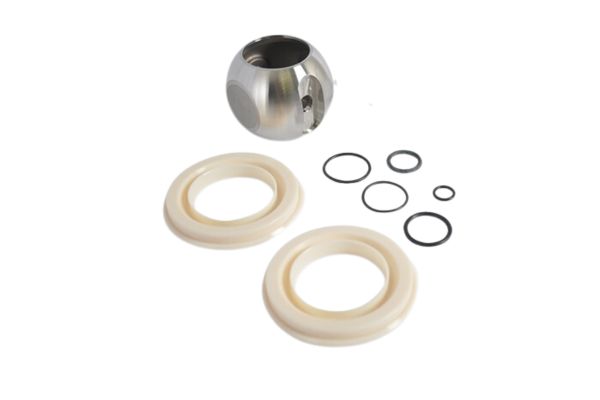
Replacing Valve Gaskets
Replacing gaskets is a straightforward process that can prevent leaks and ensure a tight seal in your ball valve.
Remove the Old Gasket
Disassemble the valve: Once the system is isolated and depressurized, remove the valve body to access the gasket.
Carefully remove the old gasket: Use a scraper or flat tool to carefully remove any remnants of the old gasket material from the valve body and cover.
Clean the Gasket Surfaces
Surface preparation: Clean both the valve body and cover where the gasket will be seated. Any dirt, debris, or old gasket material left behind can prevent the new gasket from sealing properly.
Install the New Gasket
Choose the right gasket material: Select a gasket material compatible with the valve’s operating conditions (e.g., temperature, pressure, and fluid type).
Place the new gasket: Position the new gasket properly in the valve body, ensuring it fits snugly without overhanging or being misaligned.
Reassemble the Valve
Reattach the valve cover and ensure all bolts or screws are tightened evenly. Tighten the fasteners in a crisscross pattern to prevent uneven compression of the gasket.
Test for Leaks
Once reassembled, pressurize the valve and inspect the gasket area for leaks. If there are no leaks, the repair is successful, and the valve is ready to be returned to service.
Valve Maintenance for Longevity
Best Practices for Regular Ball Valve Maintenance
To ensure that your ball valve operates efficiently for years, regular maintenance is a must. Consistent care will help avoid expensive repairs and extend the life of your valve. Here are some key practices for keeping your ball valve in optimal condition:
Schedule Routine Inspections
Visual checks: Conduct visual inspections at least once every 6 months (or as per manufacturer recommendations) to spot external signs of wear, leakage, or corrosion.
Internal inspections: Open the valve periodically to inspect for wear on internal components, such as the ball, stem, and seats.
Check for leaks: Inspect all valve connections, stems, and seals for signs of leakage, especially in high-pressure applications.
Keep Valves Clean
Clean valve surfaces: Remove dirt, debris, or corrosion from the valve body and surrounding piping regularly. Use appropriate cleaning agents to avoid damaging the valve material.
Flush the system: Depending on the fluid being transported, regular flushing can prevent debris from building up inside the valve, keeping it free from blockages that could impair performance.
Ensure Proper Valve Alignment
Correct installation: Ensure that the valve is installed correctly, with the handle or actuator in the proper position for easy operation. Misalignment can cause undue stress on the valve components and lead to premature failure.
Tighten Loose Parts
Check for loose bolts or nuts: Regularly tighten any loose bolts or nuts to maintain a secure connection, especially in high-vibration environments. Loose parts can cause leaks or even valve malfunction.
Lubrication
Lubrication plays a critical role in ensuring smooth operation and preventing wear in ball valves. Proper lubrication minimizes friction between moving parts, such as the ball, stem, and seals, which can help prevent excessive wear and failure.
Use the Right Lubricants
Choose the correct lubricant: Ensure that the lubricant used is compatible with the valve material and the type of fluid flowing through the valve. For example, if you’re working with high-temperature applications, select a lubricant designed for extreme conditions.
Grease vs. oil: Depending on the valve size and operating conditions, you may need to use grease for thicker consistency or oil for easier flow in smaller valves. Follow the manufacturer’s recommendation for best results.
Apply Lubricant Correctly
Target critical areas: Apply lubricant to key moving components like the valve stem, ball, and seals. This will reduce friction and prevent premature wear.
Lubrication frequency: Lubricate the valve at regular intervals, especially if the valve operates under high pressure or at extreme temperatures. Avoid over-lubricating, as it can attract dirt or debris.
Monitor Lubricant Condition
Inspect for deterioration: Over time, lubricants can degrade or become contaminated with particles, compromising their effectiveness. Regularly check the condition of the lubricant and replace it if necessary.
How to Properly Inspect Ball Valves for Early Detection
Regular inspections are vital for identifying potential issues before they become costly repairs. Here’s how to properly inspect ball valves for early detection of common problems:
Visual Inspection
Check for leaks: Inspect all valve bodies, stems, and seals for visible signs of leakage. A drop of fluid or even dampness around the valve could indicate early-stage failure.
Look for corrosion or wear: Examine the valve for any signs of corrosion, rust, or pitting, especially in areas exposed to harsh chemicals or high temperatures.
Operate the Valve
Turn the valve handle: Turn the valve handle or actuator to check for ease of operation. A stiff or hard-to-turn valve could indicate problems with the stem seal, ball wear, or internal damage.
Check for full closure: Open and close the valve to ensure it shuts fully without resistance. If the valve does not close completely or is difficult to turn, there may be debris or damage inside.
Pressure Testing
Conduct a pressure test: Performing a pressure test can help detect internal leaks that might not be visible on the outside. This involves closing the valve, pressurizing the system, and checking for any drops in pressure that could indicate internal sealing issues.
Check for Unusual Sounds or Vibrations
Listen to abnormal noises: A ball valve in good condition should operate quietly. Unusual sounds, such as grinding or squeaking, may indicate internal wear, friction, or damaged components.
Vibration: Excessive vibration during operation could be a sign of misalignment or an issue with the valve’s components.
Conclusion
To address these problems, regular inspections, timely repairs, and the use of high-quality parts are crucial. By staying proactive with inspections and repairs, you can enhance the lifespan and performance of your ball valves, preventing costly failures and ensuring reliable operation.
FAQ
How do I know if my ball valve is leaking?
Signs of leakage include visible fluid around the valve body, stem, or valve seat, as well as pressure loss or reduced flow rate. If you notice these issues, it’s time to inspect the valve for leaks.
Can I fix a leaking ball valve myself?
Yes, you can often fix a leaking ball valve by replacing worn-out seals, valve seats, or gaskets. For minor leaks, tightening the valve packing can help. However, if the problem persists, you may need to replace more significant components.
How often should I inspect my ball valve?
It’s recommended to inspect your ball valve at least once every 6 months or as per the manufacturer’s guidelines. Regular inspections help identify issues early and prevent unexpected failures.
What is the best lubricant for ball valve maintenance?
The best lubricant depends on the operating environment. For general applications, silicone-based or petroleum-based lubricants work well. For high-temperature or harsh chemical environments, use specialized lubricants suited for those conditions.
How do I prevent corrosion in my ball valve?
To prevent corrosion, use corrosion-resistant materials like stainless steel, regularly clean the valve, and replace damaged or worn-out components. Also, ensure proper installation and minimize exposure to harsh chemicals.
When should I replace my ball valve?
You should replace your ball valve if it is severely corroded, has irreparable seat or stem seal damage, or if it no longer functions properly despite repairs. Regular maintenance can extend its life, but if a valve is beyond repair, replacement is necessary to maintain system integrity.