How do you choose the right valve? Let’s take a closer look at two common options: the orbit valve and the ball valve. These valves may both serve the same basic function—controlling fluid flow—but they differ greatly in design, operation, and ideal applications. In short, while both valves control fluid flow, their performance and functionality vary based on design.
Orbit Valve vs Ball Valve: A Quick Overview
What is an Orbit Valve?
An orbit valve is a type of valve known for its unique rotary disc design, primarily used in applications where precise flow regulation is required. Unlike other valves that rely on a simple opening and closing mechanism, the orbit valve controls flow by rotating a disk in such a way that it gradually adjusts the opening size, allowing for more accurate flow control. This feature makes orbit valves especially useful in irrigation, HVAC systems, and any application that requires steady, adjustable flow.
Design: Orbit valves consist of a rotating disk that controls the flow of fluid. The disk is turned by a mechanical actuator, allowing operators to control the flow incrementally.
Function: Orbit valves are designed for flow modulation, not just simple on/off control. They are ideal for systems that require fine-tuned adjustments over time, providing consistent performance under varying pressure conditions.
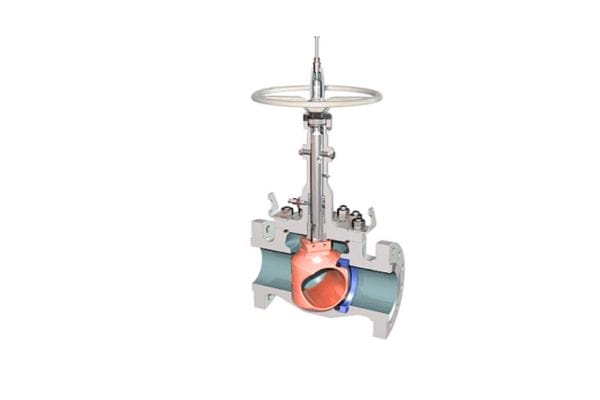
What is a Ball Valve?
A ball valve is a widely used type of valve with a spherical ball that controls the flow of fluid. The ball has a hole through the middle, and when the valve handle is turned, the ball rotates to either align the hole with the pipe (allowing flow) or block the hole (shutting off flow). Ball valves are known for their simple operation, reliable sealing, and durability, making them a go-to option in many industrial and residential settings.
Design: The ball valve features a hollow ball that rotates within the valve body. A handle or actuator is used to turn the ball, opening or closing the flow path.
Function: Ball valves excel at providing quick on/off control for fluid flow. Their ability to seal tightly and provide quick response times makes them highly effective in systems requiring reliable shutoff capabilities.
Key Differences in Their Design and Function
Flow Control vs. On/Off Control:
Orbit Valve: Designed for precise flow modulation, allowing operators to control the amount of fluid passing through at a continuous rate. This makes it perfect for applications that require variable flow, like irrigation and HVAC systems.
Ball Valve: Primarily designed for on/off control of fluid flow. When fully open, the ball valve allows maximum flow; when fully closed, it completely shuts off the flow. While some ball valves are available with modulating features, they are most commonly used for simple flow control.
Design Complexity:
Orbit Valve: More complex in design, with a rotating disc mechanism that provides gradual flow adjustments. This allows for fine-tuned flow regulation but requires more maintenance and careful operation.
Ball Valve: Simpler in design with fewer moving parts (just the ball and stem). Simplicity leads to ease of maintenance and quick operation, making ball valves ideal for systems that require fast, reliable operation with minimal maintenance.
Sealing Ability:
Orbit Valve: Typically designed for precise sealing, but not as efficient as the ball valve at preventing leaks in high-pressure situations. Orbit valves may have slightly more potential for leakage over time, depending on the material and pressure conditions.
Ball Valve: Known for excellent sealing capabilities, especially in high-pressure and high-temperature systems. The spherical ball ensures a tight seal when closed, minimizing the risk of leakage.
Application Suitability:
Orbit Valve: Best suited for systems requiring gradual and precise flow control. Popular in irrigation systems, HVAC, and water treatment systems where you need to adjust the flow over time.
Ball Valve: Ideal for quick shutoff and isolation applications, often used in water, oil, gas pipelines, and industrial chemical processes where flow needs to be rapidly stopped or started.
Orbit Valve Features: A Closer Look
Unique Design Elements of the Orbit Valve
The orbit valve stands out in the world of fluid control due to its unique design features that prioritize precise flow regulation. Here’s a closer look at the key design elements that make it different:
Rotating Disc Mechanism: Unlike traditional valves that use a simple opening and closing mechanism, the orbit valve uses a rotating disk to control flow. This disk gradually adjusts the opening size, which allows for more nuanced flow control rather than just binary open/close action.
Linear Flow Control: The orbit valve provides linear control over the flow of fluid, meaning that small adjustments to the valve position result in predictable, proportional changes in flow. This is particularly beneficial in systems that require steady, consistent flow adjustments, such as irrigation systems or HVAC setups.
Multi-Turn Actuation: Orbit valves often feature multi-turn actuation systems, meaning the valve can be adjusted slowly and incrementally to achieve the desired flow. This is in contrast to more common valve types, like ball valves, which typically offer a quick quarter-turn operation.
Increased Flow Area: Orbit valves are designed to maximize the flow area within the valve body. The larger flow passage allows for smoother fluid movement and less friction, which is critical for reducing wear and tear over time.
Self-Cleaning Design: Many Orbit valves incorporate self-cleaning mechanisms to prevent debris buildup that could obstruct the flow. This feature makes them ideal for environments where particulate matter in the fluid is a concern.
Key Features That Differentiate It from Other Valves
The orbit valve’s unique design features give it advantages in specific applications, setting it apart from other valve types like ball valves, globe valves, or gate valves:
Gradual Flow Control: Orbit valves provide more precise flow modulation compared to the typically all-or-nothing flow control found in ball valves. The ability to finely tune the flow makes orbit valves ideal for systems that require more control, such as irrigation or chemical dosing systems.
Higher Durability in Harsh Conditions: The orbit valve’s design often incorporates heavy-duty materials that allow it to withstand harsh environments, including high temperatures and abrasive fluids. This makes them more durable in industrial applications compared to other valves that might degrade more quickly.
Minimized Leakage: The design of the orbit valve generally results in lower leakage over time compared to older valve designs. The rotating disk and multi-turn actuation create a more efficient seal, which minimizes leakage when the valve is in the closed position.
Multi-Turn vs. Quarter-Turn Actuation: While ball valves use quarter-turn actuation for quick opening and closing, orbit valves require multiple turns to adjust the valve position. This gives the orbit valve more precise control over flow in applications where gradual adjustments are needed.
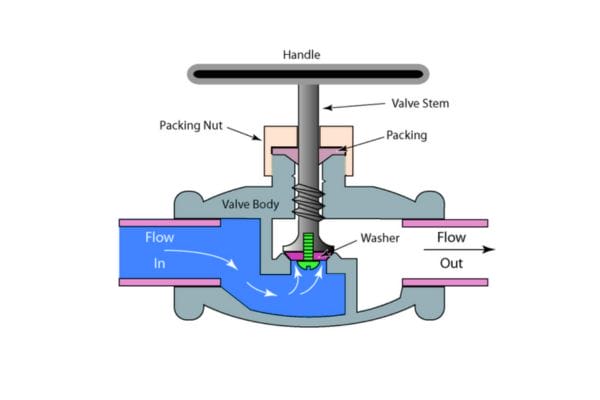
Orbit Valve Operation and Performance
The performance of an orbit valve is defined by how effectively it controls flow and handles different fluid conditions. Below are the operational characteristics that define its performance:
Flow Regulation: Orbit valves excel at modulating flow because of their rotary disk mechanism. As the disk rotates, the opening for fluid passage expands or contracts, giving the operator the ability to adjust the flow gradually. This is perfect for applications where fluid flow needs to be adjusted based on external conditions or system demands.
Pressure Handling: Orbit valves can be engineered to handle a wide range of pressures, though they are typically not as high-pressure resistant as ball valves. However, they perform exceptionally well in medium-pressure systems, such as irrigation or water treatment facilities, where steady and regulated flow is more important than withstanding extreme pressures.
Temperature Performance: Orbit valves are often designed to handle moderate to high temperatures without compromising performance. This makes them suitable for applications such as HVAC systems or boiler feedwater where temperature fluctuation is a common concern.
Leakage Prevention: Thanks to the rotating disk design and high-quality sealing materials, Orbit valves offer relatively low leakage rates, even in systems with fluctuating pressures. However, they may still experience leakage in applications where there are significant pressure spikes or where sealing components degrade over time.
Valve Operation: How Orbit Valves and Ball Valves Function
Detailed Comparison of Valve Operation Mechanisms
The way a valve operates is key to understanding how it manages fluid flow in various systems. Orbit and ball valves operate on very different mechanisms, each tailored to specific needs within fluid control systems. Here’s a detailed look at their operation:
Orbit Valve Operation: Orbit valves use a rotating disk mechanism that gradually adjusts the size of the opening through which fluid flows. When the valve is turned, the disk rotates in such a way that it incrementally changes the flow path, allowing for precise flow regulation. This multi-turn process allows the valve to modulate flow smoothly, making it suitable for systems where gradual adjustments are needed over time. This operation requires multi-turn actuation, which is typically controlled manually or via an automated actuator.
Ball Valve Operation: Ball valves, on the other hand, are designed for quick, simple on/off control. They feature a hollow ball with a hole in the middle that is positioned to allow or block flow depending on the valve’s rotation. When the valve handle is turned 90 degrees (a quarter-turn), the ball rotates, aligning or misaligning the hole with the pipe to either open or close the flow path. This simple design makes ball valves fast and easy to operate, requiring minimal turns to achieve the desired result.
How Orbit Valves Regulate Flow
Orbit Valves are particularly known for their precise flow control capabilities. Here’s how they accomplish that:
Gradual Adjustments: Unlike ball valves, which can only switch between fully open and fully closed states, orbit valves provide a gradual, incremental change in the flow as the disk is rotated. This allows for fine-tuned flow regulation over a continuous range, enabling operators to achieve the desired flow rate in real-time. This precision is especially useful in systems where constant adjustments are required, such as in irrigation, HVAC systems, or chemical dosing applications.
Controlled Flow Paths: The rotating disk inside the orbit valve can vary the size of the opening as it turns, controlling how much fluid can pass through. This variable flow control makes it ideal for applications where maintaining a steady and specific flow rate is important. Orbit valves often feature multi-turn actuators, which allow users to make small adjustments, giving them complete control over the flow rate.
Reduced Flow Resistance: The design of the orbit valve typically results in lower flow resistance than other types of valves. This is because the rotating disk design is less likely to create turbulent or obstructed flow paths, which can be common in valves like Globe Valves. The result is more efficient fluid movement and a reduced risk of pressure drops within the system.
Ball Valve’s Quarter-Turn Operation and Sealing Effectiveness
Ball valves operate using a quarter-turn mechanism, making them incredibly efficient for applications that require quick and reliable on/off control. Here’s how they function:
Quarter-Turn Operation: The most distinctive feature of a ball valve is its quarter-turn actuation. When the valve handle is rotated 90 degrees, the spherical ball inside the valve rotates to either open or close the flow path. This makes ball valves quick and easy to operate, as they require minimal motion to switch between the open and closed states. The ease of operation makes them a go-to choice for applications where rapid shutoff is necessary, such as in pipeline systems, water treatment, and chemical industries.
Sealing Effectiveness: Ball valves are renowned for their superior sealing capabilities. The spherical ball design ensures that the valve can create a tight seal when closed, significantly reducing the chance of leakage. The precision of the ball and the valve seat ensures a perfect seal even under high-pressure conditions. This makes ball valves especially useful in systems where minimizing leakage is critical.
Low Maintenance: Because of their simple construction and robust sealing properties, ball valves require less maintenance compared to more complex valves like the orbit valve. Their quick shut-off and effective sealing often result in fewer repair needs over time, making them a reliable choice in high-volume, industrial applications.
Valve Sealing and Leakage Prevention: Key Considerations
Orbit Valve Sealing Technology and Its Benefits
Sealing is a critical factor in ensuring that a valve performs reliably and efficiently without leakage, which can lead to system failures or safety hazards. Orbit valves are designed with sealing technologies that help minimize the risk of leaks, but there are certain features and considerations to keep in mind:
Rotating Disk Sealing: The Orbit valve uses a rotating disk to regulate fluid flow, and the design of this disk is often coupled with advanced sealing materials to prevent leaks at the valve’s interface. The gradual and incremental adjustment of the disk helps maintain a tighter seal over time, reducing the likelihood of wear and leakage.
Material Selection: Orbit valves are often made from durable materials like stainless steel or hardened alloys, which are resistant to corrosion and wear. These materials help ensure the integrity of the seal under varying conditions, including exposure to harsh chemicals or high temperatures.
Flow Direction and Sealing Efficiency: Orbit valves typically feature controlled flow paths that direct the fluid smoothly through the valve, reducing turbulence and the possibility of leaks. Additionally, because orbit valves are not intended for quick open/close operations, their sealing mechanisms are designed to hold up over long periods of steady use, providing consistent sealing performance in low to medium pressure systems.
Self-Cleaning Capabilities: Many orbit valves incorporate self-cleaning mechanisms that help prevent debris buildup on the seal. This feature is particularly beneficial in systems where sediment or particulate matter might otherwise compromise the valve’s sealing capability over time.
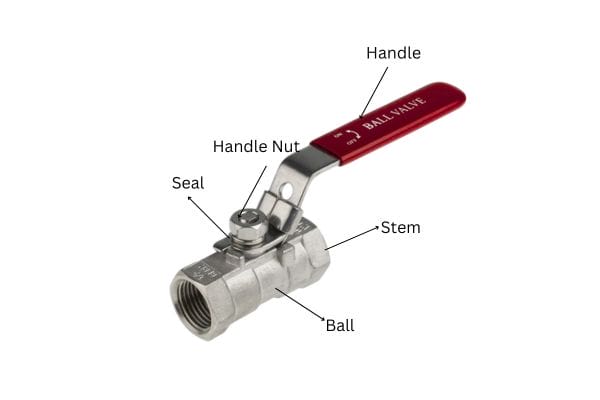
Ball Valve’s Sealing Efficiency and Leak Prevention
Ball valves are known for their exceptional sealing capabilities, which is one of the reasons they are so widely used in applications that require tight shutoff. Here are the key features of ball valve sealing technology:
Ball and Seat Design: The ball valve relies on the spherical ball with a hole in the center that rotates to control flow. When the valve is in the closed position, the ball is pressed against the valve seat, creating an airtight seal. This design makes it highly effective at preventing leaks when the valve is closed, even under high pressure or temperature conditions.
Sealing Materials: Ball valves often use soft-seated or metal-seated designs. Soft-seated ball valves use materials like Teflon (PTFE) or rubber to form a flexible seal that can withstand pressure fluctuations and ensure tight sealing. Metal-seated ball valves use materials like hardened steel or carbide for higher temperature and pressure applications, offering excellent sealing in harsh environments.
Minimal Wear and Tear: The quarter-turn operation of the ball valve minimizes friction between the ball and the seat, resulting in less wear and tear compared to other valve types that rely on more complex, multi-turn movements. This contributes to the long-term reliability and durability of the seal, which is essential in preventing leakage over the valve’s lifespan.
High Sealing Performance: Ball valves are often the preferred choice for high-pressure applications due to their superior sealing performance. When properly maintained, ball valves provide an exceptionally tight seal that reduces the risk of leakage in systems handling high-pressure fluids or gases.
Conclusion
An orbit valve is the better choice for systems that require precise flow regulation due to its ability to modulate flow gradually. The ball valve’s quarter-turn design is ideal if you need quick shutoff control. In terms of sealing performance, the ball valve provides a more reliable seal, particularly in high-pressure or high-temperature conditions.
FAQ
What is the main difference between an Orbit valve and a ball valve?
Orbit valves are designed for precise flow regulation and gradual adjustments, making them ideal for applications requiring continuous control. Ball valves, on the other hand, are used for quick on/off control and provide excellent sealing capabilities.
What applications are best suited for orbit valves?
Orbit valves are best for applications where precise flow regulation is needed, such as in irrigation systems, HVAC, and chemical dosing.
When should I choose a ball valve over an Orbit valve?
Choose a ball valve if you need a quick shutoff and tight sealing in high-pressure systems, such as gas pipelines, water systems, or chemical transport.
Are Orbit valves suitable for high-pressure applications?
Orbit valves perform well in medium-pressure systems, but they may not offer the same sealing performance under extreme high-pressure conditions as ball valves.
How does sealing performance differ between orbit and ball valves?
Ball valves offer superior sealing due to their spherical design and tight contact with the valve seat, reducing the risk of leaks. Orbit valves are designed for gradual flow control but may not seal as effectively under high pressure.
Which valve requires more maintenance, orbit valve or ball valve?
Ball valves generally require less maintenance due to their simple quarter-turn operation, while orbit valves may require more attention to ensure the rotating disk mechanism remains free from debris or wear.