A slip ball valve is a type of valve commonly used in fluid control systems to regulate the flow of liquids and gases. Unlike standard ball valves, slip ball valves feature a unique design that allows for easy installation and maintenance, typically in piping systems where space or flexibility is crucial.
What Is a Slip Ball Valve?
A slip ball valve is a specialized type of ball valve designed to allow for easy connection and disconnection of pipes without the need to remove the entire valve. This valve has a unique “slip” feature, where the valve can be slid over a pipe fitting, making installation and maintenance faster and more convenient, especially in tight or hard-to-reach spaces.
Key Differences Between Slip Ball Valves and Other Ball Valves
Slip Ball Valve vs. Full-Port Ball Valve: A full-port ball valve has a bore (hole) the same size as the pipe it connects to, allowing for unrestricted flow. In contrast, a slip ball valve typically has a slightly smaller bore, designed for ease of installation and space-saving rather than maximum flow efficiency.
Slip Ball Valve vs. Standard Ball Valve: A standard ball valve typically requires threading or welding for installation, whereas a slip ball valve uses a slip connection mechanism that simplifies the process. Standard ball valves may also be more rigid, while slip ball valves allow for easier pipe adjustments.
Slip Ball Valve vs. Compression Ball Valve: Compression ball valves require more intricate fittings for sealing, often involving compression nuts. Slip ball valves, however, use a simpler sliding mechanism to fit over pipe ends, making them more user-friendly for quick changes.
Common Industries and Applications
Slip ball valves are highly versatile and are used in a variety of industries where ease of installation, space constraints, or regular maintenance are key considerations. Some of the most common applications include:
Plumbing Systems: In residential and commercial plumbing, slip ball valves are used for water flow control, enabling quick repairs and adjustments without the need for pipe cutting or extensive rework.
HVAC Systems: Slip ball valves are often found in heating, ventilation, and air conditioning (HVAC) systems, where they help regulate water or gas flow in piping systems, especially in areas with limited space.
Industrial Systems: In manufacturing plants or chemical processing facilities, slip ball valves play a critical role in managing the flow of various fluids in machinery and piping systems. Their easy installation and maintenance make them ideal for industrial environments that require frequent adjustments or part replacements.
Materials Used in Slip Ball Valve Construction
Slip ball valves are made from various materials, each chosen based on the valve’s intended application and the type of fluid it will control:
Brass: Brass slip ball valves are commonly used for water systems, plumbing, and residential applications. They offer excellent corrosion resistance and are cost-effective for general-purpose use.
Stainless Steel: Stainless steel slip ball valves are used in industries requiring higher strength, corrosion resistance, and durability, such as chemical processing, oil and gas, and industrial systems. Stainless steel also helps handle higher pressure and temperatures.
PVC (Polyvinyl Chloride): For applications dealing with non-metallic fluids or corrosive substances, PVC slip ball valves are lightweight, resistant to corrosion, and ideal for water treatment systems or agricultural irrigation.
Sealing Mechanism and How It Affects Performance
The sealing mechanism in a slip ball valve is critical for maintaining leak-free operation. Here’s how it works:
Ball and Seat Seal: Inside the valve, the ball is sealed against the valve seat (the surface around the ball) when the valve is closed. The pressure from the fluid forces the ball into the seat, creating a tight seal that prevents leaks.
Stem Seal: The stem, which is the mechanism that turns the ball inside the valve, is also sealed to prevent leakage along the valve stem. In most slip ball valves, O-rings or packing materials are used for this purpose, ensuring that the valve operates efficiently without any leakage.
This dual-seal design (ball-to-seat and stem seal) contributes to the high-performance, leak-free operation of slip ball valves, making them reliable for fluid control.
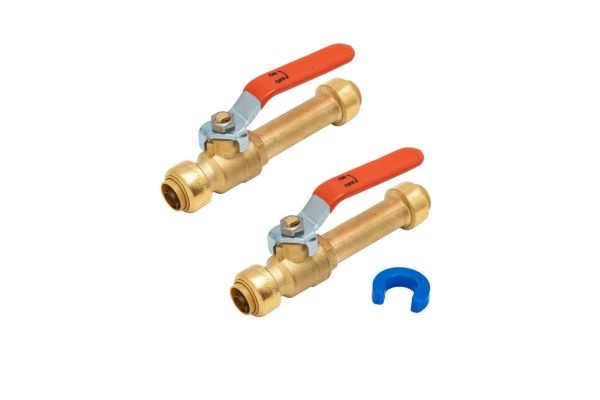
Internal Design
Ball: The ball is the central component of any ball valve, and in a slip ball valve, it’s typically made of durable materials like stainless steel, brass, or ceramic. The ball has a port (hole) in the center, which, when aligned with the pipe, allows fluid to flow. When turned 90 degrees, the port is closed, stopping the flow.
Stem: The stem connects the actuator (manual lever or motorized mechanism) to the ball. When the stem is turned, it rotates the ball inside the valve, either allowing or stopping the flow of the fluid. The slip feature in the valve design allows for easy adjustment or replacement without disassembling the entire system.
Valve Body: The body houses the internal components and is responsible for connecting the valve to the pipeline. The material of the valve body (brass, stainless steel, PVC) depends on the application requirements such as pressure tolerance, fluid type, and environmental factors.
Other Critical Components:
Seat: A sealing surface that ensures tight closure when the ball is in the “off” position.
Handle/Actuator: Used to manually or automatically rotate the stem and ball to control fluid flow.
End Connections: These could be threaded, flanged, or push-fit, depending on the specific slip ball valve design, allowing for quick installation and easy disconnection for maintenance.
How Does a Slip Ball Valve Work?
A slip ball valve operates similarly to other ball valves, with a ball inside the valve body that rotates to control the flow of liquid or gas. However, the unique “slip” feature sets it apart, making it easier to install and maintain. Here’s how it works:
Step-by-Step Explanation of the Ball Valve Mechanism
Valve Body and Ball: The valve consists of a spherical ball inside the valve body. This ball has a hole or port that aligns with the flow path when the valve is open. When the valve is closed, the ball rotates so that the hole is perpendicular to the flow, blocking the passage.
Actuation: A handle or actuator is attached to the ball. When you turn the handle, it rotates the ball inside the valve body. This action either opens or closes the valve, allowing or stopping the flow of fluids or gases through the system.
Sealing Mechanism: The slip ball valve features seals around the ball, which prevent leaks and ensure a tight shut-off when the valve is in the closed position. These seals can handle high pressures, making slip ball valves suitable for various applications.
The “Slip” Feature
The “slip” feature refers to the valve’s ability to slip over the pipe or fitting without requiring permanent attachment. This provides several benefits:
Ease of Installation: Unlike traditional ball valves that require threading or welding to secure them to pipes, the slip ball valve can simply be pushed onto the pipe or fitting, then secured in place with a collar, clamp, or other fastening mechanisms.
Quick Maintenance and Replacement: The slip feature allows for easy removal of the valve without disturbing the surrounding piping system. This is particularly beneficial for maintenance or replacement in confined spaces or systems where downtime must be minimized.
Versatility: Slip ball valves can be used in various systems where traditional ball valves may not be practical due to space or accessibility constraints.
Slip Ball Valve Installation: A Step-by-Step Guide
Installing a slip ball valve is a straightforward process, but it requires the right tools and a bit of attention to detail to ensure optimal performance.
Tools and Equipment Needed for Installation
Before beginning, gather the following tools and materials:
Slip ball valve (of the correct size and material)
Pipe wrench or adjustable wrench
Teflon tape or pipe sealant
Pipe cutters (if cutting pipes is necessary)
Lubricant (for smoother valve operation)
Safety gloves and goggles (for protection during installation)
Pre-Installation Checklist
Check Valve Compatibility: Ensure that the slip ball valve is compatible with the pipe material and size in your system. Double-check the type (e.g., brass, PVC, stainless steel) and size (e.g., 1/2″, 3/4″, 1″) to match your setup.
Inspect the Valve: Check the valve for any damage or defects before installation. Make sure the ball moves smoothly and that the valve is free of obstructions.
Ensure Proper Pressure Ratings: Verify that the slip ball valve’s pressure rating matches or exceeds the pressure of your system.
Clean the Pipes: Ensure the pipes are clean and free from debris or old sealant to create a tight, leak-free connection.
Detailed Installation Process
Prepare the Pipes: Cut the pipes to the correct length if necessary, and clean the pipe ends to remove any burrs or debris. This ensures a smooth connection.
Apply Teflon Tape or Pipe Sealant: Wrap Teflon tape around the male threads of the pipe (if applicable), or apply a pipe sealant to ensure a secure, leak-proof connection.
Align and Slide the Valve: Position the slip ball valve over the pipe fitting. The valve should be easily slid onto the pipe without needing to disassemble the system. Align the valve and pipe ends so they fit snugly.
Tighten the Fittings: Use a wrench to tighten the valve in place, ensuring a secure connection. Avoid overtightening, as this could damage the valve or pipe threads.
Test for Leaks: After installation, slowly turn the system on and check the valve and pipe connections for leaks. Tighten any connections as needed.
Check Valve Operation: Rotate the valve handle to ensure the ball moves freely and controls the flow properly.
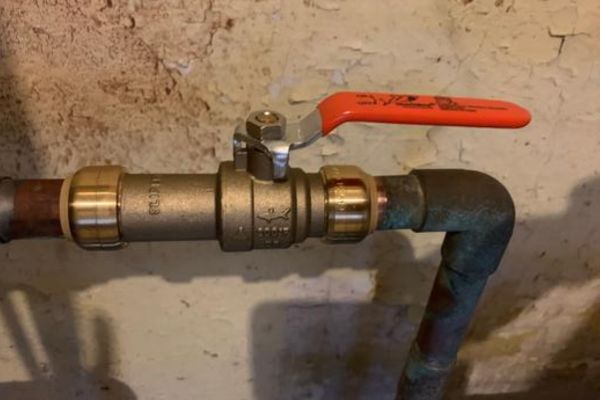
Common Mistakes to Avoid During Installation
Overtightening: Applying too much force while tightening the valve can lead to cracked fittings or damage to the valve body. Always follow the manufacturer’s recommendations for torque.
Using Incorrect Sealant: Using the wrong type of pipe sealant or Teflon tape can lead to leaks. Make sure you use the appropriate materials for the valve type and fluid being controlled.
Ignoring Compatibility: Not checking the compatibility of the valve with the system can lead to performance issues or even failure. Double-check the material and size specifications.
Skipping Leak Testing: Failing to test for leaks after installation can result in undetected issues that could lead to bigger problems down the road. Always conduct a leak test.
Slip Ball Valve vs. Other Types of Valves
When it comes to fluid control, choosing the right valve is essential to ensure efficiency, safety, and longevity in your systems. While slip ball valves are highly versatile, other valve types like gate valves, globe valves, and check valves might also be suitable depending on the application. In this section, we’ll compare slip ball valves to these other popular valve types, exploring their advantages and disadvantages.
Comparing Slip Ball Valves to Other Valve Types
Slip Ball Valve vs Gate Valve
Gate Valves are primarily used for on/off control and are ideal for applications where a full, uninterrupted flow is needed. However, they are typically slower to operate and don’t offer precise control over flow like a ball valve.
Pros of Slip Ball Valves:
Fast, reliable flow control with a simple quarter-turn operation.
Suitable for applications where quick shut-off is necessary.
Compact design that makes installation easier in confined spaces.
Cons of Gate Valves:
Slow to open/close, which can be less efficient.
Not ideal for precise flow control.
Bulkier design can make installation in tight spaces challenging.
Slip Ball Valve vs Globe Valve
Globe Valves are designed for throttling applications where flow needs to be regulated and adjusted continuously. They are better suited for precise flow control but are more complex and typically more expensive.
Pros of Slip Ball Valves:
Easier to install and maintain with its “slip” feature.
Ideal for quick on/off control, rather than throttling.
Typically less expensive and more durable for general use.
Cons of Globe Valves:
More complex installation and maintenance.
Expensive and larger in size compared to slip ball valves.
Not ideal for quick shut-off or high-flow systems.
Slip Ball Valve vs Check Valve
Check Valves are designed to prevent backflow in a system and are not used for regulating or stopping flow. They automatically open when the flow direction is correct and close when it reverses.
Pros of Slip Ball Valves:
Actively control flow direction, unlike check valves, which only prevent backflow.
Better suited for applications requiring flow regulation.
Cons of Check Valves:
Not suitable for applications needing controlled flow shut-off.
Only useful for preventing reverse flow, not for on/off control.
How to Choose the Right Valve for Your Needs
Choosing the right valve depends on several factors:
Application Type:
If you need quick, reliable on/off flow control, a slip ball valve is likely the best choice.
If precise flow regulation is required, consider a globe valve.
For systems that need to prevent backflow, a check valve is essential.
Installation and Maintenance Considerations:
For easy installation and minimal maintenance, slip ball valves stand out due to their simple design and “slip” functionality.
If space is tight, a slip ball valve’s compact size can be a significant advantage over larger valve types like gate or globe valves.
System Requirements:
For high-pressure systems, ensure that the valve you choose can handle the necessary load. While slip ball valves are durable, some high-temperature or high-pressure systems may require more specialized valves.
Conclusion
When selecting a slide valve, consider the material, pressure rating, and specific needs of your system. Be sure to select a valve that matches the size, fluid type, and environmental conditions of your application. Proper installation and regular maintenance are key to ensuring long-term performance. If you are unsure which valve is best suited to your needs, consult Topa and we can guide you in selecting the right product for your system requirements.
FAQ
What is a slip ball valve?
A slip ball valve is a type of valve used to control fluid flow, featuring a “slip” design that allows for easy installation and maintenance without needing to remove the entire valve.
How does a slip ball valve differ from a regular ball valve?
The main difference is the “slip” feature, which enables quicker installation and disconnection, making it ideal for tight or hard-to-reach spaces.
Where are slip ball valves commonly used?
Slip ball valves are widely used in plumbing, HVAC systems, industrial processes, and fluid control applications where ease of installation and leak-proof performance are critical.
What materials are slip ball valves made from?
Slip ball valves are commonly made from brass, stainless steel, or PVC, depending on the application and the type of fluid being controlled.
Can I install a slip ball valve myself?
Yes, installation is relatively straightforward, but it’s important to ensure compatibility with your system and follow proper steps to avoid leaks or other issues.
How can I maintain my slip ball valve?
Regularly check for leaks, inspect the valve and seals, and clean any debris from the valve’s moving parts to ensure smooth operation and long-lasting performance.