Among the many types of valves available, ball valves and needle valves are two common options, each offering unique benefits for controlling flow. Ball valves are widely used for on/off control, providing a simple yet effective mechanism for quickly stopping or allowing fluid flow. In contrast, needle valves are engineered for fine control, offering precise flow regulation, especially in systems where incremental adjustments are necessary.
Understanding Ball Valves
Structure and Functionality
Ball valves are widely recognized for their simple yet robust design, making them one of the most popular types of valves used in fluid control systems. The central component of a ball valve is a spherical ball that has a hole or bore, through its center. This ball is positioned between two seats, and the flow of fluid through the valve is controlled by rotating the ball.
The operation of a ball valve is straightforward. By turning the valve handle 90 degrees, the ball rotates within the valve body, aligning the bore with the pipeline to allow full flow or misaligning it to block the flow completely. When the bore is fully aligned with the piping, the valve is open, and fluid flows freely through the system. In contrast, when the ball is rotated so that the bore is perpendicular to the flow path, the valve is closed, preventing any fluid from passing through.
This 90-degree turn operation allows for quick and decisive control over fluid flow. Due to this design, ball valves offer either a fully open or fully closed position, meaning they are typically used for applications requiring rapid shutoff and not for throttling or flow modulation.
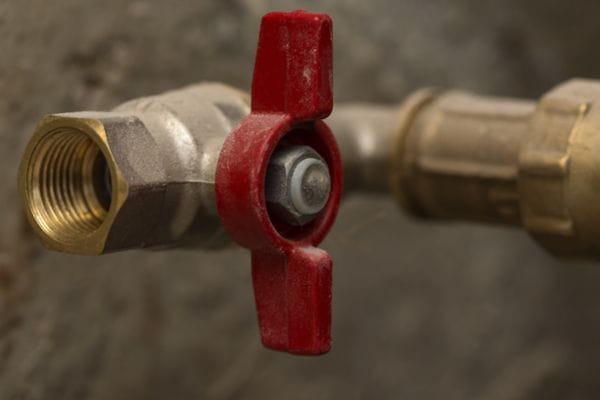
Advantages of Ball Valves
High Durability and Reliability
Ball valves are known for their durability, making them ideal for applications where repeated cycling (opening and closing) is required. The design provides a tight seal even after extended periods of non-use, reducing the risk of leaks. Additionally, the simple internal mechanism results in fewer parts that can wear out, contributing to their longevity and reliability.
Quick On/Off Operation
The 90-degree turn required to operate a ball valve allows for rapid opening or closing, making them perfect for applications where fluid needs to be stopped or started quickly. This swift action is especially beneficial in emergencies, where an immediate shutoff is necessary to prevent damage or hazardous leaks.
Minimal Pressure Drop When Fully Open
When a ball valve is fully open, the fluid flows through the bore with little resistance. The smooth interior surface and the fact that the bore is typically the same size as the pipe (known as full-bore design) mean that there is minimal pressure drop across the valve. This feature is particularly advantageous in systems where maintaining consistent pressure and flow rates is critical.
Disadvantages of Ball Valves
Not Suitable for Fine-Tuned Flow Control
While ball valves excel at providing on/off control, they are not suitable for applications that require precise flow regulation. The design of the valve does not allow for fine adjustments to the flow rate, and partial opening can cause turbulence within the valve, leading to potential inefficiencies and pressure fluctuations.
Potential Wear and Tear in Throttling Applications
Although ball valves can technically be used for throttling (partial opening to regulate flow), they are not designed for this purpose. Over time, using a ball valve for throttling can lead to erosion of the seats and ball, resulting in leaks and reduced performance. For long-term use, a different valve type, such as a globe or needle valve, is recommended for throttling applications.
Common Applications of Ball Valves
Ball valves are highly versatile and can be found in a wide range of industries due to their reliability and fast operation. Some of the most common industries and applications where ball valves are used include:
Oil and Gas Industry
In oil and gas operations, ball valves are commonly used for the transport of hydrocarbons. Their ability to handle high-pressure environments and the need for quick shutoff makes them ideal for critical pipeline applications. For example, they are often installed in emergency shutoff systems to prevent the release of hazardous materials.
HVAC Systems
Ball valves are a staple in heating, ventilation, and air conditioning (HVAC) systems, where they control the flow of water or refrigerants. Their quick operation ensures that fluid can be diverted or shut off in the event of a malfunction, protecting the system from damage.
Water Treatment Facilities
In water treatment plants, ball valves control the flow of water in various stages of the purification process. Their corrosion resistance, combined with low maintenance requirements, makes them a cost-effective choice for these long-term, critical operations.
Chemical Processing
Ball valves are frequently used in chemical plants where they control the flow of aggressive chemicals. Their durable materials (such as stainless steel or brass) ensure that they can withstand exposure to corrosive fluids without significant wear or leaks.
Understanding Needle Valves
Structure and Functionality
Needle valves are specifically designed for applications requiring precise flow regulation. The defining feature of a needle valve is its long, tapered needle-like plunger, which moves in and out of a precision seat. This needle is connected to the valve stem, and as it is gradually turned, the needle moves incrementally, either opening or restricting the fluid flow through a small orifice.
The needle valve’s design allows for fine control over flow rates, making it ideal for throttling applications where adjustments must be small and gradual. Unlike ball valves, which provide either full flow or full shutoff with a simple 90-degree turn, needle valves can easily control the fluid flow. This control is achieved through the close fitting between the needle and the seat, which enables the valve to modulate the flow in tiny increments.
The slow, deliberate movement of the needle into or out of the seat offers excellent control over fluid volume, making needle valves particularly suited for low-flow situations where precision is critical.
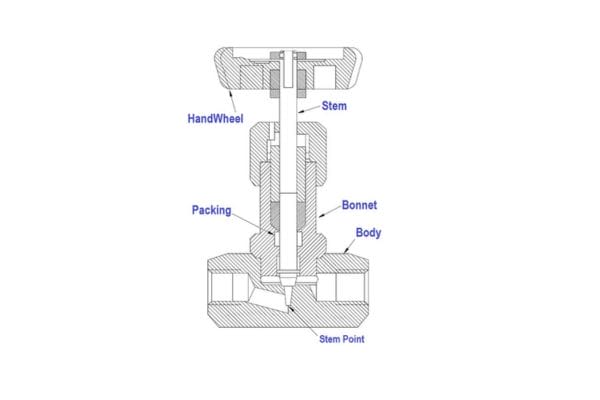
Advantages of Needle Valves
Exceptional Precision for Accurate Flow Regulation
One of the primary advantages of a needle valve is its ability to offer highly precise control over fluid flow. The long, tapered needle allows for incremental adjustments, making it possible to fine-tune the flow to exact specifications. This level of precision is essential in applications where even small fluctuations in flow rate can affect the overall performance of a system.
Suitable for Low-Flow or High-Precision Applications
Needle valves excel in low-flow applications, such as those found in laboratory experiments, where accuracy and control are more important than high-flow rates. Additionally, their precision makes them suitable for systems where slight changes in flow can significantly impact the process, such as in chemical mixing, where different substances must be combined in exact proportions.
Capable of Handling Delicate Tasks Where Fine Control Is Essential
The ability to make tiny adjustments to the flow rate allows needle valves to handle delicate tasks in industries such as instrumentation and fluid sampling. For example, in systems that measure and monitor fluid levels or pressure, precise control over the flow is necessary to ensure accurate readings and prevent damage to sensitive equipment.
Disadvantages of Needle Valves
Slower Operation Compared to Ball Valves
While needle valves are excellent for precise control, their operation is much slower than that of ball valves. Adjusting the flow with a needle valve requires turning the valve multiple times to make fine adjustments, which can be time-consuming in situations where a quick shutoff or rapid changes in flow are necessary.
Not Suitable for High-Flow or Rapid Shutoff Scenarios
Needle valves are designed for low-flow applications, and their design limits the amount of fluid that can pass through the orifice at any given time. This makes them unsuitable for high-flow systems, where large volumes of fluid need to be controlled or shut off quickly. In addition, needle valves are not typically used in emergencies where immediate shutoff is required, as their slow operation can be a drawback.
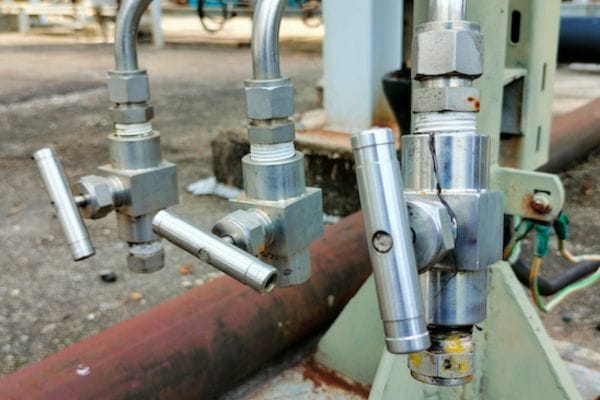
Common Applications of Needle Valves
Needle valves are commonly used in industries where precision and control over fluid flow are paramount. Some of the key industries and applications that rely on needle valves include:
Chemical Processing
In chemical processing plants, needle valves are often used to control the flow of chemicals into reactors or mixing vessels. Because even small deviations in flow can affect the outcome of a chemical reaction, the precision offered by needle valves is essential for maintaining consistency and safety in the process.
Laboratories
In laboratory settings, needle valves are frequently used to regulate the flow of gases or liquids in experiments that require exact measurements and careful control. For example, in chromatography, a technique used for separating chemical substances, needle valves are used to ensure that the flow of carrier gas or liquid is precise, ensuring accurate results.
Instrumentation and Fluid Sampling
Needle valves are a critical component in systems that measure and control fluid levels, pressures, and flow rates. In instrumentation systems, they provide the fine adjustments needed to maintain accurate readings. Similarly, in fluid sampling applications, needle valves control the flow of small amounts of fluid into a sample container, ensuring that the sample is representative of the larger system.
Hydraulic Systems
While less common in high-flow hydraulic systems, needle valves are sometimes used in hydraulic applications where fine control over fluid pressure is required. For instance, they can be used in hydraulic pressure testing systems to slowly increase or decrease pressure, preventing sudden spikes that could damage equipment.
Ball Valves vs Needle Valves: Key Differences
Flow Control
Ball Valves: Ball valves are optimized for applications where quick on/off control is required. Their design ensures full, unrestricted flow when the valve is open, making them ideal for applications requiring fast fluid control.
Needle Valves: Needle valves, on the other hand, are designed for throttling and precise flow adjustments. They allow for fine control of the fluid flow by gradually moving the tapered needle into or out of the seat. This level of control is vital in applications where small variations in flow can impact the overall process.
Operation Speed
Ball Valves: Ball valves offer a fast, efficient mechanism for opening and closing with a simple 90-degree turn. This makes them perfect for situations where rapid response is required, such as emergency shutoffs.
Needle Valves: Needle valves operate more slowly, as the gradual turning of the valve stem adjusts the needle’s position within the seat. This deliberate adjustment is necessary for achieving precision, but it makes needle valves unsuitable for applications where fast shutoff is needed.
Durability and Maintenance
Ball Valves: Known for their durability, ball valves require minimal maintenance and have a long lifespan, especially in high-pressure environments. Their simple design minimizes wear and tear, making them a cost-effective choice for many industries.
Needle Valves: Needle valves, with their intricate design, are more delicate and require regular maintenance to ensure accuracy. The fine components are more prone to wear and may need more frequent replacements, particularly in systems with corrosive or abrasive fluids.
Pressure and Flow Rate Handling
Ball Valves: Ball valves are better suited for high-pressure, high-flow applications where large volumes of fluid must be controlled quickly. Their full-bore design ensures that there is minimal pressure drop when the valve is fully open.
Needle Valves: Needle valves perform best in low-pressure, low-flow situations where precise control over small volumes of fluid is essential. They are not designed for high-flow scenarios, as the narrow orifice limits the volume of fluid that can pass through.
Flow Control Efficiency: A Comparative Analysis
Efficiency of Ball Valves
Ball valves are known for their efficiency in systems where fluid flow needs to be controlled quickly and with minimal resistance. One of the primary advantages of ball valves is their simple and effective design. The spherical ball inside the valve has a bore, and when fully open, the bore is aligned with the piping system, allowing fluid to flow through the valve with very little resistance. This unobstructed flow path is particularly advantageous in high-flow systems where maintaining consistent flow rates with minimal pressure loss is critical.
The smooth interior surface of a ball valve, combined with the full-bore design (where the diameter of the bore matches the pipe diameter), ensures that the fluid passes through the valve without being disrupted by internal components. As a result, ball valves offer almost no resistance when fully open, contributing to their high efficiency in fluid transport. This is especially important in systems that deal with high volumes of fluid, such as oil and gas pipelines, water treatment facilities, and HVAC systems.
In industries like oil and gas, quick flow control is crucial to ensuring operational safety and efficiency. Ball valves excel in these environments because they allow operators to stop or start the flow of fluid almost instantaneously with a simple 90-degree turn. This capability reduces downtime and improves overall system efficiency. For example, in pipeline systems where the rapid shutdown of fluid is essential in emergencies, ball valves minimize the time it takes to stop the flow, preventing potential damage or hazardous situations.
Ball valves also help improve efficiency by reducing the energy required to pump fluids through a system. Since the valve offers minimal resistance when fully open, pumps do not have to work as hard to maintain the desired flow rate. This reduces energy consumption, which can lead to significant cost savings in large-scale industrial applications where energy efficiency is a priority.
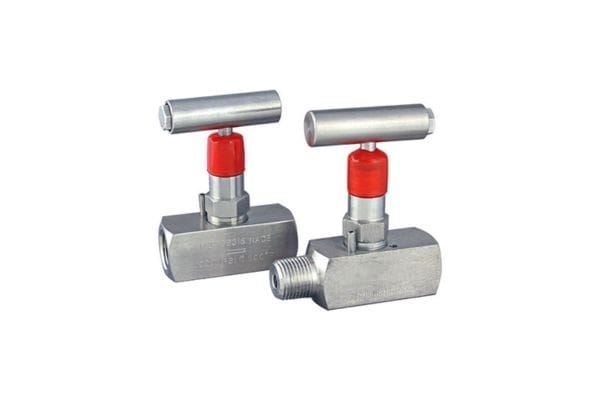
Efficiency of Needle Valves
While ball valves are favored for their quick operation and low resistance in high-flow systems, needle valves offer unmatched precision in flow control, which is vital in systems that require exact flow rates and pressure regulation. Needle valves are designed for applications where fine adjustments to fluid flow are necessary, and their incremental control mechanism ensures that even the smallest changes in flow can be achieved with accuracy.
In industries such as chemical processing, laboratories, and instrumentation systems, precision is key to maintaining the quality and consistency of operations. Needle valves allow operators to make fine-tuned adjustments to the flow, ensuring that the system operates within the required parameters. For example, in chemical mixing processes, maintaining the correct flow rate is crucial to achieving the right chemical composition. A needle valve’s ability to control flow with high precision ensures that the mixture remains stable and consistent, preventing costly errors or product waste.
The design of the needle valve allows for small, incremental adjustments to the flow of fluid. The tapered needle moves gradually into or out of the valve seat, regulating the flow with a high degree of accuracy. This is particularly beneficial in delicate processes, such as laboratory experiments, where even slight fluctuations in fluid volume can affect the outcome of the experiment. Needle valves are also commonly used in gas systems, where accurate control of gas flow is essential for maintaining pressure and avoiding leaks.
While needle valves operate more slowly than ball valves, this slower operation allows for greater control over the flow rate. This precision can improve system efficiency by ensuring that the correct amount of fluid is delivered to the process, minimizing waste and reducing the risk of system imbalances. Needle valves are also ideal for systems that require constant adjustments to maintain the desired flow, as their incremental control ensures smooth and steady flow rates.
Energy Consumption Considerations
When comparing the energy efficiency of ball valves and needle valves, it’s important to consider the specific requirements of the system. Both valve types offer energy-saving benefits, but their efficiency depends on the nature of the application.
Ball Valves: Ball valves are highly energy-efficient in high-flow systems where minimal resistance is needed to maintain the desired flow rate. Because the ball valve offers little to no obstruction when fully open, the system requires less energy to pump fluids through the valve, reducing overall energy consumption. This makes ball valves an excellent choice for systems where high-volume fluid transport is essential, such as in water distribution or oil pipelines. By minimizing resistance, ball valves help pumps operate more efficiently, which can lead to significant energy savings, especially in large-scale operations.
Needle Valves: Although needle valves are not typically used in high-flow applications, their precision makes them highly efficient in systems that require constant adjustments to maintain the desired flow rate. In applications where flow rates need to be controlled with great accuracy, such as chemical dosing or gas regulation, needle valves help ensure that the system operates efficiently without excessive energy waste. By providing fine control over the flow, needle valves prevent over-delivery or under-delivery of fluids, which can result in wasted energy as the system compensates for these fluctuations.
Conclusion
When selecting between ball and needle valves, the specific needs of the system should be taken into account: if fast on/off control and high flow efficiencies are a priority, then a ball valve may be a better choice. If precise incremental flow control is required, especially in low-flow applications, needle valves are the best choice. For more complex systems or unique applications, you may wish to consult a more specialized technician.
FAQ
What is the main difference between ball valves and needle valves?
Ball valves provide quick on/off control, while needle valves offer precise flow regulation with fine adjustments.
Which valve is better for high-flow systems?
Ball valves are better suited for high-flow systems due to their full-bore design and minimal resistance when fully open.
Can needle valves be used for fast shutoff?
No, needle valves are designed for precision, not speed, and are not ideal for rapid shutoff applications.
Are ball valves energy efficient?
Yes, ball valves are energy efficient in high-flow systems because they minimize resistance and reduce the energy needed to pump fluids.
When should I use a needle valve?
Use a needle valve when precise flow control is required, such as in chemical processing, laboratory experiments, or instrumentation.
Do ball valves require frequent maintenance?
No, ball valves generally require minimal maintenance due to their simple design and durable construction.