A hydraulic hose mandrel serves as the backbone of the hose production process. It is a cylindrical form around which the hose material is extruded and shaped, ensuring that the internal diameter of the hose is uniform and precise. The mandrel is integral in forming the hose’s structural integrity, maintaining its strength while allowing for flexibility.
What is a Hydraulic Hose Mandrel?
A hydraulic hose mandrel is a cylindrical form that serves as the foundation around which a hydraulic hose is formed during the manufacturing process. It acts as a mold or core around which the various layers of hose material — such as rubber, thermoplastic, or metal wire reinforcement — are applied. The primary function of the mandrel is to give the hose its internal shape and diameter while ensuring that it maintains the required structural integrity, flexibility, and performance characteristics once the hose is complete. The mandrel’s role is pivotal in ensuring that the hose meets the necessary specifications, including pressure resistance, bend radius, and overall durability for various industrial applications.
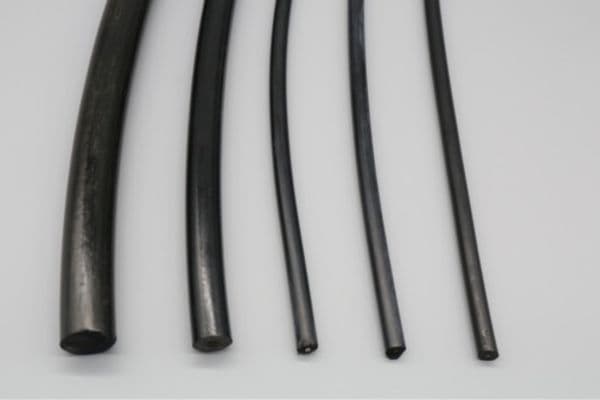
Types of Mandrels
There are two main types of hose mandrels, each serving a distinct purpose in hose production:
Solid Mandrels:
Solid mandrels are a solid, cylindrical piece typically made of steel or aluminum. They are used in the production of hoses that require greater internal pressure resistance and structural integrity. The solid mandrel is often used for hoses with thicker walls or those that need to handle high-pressure applications. The solid core helps ensure the hose retains its internal diameter as the layers of material are applied and the hose is cured, resulting in a durable and robust hose structure.
Hollow Mandrels:
Hollow mandrels, as the name suggests, have a hollow center and are commonly used in the production of hoses that require lighter weight or greater flexibility. These mandrels are ideal for creating hoses that need to bend more easily, such as flexible hydraulic hoses. The hollow design makes them more suited for hoses where the internal diameter must be kept consistent but the overall weight and flexibility of the hose are key considerations. Hollow mandrels are also used in situations where hoses are designed for low-pressure systems.
Basic Structure and Material
The structure and materials of a hose mandrel play a significant role in ensuring the hose is formed correctly and maintains its shape throughout the manufacturing process. Mandrels are generally cylindrical, smooth, and precisely shaped to meet the desired hose specifications.
Mandrel Material:
The materials used for mandrels are chosen based on their durability, corrosion resistance, and ability to withstand the heat and pressure during the hose extrusion process. Common materials include:
Steel: Steel mandrels are often used for their strength and durability. They are resistant to wear and tear and can withstand the high pressures involved in manufacturing high-performance hoses. Steel is a popular choice for solid mandrels.
Aluminum: Aluminum mandrels are lighter than steel and are typically used for hoses where weight is a critical factor. Aluminum is also resistant to corrosion, making it suitable for hoses exposed to harsh environments.
Rubber-Coated Mandrels: Some mandrels are coated with rubber to prevent damage to the hose during the manufacturing process. This rubber coating also helps to create a smooth internal surface for the finished hose, which can improve flow characteristics and reduce friction.
Mandrel’s Role in the Manufacturing Process
The mandrel is integral to the extrusion process of hydraulic hose production, ensuring that the hose takes the desired shape and size. Here’s how the mandrel functions in the manufacturing process:
Extrusion:
The hose material, typically a mixture of rubber or thermoplastic, is fed through an extruder, where it is heated and shaped around the mandrel. The mandrel provides the necessary form for the hose’s internal diameter, ensuring uniformity and consistency throughout the production process.
Layering:
As the hose material is extruded, multiple layers may be added, such as reinforcement layers made of steel wires or braided metal. These layers are designed to provide additional strength and pressure resistance to the hose. The mandrel holds the layers in place and helps to ensure that the hose maintains its shape and uniform thickness.
Curing:
Once the hose is formed around the mandrel, the entire assembly is moved to a curing oven where it is heated to the required temperature. This curing process solidifies the rubber or thermoplastic material, bonding the layers together and setting the hose’s final shape. The mandrel continues to play a role here by preventing the hose from deforming during the curing process.
Removal:
After curing, the hose is cooled, and the mandrel is removed. In some cases, the mandrel is removed immediately, while in other cases, it may be designed to stay inside the hose, serving as an inner layer. This depends on the specific requirements of the hose and its intended application.
The Importance of the Mandrel in Hydraulic Hose Production
Ensuring Consistent Quality
One of the primary functions of the hose mandrel is to ensure uniformity in wall thickness and maintain consistency in hose quality. When manufacturing hydraulic hoses, achieving a precise and uniform internal diameter is crucial. The mandrel acts as the internal form around which the hose is built, ensuring that the wall thickness is consistent throughout the length of the hose. This uniformity is important for several reasons:
Pressure Resistance: The uniform wall thickness is directly related to the pressure rating of the hose. If the wall thickness varies, it can lead to weak points where the hose is more likely to fail under pressure. The mandrel ensures that the hose has consistent pressure tolerance across its entire length.
Performance Consistency: In hydraulic systems, reliability is key. A hose with inconsistent wall thickness might perform poorly or even fail in the field, leading to downtime or accidents. The mandrel guarantees that each hose produced will meet stringent performance standards, especially in demanding, high-pressure applications.
Quality Control: By standardizing the shape and dimensions of the hose during production, the mandrel system serves as a critical tool for quality control. It ensures that each hose produced meets precise specifications, reducing the likelihood of defects and ensuring that the final product performs optimally in its intended application.
Impact on Flexibility and Durability
The design and material of the mandrel have a significant impact on the flexibility, pressure tolerance, and durability of the finished hydraulic hose. These factors are essential for the hose’s performance in dynamic, high-pressure environments.
Flexibility:
Hydraulic hoses are often required to flex and bend in various directions without kinking or losing their shape. The type of mandrel used during manufacturing — solid or hollow — influences the final hose’s flexibility. Hollow mandrels are typically used when flexibility is a top priority, as they help create hoses that are lightweight and easy to maneuver. The flexibility of the hose is essential in applications where it needs to move with machinery or equipment, such as in construction or agricultural settings.
Pressure Tolerance:
Hydraulic hoses are often used in systems that involve high-pressure fluid transfer. The mandrel plays a critical role in determining the pressure tolerance of the hose. By shaping the hose accurately and uniformly, the mandrel ensures that the hose can withstand the pressure forces without collapsing or rupturing. Solid mandrels, due to their structural integrity, are often used when creating hoses for high-pressure systems.
Durability:
The durability of a hydraulic hose is largely dictated by the materials and construction used during manufacturing. The mandrel helps maintain the structural integrity of the hose throughout the production process. For example, if a hose needs to withstand extreme weather conditions, abrasive materials, or high temperatures, the mandrel will ensure the hose is formed with the appropriate materials and structure to provide durability. Additionally, the rubber-coated mandrels prevent damage to the hose during the manufacturing process and ensure a smooth internal surface, which enhances the hose’s ability to withstand wear and tear over time.
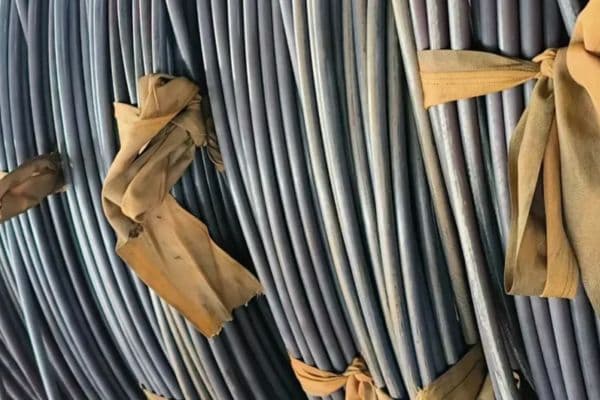
Customization and Precision
The hose mandrel plays a vital role in the customization and precision required in many hydraulic applications. Often, hydraulic systems require hoses with unique dimensions, configurations, or performance characteristics that are tailored to a specific machine or operating environment.
Custom Sizes and Shapes: Hydraulic hoses may need to be produced in non-standard sizes or configurations. Mandrels are essential for ensuring these custom hoses are formed correctly and precisely, adhering to specific internal diameters and wall thicknesses. For instance, a mandrel might be used to produce hoses that need to fit into tight spaces or specific connectors. Custom mandrels can also be designed to produce hoses with non-circular cross-sections or complex internal profiles.
Specialized Applications: Some applications may require hoses that can operate in extreme conditions, such as high-pressure environments, fluctuating temperatures, or exposure to corrosive fluids. Mandrels can be customized to produce hoses with specific performance characteristics, such as enhanced flexibility, abrasion resistance, or chemical compatibility. For example, a high-temperature mandrel can help produce hoses that can withstand elevated temperatures, while abrasion-resistant mandrels can ensure that the hose can endure harsh environmental conditions.
Precision Manufacturing: Hydraulic hose production requires highly precise manufacturing to ensure the hose meets rigorous industry standards. The mandrel’s ability to maintain uniformity and accuracy in dimensions is crucial for ensuring precision in every hose produced. This precision is vital not only for performance but also for safety, as poorly made hoses can lead to leaks, ruptures, and system failures.
Common Issues with Hose Mandrels
Mandrel Wear and Tear
Like any component in hydraulic hose production, mandrels experience wear and tear over time, especially with frequent use in high-pressure environments. These stresses can lead to several issues that impact their performance and the quality of the hoses produced.
Surface Damage: Continuous contact with the hose material, high extrusion temperatures, and mechanical stress can cause abrasions or scratches on the mandrel’s surface. Over time, this damage can affect the smoothness of the hose’s interior, resulting in uneven internal diameters, which can negatively affect fluid flow.
Material Degradation: Frequent use in extreme conditions can degrade the mandrel material, especially for those made of aluminum or composite materials. This can reduce the mandrel’s strength and resilience, making it more susceptible to bending or breaking under pressure.
Loss of Structural Integrity: For solid mandrels, repetitive use can cause the material to fatigue, weakening its overall structural integrity. For hollow mandrels, pressure buildup during the hose manufacturing process may lead to deformation, making them less effective at creating the desired hose shape.
Inaccuracies in Hose Formation
If a mandrel is damaged or out of alignment, it can lead to significant inaccuracies in the hose formation, ultimately resulting in defective hoses. Common issues include:
Non-uniform Wall Thickness: If the mandrel is bent, scratched, or misaligned, it can cause variations in the hose’s wall thickness. This inconsistency can affect the pressure tolerance and durability of the hose, potentially causing it to fail under pressure.
Internal Deformities: If a mandrel has lost its shape or alignment, it may not support the hose evenly during production, leading to internal defects such as indentations or narrow sections within the hose. These defects can result in flow restriction, affecting the efficiency of the hydraulic system.
Poor Hose Flexibility: Inaccurate mandrel alignment or wear can also influence the hose’s flexibility. A damaged or improperly aligned mandrel can prevent the hose from being properly formed, leading to stiffness and reduced bending capacity. This can impact performance in systems that require hoses to flex or move regularly.
Cleaning and Maintenance
Regular cleaning and maintenance are essential for keeping mandrels in optimal working condition, ensuring consistent hose production quality, and preventing common issues like wear and inaccuracies. Here are some essential maintenance tips:
Regular Inspection: Mandrels should be routinely inspected for signs of damage, such as cracks, dents, or surface wear. Regular checks will help identify issues early before they impact hose production. The inspection should also assess alignment, ensuring that the mandrel is straight and level to avoid inaccuracies in hose formation.
Cleaning: Mandrels should be thoroughly cleaned after each use to remove any buildup of residue, such as rubber, grease, or debris. Solvents and soft brushes are commonly used for cleaning. For more stubborn residues, abrasive pads or cleaners can be used, but care should be taken to avoid damaging the mandrel’s surface.
Lubrication: Proper lubrication can reduce friction during the extrusion process, helping prevent abrasions and ensuring the mandrel remains smooth. A light coating of lubricant can be applied to the mandrel before each use.
Conclusion
Choosing the correct hose mandrel is not just about creating a durable and flexible hose; it’s also about enhancing the efficiency, safety, and cost-effectiveness of the entire hydraulic system. The right mandrel ensures that the hoses meet the specific demands of the application, providing the strength to handle pressure while maintaining flexibility and reliability over time. If you need suitable hydraulic hoses, just contact us!
FAQ
What is a hose mandrel?
A hose mandrel is a cylindrical form used in the manufacturing process of hydraulic hoses to shape the hose and maintain its internal diameter and structural integrity during production.
What are the different types of hose mandrels?
The three main types of hose mandrels are solid mandrels, hollow mandrels, and flexible mandrels. Each type serves a specific purpose, such as creating thicker, high-pressure hoses or flexible hoses for dynamic applications.
How does a mandrel affect hydraulic hose performance?
The mandrel plays a critical role in ensuring uniform wall thickness, strength, and flexibility, all of which are essential for the hose to perform well under pressure, resist wear, and maintain fluid flow.
What materials are hose mandrels made from?
Mandrels can be made from various materials, including steel, aluminum, rubber-coated materials, and composites. The choice of material depends on the desired hose properties such as weight, strength, and corrosion resistance.
How do I maintain a hose mandrel?
To maintain a mandrel, regularly inspect it for damage, clean it after each use, lubricate it to reduce friction, and store it properly to avoid wear and corrosion.
What happens if the mandrel is damaged during production?
If the mandrel is damaged, it can lead to inaccuracies in hose formation, such as uneven wall thickness, internal defects, or reduced flexibility, which can compromise the hose’s performance and safety in hydraulic systems.