Metal hoses are designed to transport fluids and gases in environments where flexibility, pressure resistance, and durability are paramount. Inaccurate measurements can lead to improper fitting, increased wear and tear, or even catastrophic failures, which can pose safety risks and lead to costly downtime in operations.
Understanding Metal Hose Assemblies
A. Definition of Metal Hose Assemblies
Flexible metal hose assemblies consist of flexible metal hoses combined with end fittings that enable them to connect to piping systems or equipment. These assemblies are engineered to transport a variety of fluids and gases, providing flexibility and resilience in challenging environments. Unlike rigid piping, metal hoses can accommodate movement, thermal expansion, and vibrations, making them ideal for applications where conventional piping might fail. The design typically features a corrugated inner tube, which allows for bending and flexing while maintaining a high level of pressure resistance.
Metal hose assemblies are characterized by their ability to handle a wide range of temperatures and pressures, often exceeding those tolerated by other materials. They are essential components in systems requiring reliable performance under dynamic conditions, ensuring safe and efficient fluid transfer.
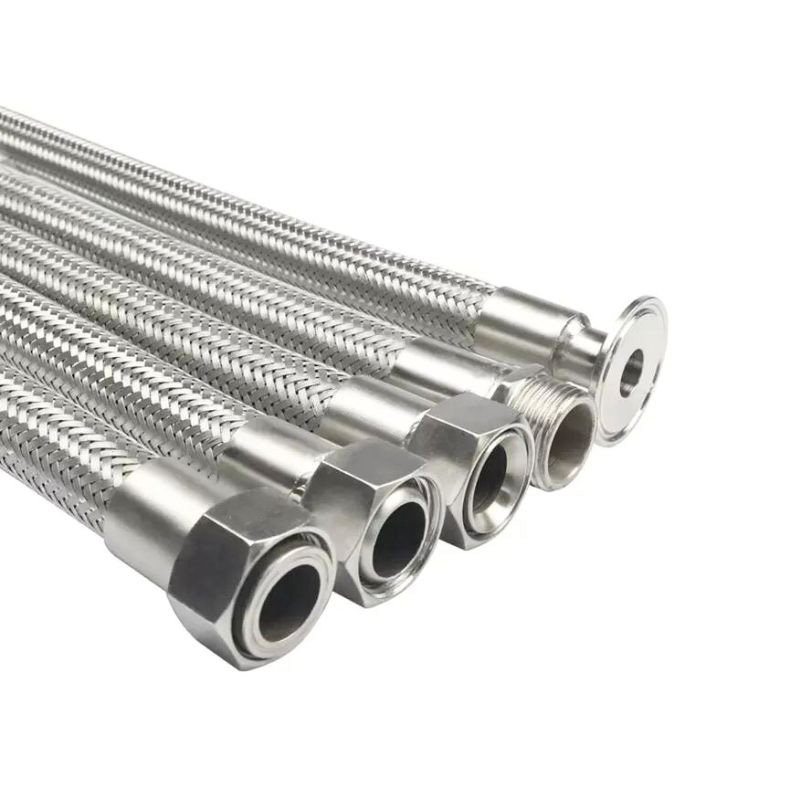
B. Common Materials Used in Metal Hoses
The choice of materials for metal hoses is critical to their performance and durability. The most commonly used materials include:
Stainless Steel: The most prevalent material, often used in grades 304 and 316. Stainless steel offers excellent corrosion resistance, strength, and high-temperature performance. Grade 316 is particularly suitable for more corrosive environments, such as those found in chemical processing.
Alloys: Various alloys may be used to enhance specific properties, such as increased strength or improved corrosion resistance. These are selected based on the operational requirements of the application.
Other Metals: In certain applications, other metals like brass or monel may be utilized, especially where specific chemical resistance is required. However, these materials are less common compared to stainless steel.
The selection of material affects not only the hose’s lifespan but also its suitability for specific applications, making it vital to choose the right material based on environmental conditions and the nature of the fluids being transported.
C. Overview of Various Applications and Environments
Metal hose assemblies are employed in a diverse range of applications across multiple industries due to their versatility and reliability. Some notable applications include:
Aerospace: In the aerospace sector, metal hoses are used for fuel lines, hydraulic systems, and air conditioning systems. The high flexibility and strength of metal hoses make them suitable for the dynamic environments of aircraft, where they must withstand extreme temperatures and pressures.
Chemical Processing: Metal hoses are essential in transporting corrosive chemicals safely. Their resistance to chemical reactions and their ability to handle high pressures make them ideal for use in reactors, storage tanks, and transfer lines.
Oil and Gas: In the oil and gas industry, metal hose assemblies are used in drilling operations, as well as for transporting hydrocarbons and other fluids. The ability to withstand high pressures and harsh environmental conditions is crucial in this field.
Food and Beverage: Metal hoses are employed in the food and beverage industry for transferring liquids and gases, ensuring that the materials used do not contaminate the products. Their easy-to-clean surfaces help maintain hygiene standards.
Pharmaceuticals: Similar to food and beverage applications, metal hoses in the pharmaceutical industry must meet strict regulatory standards. They are used for transferring liquids, gases, and powders in manufacturing processes while preventing contamination.
Manufacturing: Many manufacturing processes utilize metal hose assemblies for fluid transfer, cooling systems, and pneumatic applications. Their flexibility allows for easy integration into complex systems, enhancing operational efficiency.
Key Measurement Terminology
A. Live Length vs. Overall Length
When measuring metal hose assemblies, it’s essential to distinguish between “live length” and “overall length,” as these terms refer to different aspects of hose measurement.
Live Length: This is the length of the metal hose that is actively engaged in the flow of fluid or gas. It excludes any fittings or connections at both ends. The live length is crucial for understanding how much of the hose will experience pressure and movement during operation. Accurately measuring live length helps ensure that the hose can accommodate bends, thermal expansion, and other dynamic forces without compromising performance.
Overall Length: In contrast, overall length includes the entire length of the assembly, encompassing the fittings and any additional components. This measurement is important for determining how the assembly will fit into a specific installation or piping layout. Overall length is often used in system design and installation to ensure compatibility with existing infrastructure and to allow for proper connections.
Understanding the difference between these two measurements is vital for ensuring accurate hose selection and installation, as using the wrong measurement can lead to improper fit and potential failure in the assembly.
B. Fitting Types and Their Impact on Measurements
Fittings play a critical role in the functionality of metal hose assemblies and significantly impact measurement considerations. Different types of fittings can affect how the hose is measured and installed:
Welded Fittings: These are permanently attached to the hose and provide a secure connection. When measuring assemblies with welded fittings, it’s essential to include the length of the fittings in the overall length measurement but exclude them from the live length.
Threaded Fittings: These fittings can be easily installed and removed, making them versatile for different applications. When measuring hoses with threaded fittings, care should be taken to consider the length of the threads and how they may impact the overall length and fit in the system.
Flanged Fittings: Flanged fittings create a flat surface for bolting connections. When measuring for flanged fittings, both the flange thickness and the bolt hole dimensions need to be considered to ensure a proper fit.
Quick-Connect Fittings: These fittings allow for rapid connection and disconnection. Measuring assemblies with quick-connect fittings should take into account the fitting’s overall dimensions and how they affect installation space.
Understanding the specific type of fitting used is crucial for accurately measuring metal hose assemblies, as the fitting dimensions and installation methods can vary widely.
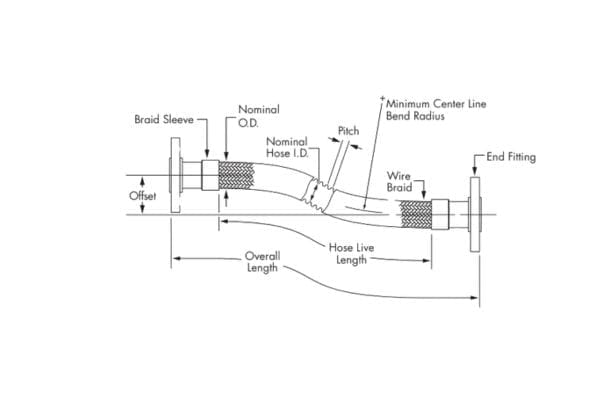
C. Additional Terms: Bend Radius, Assembly Length, and Straight Length
In addition to live length and overall length, several other key terms are important for accurately measuring and understanding metal hose assemblies:
Bend Radius: This term refers to the minimum radius that a hose can be bent without kinking or compromising its structural integrity. The bend radius is critical for maintaining flow characteristics and preventing damage during installation and operation. A tighter bend radius may lead to increased stress on the hose, potentially causing failure. Properly measuring and adhering to bend radius specifications is essential for ensuring the longevity and reliability of metal hose assemblies.
Assembly Length: This term encompasses the complete length of the metal hose assembly, including the fittings and any necessary attachments. Understanding assembly length is vital for planning installations and ensuring that hoses fit within the designated spaces without causing strain on connections.
Straight Length: Straight length refers to the portion of the hose that is completely linear without any bends or fittings. Measuring the straight length is important for determining how much hose is available for specific applications, especially in systems where direct routing is essential.
Step-by-Step Guide to Measuring Metal Hose Assemblies
A. Preparing for Measurement
Before diving into measurements, proper preparation is essential to ensure accuracy.
Ensuring the Assembly is Clean and Accessible:
Begin by thoroughly cleaning the metal hose assembly. Dirt, grime, or residue can obscure measurement points and lead to inaccuracies. Use appropriate cleaning agents that won’t damage the hose material.
Ensure the assembly is accessible, meaning it should be free from obstructions and positioned in a way that allows for straightforward measurement. If the assembly is installed, temporarily removing any coverings or supports may be necessary.
Identifying Measurement Points:
Determine the specific points on the hose assembly that require measurement. These typically include the ends of the hose, any bends, and the fittings.
Mark these points clearly with a non-permanent marker or tape to avoid confusion during the actual measuring process. This preparation step helps streamline the measuring procedure and minimizes the chances of errors.
B. Measuring Overall Length
Definition and Method:
Overall length is defined as the total length of the metal hose assembly, including all fittings and any other components.
To measure overall length, use a measuring tape to stretch from one end of the assembly to the other, ensuring that the tape follows the contours of the hose. Start at the end of the fitting or connector and measure to the end of the opposite fitting.
Tips for Accurate Measurement:
Ensure that the tape measure is straight and taut, without any sagging. A slack tape can result in inaccurate readings.
If the assembly includes bends, measure along the path the hose takes rather than in a straight line. This will provide a more accurate overall length.
Take multiple measurements if possible and average them to account for any discrepancies.
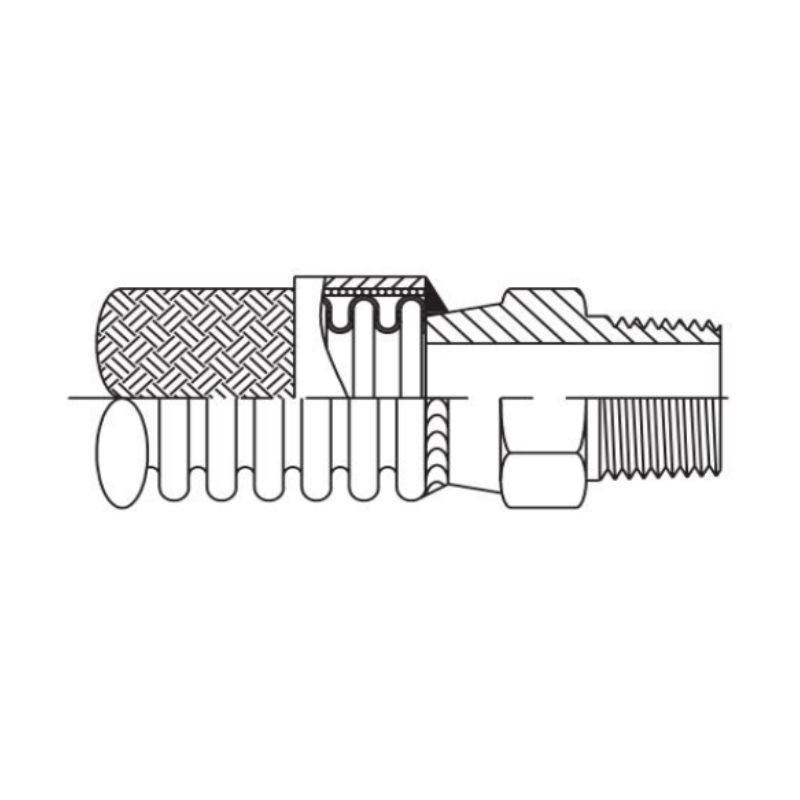
C. Measuring Live Length
Definition and Method:
Live length is the segment of the hose that is actively engaged in fluid or gas flow, excluding the fittings.
To measure live length, identify the points where the fittings connect to the hose. Measure from the end of one fitting to the end of the other fitting, ensuring that the tape does not include any part of the fittings themselves.
Tips for Accurate Measurement:
Similar to measuring overall length, ensure that the tape is taut and straight.
Pay special attention to the fitting ends, as they can sometimes obscure the true starting point of the hose.
Double-check the measurement by comparing it against the assembly’s specifications or previously recorded lengths.
D. Measuring for Fittings
Measuring Different Fitting Types (Welded, Threaded, Flanged):
Welded Fittings: Measure from the end of the hose to the end of the fitting. Since these are permanent, ensure the measurement is precise.
Threaded Fittings: Measure the length of the threads in addition to the hose length. The fitting’s total length should include the threads to ensure proper installation.
Flanged Fittings: For flanged fittings, measure from the edge of the flange, accounting for any additional dimensions necessary for bolting. This includes the thickness of the flange and the bolt-hole dimensions.
Importance of Fitting Type in Measurement:
Different fitting types can significantly impact the overall and live length measurements. Each fitting has unique dimensions that must be accounted for to ensure a secure and effective connection.
Understanding these dimensions will help prevent leaks and enhance the reliability of the hose assembly.
E. Special Considerations for Bends and Curves
Measuring Bend Radius:
The bend radius is the minimum radius at which a hose can be bent without kinking or damaging it. Measuring this correctly is crucial for ensuring that the assembly can operate without restrictions.
To measure bend radius, identify the centerline of the bend and measure from the centerline to the innermost edge of the bend. This can typically be done by measuring perpendicular to the curve.
Calculating Length Adjustments for Bends:
When a hose is bent, it doesn’t follow a straight line, which can affect the effective length of the hose. To calculate length adjustments for bends, consider the angle of the bend and the specified minimum bend radius.
Use the formula for calculating length adjustments based on the bend angle and radius. For example, if you have a 90-degree bend, you may need to add a certain length to accommodate the curve, depending on the specifics of the hose and its intended application.
Common Mistakes to Avoid
Measuring metal hose assemblies accurately is critical for ensuring their performance and reliability. However, several common mistakes can lead to measurement errors, resulting in improper installations and potential system failures.
A. Overlooking the Difference Between Live Length and Overall Length
One of the most significant mistakes is failing to distinguish between live length and overall length.
Impact of Confusion: Using overall length instead of live length can lead to incorrect fittings and connections, causing stress on the hose during operation. Conversely, measuring live length as overall length can result in hoses that are too short, which may lead to kinking or leaks.
Solution: Always clarify which measurement is needed for the specific application. It is advisable to mark the live and overall lengths during the measuring process to avoid confusion later on. Clear documentation can also help prevent misunderstandings in the future.
B. Incorrectly Measuring Fittings
Fittings are integral components of metal hose assemblies, and inaccurate measurements can lead to significant issues.
Common Errors: A frequent mistake is measuring only the hose length and neglecting to account for the dimensions of the fittings. For threaded or flanged fittings, omitting thread length or flange thickness can result in improper connections.
Solution: Ensure that you measure each fitting type accurately, including all relevant dimensions. When dealing with threaded fittings, include both the length of the threads and the hose length. For flanged fittings, remember to factor in the thickness and bolt hole dimensions.
C. Failing to Account for Thermal Expansion or Movement
Metal hoses can expand or contract based on temperature changes and operational movements, which can affect measurements.
Consequences: Ignoring thermal expansion can lead to hoses that are either too tight or too loose in the assembly, potentially causing leaks or damaging the hose over time. Movement from vibrations or machinery can also change the effective length of the hose.
Solution: Always consider the operational environment when measuring. Consult the manufacturer’s guidelines for allowable thermal expansion and movement allowances for specific hose materials. Additionally, it may be beneficial to incorporate flexibility in the installation to accommodate any potential movement.
D. Not Using the Right Tools
The tools used for measurement can greatly influence the accuracy of the results.
Common Tool Mistakes: Using inappropriate measuring devices, such as flexible tape measures for rigid or complex shapes, can lead to inaccurate readings. Moreover, failing to use precision measuring tools can result in a lack of accuracy in critical measurements.
Solution: Invest in high-quality measuring tools, such as calipers for small fittings and tape measures designed for metal hoses. Additionally, ensure that the tools are calibrated regularly for consistent accuracy. When measuring complex shapes or bends, consider using templates or specialized measuring devices designed for that purpose.
Conclusion
In conclusion, take the initiative to refine your measuring techniques and knowledge. The effort invested in understanding and applying proper measurement practices will pay dividends in the efficiency and safety of your hydraulic and fluid systems.
FAQ
What is the difference between live length and overall length in metal hose assemblies?
Live length refers to the portion of the hose actively involved in fluid flow, excluding fittings, while overall length includes the entire assembly with fittings.
How do I measure the bend radius of a metal hose?
Measure from the centerline of the bend to the innermost edge of the hose. This ensures you account for the minimum radius the hose can bend without kinking.
What tools are best for measuring metal hose assemblies?
High-quality measuring tapes, calipers for smaller fittings, and specialized measuring devices for bends and complex shapes are recommended for accurate measurements.
Why is it important to consider thermal expansion when measuring metal hoses?
Metal hoses can expand or contract with temperature changes, affecting their fit and performance. Ignoring this can lead to tight or loose installations, risking leaks or damage.
What should I do if I’m unsure about the measurements?
If uncertain, it’s best to consult the manufacturer’s guidelines or seek advice from experienced professionals in the field to ensure accurate measurements.
How can I avoid common measurement mistakes?
Double-check your measurements, ensure clarity on measurement points, use the right tools, and maintain awareness of fitting types to minimize errors.