How to Choose the Right Quick Coupling for Your Needs
Introduction
In a variety of industrial applications, choosing the right quick couplers is a critical decision that affects the efficiency, safety and overall performance of hydraulic and pneumatic systems. Therefore, it is important to fully understand the specific requirements of each industry, the environmental conditions in which the couplings will operate, and the compatibility with existing systems during the selection process. This article provides a comprehensive overview of how to select the right quick coupler for your industry needs by delving into technical aspects, industry-specific considerations and practical tips.
Understanding Quick Coupler
Quick couplers, fundamental in a range of industries, are mechanisms designed to connect and disconnect fluid lines swiftly and securely, without the need for intricate tools or procedures. Their primary function is to facilitate the easy and efficient management of fluid or air transfer in various systems, a task crucial in maintaining operational continuity and safety.
To expand on their definition, quick couplings are devices that provide a fast and convenient way to connect and disconnect hoses or pipes. They are typically used in situations where frequent changes of lines are necessary or where speed and flexibility are required. The basic functionality of these couplings lies in their ability to allow for immediate control of the flow of materials – be it liquid, gas, or air – thereby preventing leaks and maintaining the pressure integrity of the system.
Types of quick release couplings
The market for quick release couplings is diverse, with a range of types designed to meet specific needs and applications. Some of the common types include:
Threaded Couplings: Utilized in applications where a secure connection is essential, these couplings involve screwing two parts together to form a tight seal.
Push-to-Connect Couplings: Known for their ease of use, these couplings allow for a connection to be made by simply pushing the coupling components together.
Camlock Couplings: Widely used in industrial applications, these couplings use a camming or latching mechanism to securely lock the coupling halves.
Flat Face Couplings: Designed to prevent spillage and contamination, these are used in environments where cleanliness is paramount.
Ball and Sleeve Couplings: These couplings use a ball-locking mechanism inside a sleeve and are common in applications involving hydraulic systems.
Each type serves distinct purposes, factoring in the fluid type being transferred, the required pressure levels, and the environmental conditions of operation. For instance, materials used in manufacturing these couplings, such as stainless steel, brass, or plastic, are chosen based on their compatibility with the fluids, durability, and resistance to various factors like corrosion or UV exposure.
Understanding these quick couplers’ basic principles and the variety available is crucial in making an informed selection that aligns with specific industrial needs. This knowledge is not just a matter of operational efficiency but is fundamentally linked to ensuring safety and longevity in a range of mechanical and industrial applications.
Factors to Consider When Choosing Quick Connectors
When it comes to selecting the right quick coupler for any industrial application, several critical factors must be considered to ensure optimal performance and safety. Each aspect plays a pivotal role in determining the suitability of a quick release coupling for a specific purpose.
Material
The choice of material for quick connect hydraulic fittings is foundational to their performance and longevity. Materials commonly used include stainless steel, brass, and plastic. Stainless steel is prized for its strength and corrosion resistance, making it ideal for harsh environments. Brass is often chosen for its corrosion resistance and compatibility with a wide range of fluids. Plastic couplings are lightweight and economical, suitable for less demanding applications. The selection depends largely on the type of fluid being transferred, the ambient conditions, and the required durability.
Size and Compatibility
The size of the quick coupler must match the size of the hoses or pipes it is intended to connect. An improperly sized coupling can lead to leaks or a complete failure of the connection. Compatibility with the existing system is equally crucial. This includes not only physical dimensions but also the design standards and operational parameters of the system. A thorough understanding of the system’s requirements is necessary to choose a coupling that will integrate seamlessly.
Pressure Ratings
Quick release couplings must be able to withstand the operational pressures of the system. Each coupling is rated for a maximum operating pressure, and selecting a coupling that meets or exceeds the system’s requirements is essential. Failure to do so can result in dangerous situations, including the rupture of the coupling or the connected hose.
Environmental and Operational Conditions
The operating environment plays a significant role in the selection process. For applications exposed to extreme temperatures, corrosive substances, or UV radiation, couplings must be chosen that can withstand these conditions without degrading. Additionally, factors like vibration, pulsation, and the presence of abrasive materials in the fluid can influence the choice of coupling.
Taking these factors into account is imperative in choosing the right quick coupler. This careful consideration not only ensures the smooth operation of your system but also contributes to the safety and reliability of the entire operation.
Industry-Specific Requirements
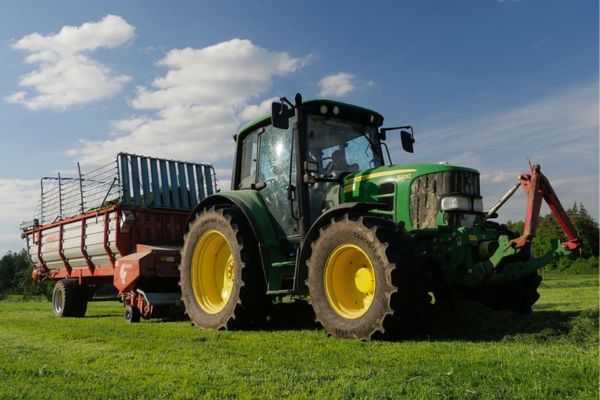
The selection of quick couplers is not uniform. Different industries have unique needs and environments, and therefore specific requirements for quick-release couplings. Understanding these requirements is essential to ensure that the quick connector selected is suitable and improves the efficiency and safety of your operations.
Different applications
For example, in Agriculture, couplings are often exposed to dirt, fertilizers, and varying weather conditions. Durability, corrosion, and wear resistance are key. In addition, ease of use is critical, as equipment may need to be quickly replaced or repaired in the field. Therefore, quick-disconnect hydraulic fittings used in irrigation systems must be robust, easy to handle, and resistant to environmental factors.
Moving to manufacturing, the focus shifts to precision and reliability. Here, quick-disconnect hydraulic fittings are used in a variety of applications, from pneumatic tools to hydraulic systems. The couplings must be able to withstand constant use, high pressures, and sometimes abrasive fluids. The requirement for minimal leakage and the ability to maintain a secure connection even in the presence of vibration and motion is paramount.
In the aerospace, the stakes are even higher. Couplings here are used in critical applications, such as fuel, hydraulic, and air systems of aircraft. They must adhere to stringent safety standards, handle extreme pressures and temperatures, and be lightweight yet durable. Aerospace quick connect hydraulic fittings often require custom designs and materials, like titanium or specialized alloys, to meet these demanding specifications.
Each of these industry examples highlights the diversity in the application and the necessity for specialized quick couplers. The selection process must consider the specific challenges and operational demands of the industry to ensure that the coupling not only fits but also contributes to the optimal functioning of the system.
The Role of Safety and Regulations
Role in Hydraulic Systems
In the selection of quick-disconnect hydraulic fittings, safety, and adherence to regulatory standards are paramount. The consequences of choosing a coupling that fails to meet safety requirements can be severe, ranging from equipment damage to serious workplace accidents. It is crucial to understand and comply with the safety standards and regulations that govern the use of quick connectors in various industries.
Safety standards for hydraulic quick disconnect fittings vary depending on the industry and the specific application. In general, these standards address issues such as the maximum pressure the coupling can handle, the materials that can be safely used based on the fluids being transferred, and the environmental conditions the coupling can withstand. For instance, couplings used in the oil and gas industry must adhere to standards that ensure they can handle the high pressures and potentially corrosive nature of the materials being transferred.
Regulatory compliance is another critical factor. Various international and national bodies set regulations for hydraulic quick disconnect fittings to ensure safety and reliability. In the United States, for example, the Occupational Safety and Health Administration (OSHA) sets guidelines for the safe use of quick hydraulic couplings, especially in hazardous work environments. Similarly, the International Organization for Standardization (ISO) provides standards that are widely adopted in many countries, ensuring a high level of safety and interoperability of components.
Practical steps
Ensuring safety in the workplace with the right coupling choice involves several practical steps:
– Regularly inspect couplings for signs of wear, corrosion, or damage.
– Train staff on the proper use and maintenance of quick couplers.
– Implement a maintenance schedule that includes routine checks and timely replacement of worn or damaged parts.
– Choose couplings with safety features such as secure locking mechanisms to prevent accidental disconnections.
In summary, knowing and complying with safety standards and regulations is not only a legal requirement, but also an essential practice for maintaining a safe working environment. Proper selection, use, and maintenance of quick-release couplings are critical.
Cost Considerations
Overview of Varieties
When it comes to selecting hydraulic quick disconnect fittings, cost considerations play a significant role. It’s a delicate balance between ensuring quality and managing expenses. This decision-making process involves understanding the long-term value of a coupling versus the immediate cost savings that might be achieved with a less expensive option.
How to choose
The first step in balancing quality and cost is to recognize that the cheapest option is not always the most cost-effective in the long run. Initial savings may be overshadowed by frequent replacements, maintenance costs, or even system failures. For example, a low-cost coupling might suffice for a light-duty application with minimal pressure requirements. However, in high-pressure systems or corrosive environments, investing in a higher-quality, more durable coupling is necessary to prevent leaks, breakdowns, and potential safety hazards.
In contrast, long-term investment in quality quick couplers can lead to substantial savings over time. High-quality couplings generally offer better performance, longer lifespan, and fewer maintenance issues, thereby reducing downtime and repair costs. This is especially true in industries where equipment reliability is crucial, and system failure can result in significant financial and operational setbacks.
It’s also important to consider the total cost of ownership, which includes the purchase price, installation costs, maintenance expenses, and the potential cost of system downtime due to coupling failure. A comprehensive cost analysis can provide a clearer picture of the long-term financial implications of the coupling choice.
Ultimately, the key is to find the best value – a coupling that meets the system’s requirements at a reasonable cost without compromising on quality and reliability. This approach ensures that the coupling serves its purpose effectively while aligning with budget constraints.
Common Mistakes to Avoid
Selecting and using hydraulic quick disconnect fittings may seem straightforward, but there are common pitfalls that can lead to inefficient operation, increased costs, or even safety hazards. Being aware of these frequent errors can help in making more informed decisions and ensuring the optimal use of quick couplings.
Selecting the wrong material
One common mistake is selecting the wrong material. Different materials offer varying levels of strength, corrosion resistance, and compatibility with fluids. Choosing a material without considering these factors can result in premature failure of the coupling. For instance, using a brass coupling in a system that handles corrosive fluids can lead to rapid degradation.
Ignoring size and compatibility requirements
Another error is ignoring size and compatibility requirements. It is crucial to select a coupling that precisely matches the size specifications of the existing system. An incorrect size can cause leaks or fail to withstand the system’s pressure, leading to potential accidents or system downtime.
Overlooking pressure ratings
Overlooking pressure ratings is also a critical mistake. Quick hose couplings are rated for specific pressure ranges, and using a coupling in a system with a pressure higher than its rating can lead to catastrophic failures. Always ensure that the coupling’s pressure rating meets or exceeds the system’s maximum operational pressure.
Overlook the importance of environment
Additionally, many importance of environmental and operational conditions. Couplings used in extreme temperatures or exposed to harsh environmental conditions require specific designs and materials to ensure reliable performance. For example, couplings used outdoors in marine environments should have high corrosion resistance.
Neglecting proper installation
Finally, a mistake often made is neglecting proper installation and maintenance. Improper installation can lead to leaks and system failures, while lack of regular maintenance can result in unnoticed wear and tear, ultimately leading to coupling failure.
By avoiding these common mistakes, you can ensure that your quick hydraulic couplings function effectively, last longer, and contribute to the overall safety and efficiency of your systems.
Conclusion
In summary, choosing the right quick release coupling requires careful consideration of materials, size and compatibility, pressure ratings, and environmental factors. Each aspect plays a vital role in ensuring the efficiency, safety, and longevity of your system. Remember, the most cost-effective choice is to find the best value with long-term performance and reliability. Proper installation and maintenance can further extend the life and enhance the functionality of these important components. We encourage you to continue your research and make a decision that is smart, safe, and best suited to the needs of your industry.
FAQ
How to choose the right material for a quick connector?
When selecting the material, consider the operating environment’s corrosiveness, temperature, and pressure requirements. Common materials include stainless steel, brass, and carbon steel.
What are the types of hydraulic quick connect fittings available?
Common types include push-to-connect, threaded, and flange connections. Choose based on the system’s connection method and usage scenario.
How to ensure compatibility of hydraulic quick connect fittings?
Ensure compatibility by checking the coupling’s connection size, sealing method, and material against the existing system specifications.
Do quick connect fittings require seals, and how to select the right ones?
Yes, hydraulic quick-connect fittings typically require seals. Select seals by considering the type of media and operating temperature, with common materials being Viton and NBR.
How do I determine the appropriate size for a quick connect fittings?
Determine the right size by understanding the system’s flow rate and pressure requirements. Standard sizes include 1/4 inch, 3/8 inch, and 1/2 inch.
How to maintain and care for quick couplings?
Regularly inspect seals and connection parts, remove dirt and debris, and avoid using incompatible lubricants and cleaners.